Introduction: 3D Printed Concrete Table Mold
A friend of mine is obsessed with pusheen toys and anything pusheen-shaped. He mentioned making pusheen-shaped table for quite a while, but never got around making it, so we joined forces and made it together. Initially, he planned on making it by bending stripes of plywood and shaping it to create a mold, but why do it if your friend has a 3D printer? 3D printing the mold allows you to create a very precise shape and small details. My method is easy and requires very few tools to create this amazing table top.
I provided STL files for that particular shape, but with a bit of ingenuity you can make concrete table top in any shape you want.
You will need:
3D printer
Two part epoxy
Filler (wood filler will do)
Sanding paper (40/80/120/240 grit)
Concrete polishing pads (https://www.amazon.com/Diamond-Polishing-Backer-Gr...
Glue gun and glue sticks
Silicon sealant
Release agent (vaseline, WD40 etc)
Concrete mix, mixing bucket, varnished plywood board, screws, two long pieces of wood
Gloves, face mask
Disposable containers for mixing epoxy, scotch tape
Black concrete pigment (or white and black acrylic paint if using my epoxy method for filling cavities)
Polyurethane varnish or concrete sealer
Table legs
Step 1: STL Files
I used pusheen cookie cutter file available on Thingiverse (https://www.thingiverse.com/thing:773683) as a base to make this concrete table top mold. I resized it, cut into pieces, added bolts and made a few minor adjustments.
The key to making this mold work is printing it in low quality (0.3mm layer height) and using low infill (ideally 5%, maximum 10%). It will hold its shape just fine, it will be sturdy enough to hold concrete and weak enough to break away once everything is cured. STL files I provided can be easily resized to make this table top as big or as small as you please. Print using PLA to prevent warping and splitting.
Step 2: Assembly
1) Print all parts and assemble them to check if they align.
2) Clean each part with a craft knife, make sure bolts fit snugly and sand with coarse sand paper. There is no need to make the mold smooth, so don’t spend too much time on that part.
3) Use two part epoxy to assemble the mold. Make sure everything is flushed and straight.
4) Use filler (I used wood filler) to fill the gaps where mold parts met. Sand once dried.
Step 3: Attach to the Board
1) Attach the mold to plywood or melamine board (we need smooth surface) using special glue for plastics or epoxy, but don’t use superglue. Make sure you spread the glue everywhere, don’t leave any gaps.
2) Fire up your glue gun and secure the mold with hot glue. Be generous, we want the mold to stick to the board.
Step 4: Silicone
I went for an overkill here and secured it further with a thick layer of silicone. I wanted it to be extra secure as I was moving and transporting the mold, but its not necessary to apply THAT much silicone.
Step 5: Stencil
I used this printable stencil to mark the location of eyes and whiskers, and I glued them with epoxy.
Attachments
Step 6: Lubricate
Use a release agent to cover the inside of the mold.
Anything oily will do- cooking oil, Vaseline, professional mold release products, WD40… This is a very important step, so make sure to get every nook and cranny. I opted for (warmed up) Vaseline to cover up my laziness, Vaseline got into all those tiny gaps I didn’t fill with wood filler. It was easy to spread it with my finger, I used a disposable brush to lubricate small details like the eyes and whiskers.
Step 7: Concrete
Mix a batch of concrete and fill the mold. Start by filling the mouth/eye area to make sure there are no air pockets. Once filled vibrate the whole mold using an orbital sander without the sanding pad. You could also use a rubber mallet or simply bang the table with your bare fists. Anything to get rid of those air bubbles.
Step 8: Plywood Board
You will need to drill holes to attach the legs once the table is ready and plywood is easier to drill than concrete.
This part is optional. Screw two long pieces of wood to a piece of varnished plywood and press the plywood into the mold. Those two pieces of wood will rest on top of the mold making sure your plywood is flushed. Weight it down with something heavy and leave to cure for a minimum of 2 days.
Step 9: Removing the Mold
Remove the mold. Be careful not to chip any small parts. Leave to dry for 2 more days, it will change color once dry.
1st picture: straight from the mold
2nd picture: 2 days later
Remove remaining pieces of the mold (eyes, whiskers, tail). Make a hole in the middle of the plastic, cut it away with a craft knife and use nose pliers to remove it.
Step 10: Sanding
Sanding is by far the most annoying thing ever, but there is no way around it, so prepare yourself for some sore muscles. I started with 40 grit to get rid of rough pieces especially at the bottom and sides, followed by 80, 120 and 240. The top part was relatively smooth, so I barely touched it with 120 and 240 grit. I used a combination of wet and dry sanding (make sure to wear a mask while sanding!).
Step 11: Polishing
When I finished sanding I realized I was left with some holes and imperfections, so I decided to use a concrete slurry to cover bigger gaps. I wet-polished the top with polishing pads before applying the slurry. I used 50, 150, 300 and 500 grit polishing pads, mixed a small batch of thin concrete and applied that with my hand. I let it dry for 12 hours and came back to sand the top with 240 sand paper and polish it with polishing pads again. This time I used the whole polishing set, started with 50 and ended with 3000 grit. I used every pad for approximately 2-3 minutes and applied a lot of pressure. I should probably mention that I was sanding and polishing manually so my arm was dying in the end.
All that polishing paid off, the result was spectacular. The top was shiny, smooth to the touch and felt like marble. It still had some imperfections on the top and I could have applied another coat of slurry, but I decided to leave it just as it was.
Step 12: Filling the Cavities
Originally, I intended to fill eyes, whiskers and so on with pigmented concrete but I lost my bag of pigment and decided to use colored, two part epoxy (read this instructable to familiarize yourself with my --> https://www.instructables.com/id/DIY-Epoxy-Enamel... ).
I printed pieces of the mold to use as a border and prevent cement/epoxy spillage. I made sure they are flushed, and I covered them with scotch tape to prevent epoxy from sticking to PLA. I used glue gun and duck tape to attach them.
I mixed three separate batches of black and grey epoxy using black and white acrylic paint and poured it in the cavities using small piping bags. Left it to cure for 24 hours, removed the plastic borders and gently sanded those epoxy parts.
Step 13: Varnishing
I cleaned the whole table top with water, removed any debris and varnished with polyurethane varnish. Left that to cure for 3 hours and finally attached the legs.
Step 14: Finished
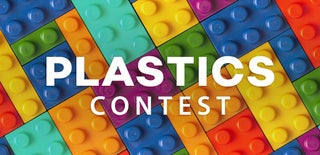
Runner Up in the
Plastics Contest