Introduction: 8 Ft Room Organizer
I recently took on a project that required a work area large enough to house test instruments, computers and other objects, as well as provide a longish work surface. I wasted time trying to find something suitable on the web. Everything seemed either too expensive or too flimsy or both. So I set about creating an 8 foot long work area from scratch. Why 8ft? Because that was the space available!
One of the things I realized while constructing an 8 ft long organizer is that it gets heavy fast and maneuvering it into a house, especially up a flight of stairs, presents a major challenge. The final design was therefore constructed in parts for assembly in it's allocated resting place.
Step 1: The Stuff
The organizer framework is built from 2x4's using pocket-hole screws and glue. I had a number of 2x4's in my garage that had been used to create a temporary paint booth so my additional purchases were minimal. The plywood shelving was also made from random pieces of 1/2" plywood that I had in my scrap pile. The overall spend on the project was under $60. The biggest expenses was the counter top and the screws. And of course, I already had all the tools...
Materials
- 2x4x96 construction lumber. You will need 9 pieces. This project will be a lot easier if you make sure the lumber is straight. I had a tough time with mine because some of it was twisted and bowed from getting wet during their previous life as a spray paint part hangers.
- 100 x 2-1/2" pocket hole screws. I use the Kreg Brand simply because that's what my hardware store stocks. They are good quality but a little spendy...
- 15x96x21/32 counter top. I used the cheapest top I could find. It ran $20.
- Offcuts of 1/2" plywood to make the shelves. You will need the following sizes
- 8" x 19 3/4" Qty 2 for the 2 shelves on either end
- 10" x 40" Qty 1 for the central shelf
- 8"x2"x3/4" whitewood strips. This will be ripped down the middle and be used to create a thicker edge on the counter top so that it looks better, and the remainder will be used to create ledger boards for the shelves to rest on
- 3d 1-1/4" nails for securing the ledger boards
- Wood glue - all joints are both screwed and glued. Some might say overkill!
Tools
- Pocket hole jig. I use the Kreg Jig. I've had this jig for easily 6 years and have built a home full of cabinets with it. It's really well made and just works. It makes woodworking accessible to people like me with limited woodwork joinery prowess!
- Electric Drill for making the pocket holes. A battery powered drill will require frequent battery replacement - you will be making in excess of 100 pocket holes so electric is the way to go.
- Battery powered drill or screwdriver for driving the screws. Make sure you have a torque setting so that you don't strip screws out of the wood. 2x4's are strong, but no match for a screw driven by a power tool.
- A miter saw for cutting the 2x4's to length. You could get the 2x4's cut at the hardware store although they frown on making too many cuts. My local Home Depot has a sign up that limits the number of cuts per customer....
- A circular saw for trimming shelving boards as well as for ripping the 8x2x96 whitewood strip
- Safety glasses to protect your eyes from flying wood splinters and chips.
- 3 ft wood clamp
- Random Orbital Sander or sanding sheets or sanding sponge
- Paint and primer - your choice. I had left over ceiling paint that I used as a primer (it covers really well) and left over white trim paint.
Please be careful. Power tools can cause major bodily harm. You don't want your weekend project to require a trip to the emergency room. Please pay attention to the safety notices that accompanied your power tools. Seek the advise of a professional carpenter if you are unfamiliar with safe tool practices.
Step 2: The Plan
Every project should start with a plan. I had a plan but had to throw it out of the window on day 1. Plan #2 was the charm!
The twists and bows in the 2x4's were too bad for me to use long sections. The original idea was to build a roughly 8 foot frame using long lengths of 2x4. After struggling on the first frame I realized that I either needed straighter wood, or I needed a new plan. So I slept on it and awoke with a new plan. The new plan had the benefit of portability.
The idea was to make smaller parts so that the imperfect wood is less of a factor. The design you see here is the second stab at making. You will see in the photo's that some parts do not appear well lined up. That's because the wood is terrible (that's my excuse and I'm sticking to it!). But it is better to use it than throw it out.
Essentially the design consists of two end tables connected together to create the overall structure. This turned out to be a very good thing because the final product is heavy and long - getting it upstairs would have been mission impossible. By making the design in pieces, final assembly is done in-situ. If you ever need to move it, it's easy to break down.
You will construct 2 end "tables" which will be joined with 40" long 2x4 to create the appearance of a single unit. The 8 foot counter top ties it all together.
Step 3: Making the Cut
The first thing to do is to measure, mark and then measure again and then cut. This will save you a return trip to the hardware store to buy more wood.
To make the most efficient use of the 2x4s, make your miter saw cuts as follows:
- 2x4 #1 to #4 - Cut 40" then 35.5" then 2 x 8"
- 2x4 #5 and #6 - Cut 2 x 24" + 35.5"
- 2x4 #7 - Cut 3 x 24"
- 2x4 #8 - Cut 1 x 24 - the rest is scrap. If you adjust the width to 23.5" you will need one 2x4 less.
- 2x4 #9 - Cut 2 x 35.5
Then rip the 8x2 strip in half using the circular saw. This does not need to be accurate. Roughly in the middle is all you need. If you have a table saw, that is the preferred way to do this. Handling a circular saw and the thin piece of wood at the same time is tricky. Please be careful - this could easily turn into a dangerous situation. A circular saw will remove your finger faster than you can say ouch. You can buy 1" molding strips directly from the hardware store. I chose to rip a cheap piece of wood to save money. Don't let the desire to have a cost effective build create a dangerous situation for yourself.
Step 4: Pocket Holes and End Table Assembly
Making the pocket holes is a very tedious process. There are a lot of holes in this construction because I chose to make 3 holes for each join. I wanted the unit to be strong enough to handle the weight of heavy test equipment.
Creating the pocket hole is quite simple. Make sure the jig is adjusted to the thickness of the wood. Make sure the drill bit stop collar is set for the correct wood thickness. Clamp the jig to the wood using either a Kreg clamp or a welding clamp. Insert the drill bit into the hardened steel hole and make the pocket. My Kreg jig has 2 holes so I need to re-position and clamp to make the third pocket hole. Their plenty of informational video by Kreg and others on YouTube.
You need to make pocket holes as follows:
- 40" pieces - 3 pocket holes on either end
- 24" pieces - 3 pocket holes on either end
- 8" pieces - 3 pocket holes on either end
After what feels like an eternity, you will have all your pocket holes made. The 35.5" upright legs don't get pocket holes..... I made a mistake and did make holes in 2 of them....at some point you go a little hole crazy.
Start assembly by taking 2 x 35.5" pieces and a 24" piece.Apply glue to the ends of the 24" piece and then clamp the 24" piece between the two 35.5" pieces with the pocket holes facing outward.
Use a framing square to make sure everything is square. It helps to do this on a flat surface to make sure the alignment of the left and right legs is set correctly. I used my garage floor which is not perfect but good enough for this job. Drive pocket hole screws into each pocket. Check for for square after each screw to make sure nothing shifts on you. I find it best to drive a screw in on the left, check, and then drive a screw in on the right. Check for square again and continue with the remaining screws.
With the top rail in place, measure about 14 inches down and screw/glue the middle rail in place. Then repeat the process with another set so that you have the front and back of the "end table" complete. I found it useful to place the second set on top of the first set to make sure I got the lower rail in exactly the same place so that the shelf would be flat.
Now the front and rear legs get clamped to each other with the 8" rails separating them. Drive all the screws in checking for square and alignment as you go. You should end up with a complete end table. Now repeat the process for the second end table.
Step 5: Table Top and Shelves
I wanted the table top to have a thick chunky look to match the thickness of the 2x4s. This was accomplished by gluing the ft long ripped white wood to the front and sides of the table top. I didn't do anything to the rear.
The shelves drop into place and rest on ledgers that are glued and nailed to the insides of the front and rear rails. I used the remnants of the ripped 8ftx2" whitewood to make the ledgers and scraps from my wood pile when I ran out of whitewood. Anything will work here - it's not a precision operation. Just make sure that you have a nice flat surface facing upward - the factory edge of the wood is always nice and flat.
Due to variances in your construction and initial cutting, you will need to measure the shelf opening and trim your shelf boards to fit the space. There is no need to secure the shelves in place - gravity and whatever you put on them will do the job for you.
Step 6: Sanding and Painting
Using either an electric sander or hand sanding, smooth down the 2x4 surfaces to remove the worst of the imperfections. I used 120 grit which is pretty aggressive stuff but works well for 2x4s. I did not waste time going for a perfect finish here. 2x4s can be very rough in places so the goal is to remove enough of the surface roughness so that the paint will be reasonably smooth. This is not heirloom furniture after all. Use a sanding mask to prevent unnecessary dust from entering your lungs.
Blow or wipe the dust from the wood and prime it. I used leftover ceiling paint as a primer. After the primer had dried, I lightly sanded again with 220 grit sandpaper to knock down any nubs and raised fibers. Then I applied 2 coats of trim paint, waiting about an hour between coats. I used a 3/8" nap roller for the paint and a small 2" chip brush for the corners. It worked out OK. You could get a special foam cabinet roller to get the paint smoother.
Step 7: Final Assembly
After lugging all the pieces upstairs, I realized that I had forgotten to add the supports for the center shelf. Fortunately this is easily remedied but I suggest you do this before painting so that you can glue the ledger to the 2x4. Since my wood was already painted, I used screws to secure the ledgers.
Start assembly by securing one of the 40" rails to the rear legs of one end table. Then position the other end table as best possible and drive a screw into that end. The screw will pull the table to be square to the end of the rail. Just make sure everything is straight and square before you drive the rest of the screws in. It is beneficial to have a helper here.
With the two rear rails in place, the front rails are installed horizontally, so that the front of the unit has uniform thickness for all vertical and horizontal parts. Drop the center shelf in place and you are done!
Step 8: More Shelving
Originally I had intended to have another layer of shelving on each end table. However, I had used up all the wood I had so have left the piece as you see it. It has already been pressed into operation and the additional table surface available for testing is great. The height was done specifically so that I would be able to stand and work on the top surface, without bending over to avoid stress on my back. You may want to adjust the height to suite your personal working height.
In the end, it looks nothing like a 2x4 piece of furniture, is very sturdy and cost fraction of a store bought unit... if you can find one in a store that is!
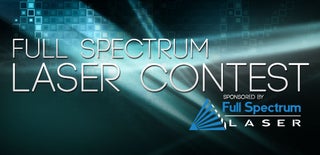
Participated in the
Full Spectrum Laser Contest
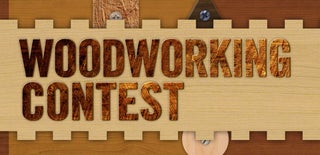
Participated in the
Woodworking Contest