Introduction: 3D Printed CO2 Rocket Cars
Traditional CO2 racers have been around for years, and have been historically carved by hand out of blocks of balsa wood. I decided to update and modify the process for my students by 3D modeling the vehicles and using a 3D printer to make the cars instead of carving them out of wood.
It does take a bit of practice to get the process just right, and the key to doing this economically is to make the cars a "shell" instead of a solid hunk of plastic. You also need to provide students with very specific requirements since most cars can't be modified once printed.
The finishing process gives students a real appreciation for automotive bodywork. It is an optional, labor intentive process, but rewarding. They'll definitely understand why it costs to much to fix a dent in your car!
There a few educational material websites you can visit for supplies, I purchased most of mine from Pitsco
Supplies
3D Printer
150 grit sandpaper
Automotive glazing putty
Spray primer
Spray paint
Wheels & Axles
CO2 cartridges
Track or smooth floor
Fishing line
CO2 car launcher
Step 1: Physical Constraints
Traditional car blanks measure around 300 mm (approx 12 inches) in length, which is too big for most 3D printers. I settled on 200mm - 210mm (approx 8") as the max/min length which allows me to print multiple cars at once. Of course you can choose whatever size you want, but for stability purposes you want to make them as long as practically possible. Printing them diagonally, one at a time is feasible, but nor practical (see pics). My complete list of constraints are as follows:
Length: 200mm - 210mm
Width: 30mm - 60mm
Max Height: 55 mm
Height of center of hole for CO2 tank: 30mm
Diameter of hole for CO2 tank: 19mm
Depth of hole for CO2 tank: 45mm
body shell thickness: 1.5mm
Must have a 3mm holes for axles
Bottom of car must be completely flat
I'm also showing the wheels, axles and CO2 tanks here because they are also some of your biggest constraints! You have to make sure the design is made to work with the parts you have on hand.
Step 2: 3D Modeling
In order to get printed cars that work the first time, keep these tips in mind during the 3D modeling process:
- Instead of using eye hooks like traditional CO2 cars, make your 3D printed cars with a 3mm hole lengthwise through entire body, centered and 5mm from bottom. This hole will be used for the fishing line that guides cars along the track.
- Make all body fillets BEFORE shelling. If you shell and then fillet, you risk open edges. Try it both ways and look at a cross section - you'll see what I mean.
- Leave the shelling command until near the end, but keep in mind that very small and/or sharp features may cause the shell command to fail.
- Make axle and fishing line holes AFTER shelling.
Step 3: Create Orthographic Projection Drawing
Document your build by making a 3-view orthographic projection with basic dimensions and a shaded isometric view.
I also require an exploded assembly drawing, but that is up to you.
Attachments
Step 4: 3D Print
Generate the STL files and arrange in your slicer software.
I use PLA with 18% infill with 15% support density for easy removal.
Note that the requirement for a flat bottom helps in the adhesion of the car to the printing bed.
Use a large brim and only use support touching buildplate
I've printed cars with printers from Makerbot, Airwolf3D, Raise3D, Robo3D, Dimension, and even a Formlabs resin printer. Almost any modern 3D printer should work!
Step 5: Sand Body With 150 Grit
Traditional FDM printers leave surfaces with visible layer lines. These would be just fine, but I make my students do some additional body work to make them pretty.
Sand, glaze, sand, primer, sand, paint.
You don't want to try and make your print totally smooth just by sanding, it won't work. Instead, do an initial sanding with 150 grit, then move on to the glazing putty.
Step 6: Smooth Body Using Glazing Putty
I use Bondo Glazing Putty. It dries quickly and sands easy. The fumes are strong, so use it either outdoors ir in a well-ventilated environment.
After drying for 24 hrs, sand again with 150 grit. The dust does get all over everything, so sand outdoors. Sand until almost all of the putty is gone. You'll notice that the only filler left is inside small ridges and print lines.
If you don't do this, you can still get a good looking car, but the layer lines will be visible (see car #5).
Step 7: Primer & Paint
I use a high-build automotive primer, but most any spray primer will work. You can also sand lightly with 400 grit or a Scotch Brite pad after priming if you'd like. Regular gloss spray paint works well, one coat is usually good enough once you get good at it. As an option, you may follow up with clear coat.
Step 8: Assemble & Decorate
Students can either draw/paint on the car itself or use stickers to decorate it. At minimum, you should have large numbers on either side.
Step 9: RACE!
Of course, a dedicated track is best, but I've run cars successfuly on the floor either in a long tiled corridor or the gym floor. I highly recommend a launcher of some sort - I purchased mine from Pitsco. It is simply a spring-loaded nail mechanism to pierce the CO2 tank.
Put some blankets or sweaters at the end of the track to stop the cars - crucial!
The Pitsco launchers give you the option to launch both cars at the same time
Attachments
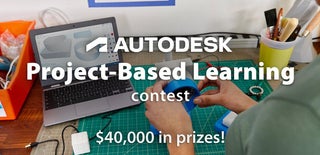
Runner Up in the
Project-Based Learning Contest