Introduction: 3D Printed Stone Head
3D Printing is awesome. But after printing out lots of fun things with my 3D printer, I got sick of them all looking like they came from a 3D printer. Relatively inexpesive FDM printers always have layer lines that you can both see and feel. I wanted a final product that nobody would expect was 3D printed. I had a few small prints of an Easter Island moai head, and then it hit me. Without having to carve any stone, I was going to make a stone-like replica that would look great sitting in the yard.
Step 1: Materials
-3D printer with filament
-A 3D model to print
-Plastic Primer
-Autobody Filler Primer
-Sandpaper (200 grit)
-Stone textured spray paint
Step 2: 3D Print Stone!?
I know what you're thinking. You can't 3D print stone... at least not yet. My plan was to 3D print my object and give it the most realistic stone finish I could manage. The first step of course, was to make the print. After poking around on Thingiverse I found quite a few versions of these moai heads. This one was my favorite because of the cleaner look, although it might be a little less realistic.
https://www.thingiverse.com/thing:2422543
I downloaded the file and printed it as big as my Robo 3D would let me. (Make sure to use supports when printing something this large with this many overhangs. )
Attachments
Step 3: Coating
Now begins the process of smoothing out the lines. I wanted to be sure they were completely invisible on the final product. In the past I've tried to sand the surface of the plastic itself. The results were not pretty with PLA. If you were to print this with ABS you could use acetone to smooth the surface of your model. There are tons of tutorials out there on how it can be done. My method was more of an additive approach.
The first thing I did was to use a plastic primer to ensure any later coats would adhere properly. Then came the automotive filler primer. This allows you to build up the surface enough to sand it down. I used about 3 or 4 coats of this before I started sanding. Besides waiting around for paint to dry, the sanding took the longest. 200 grit sandpaper works well because it removes quite a bit of material at once. It does leave visible marks, but nothing that you'd be able to see after texturing.
Step 4: Texture!
After the model is beautiful and smooth looking, it's finally time for the stone texture. I had a serious problem with the packaging of Valspar brand of stone texture spray. When it was time for me to do the spraying, the spray tip broke off stuck inside the cap. I headed out to the store to get another can. This time I made sure to check the cap in the store. The first can I checked had the same problem, and so did the second. It seems to be a manufacturing issue or a design flaw, so be sure to check first if you decide to try this.
Finally it was time to spray! Following the instructions on the can it took 2 coats to get a good look, and a follow up coat to get some spotty areas. There is still plenty left in the can too.
Step 5: It's Done!
I was really pleased with the final look and a few people who I showed it to had no clue that it was 3D printed. They were convinced it was stone until they held it. It looks awesome in the backyard or in the garden. But it's going to need some clearcoat before it can spend too much time outdoors.
I found this really easy to make. I may have complicated it even more than necessary too. The stone texture spray turned out to be VERY thick. It might be entirely possible to directly spray the stone onto the 3D print right off the bed. I intend to try a few more options for some slightly different results. I hope you enjoyed this, and maybe it's given you some ideas of your own. If you try it, please post some photos!
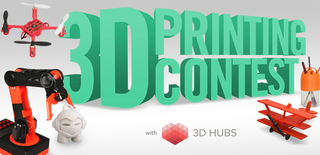
Participated in the
3D Printing Contest
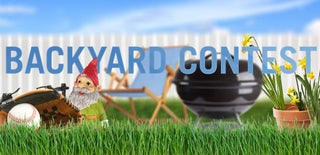
Participated in the
Backyard Contest
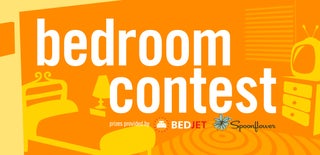
Participated in the
Bedroom Contest