Introduction: 3d Printing: Zizzy-A Robot Assistant
Zizzy is a personal robot prototype for people with limited mobility. The head, body, arms, mounting brackets, air valves, and the artificial muscles that actuate it, are all 3d printed. While no one is likely to try and duplicate this robot exactly, the body and arms, muscles and muscle control system, could be useful in other robotic projects.
The intro pic shows how the robot could operate a cell phone. In practice it would probably be much easier to control a phone by putting the phone on a fixed stand and then remote controlling the arms and drive motors to select icons. A thin wire would have to be attached from the person to the stylus to provide the activating capacitance.
The video shows the robot in a pre-programmed sequence--picking up a water tube and power bar and taking it to the edge of the table. From there it could be remote controlled to feed the person in control of it. As the video shows, the compressor is fairly loud. I am trying to find small battery operated compressors that are less noisy. If anyone knows of a source, please let me know.
Step 1: How It Works
Zizzy the robot is designed to move freely on a smooth desktop or table. The two arms can be used to pick up objects and move them to the person controlling it. It could be used to provide medicine, food and water or manipulate a phone or other device. The voice circuit could be used to facilitate communication for those with limited or no speech. The face is basically an emoticon that could be used to display emotions.
It can be remote controlled using infrared signals from a standard universal remote control. An infrared remote control could easily be modified to interface with a wheel chair, puff and blow, eye tracker, or other controller. This would allow the user to remote control all motions or to activate pre-programmed sequences.
Modular Construction
This robot uses modular construction with the muscles and grippers able to plug in and out to allow for easy replacement or upgrades whenever a better design becomes available. The talking circuit and Master neuron also plug in and out to allow for upgrades or to use them in other robots.
The Future Of Robotics
I believe the future of practical and affordable robots will involve soft artificial muscles such as those used here. They are lighter and less expensive than the standard gear motors and power servos used for most present day robots. They are also less dangerous around humans as they have a certain amount of built in give if they push against a human. While some gear motors and servos will still be necessary, many can be replaced with air powered artificial muscles.
While much is made about the purely soft robots that have little or no bone structure, my experiments have shown that a fairly stiff skeleton with flex or hinge joints is necessary with soft robot muscles to get precise movements that are repeatable.
Step 2: Materials
Access to a 3D printer, I used a Makerbot Replicator 2
Ninjaflex filament available from: http://www.adafruit.com/products/
PLA filament- Available from: http://www.3dxtech.com/pla-filament/ or from: http://www.3dxtech.com/pla-filament/ These are the two best places to buy PLA that I have found so far. They have great colors, uniform filament that does not jam, and the best prices for a quality filament.
4 tubes Loctite Vinyl, Plastic and Fabric flexible adhesive- available from Amazon or Ace hardware.
MEK solvent-available at Ace hardware or online.
3 Picaxe microcontrollers available from: https://www.sparkfun.com/categories/new_products
12 volt air compressor available from: https://www.sparkfun.com/categories/new_products
Motor controller available from https://www.pololu.com/category/42/new-products
Sparkfun micro sd card audio module available from Sparkfun or https://solarbotics.com/
Various standard electronic parts-see the schematics for details.
Universal remote control-infrared set to Sony code.
20 feet of 1/8" O.D. Silcon Med-X silicone tubing and 1/16" I.D. nylon tube fittings-available from: http://www.usplastic.com
20 feet of 1/8" vinyl tubing available from: http://www.usplastic.com
Vacuum guage 0-30PSI, available from Ace hardware or online.
Plastic dome transparent to infrared, from a dummy camera housing available from sciplus.com If no longer available, a half dome to fit could easily be 3d printed.
24- 4-40x1/2 inch nuts and bolts available online.
2-Futaba servos-s3110 or s3114 available online.
5-Tower Pro SG92R micro-servo available from: http://www.adafruit.com/products/
12 volt, gear motors, 20 rpm-available from: http://www.jameco.com
3.7 volt Polymer Lithium Ion Battery - 2000mAh, available from: https://www.sparkfun.com/products/8483
Polymer Lithium Ion Battery - 1000mAh 7.4v- available from: https://www.sparkfun.com/products/11855
Step 3: 3D Printing the Robot Arm
All 3D printed parts were easily designed using the free and excellent 123D Design program from Autodesk--Beta version. Too bad it is no longer available. The newer free versions, while stripped down and less intuitive, are still extremely useful.
The robot arm is printed in one piece using PLA. It contains four built-in hinge joints. The air powered artificial muscles are printed in Ninjaflex and after they are sealed, they simply pop into the sockets built into the arms. A micro servo slides in and a single bolt holds it in place to rotate the wrist joint.
Step 4: 3D Printing the Soft Robot Artificial Muscles
Printing The Muscles in Ninjaflex
There are three different types of muscle. The gripper, elbow and top rotator muscle are different. The elbow muscle is the same as the shoulder muscle.
Print The Muscles
A Makerbot Replicator 2 and Ninjaflex was used to print the muscles. Here are the settings:
Infill: 10 per cent
Shells: 2
Layer Height: .2mm
Temp: 235 C
Speed Extruding: 30 mm/s
Speed Traveling: 150 mm/s
No raft and no supports.
To be of use, the artificial muscles must be sealed by dipping in the fabric glue twice. The glue should be thinned down with MEK solvent at about 2 parts MEK to 8 parts glue by volume. Attach a piece of vinyl tubing to the inlet socket and then dip once, let dry for an hour and then dip again. After 24 hours test under 20 PSI pressure and if it leaks underwater, dry it and then dip a third time.
For more details on sealing the muscles see here: https://www.instructables.com/id/Soft-Robots-3D-Pr...
Step 5: 3D Printing the Robot Body
The head, upper torso, lower torso and arms and brackets were printed in PLA.
They bolt together using 4-40 nuts and bolts with the nut held captive on the inside using silicone caulk.
Pic2 shows the bottom and the two gear motors along with the servo controlled wheel that allows turning.
A Makerbot Replicator 2 was used to print the body parts. Here are the settings:
Infill: 10 per cent
Shells: 2 Layer
Height: .2mm
Temp: 230 C
Speed Extruding: 90 mm/s
Speed Traveling: 150 mm/s
No raft and no supports.
Attachments
Step 6: 3D Printing the Soft Robot Gripper
The gripper was printed with Ninjaflex using the same settings as the muscles.
The gripper is designed to be easily slid out so it can be replaced by newer designs.
The grip frame is printed in PLA.
Step 7: The Valve System
The servo controlled valves and valve bracket were printed with PLA using the previous printer settings. I did a whole instructable on how to print the 3 valve controllers. You may have to cut off the top valve of the controller to be able to fit it in the torso.
See STLs and details on the valves here:
https://www.instructables.com/id/3d-Printing-Servo-...
For now, the robot is tethered to a separate 12 volt air pump. I hope to eventually find a small quiet pump that can be mounted on the back of the robot.
Attachments
Step 8: The Master Robot Neuron
The master robot neuron is a 20m2 Picaxe microcontroller that controls the artificial muscles and drive motors. Eventually it will be networked with the other microcontroller that are onboard. Step8 pic shows the master neuron circuit attached to the valve bracket.
I have been experimenting with microcontrollers networked as very simple robot neurons. See here for details:
https://www.instructables.com/id/Tinkertrons-Make-A...
Much more programming needs to be done to get full control of the robot. I have only scratched the surface. Programming artificial muscles turns out to be fairly tricky and very time consuming. Look at master.txt to see the Picaxe code so far.
Attachments
Step 9: The Robot Head
The least threatening and most attractive robot heads tend to be a combination of futuristic and cartoonish design. The robot Asimo is a good example.
This robot head is still undergoing development and for now only has basic functions activated. The eyes light up and it can smile. A servo can control the mouth from a smile to a frown. It may be the subject of a future separate instructable.
Head.txt has the code that you can copy and paste into the Picaxe editor.
Step 10: The Talking Circuit
The sparkfun micro sd card audio module can play back converted wave files saved on an sd card. Up to 99 files of words or phrases can be played back by a standard universal remote control set to Sony code. With additional programming, up to 999 files could be played.
A 20x-2 Picaxe is used to control it by infrared or serial input. Many thanks to the folks at the Picaxe Forum for providing the tricky interface program code.
See the Sparkfun or Solarbotic website for details on its use.
See talk.txt for the Picaxe code.
Step 11: Other Possibilities
Adding Sensors
Step11 pic--Eventually I hope to add a sensor scanner on top of the head so it can automatically locate people and objects using infrared or ultrasonic sensors rotated by a servo. Sensors may also be added to the grippers to more precisely pick up objects.
Scale it up
After experimenting with this robot, if another version is built, I would scale up the whole thing about 20 per cent to have room for stronger muscles. The arms and body could be scaled up fairly easily by enlarging the STL file. The muscles, however, would have to be redesigned as the wall thickness is critical to avoid delamination.
More Precise Movement
More precise movement could be obtained by refining the programming and varying the compressor pressure. I have not had time to work on that yet.
Less Noise
As the video shows the compressor is fairly loud. I am trying to find small battery operated compressors that are less noisy. If anyone knows of a source, please let me know.
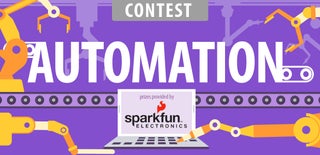
Runner Up in the
Automation Contest 2016
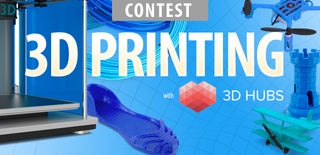
Participated in the
3D Printing Contest 2016