Introduction: 3D Printed SlamDunk Mini Hoop
Since my early test of 3D printed objects I experimented many ways how to make mini basketball hoops for my son
Two of these are available on my thinghiverse account: mini basketball hoop - MINI BBALL HOOP MK2
Unfortunately these proved to be brittle and even the mixed construction with metal parts of the second model inevitably has yielded to the repeated stresses of my son's dunks.
Therefore I tried creating a model that was mechanically designed to absorb the loads of the dunks who, in the meantime, have grown up like my son.
The result is a simple and essential object that owes its performance to the correct choice of the plastic filament used for the 3D printed parts combined with a spring that takes care of withstanding the extra stress.
Step 1: Material - PETG
I decide to use PETG filament (black) for printing the parts of this project because this material has several features that make it ideal for the job.
PET-G is an acronym for Poly-Ethylene Terephthalate Glicol and is one of the most common polymers.It is mainly used to make water bottles, food packaging, and several other common plastic parts.
It combines the most useful mechanical properties of ABS filament with the ease of printing of PLA filament
One of its best features it is the resistance to impact making it suitable to create objects that can be subjected to collision or repeated bumps. It is less harder than the ABS so it could be scratched easier but, in my application, the ball is round and softer than the hoop so no problem.
Another peculiarity is the low shrinkage, which involves minimal deformations and no warping, making it ideal for printing large objects like this hoop that has a diameter of 190mm and the bigger dimension of 220 mm.
In brief a list of material Pros
- Durable
- Strong not brittle
- Great impact resistance
- Great chemical resistance
- Low shrinkage
- Great layer adhesion
- Odourless during printing
- food safe (if handled properly)
In the other hand a list of Cons
- Not so easy to print (requires some calibration)
- sticky and stringing
- not suitable for sharp details
- not so hard
hygroscopic
common 3d printing settings
Print temperature range 210°C – 240°C
print bed temperature range 50°C – 75°C
- speed around 60mm/s
Step 2: Assembly
BOM (Bill of material)
3D printed parts (attached)
- Hoop
- hinge
Hardware
- 1 - M4x65 screw
- 5 - M4 nut
- 4 - M4x20 countersunk head screw
- 1 - dia 10x30x1,5 mm spring
- 1 - 300x400 mm plywood panel
The assembly is quite simple and intuitive:
join the hoop in the hinge inserting the spring in the receptacle and the M4 screw 65mm long
fix the hinge to a plywood panel using the four countersunk screws
attach the whole assembly at the wall using a couple of wall plug
and now ..... DUNK like there's no tomorrow !
bye
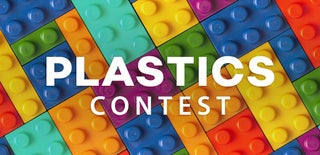
Participated in the
Plastics Contest