Introduction: 3D Printed USB Case
The USB I use for most things had a not very well designed key ring attachment point, and it ended up breaking, so I can no longer attach it to my keys.
To fix the problem, I could have just bought a brand new USB that was better designed for a key ring, but that would have been wasteful. There was nothing to all wrong with the actual USB circuit board, so why waste resources and contribute to the growing mentality that "If it's broken, throw it out and buy a new one"
Instead, I modelled a new USB Case in a 3D modelling software and 3D printed it, fixing the problem
I have entered this project in the Fix It! Contest!, so please vote for me.
Disclaimer: I will not be held responsible for any damages or injury with tools or machinery shown in this Instructable.
Step 1: Design
I had complete freedom over the new design. It didn't need to look like a USB if I didn't want it to.
In saying that, when designing something like this, there are the size constraints of the USB circuit board and the 3D printer capabilities, but I will talk more about them later.
I knew that I wanted the USB to have a sleek, almost futuristic appearance. I started by sketching my ideas on a bit of paper.
Some of the sketches are pretty bad, while others I quite liked the shape. This is normal though in the design process. You have to record even the bad designs or iterations, because they all help you to reach the resolved design you set out to achieve.
Once I was happy with the design, I was able to start the modelling process.
Step 2: 3D Modelling
I used Rhinoceros 6 for Windows as my modelling software, as that is what I had learnt to use at Uni and had access to.
Some other alternatives to Rhino are :
Fusion 360
3ds Max
Sketchup
These programs all share similarities and some are easier to learn than others, but they all have their benefits. It pays to do some research into what you want
I began by drawing the USB outline as a series of arcs, defined through control points. This allowed me to drag the control points and reach the shape I wanted.
Then I created a surface from that, to then extrude to the correct dimensions. This created a 3D shape. Once you have a 3D shape, you can then use the control points to drag and manipulate the shape until the shape matches what you want.
Because the case had to fit the USB as well, I modelled the dimensions of the USB Circuit board and extruded that to be a solid object so that I could use a Boolean operation to create the shape of the case that had a slot for the USB.
To create the key ring hole I drew a tube that was the same diameter as the key ring I wanted to fit it on. The tube was 4mm thick by 6mm wide. This slightly oversized size was to account for the offsets of the 3D printer.
To fit the three shapes together, the USB case, the Tube, and the USB circuit board, I used Boolean operations. A Boolean operation is a mathematically defined operation that that allows the adding, subtracting or intersecting of solid objects.
The USB case and the USB chip Model were joined together with a Boolean Union function.
This shape was then joined to the Tube with a Boolean Difference Function.
The final shape had 2mm edge fillets applied to it to round over the edges.
To check that the object was a solid watertight object I used a Volume Function. The program told me the volume of the shape, which means that it watertight, all joined together, and 'holds' volume. If the volume tool did not work, then I would have had to begin trouble shooting it.
Step 3: Preparing for 3D Printing
The file needs to be saved as and STL or STereoLithography.
The model needs to be selected and then depending on the modelling program, the Export Selected tool can be used.
I used a 0.01mm Tolerance
Do not export open objects (they should all be closed for printing, another way to check it will work)
Binary File type
I opened the stl. file in MakerBot.
Makerbot allows you to orient the part for printing, preset some of the machine settings, set the print layer height, thickness etc.
The smaller the Layer Height in a 3D print, the less lines visible, and the cleaner and more detailed the print. The smaller the layer height also means the longer it takes to print, so you need to take that into consideration.
The settings I used for the print:
25% Infill with a Hexagonal Pattern
1mm Roof and Floor Thickness
0.1mm Layer Height
3 Shells
Step 4: Printing
Once the file is saved from MakerBot, with the correct settings and the correct printer etc, it is ready to print.
I loaded the file onto the Makerbot Replicator Z18 printer and set it printing.
Ironically, I was still using the same USB, so the USB was printing it's own new case...
It took approximately 3.5 hours to print.
Step 5: Problems and Trouble Shooting
If you picked it up from the previous images, you noticed my mistake. I printed the USB case in the wrong orientation.
I printed it the first time horizontally. But the USB case has a slot in it for the USB circuit board.
This means that for the first layer of that slot, the printer is trying to establish a solid surface in mid air. This caused drooping, and made the slot smaller than it should be.
I printed it again, but vertically, this time the printer not having to print any part of it in mid air.
This worked a lot better!
Step 6: Paint Prep
When the print was finished, I removed it from the build plate and removed the supports. I pressed the USB circuit board into the slot, and it fit with a very good friction fit, so I did not have to glue it in.
The PLA filament sands reasonably well with normal timber sandpaper - Just remember to wear a mask!
I sanded down the print edges and the ridges formed when printed.
I then filled the surface with a 2 part builders bog and sanded once more.
I taped and masked off the metal USB part and then taped the case to a paddle pop stick so that I could hold it while painting all sides of it at once.
I applied 3 coats of a grey spray paint primer, sanding with 600 grit wet and dry paper in between.
Then I applied 4 coats of a beautiful green spray paint, again, sanding in between each coat.
The USB case was then left to cure.
Step 7: Thoughts on Drying Vs Curing
The terms 'drying' and 'curing' are often used interchangeably when it comes to painting, varnishing or finishes.
They are not, however, the same thing.
The more accurate term is 'touch dry'. When a solvent based finish goes through its first stage of transitioning from a liquid to a hard strong protective, solid layer, it becomes touch dry. This can happen after a few minutes, a few hours, or even after a few days. It depends on the type of finish, the manufacturer, the weather conditions etc.
A finish will become 'touch dry' when the solvent evaporates. This leaves the pigment, or colour on the surface as a layer that feels 'dry' but is still very very fragile and weak.
As the finish 'cures' it undergoes chemical and physical changes, often reacting with the air to form a hard finish. This process takes much much longer, in many cases, a minimum of a month.
This is an important distinction to make, because if I tried to put the key ring on the USB case when the paint had just 'dried' it would have completely scratched and removed the paint.
I had to wait until the paint had cured, and was hard enough to withstand the metal ring moving against it.
Step 8: Limitations
With the extrusion head the 3D printer I used has, the minimum thickness I could extrude is 0.1mm.
This is a tiny amount, but when compared to the relationships between the edge thickness and the USB circuit board, it is not enough.
I originally designed the USB shape, but upon measuring the distances and wall thicknesses, realised that the shape would have to be proportionally enlarged to be printed with a 3D printer.
I printed another one of the original size, to show the ideal size and shape it would be if made through injection moulding or another similar process, rather than the 3D printed additive process.
This is not knock on 3D printers, but really shows some of the limitations they have, which in turn, present design challenges that can be resolved and furthered into something better and more innovative.
Step 9: Finished
With the metal ring installed on the 3D printed key chain, the only thing left is to attach it to my keys.
With the advancments in the 3D printing technology, access to modelling software, and a 3D printer, I was able to fix the problem of my USB not being able to attached to my key ring, by myself, with out having to purchase a new USB.
Obviously this process greatly depends on your accesses to a 3D printer. A 3D printer can be bought rather cheaply these days, but if you don't think you'll use it very much, then a better option might be to find a local makerspace or library with a 3D printer. These places will also have the software and knowledge to help you facilitate your project.
I have uploaded the stl. file I used. Feel free to print it, but it may not fit all USB's so download some software and have some fun playing around!
I hope you enjoyed this Instructable.
I have entered it in the Fix It challenge, so please vote for me.
Mark
Attachments
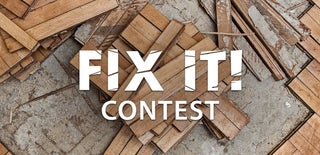
Participated in the
Fix It! Contest