Introduction: 1200W 12/24V DC Power Supply for Cheap
It's been a very long time since I've posted anything on Instructables, so I decided I would make one for my power supply which I built for a HHO generator which I will also put up.
This power supply is capable of 96A @ 12V or 47A at 24V. My original plan was to use 3 in series to total 36V but it seems that the protection circuits don't allow this. After finding this out I decided I wasn't going to make an instructable due to the number of similar builds on google, but then decided I would make something unique worth posting. Due to this I am missing a few pictures but it is a relatively simple build and I will explain things in detail.
For all you people so concerned about safety, yes this is a dangerous project if you don't know what you're doing. Build at your own risk.
Step 1: Parts and Tools
These are the parts and tools I used, you could of course substitute anything with a part of your choice.
Parts:
- x2 DPS-600PB HP Server Power supplies. These are surprisingly cheap and I got 3 of them for $35 on eBay
- at least 5ft each of red and black 12awg wire
- x2 LCD volt meters. Got 3 for $10 on eBay
- x2 5k potentiometers
- x3 SPST toggle switches
- 4 Pole terminal block. I go two TGP-085 blocks on eBay for $6.
- Straight and L shaped aluminum stock
- Plexiglass
- Female spade terminals
- Small awg wire
- Heatshrink
Tools:
- Dremel with cutting and sanding attachments
- Soldering iron and solder. Having a fine tip will make things easier
- Drill with various bits
- Having some Dewalt Clamps (DWHT83148) makes everything better
Step 2: Modifying the Power Supplies
First and foremost, digging into these power supplies and changing circuits without knowing what you're doing can be very dangerous. All of the capacitors will discharge on their own relatively quickly but always be aware of them, once you get shocked by them you learn to keep your ass away! (they can kill you)
For this tutorial we will separate them into PS A and B.
For PS B you MUST open the case and separate the DC - from earth ground. I can't remember why this has to be done, couldn't find the post that explained it. To do this, remove the screw on the right corner of the board and use a small screwdriver to pry and break the jumper pins on the left side, this is better explained by just looking at the first picture. Cut a piece of the insulating plastic and stick it between the board and the standoff where the screw went. The board will remain solid even without the screw, fill the hole with glue so the plastic does not slide out. Use a multimeter to make sure there is no continuity between the case and the - terminal (the left one). This step is not necessary for PS A. *
The next steps are optional.
Before closing the PS's up you could wire the output as shown in the 4th picture If you didn't want to use the factory connector that plugs into the server unit. This would probably be a little easier than soldering to the external 12 pin connector. *
( Proceed to the next step before closing unit - optional) After closing them up we must wire the controls, this is where a fine tip iron and small wire comes in use. As shown in the 5th picture you must short pins 10, 8 and 6 to turn the unit on, combine any two together and add a switch between them and the 3rd wire (you can permanently connect them and use a switch on the mains instead). Shorting pins 4 and 8 will allow the PS to control the fan speed based on temperature. If these pins arent shorted then the fan will run at max and it's pretty loud. To add a voltage adjust put a potentiometer on 3, 5 (outer pins) and 9 (sweeper), this allows you to adjust between about 11V and 12.8V, The PS will go into shut down if the voltage goes too high or low. Voltage control is not necessary and is the only reason you would want to add volt meters, but I figured if I have the option I would use it. If you ever want to use them in parallel then add a switch between pin 11 on A & B, this is current share, pretty self explanatory. *
Lastly I soldered a 12awg wire between the clips of each connector, 2 for each pole, and used heat shrink to cover the uglyness. The conductors carry away so much heat I had to use a bigger iron with a wide tip to allow the solder to flow and bond.Aside from building wiring and NEC code, 12awg wire is rated for 41A when used in open air and not inside a jacket with other wires and having 2 wires in parallel is well over the max output on 47A. Of course there are many variables to a wires current capacity but ratings are made within a decent margin of its actual max value for safety reasons.
I used L bracket to attach the units together where the handle used to be, there are also two holes on the bottom and I used pop rivets to secure those, I also used a short piece of flat stock and screwed it in between the fan mounts (this can be seen in the next step)
* = example pictures from Google.
Step 3: Power Wiring
Due to the length of this step as well as the previous I decided to separate them.
I removed the power connectors from A and B and soldered wires in their place to splice them into a single power cable. It must be rated for at least 15A, preferably 20 because each unit can draw a max of 8.6A. While the board is outside of the case it is a good time to reroute the LED pwr indicator to the front of the unit if desired (the board must be completely out of the case to do this). there are holes in the DC connector that the light will fit through.
After removing the original plug the hole it was in will have sharp edges, so it is recommended to heatshrink the wires where they come out to prevent nicks in the insulation. After this I cut each wire to length and soldered them together, using a tire wrap to hold them together and a 3rd hand is extremely useful here. Tin each wire and make sure solder bridges the gap on both sides of the two that are joined, add a piece of heatshrink to the single wire and join them together. Mine looks a bit rough due to the wire being a little dirty but as you can see there are no gaps in the solder. It is also a good idea to stagger the joints and wrap some tape around the live and neutral wires just incase there are any strands sticking out, they are very sharp. After all the soldering is done it used one large piece of heatshrink to cover the whole thing and a tie wrap to hold it all together.
One Idea that would've been kinda cool would be to add a toggle switch in the cavity of the old plug to completely deenergize the units, because as long as they have mains power they remain in standby and the fans will run constantly.
Step 4: Building the Control Panel and Mounting the Terminal Block
For this I used an 11 x 15mm sheet of thin plexiglass, My HHO generator will be built inside a PC case, so the size of the case dictated the overall length of my PS. 15mm allows room to screw one end to the top of the PS, mount all the electronics, and bend down to protect the wiring as well as add stability. 11mm is the width of both units combined. I don't know the size of the screws used, I have a bin full of assorted hardware that I found them in.
A 4 pole terminal block was chosen to allow switching between series and parallel, the one I used is rated for 85A. If you only need the PS for one or the other, you can just use a 2 pole, but I like options. Just make sure it is rated for the current you intend to draw.
I marked a line where I wanted the bend and held it over my iron for a few minutes on each side and bent it over the edge of my desk. This was my first time ever using heat to shape plexiglass and I was very pleased with the outcome. Afterwards I added aluminum supports which screw to the side of the case. I then marked the layout for each part, I used a drill bit in my dremel as a router to get the rough shapes for my meters and refined them with the sander wheel. for everything else I used my soldering iron to melt a hole which eliminates cracking from drilling. This of course released toxic fumes, didn't bother me much though. The DC power wires were routed out the side and to the top, I used extra care in making them neat and straight. Sticky backs were used to bind them to the side of the case.
limited to space, I had to mount the terminal block to the top of the unit and use a thick piece of plexiglass to secure it due to lack of mounting holes. If you have more space then itd probably look better having the terminal block at the front. I used some long set screw and glued them to the plexiglass to attach the terminal block to it. Aluminum was used to level it as well as help secure the units. The wires were cut and terminated to create a neat arch onto the block and the meter wires were added after since I didn't have the chance to solder them to the connector.
Step 5: Conclusion
I was very happy with the way this project turned out, especially for the cost which was around $65. Because of its versatility I put in the extra effort to make it look professional and useful for any other project that requires a lot of DC power.
As you can see, I have already started on my HHO generator and am working on collecting parts right now so hopefully it shouldn't be too long before I post that too.
A couple of notes:
If for whatever reason 100A is not enough, more units could be used in parallel. just use a 2 pole switch or permanently wire the current share pins. There are many tutorials on creating different variations for different projects.
Keep in mind that I went above and beyond what is required to turn these into a hobbyist power supply. All that really needs to be done is to connect the power pins and they will turn on, so if you want something quick and dirty that's all it takes. some people just solder binding posts directly to the DC outputs. Most people also use these just to power RC battery chargers so there is not much of a need for the fanciness there.
So as Great Scott always says, "stay creative and I will see you next time!"
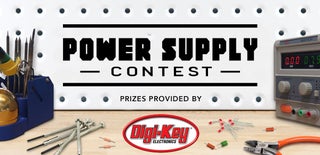
Participated in the
Power Supply Contest