Introduction: 3D Printed Smartphone Case
[2020 UPDATE]: Hello all, this is just a quick update after yet *another* long absence. Now that I'm back, feel free to ask any questions in comments.
This instructable may contain links to affiliate(Amazon and eBay) websites, and I receive an affiliate commission for any purchases made by you on the affiliate website using such links, at no additional cost to you.
- Edited Instructable to "fit with the times"
- Added captions in pictures instead of explanation outside.
- Added/Modified keywords
- Added product links
- Rewrote the whole thing basically
Hello everyone! After a long time of absence, I am finally back on my favorite How-to site, Instructables!
Smartphones are NOT indestructible Nokias. Without a phone case, there is a GUARANTEED chance that you will drop it and the screen will look like a spiderweb. I've had so many smartphones now and not one of them has come out unscathed. As you can see in the picture, even my old flip phone took a hit. Trust in Murphy's Law: If your screen can break, it will break. Here's a phrase that applies to many things in life: USE PROTECTION ;)
This Instructable explains my process of creating a 3D-printed phone case for the phone I had at the time, which was a HTC HD7 Windows Phone (this one). If you have this phone, you can use my dimensions and files to create an identical case to the one in this 'ible. I understand that you may have some newer, sleeker, sexier phone, but the steps to make the case are the same. I even included updated recommendations for newer phones that work especially well with cases in the Improvements step.
So, without further ado, let's get started.
Step 1: What You'll Need (Materials and Tools)
Here is the list of materials I used to make this custom 3D printed phone case.
Materials Needed:
- Your phone: I used this phone for the project.
- Headphone cable: Get a cable with a larger plug head so you can dimension it accordingly so all plug sizes equivalent or smaller will fit in the phone with the case on. This forum post highlights this issue and had case fitment problems with these headphones. I'd recommend using them as reference for your case.
- Phone charger cable: The standard cable that comes with your phone should be fine. If you have a third-party charger with a larger plug head I'd recommend using that instead. My phone used this charger.
- String: Preferably some type of flat ribbon as round strings tend to slip. You really don't need that much. The cheapest roll I found on Amazon is here. If you find one for less, let me know and I'll update.
Tape: To tape the string down. Any tape will do, although I went with clear tape that did not leave residue.
Tools Needed:
- 3D Printer: I was fortunate enough to have access to a 3D printer from my school. It was one of those super large printers that most hobbyists don't have access to. I can, however, give tips and recommendations for 3D printers based on experience. First, I would not recommend using an SLA resin type 3D printers as in my experience as the resulting plastic is quite brittle. I did a lot of research and found what I consider the best in low, middle, and high priced 3D printers for this job. Keep in mind that these printers have large build volume to accommodate larger phones like iPhone 8 plus (6.24 in) and are very good for other projects too.
- Lower tier:XYZprinting da Vinci Pro 1.0 => Huge 7.9" build volume and comes with laser engraver.
- Mid-range: LulzBot Mini 2 => Overall a fast, flexible, and reliable printer.
- Upper tier: Ultimaker S5 3D Printer => The epitome of the perfect 3D printer. If you are getting a printer just to make phone cases this may be overkill. Although I could go on and on about the benefits, the main 3 would be filament variety, the large build volume (33 x 24 x 30cm or 13 x 9.4 x 11.8 inches), and the dual extrusion which allows for hybrid material AND/OR multicolored prints.
- Printer Filament: My phone case was originally printed in PLA because that was the only material I had access to at the time. However, due to improvements in 3D printing technology there are new filament materials that I would recommend.
- PETG: PETG is a "hard" material that is the "best-of-both-worlds" of PLA and ABS. It is overall resilient like ABS, yet has the ease of printing and variety that PLA filaments offer. PETG also does not degrade from UV exposure.
- TPU: TPU is a "soft" material and is what most commercial soft phone cases are made of. It has a matte rubbery feel that is a good balance between stiffness and flexibility.
- Soft PLA: Slightly softer than TPU, the main advantage that it has over TPU is that it can be printed just like ordinary PLA without any fine-tuning or setup.
- Dial or Digital Calipers: The most useful measuring tool (in my opinion); needed to measure phone dimensions and the distance of the buttons/ports relative to the edge and to each other. I chose some 8 inch calipers since 6 inch calipers are sometimes not large enough. I personally prefer digital calipers over dial calipers, but both of these are good:
- Yardstick: Used to measure the length of the string and to determine the fillet radius (with the string). A longer ruler can be used in place of the yardstick, but the ruler length should be 15 inches or longer. Any old yardstick will do, but if you ask me I prefer this one.
- Some type of 3D modeling software/CAD: You can use Google Sketchup, Autodesk Inventor, SolidWorks, etc. I like to use Autodesk Inventor because that is the program I am most familiar with, but feel free to use what you like.
- Sandpaper/Dremel: Sandpaper or a Dremel is recommended if you have a lower-end 3D printer to make minor changes to your print after printing because sometimes the phone won't fit. Sanding also removes the bumps left on the print by the print support structures. Another strategy that works is to intentionally make the case dimensions smaller than the phone, then sanding it bigger for perfect fit.
·
Step 2: Choose Your Design
N̶o̶w̶ ̶c̶o̶m̶e̶s̶ ̶t̶h̶e̶ ̶p̶a̶r̶t̶ ̶w̶h̶e̶r̶e̶ ̶y̶o̶u̶ ̶g̶e̶t̶ ̶t̶o̶ ̶m̶a̶k̶e̶ ̶a̶ ̶c̶h̶o̶i̶c̶e̶.̶.̶.̶a̶ ̶c̶h̶o̶i̶c̶e̶ ̶t̶h̶a̶t̶ ̶w̶i̶l̶l̶ ̶d̶e̶t̶e̶r̶m̶i̶n̶e̶ ̶t̶h̶e̶ ̶f̶a̶t̶e̶ ̶o̶f̶ ̶y̶o̶u̶r̶ ̶p̶h̶o̶n̶e̶.̶ ̶D̶o̶ ̶y̶o̶u̶ ̶w̶a̶n̶t̶ ̶a̶ ̶c̶a̶s̶e̶ ̶t̶h̶a̶t̶ ̶c̶l̶o̶s̶e̶s̶ ̶i̶n̶ ̶o̶n̶ ̶y̶o̶u̶r̶ ̶p̶h̶o̶n̶e̶ ̶f̶r̶o̶m̶ ̶t̶h̶e̶ ̶s̶i̶d̶e̶s̶?̶ ̶O̶r̶ ̶o̶n̶e̶ ̶t̶h̶a̶t̶ ̶p̶i̶e̶c̶e̶s̶ ̶t̶o̶g̶e̶t̶h̶e̶r̶ ̶a̶r̶o̶u̶n̶d̶ ̶y̶o̶u̶r̶ ̶p̶h̶o̶n̶e̶ ̶l̶i̶k̶e̶ ̶a̶ ̶p̶u̶z̶z̶l̶e̶?̶ ̶M̶a̶y̶b̶e̶ ̶o̶n̶e̶ ̶t̶h̶a̶t̶ ̶s̶n̶a̶p̶s̶ ̶t̶o̶g̶e̶t̶h̶e̶r̶ ̶w̶i̶t̶h̶ ̶o̶n̶e̶ ̶h̶a̶l̶f̶ ̶o̶n̶ ̶t̶o̶p̶ ̶a̶n̶d̶ ̶o̶n̶e̶ ̶o̶n̶ ̶t̶h̶e̶ ̶b̶o̶t̶t̶o̶m̶?̶ ̶W̶h̶a̶t̶e̶v̶e̶r̶ ̶y̶o̶u̶r̶ ̶d̶e̶s̶i̶g̶n̶ ̶i̶s̶,̶ ̶t̶h̶e̶r̶e̶ ̶a̶r̶e̶ ̶2̶ ̶t̶h̶i̶n̶g̶s̶ ̶t̶o̶ ̶k̶e̶e̶p̶ ̶i̶n̶ ̶m̶i̶n̶d̶.̶ ̶F̶i̶r̶s̶t̶,̶ ̶y̶o̶u̶ ̶n̶e̶e̶d̶ ̶t̶o̶ ̶r̶e̶m̶e̶m̶b̶e̶r̶ ̶t̶h̶a̶t̶ ̶t̶h̶e̶ ̶p̶l̶a̶s̶t̶i̶c̶s̶ ̶u̶s̶e̶d̶ ̶i̶n̶ ̶3̶D̶ ̶p̶r̶i̶n̶t̶i̶n̶g̶ ̶a̶r̶e̶ ̶s̶o̶l̶i̶d̶ ̶(̶n̶o̶t̶ ̶f̶l̶e̶x̶i̶b̶l̶e̶)̶,̶ ̶s̶o̶ ̶y̶o̶u̶ ̶c̶a̶n̶n̶o̶t̶ ̶m̶a̶k̶e̶ ̶a̶ ̶c̶a̶s̶e̶ ̶t̶h̶a̶t̶ ̶i̶s̶ ̶o̶n̶e̶ ̶p̶i̶e̶c̶e̶,̶ ̶b̶e̶c̶a̶u̶s̶e̶ ̶t̶h̶a̶t̶ ̶w̶a̶y̶ ̶y̶o̶u̶ ̶c̶a̶n̶n̶o̶t̶ ̶f̶i̶t̶ ̶t̶h̶e̶ ̶p̶h̶o̶n̶e̶ ̶i̶n̶s̶i̶d̶e̶.̶ ̶R̶a̶t̶h̶e̶r̶,̶ ̶y̶o̶u̶ ̶w̶o̶u̶l̶d̶ ̶n̶e̶e̶d̶ ̶t̶o̶ ̶p̶r̶i̶n̶t̶ ̶m̶u̶l̶t̶i̶p̶l̶e̶ ̶p̶i̶e̶c̶e̶s̶ ̶o̶r̶ ̶h̶a̶l̶v̶e̶s̶ ̶t̶h̶a̶t̶ ̶c̶a̶n̶ ̶b̶e̶ ̶f̶i̶t̶ ̶a̶r̶o̶u̶n̶d̶ ̶t̶h̶e̶ ̶p̶h̶o̶n̶e̶.̶ ̶T̶h̶e̶ ̶f̶i̶r̶s̶t̶ ̶i̶d̶e̶a̶ ̶I̶ ̶c̶a̶m̶e̶ ̶u̶p̶ ̶w̶i̶t̶h̶ ̶f̶o̶r̶ ̶m̶a̶k̶i̶n̶g̶ ̶a̶ ̶c̶a̶s̶e̶ ̶w̶a̶s̶ ̶a̶c̶t̶u̶a̶l̶l̶y̶ ̶j̶u̶s̶t̶ ̶a̶ ̶s̶i̶n̶g̶l̶e̶ ̶p̶i̶e̶c̶e̶ ̶o̶f̶ ̶p̶l̶a̶s̶t̶i̶c̶ ̶t̶h̶a̶t̶ ̶w̶o̶u̶l̶d̶ ̶f̶i̶t̶ ̶a̶r̶o̶u̶n̶d̶ ̶t̶h̶e̶ ̶p̶h̶o̶n̶e̶.̶ ̶I̶ ̶w̶a̶s̶ ̶t̶h̶i̶n̶k̶i̶n̶g̶ ̶a̶b̶o̶u̶t̶ ̶c̶o̶m̶m̶e̶r̶c̶i̶a̶l̶ ̶p̶h̶o̶n̶e̶ ̶c̶a̶s̶e̶s̶ ̶a̶t̶ ̶t̶h̶e̶ ̶t̶i̶m̶e̶,̶ ̶w̶h̶i̶c̶h̶ ̶w̶e̶r̶e̶ ̶u̶s̶u̶a̶l̶l̶y̶ ̶m̶a̶d̶e̶ ̶o̶f̶ ̶a̶ ̶r̶u̶b̶b̶e̶r̶y̶ ̶m̶a̶t̶e̶r̶i̶a̶l̶ ̶t̶h̶a̶t̶ ̶c̶o̶u̶l̶d̶ ̶b̶e̶ ̶s̶t̶r̶e̶t̶c̶h̶e̶d̶ ̶o̶v̶e̶r̶ ̶t̶h̶e̶ ̶p̶h̶o̶n̶e̶.̶ ̶T̶h̶e̶ ̶s̶e̶c̶o̶n̶d̶ ̶t̶h̶i̶n̶g̶ ̶t̶o̶ ̶t̶h̶i̶n̶k̶ ̶a̶b̶o̶u̶t̶ ̶i̶s̶ ̶d̶i̶s̶a̶s̶s̶e̶m̶b̶l̶y̶ ̶o̶f̶ ̶t̶h̶e̶ ̶c̶a̶s̶e̶ ̶i̶f̶ ̶n̶e̶c̶e̶s̶s̶a̶r̶y̶.̶ ̶Y̶o̶u̶ ̶m̶a̶y̶ ̶w̶a̶n̶t̶ ̶t̶o̶ ̶t̶a̶k̶e̶ ̶t̶h̶e̶ ̶c̶a̶s̶e̶ ̶o̶f̶f̶ ̶a̶t̶ ̶s̶o̶m̶e̶ ̶p̶o̶i̶n̶t̶ ̶i̶n̶ ̶t̶h̶e̶ ̶f̶u̶t̶u̶r̶e̶,̶ ̶s̶o̶ ̶i̶t̶ ̶w̶o̶u̶l̶d̶ ̶b̶e̶ ̶a̶ ̶g̶o̶o̶d̶ ̶i̶d̶e̶a̶ ̶t̶o̶ ̶m̶a̶k̶e̶ ̶y̶o̶u̶r̶ ̶d̶e̶s̶i̶g̶n̶ ̶h̶a̶v̶e̶ ̶r̶e̶m̶o̶v̶a̶b̶l̶e̶ ̶h̶a̶l̶v̶e̶s̶/̶p̶i̶e̶c̶e̶s̶.̶ ̶ ̶
F̶o̶r̶ ̶m̶y̶ ̶d̶e̶s̶i̶g̶n̶,̶ ̶I̶ ̶c̶h̶o̶s̶e̶ ̶a̶ ̶d̶e̶s̶i̶g̶n̶ ̶w̶i̶t̶h̶ ̶2̶ ̶h̶a̶l̶v̶e̶s̶.̶ ̶O̶n̶e̶ ̶h̶a̶l̶f̶ ̶o̶f̶ ̶i̶t̶ ̶e̶n̶c̶l̶o̶s̶e̶s̶ ̶t̶h̶e̶ ̶p̶h̶o̶n̶e̶ ̶o̶n̶ ̶a̶l̶l̶ ̶s̶i̶d̶e̶s̶ ̶e̶x̶c̶e̶p̶t̶ ̶t̶h̶e̶ ̶b̶a̶c̶k̶,̶ ̶w̶h̶e̶r̶e̶ ̶i̶t̶ ̶p̶r̶o̶t̶r̶u̶d̶e̶s̶ ̶a̶ ̶b̶i̶t̶;̶ ̶t̶h̶e̶ ̶p̶r̶o̶t̶r̶u̶s̶i̶o̶n̶ ̶a̶l̶l̶o̶w̶s̶ ̶f̶o̶r̶ ̶t̶h̶e̶ ̶o̶t̶h̶e̶r̶ ̶h̶a̶l̶f̶,̶ ̶w̶h̶i̶c̶h̶ ̶a̶c̶t̶s̶ ̶l̶i̶k̶e̶ ̶a̶ ̶p̶l̶u̶g̶,̶ ̶t̶o̶ ̶s̶n̶a̶p̶ ̶i̶n̶ ̶p̶l̶a̶c̶e̶.̶ ̶M̶y̶ ̶o̶r̶i̶g̶i̶n̶a̶l̶ ̶d̶e̶s̶i̶g̶n̶ ̶w̶a̶s̶ ̶a̶ ̶f̶r̶i̶c̶t̶i̶o̶n̶ ̶f̶i̶t̶ ̶d̶e̶s̶i̶g̶n̶ ̶w̶i̶t̶h̶ ̶p̶e̶g̶s̶ ̶a̶n̶d̶ ̶h̶o̶l̶e̶s̶,̶ ̶w̶h̶e̶r̶e̶ ̶2̶ ̶h̶a̶l̶v̶e̶s̶ ̶w̶h̶e̶r̶e̶ ̶p̶u̶s̶h̶e̶d̶ ̶t̶o̶g̶e̶t̶h̶e̶r̶ ̶f̶r̶o̶m̶ ̶t̶h̶e̶ ̶s̶i̶d̶e̶s̶,̶ ̶b̶u̶t̶ ̶t̶h̶e̶n̶ ̶I̶ ̶d̶i̶d̶ ̶s̶o̶m̶e̶ ̶r̶e̶s̶e̶a̶r̶c̶h̶ ̶a̶n̶d̶ ̶f̶o̶u̶n̶d̶ this ̶s̶i̶t̶e̶.̶ ̶I̶t̶ ̶g̶a̶v̶e̶ ̶m̶e̶ ̶t̶h̶e̶ ̶i̶d̶e̶a̶ ̶t̶o̶ ̶u̶s̶e̶ ̶a̶ ̶s̶n̶a̶p̶ ̶f̶i̶t̶ ̶d̶e̶s̶i̶g̶n̶ ̶i̶n̶s̶t̶e̶a̶d̶,̶ ̶w̶h̶i̶c̶h̶ ̶i̶s̶ ̶v̶e̶r̶y̶ ̶s̶i̶m̶i̶l̶a̶r̶ ̶t̶o̶ ̶t̶h̶e̶ ̶o̶n̶e̶ ̶i̶n̶ ̶t̶h̶e̶ ̶p̶i̶c̶t̶u̶r̶e̶,̶ ̶b̶u̶t̶ ̶w̶i̶t̶h̶ ̶4̶ ̶c̶o̶n̶n̶e̶c̶t̶i̶o̶n̶ ̶p̶o̶i̶n̶t̶s̶ ̶i̶n̶s̶t̶e̶a̶d̶ ̶o̶f̶ ̶2̶.̶
[UPDATE]: Like previously mentioned, advancements in filament technology means that it is now possible to make rubbery, one-piece phone cases that stretch over your phone. Keep in mind that my snap-fit case was made when rubber-like filament wasn't around, and that trying to create a snap-fit design using the rubber filament would not work as well as a snap-fit case made of hard plastic. Basically, make your case snap-fit if printing with a hard material and make it a one-piece if using soft material.
Step 3: Measure and Take Notes!
This is probably the most important step in making a case specifically for your phone: taking very exact measurements of the phone. There are many important things to note when measuring and recording dimensions. First you'll need to decide a thickness for the case (I chose 0.1 in, which was too thick in hindsight). Then use the calipers to measure the distance of everything relative to the edges and other parts of the phone. This should be recorded because you will need to know where to draw the openings for headphone output, charging port, buttons, etc. in the 3D modeling software. I personally took 2 pages of very specific notes; they are very messy though and most people would not understand it, but as long as you can understand your own notes it should be fine.
Also, now is the time to find the fillet radius for the rounded corners of your phone. To do this, you must first find the perimeter of the phone. Take the flat ribbon, and tape it somewhere on the edge of the phone. Then, tightly "wrap" the ribbon around the edges of the phone, using tape to hold it down if necessary. When you get back to the starting point, cut it. Now measure the ribbon, the length will be your perimeter. Now that you have the perimeter, you must find the length of the sides (length and width) just before the rounded corner of the phone (see picture). Measure the green and pink edges, and add the lengths together. In my case, my side lengths were approximately 4.060 and 2.030 in, so I did 4.060 + 4.060 + 2.030 + 2.030 = 12.18. You may have noticed that if you take the 4 corners (highlighted yellow) and pieced them together, you get a full circle! This is very useful, because now you can use the equation p = 2πr + n to solve for r, where p is the perimeter, 2πr is the circumference, and n is the sum of the edges. For me, r was about 0.337. The fillet radius will be needed later in the CAD work.
Another thing to point out are the cables, which should be measured and dimensioned where the plastic is, not where the metal is. This is because you want the opening to be big enough to fit the plastic part, or else the cables can't be plugged in with the case on.
Step 4: Draw It Out!
With all the data and measurements, we can now proceed to model the case on your favorite CAD software. So the first thing that must be done is to outline the inside of the case, where the phone will actually sit. A good idea would be to take the actual exact dimensions of the phone, and "rounding it up" a bit. For example, if you have a measurement of 2.011 inches, you might want to round it up to 2.02 inches. This is because if you make the case the exact same dimensions as the phone, it may not fit in the case as well as you'd like. The exact length and width of my phone were 4.814 and 2.662 respectively, but I rounded them up to 4.820 and 2.670. Alternately, you could use the "Sand and Drill" method I mentioned earlier. The Sand and Drill method is when you intentionally make the dimensions smaller or same as that of the phone, then you sand and/or dremel the plastic after you print it, to achieve a proper fit. This method may be preferred over the other method, because it can get a better fit; the other method may create a slightly larger/loose case. As for cases printed with rubber material, using exact (or perhaps even smaller) dimensions would be preferred as the case will stretch out over time.
Anyways, back to the drawing. Now you will need to apply the fillet radius to the corners of the rectangle shaped box you made. Since I have a 0.337 fillet radius, that is what I used. After that, you can use your amazing CAD skills to draw out the rest of your phone case.
Some other advice for designing your case:
- If you decide on a hard case, a good design would a "4 corners" phone case, which only snaps onto the phone by the corners. This offers all the realistic protection that the phone needs without hindering the ability to use the phone/press the side buttons. See the minimalist case picture (picture source)
- If you decide to make a soft rubber case, I'd recommend not cutting out slots for the buttons and instead designing the case shape to overlap them while still allowing for easy access to the buttons through the case. See the case with the "independent" red buttons picture (picture source)
- I made my case too thick at 0.1 inches, in hindsight I'd probably make it 0.05 inches at max, maybe a bit more on the corners. That goes for both hard and soft cases.
Step 5: Printing It Out!
Now you can export your model as an stl. file and 3D print it! Before printing, make sure to set up your 3D printer to work optimally with whatever filament you choose to use. For example, if you are using the PETG filament I recommended (here), you'd need higher extrusion temperature compared to PLA prints and a heated bed. The TPU and Soft PLA filaments are much more forgiving and should print on any printer really. After you print it, grab your sandpaper and make any necessary adjustments to the plastic to ensure that your phone fits perfectly. If the case was designed too large, then you can learn from your mistakes and remake the model. Alternatively, you could also fill in the volume with hot glue or epoxy and then sand that down for a perfect fit.
For me, everything turned out fine, except the headphone cable hole was a little small so I slightly widened it with a dremel. If you want to look at my model, I've included the stl. files on here if you want to download, maybe you have the same phone as me. Once again I would like to thank my school for letting me use their 3D printer...and their green filament!
I like this color :)
Step 6: Improvements?
N̶o̶w̶ ̶t̶h̶a̶t̶ ̶y̶o̶u̶'̶v̶e̶ ̶b̶u̶i̶l̶t̶ ̶t̶h̶e̶ ̶b̶a̶s̶i̶c̶ ̶p̶h̶o̶n̶e̶ ̶c̶a̶s̶e̶,̶ ̶w̶h̶y̶ ̶n̶o̶t̶ ̶i̶m̶p̶r̶o̶v̶e̶?̶ ̶Y̶o̶u̶ ̶c̶a̶n̶ ̶a̶d̶d̶ ̶d̶i̶f̶f̶e̶r̶e̶n̶t̶ ̶s̶h̶a̶p̶e̶s̶,̶ ̶t̶e̶x̶t̶u̶r̶e̶s̶,̶ ̶p̶a̶t̶t̶e̶r̶n̶s̶.̶.̶.̶t̶h̶e̶ ̶p̶o̶s̶s̶i̶b̶i̶l̶i̶t̶i̶e̶s̶ ̶a̶r̶e̶ ̶e̶n̶d̶l̶e̶s̶s̶!̶ ̶Y̶o̶u̶ ̶c̶o̶u̶l̶d̶ ̶m̶a̶k̶e̶ ̶o̶n̶e̶ ̶o̶f̶ ̶t̶h̶o̶s̶e̶ ̶P̶i̶k̶a̶c̶h̶u̶ ̶p̶h̶o̶n̶e̶ ̶c̶a̶s̶e̶s̶,̶ ̶a̶l̶t̶h̶o̶u̶g̶h̶ ̶i̶t̶ ̶p̶r̶o̶b̶a̶b̶l̶y̶ ̶w̶o̶u̶l̶d̶n̶'̶t̶ ̶b̶e̶ ̶a̶ ̶g̶o̶o̶d̶ ̶i̶d̶e̶a̶ ̶b̶e̶c̶a̶u̶s̶e̶ ̶y̶o̶u̶'̶d̶ ̶g̶e̶t̶ ̶j̶a̶b̶b̶e̶d̶ ̶i̶n̶ ̶t̶h̶e̶ ̶l̶e̶g̶ ̶b̶y̶ ̶t̶h̶o̶s̶e̶ ̶s̶o̶l̶i̶d̶ ̶(̶a̶n̶d̶ ̶p̶o̶i̶n̶t̶y̶)̶ ̶e̶a̶r̶s̶.̶ ̶A̶l̶t̶h̶o̶u̶g̶h̶ ̶i̶t̶ ̶i̶s̶ ̶n̶o̶t̶ ̶p̶o̶s̶s̶i̶b̶l̶e̶ ̶t̶o̶ ̶3̶D̶ ̶p̶r̶i̶n̶t̶ ̶i̶n̶ ̶m̶u̶l̶t̶i̶p̶l̶e̶ ̶c̶o̶l̶o̶r̶s̶ ̶a̶s̶ ̶o̶f̶ ̶n̶o̶w̶,̶ ̶y̶o̶u̶ ̶c̶o̶u̶l̶d̶ ̶s̶t̶i̶l̶l̶ ̶p̶a̶i̶n̶t̶ ̶t̶h̶e̶ ̶c̶a̶s̶e̶ ̶a̶f̶t̶e̶r̶ ̶p̶r̶i̶n̶t̶i̶n̶g̶.̶ ̶I̶ ̶w̶o̶u̶l̶d̶ ̶a̶l̶s̶o̶ ̶l̶i̶k̶e̶ ̶t̶o̶ ̶m̶e̶n̶t̶i̶o̶n̶ ̶o̶n̶e̶ ̶o̶f̶ ̶t̶h̶e̶ ̶m̶i̶s̶t̶a̶k̶e̶s̶ ̶t̶h̶a̶t̶ ̶I̶ ̶m̶a̶d̶e̶ ̶o̶n̶ ̶m̶y̶ ̶p̶h̶o̶n̶e̶ ̶c̶a̶s̶e̶;̶ ̶t̶h̶e̶ ̶c̶a̶s̶i̶n̶g̶ ̶i̶t̶s̶e̶l̶f̶ ̶w̶a̶s̶ ̶m̶a̶d̶e̶ ̶a̶ ̶b̶i̶t̶ ̶t̶o̶o̶ ̶t̶h̶i̶c̶k̶!̶ ̶I̶ ̶c̶h̶o̶s̶e̶ ̶a̶ ̶0̶.̶1̶ ̶i̶n̶c̶h̶ ̶t̶h̶i̶c̶k̶ ̶c̶a̶s̶e̶,̶ ̶a̶n̶d̶ ̶a̶ ̶p̶r̶o̶b̶l̶e̶m̶ ̶I̶ ̶e̶n̶c̶o̶u̶n̶t̶e̶r̶e̶d̶ ̶w̶a̶s̶ ̶p̶r̶e̶s̶s̶i̶n̶g̶ ̶t̶h̶e̶ ̶b̶u̶t̶t̶o̶n̶s̶ ̶t̶h̶r̶o̶u̶g̶h̶ ̶t̶h̶e̶ ̶c̶a̶s̶e̶ ̶b̶e̶c̶a̶u̶s̶e̶ ̶t̶h̶e̶ ̶c̶a̶s̶e̶ ̶i̶t̶s̶e̶l̶f̶ ̶w̶a̶s̶ ̶t̶h̶i̶c̶k̶e̶r̶ ̶t̶h̶a̶n̶ ̶t̶h̶e̶ ̶b̶u̶t̶t̶o̶n̶s̶ ̶w̶e̶r̶e̶ ̶t̶a̶l̶l̶.̶ ̶L̶u̶c̶k̶i̶l̶y̶ ̶f̶o̶r̶ ̶m̶e̶ ̶I̶ ̶h̶a̶v̶e̶ ̶d̶e̶c̶e̶n̶t̶l̶y̶ ̶l̶o̶n̶g̶ ̶n̶a̶i̶l̶s̶,̶ ̶b̶u̶t̶ ̶f̶o̶r̶ ̶t̶h̶o̶s̶e̶ ̶p̶e̶o̶p̶l̶e̶ ̶w̶h̶o̶ ̶d̶o̶n̶'̶t̶ ̶h̶a̶v̶e̶ ̶l̶o̶n̶g̶ ̶n̶a̶i̶l̶s̶,̶ ̶I̶ ̶w̶o̶u̶l̶d̶n̶'̶t̶ ̶r̶e̶c̶o̶m̶m̶e̶n̶d̶ ̶m̶a̶k̶i̶n̶g̶ ̶a̶ ̶c̶a̶s̶e̶ ̶t̶h̶i̶c̶k̶e̶r̶ ̶t̶h̶a̶n̶ ̶0̶.̶0̶5̶ ̶i̶n̶.̶ ̶B̶u̶t̶ ̶w̶h̶a̶t̶e̶v̶e̶r̶ ̶y̶o̶u̶ ̶w̶a̶n̶t̶ ̶t̶o̶ ̶d̶o̶ ̶w̶i̶t̶h̶ ̶t̶h̶i̶s̶ ̶i̶s̶ ̶e̶n̶t̶i̶r̶e̶l̶y̶ ̶u̶p̶ ̶t̶o̶ ̶y̶o̶u̶.̶.̶.̶s̶o̶ ̶b̶e̶ ̶c̶r̶e̶a̶t̶i̶v̶e̶!̶ ̶A̶n̶d̶ ̶a̶l̶s̶o̶ ̶i̶f̶ ̶y̶o̶u̶ ̶h̶a̶v̶e̶ ̶a̶n̶y̶ ̶q̶u̶e̶s̶t̶i̶o̶n̶s̶,̶ ̶f̶e̶e̶l̶ ̶f̶r̶e̶e̶ ̶t̶o̶ ̶a̶s̶k̶ ̶i̶n̶ ̶t̶h̶e̶ ̶c̶o̶m̶m̶e̶n̶t̶s̶.̶
[UPDATE]: It's now possible to print in multiple colors using dual extrusion printers like the Ultimaker S5, so that previously impossible Pikachu case is now possible! Oh, you don't need to worry about those "solid and pointy" ears anymore if you use soft flexible filaments. I just love new technology!
If you really don't want to worry about ports, the newest available iPhone (iPhone 11) and all iPhones since iPhone 7 don't have headphone jacks. BUT there are also new phones such as Meizu Zero and Vivo Apex that don't have any ports, jacks, or buttons at all! I may decide to make a case for one of those in the future. Until then, peace.
P.S: I dropped my phone twice during the making of this phone case. I dropped it once while measuring it and again after I put the case on.
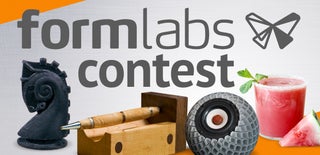
Participated in the
Formlabs Contest
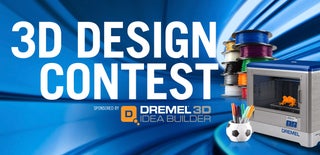
Participated in the
3D Design Contest
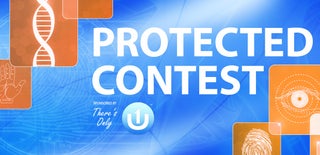
Participated in the
Protected Contest