Introduction: 3D Printer Part Recycling Grinder
I was getting tired of cutting up failed parts and my research materials by hand. So I decided I wanted a part grinder to compliment my Filastruder. There are a few options for grinding up failed printed parts for turning them back into filament. I didn't want to spend $500+ dollars and also wanted something that was more effective than the other low cost DIY solutions I've seen. I don't have access to a machine shop anymore so I had to make something in my garage with somewhat basic hand tools. The design is based around this tooling restriction. It is smaller than I would have liked and took about 40hours to build.
The design relies on the plates for the spacing of the cutting faces (which are the most important part). The other faces are not as critical, so cutting using templates is accurate enough. The design is intended to be expandable in the future to grind up larger parts, and hopefully switch to a dual blade design.
The manufacturing technique I used is incredibly labor intensive and fairly time consuming. I feel most people who are capable of this kind of work will already own some of the tools I would've preferred to use. But for those of you who are poor and hate themselves just like me I'll go through the steps I took to build this grinder.
Disclaimer: If you choose to build this you will soon understand I am not joking about hating yourself. You will be sweating and bleeding a lot during the massive amount of time you will be working on this. Hand sawing and filing is a very slow and very labor intensive process. You need to be capable of high intensity work for hours at a time. If your not, you will be a lot stronger by the end of this project or you will give up. Don't start this without assessing your own physical and time limitations.
Step 1: Design
I designed this grinder in Inventor. It is designed to cut similar to scissors with a progressively forward closing cutting faces. The end of the scissor faces has an acute angle to stop material from sliding out and not getting cut. It only has one set of moving blades for simpler manufacturing and construction. The design assumes the material always has the same thickness. So the only features that needs to be added are in a single plane. All the plates are held together with more bolts than are necessary to increase stiffness.
DXF files of the flat parts and Step files of all parts are included in the zip file.
Step 2: Tools and Materials
These are the tools and materials I used to complete this project.
Tools:
- Vice
- Drill press
- Drill index (I used a cheap harbor freight set)
- Wire wheel
- Hacksaw (and a few blades)
- Bastard file
- Half-round bastard file
- Triangular bastard file
- A few needle files
- Bronze brush to clean files
- Center punch
- Sledge hammer
- Rotary tool (and some abrasive discs)
- Ratchets and Sockets
- Some Pliers
- Crescent wrench
- Some clamps
- Printer
I would've preferred to have had a few more tools that would have removed most of the labor from this project. These are a band saw and a belt sander. This project would be relatively easy with both of these.
Materials:
- 3/16" x 3" x 48" mild steel stock (~$20, I had to buy two 36" bars at $17.95 each)
- 1/2" x 12" mild steel round stock ($5.77)
- 1/8" x 1/8" x 3" mild steel stock ($2.21)
- (2) 1/2" bearing 2-bolt pillow block flange (I bought this one, $21.35 for two shipped)
- (2) 3/8"-16 x 4" steel bolt
- (4) 3/8" steel washer
- (2) 3/8"-16 steel nut
- (4) 1/4"-20 x 3" steel bolt
- (8) 1/4" steel washer
- (4) 1/4"-20 steel nut
- Paper
- Glue
- Rubbing alcohol
The fasteners totaled about $3.00. To build the whole thing the cost of materials was about $52.
Step 3: Print, Cut, and Paste
Print out 1:1 scale drawings with hole centers marked. Make sure to print enough for a cut out for each part that needs to be made.
Cut out each part along the outer edge of the geometry. Don't cut out the holes because the center lines are needed later.
Now test layouts of the templates to decide which will work best to minimize cutting and/or waste material. Once you have decided how to lay them out clean the surface using a mild solvent such as alcohol. The surface needs to be cleaned thoroughly or the glue won't stick. Completely cover the back of the templates (including the edges) in glue to ensure it does not move during later operations. Place the template onto the clean steel surface and lightly press them flat. DO NOT press or slide the paper to hard or you will introduce dimensional inaccuracies.
Now wait 10-15 minutes for the glue to dry before moving to the next step.
Step 4: Cut and File Parts
After the glue has dried the parts are cut out with the hacksaw. The goal for cutting is to remove as much material as possible to minimize the amount of filing needed to finish each part. Leaving 1-2mm around the perimeter was the goal for me before I began filing. It takes some practice and a lot of patience to cut close but not too close to the final dimensions. The sawing can also be quite tiring so take a lot of breaks and switch to filing for some time to rest your arm.
Once you have cut in an edge filing is done in two steps. First use the more aggressive half round bastard file to remove material quickly. Then use the flat bastard file to flatten and improve the surface consistency. This will also take some practice to do quickly and accurately. The most important thing to do while filing is maintain the flatness of the surface you are filing. If you file of the edges in an attempt to move faster it is easy to remove too much material and to get the face perpendicular to the plate face again.
Step 5: Drilling Holes and Removing Templates
I have a small drill press in my garage, but this step can also be done with a hand drill. I chose to use my drill press because I didn't want to wait for batteries to charge constantly. It still chatters a lot and the finish and accuracy was similar to that of a hand drill.
The steps to drill the holes are:
First use a center punch to start each hole.
Drill a smaller pilot hole, I used 1/8".
Using a file, clean up the burs on the back of the part after drilling.
Drill the larger hole.
- Again, use a file to clean up the burs.
To make drilling easier use cutting fluid. A heavy engine oil works well for this. I didn't have a heavy weight and just settled for 5W-30. Use a cheap paint brush and a tin can to avoid making a mess.
After all the features have been added to a part, the template can be removed. This was done by grinding it off using a wire wheel. Do not remove the template from the cutting blades yet, they need to have key ways added.
Step 6: Cutting Keyways and Hex Flats
The keyway in the shaft is made using a rotary tool and a small abrasive wheel. Slowly work the slot down and check its dimensions against the key you already cut. I rounded off the corners of the key that are in the shaft to make fitting easier.
The keyways on the blades are made by filing out the bulk of the material using a more aggressive triangular file. Then finishing them up with some needle files. Test fitting along the way until it fits perfectly over the key. Each blade needs to be at a different angle, so make sure to put the keyways at 90 degrees to eachother.
To make the hex drive on the end of the shaft you need to add flats that are 7/16" apart and 120 degrees separated. I don't have a special trick for this. File one flat. Move to the other side and file a flat parallel to the first. Measure the distance between the flats and remove material evenly from each side. Now file the other ones. Use a deep socket to determine how close you are. You should be able to see if you are parallel to the flats in the socket. Keep filing the parts the socket runs into until it fits.
Step 7: Fitting and Assembly
Now that the parts are all cut to shape they can be final fitted together. This is not an exact manufacturing process and the bolt holes are only drilled to standard fit, so it is likely that there are going to be holes that don't align properly. To compensate for this some of the misaligned holes are drilled out to the next largest size.
Steps:
- Stack the plates in the order they will be when assembled.
- Attempt to thread one of the bolts through.
- Mark where the bolt stopped with your finger.
- Hold the bolt next the outer faces of the plates to see which plate it stopped at.
- Drill out the hole to the next largest size you have.
- Repeat with each bolt until everything fits.
I don't have any pictures of how to put the blades and shaft in. It isn't too difficult though. I did it by leaving the 3/8" bolts in and spinning the plates out of the way. The sliding in the shaft into place, followed by the blades and spacers. Spin the outer plates back in and mesh them with the blades. (I need to add some pictures of this, I'm just happy with it being assembled right now)
Step 8: Testing and Final Thoughts
After some testing the grinder showed it is capable of cutting up some printed parts. I able to cut fairly thick (~1/4") solid printed PLA walls. I didn't test anything but PLA because I don't have anything else. But it should cut most of the common printed plastics. It may have trouble with polycarbonate.
The downside to this design is the maximum part size that it can bite into is small. The blades separate to about a 0.5" square opening. Which only allows very small parts or some pre-cutting to get the blades to bite. This was sort of intentional because the Filastruder works much better with small pellets. And to get smaller pellets the opening size was reduced. If I were to redesign it I would make the blades longer to allow larger pieces to be cut without the need to pre-cut.
Now I need to figure out the best way to mount it so something. I didn't have a plan for mounting when I started this, but it shouldn't be too difficult to add more holes for a good mounting solution.
If someone wants me to add something I'd be more than happy to. I am fairly new to righting the things down that I do, so any suggestions would be helpful.
EDIT: Added a video and photo of grinding PETE. While doing this I found a flaw in the design that I'll discuss in the next step I'm adding.
Step 9: Future Work
While grinding PETE some of it became wedged in a few places and required the grinder to be disassembled. One of the blades spins flat against the outer wall and plastic wedged into the gap. It could get into this gap because I couldn't tighten the plates as much as was needed. This was caused by the plates all being the same thickness and some of them collided when tightened. I came up with two things to fix this problem:
- Lapping the faces using grinding compound. I did this and it worked very well at reducing binding with minimal surface pitting.
- Adding another set of stationary cutting blades to space all of the blades off the outer walls. I think I'm going to do this and it will remove the binding issues.
Another problem that became apparent after testing with the flat PETE was the material getting hung up on stationary blades. This explains why almost all commercial material grinders use counter-rotating blades. I might iterate on this design to improve the grinder's ability to handle strange shaped and larger parts. For now it fulfills my needs of making small parts into small enough bits for a Filastruder.
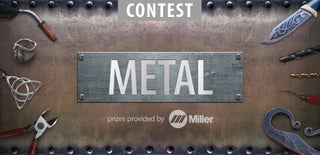
Participated in the
Metal Contest 2016