Introduction: 3d Printing Servo Controlled and Other Valves
Very functional valves that can control air or water can be easily 3D printed. I am mainly using them for the control of artificial air muscles for robots, but they can be used in many situations where a small and inexpensive valve is needed.
This instructable shows how to make micro-servo controlled valves, gate valves, check valves, and adjustable flow valves. Intro pic shows all the valves.
Step 1: How It Works
I believe that the future of robotics will involve the use of soft artificial muscles that are powered by air pressure. To control them, various kinds of valves are necessary. Most of these 3D printed valves work by pinching or kinking a soft silicone tubing. All of the valves have been tested at 30 PSI but will probably work at higher pressures.
In the case of the servo controlled valve, it is actually 3 valves controlled by one servo. They can be all off or they can be opened one at a time. A cam that presses against a cam-follower is rotated to open the valves. As shown in pic 2, the servo controlled valve can replace 3 conventional solenoid valves.
It does this at a much smaller volume, weight, and cost. The servo controlled 3 valves can be made for about 7 dollars, while the conventional solenoid valves typically cost about 20 dollars each. The servo controlled valves also use considerably less power than the solenoid valves.
Step 2: Supplies
3D filament printer
PLA filament- Available from: http://www.3dxtech.com/pla-filament/
or from: http://www.protoparadigm.com/advanced-ingeo-pla/
These are the two best places to buy PLA that I have found so far. They have great colors, uniform filament that does not jam, and the best prices for a quality filament.
Loctite Vinyl, Plastic and Fabric flexible adhesive- available from Amazon or Ace hardware.
MEK solvent-available at Ace hardware or online.
100% silicone caulk
corn starch
2 feet of 1/8" O.D. Silcon Med-X silicone tubing and 1/16" I.D. nylon tube fittings-available from: http://www.usplastic.com
1 foot of 1/8" vinyl tubing available from: http://www.usplastic.com
4-40 nut and bolt available online.
1/16" or 1/8" thick sheet acrylic available online.
Tower Pro SG92R micro-servo available from: http://www.adafruit.com/products/
Step 3: 3D Print a Servo Controlled Valve
The servo controlled valve is actually 3 valves. They can be all off or they can be opened one at a time. A cam that presses against a cam-follower (camfollower.stl) is rotated to open the valves. The servo controlled valve can replace 3 conventional solenoid valves. It has been tested to over 4000 cycles and did not show significant wear on the parts.
Pic3 shows how a cut down servo horn slots into the cam.
Pic4 and pic5 show the valve closed and under 22psi pressure and then open to activate a 3d printed artificial muscle.
Print The Valve
A Makerbot Replicator 2 was used to print this and the other valve parts. Here are the settings:
Infill: 10 per cent
Shells: 2
Layer Height: .2mm
Temp: 230 C
Speed Extruding: 90 mm/s
Speed Traveling: 150 mm/s
No raft and no supports.
Step 4: 3D Printed Gate Valve
The gate valve consists of a housing with a slide bar that manually kinks and unkinks the 1/8" silicone tubing. It has been tested to 30 PSI but will probably work at higher pressures.
The pics show the valve closed and opened.
Step 5: 3D Printed Check Valve
The check valve lets air or liquid flow one way only. It consists of two 3d printed housing parts that are glued together with a thin piece of acrylic between them. The acrylic has a 1/16 inch hole drilled in it. A thin cast membrane of silicone is loosely placed in between the acrylic and one of the housing parts. The silicone is cast using the form that is 3d printed along with the two housing parts. Two part silicone or Oogoo can be used to make the membrane.
Once the housing parts are glued lightly with fabric glue to the acrylic, the vinyl tubing is inserted and the whole thing dipped in fabric glue that has been thinned with MEK solvent: 3 glue to 1 MEK by volume. Let it dry for an hour and then dip it for a second time to get a good seal. Do this outside or under a fume hood as the fumes are not healthy to breathe.
Let it dry overnight before testing. Step 5 pic shows all the parts and an assembled check valve.The acrylic plate was left larger than necessary so that its position is apparent.
Attachments
Step 6: 3D Printed Adjustable Flow Valve
The adjustable flow valve uses the same principal as the servo valve where a cam follower pinches the tube until it shuts. In this case, the pinch is adjustable by a 4-40 screw with a captive nut to give it a variable flow control.
Step 7: Other Possibilities
Scaling The Valves Up
The valves were designed for 1/8 inch silicone tubing in order to make them as small as possible and still have good air flow. They can probably be scaled up to use larger diameter silicone tubing. Larger tubing usually has a thicker wall, so more force will be required to pinch them. For the servo valve, a larger servo would be required and the servo base and cam would probably need to be modified.
Step 7 pic shows a soft robot gripper and artificial muscle that is in development and can be controlled by the servo valve in this instructable.
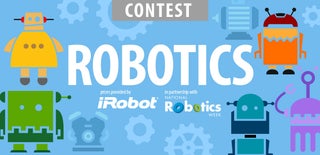
Participated in the
Robotics Contest 2016
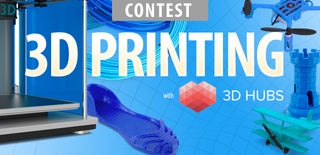
Participated in the
3D Printing Contest 2016
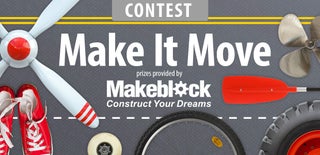
Participated in the
Make it Move Contest 2016