Introduction: All Wooden Climbing Wall (with Interchangeable Wall Parts)
So it is very common to build climbing walls with wood, even in the big climbing halls normally the wall itself is made from plywood. much rarer is that everything is made from wood including the holds.
The room in which we build the climbing wall is the common-room for a housing community of around a hundred and fifty people. we needed something that was functional, diverse, but also nice to look at, since the room is normally used for yoga. and those doing yoga they were very reluctant to the idea of a climbing wall with the typical look, a white wall, that gets dirty with time and has lots of coloured climbing holds on it.
Another reason why we used wooden holds was that this way it is possible to climb barefoot. this way the many kids, but also those adults until now not into climbing can use the wall without the need of extra climbing shoes.
After using the wall for almost half a year, we are really happy with our choice, so we would like to share the details here.
Step 1: Deciding the Basic Design
So the first step is to decide where to put your wall. a couple of things to consider:
a good wall doesn't necessarily have to be big, check out the moon board for example...
its important to have enough space in front of the wall for falling
build a model!!!! I cannot stress this enough, it was a huge help for us. We made a model out of cardboard and made it to scale (1:10). It helped us decide on the construction, calculating material, visualization and so on. of course you could do this digitally, and that might be a good idea also, but I still think a cardboard model gives you a better understanding of structural weaknesses of your design.
If you can, use corners, or as we had the possibility to do: put it into a kind of niche....this means that it is way easier to have a self reliant construction and overhang, meaning the wall can stand by itself and doesn't rely on the strength of the wall behind it.
Some good examples can be found here, like this one:
Step 2: Some Basics About Climbing Walls
there are a lot of instructables out there, but anyway, let me just say a couple of thing about the basics.
1. Obviously you want a system where you can change holds to different positions. This is normally done by drilling a lot of holes in the wall and adding t-nuts in the back. then you screw your holds into these holes.
2. You need some space behind the wallpanels! Screws will stick out the back and also its very difficult to screw the panels onto your existing wall directly. so you need some kind of construction unterneath the panals. Most people do this with standard sized construction wood (in our case we used 6*8cm beams, but in the US you would probably use 2*4 Inch beams).
3. DONT use OSB. its cheaper, but unless you paint it or do something with all of the surface, it won`t be nice to touch. We used 21mm birch Plywood. it is strong enough that your construction can be 1m apart. it also looks nice.
4. Use a standard size for your t-nuts, in europe this is M10
Step 3: More Flexibility With Profiled Elements and Interchangable Panels
There are basically to ways of building a wall:
1. as a static wall, so all the flexibility comes from changing holds
2. as a wall in which all, or parts of it can be tilted to different angles. We wanted to do this at first, but then decided against it. You need a titling mechanism and this needs a lot of planing and isn't that feasible in a project were a lot of different people use the wall.
So our "3rd" way is this.
The wall consist of to sidewalls that are straight, as well as a lower part that is straight. on top of this sit four elements each of which has a different profile with different angles. (eg. a lower part with 10 degrees, and an upper part with 20 degrees). These for elements can be changed around, so in total the wall has 24 setups.
Additionally we divided our wall into segments of 1*1m panels. These panels are also interchangeable. This way we can make panels with huge volumes on them or sculpture wooden panels in much greater detail than would be possible with just screw on holds.
Another advantage is that we can easily replace parts of the wall, should they be damaged (or a t-nut is loose) and we can easily reach our construction behind the panels (and for example put lights behind it).
Step 4: Making the Straight Parts and the Panels
The first thing we made where the straight parts on the sides of the wall. These were simply plywoodpanels cut to the right size and construction wood (8*6cm) which was attached to the wall. Then we made two Elements that make up the lower part of our main wall, which is also straight, because we didn´t want to "steal" any space from the yoga people, so our wall starts of straight and then tilts at about 1.4m height.
We also prepared all of our 1m-panels. for this we made one template with holes in rows of four and five, each row 10cm apart and each hole in one row 20cm apart. also we added eight holes for the panels later to be attached on the elements (these holes do not get T-Nuts!) When the template was ready we drilled through the template into the other boards.
When we had installed the sides, we put one large 12*14cm beam across, that gives the profile elements something to "lean against"
Step 5: Building the Main Elements
This is how we made the main elements:
Each Element consist of two sidepanals, construction wood that is clued to the profiled side of the side panels and front parts that are positioned so that two 1m*1m panels fit in between.
First we cut out the sidepanels. we used one sheet of plywood (2.5m*1.25m) for four sidepanels, but you could do this anyway you wand. what is important in our design is that the bottom and top they meet again.
In order to be able to put holds on these panels we made holes in them as well and put t-nuts in.
Then we glued 6*6cm construction wood to the sidepanels. wehn the sides were ready we clamped our 1m*1m panels on to them so that they had the corect distance and then "filed" the space around the panels with woodstrips. Then we drilled holes trough the 1m*1m panels all the way through the construction wood and put t-nuts in from the back. This way each element is stable in itself also without the 1m-panels and the panals cna later be atached, switched and so on.
When all four elements were ready it was time to install everything.
Step 6: Attaching the Elements to the Wall
we put all four elements on to the lower part of the wall and then attached them each with six screws to the wall, by gluing threads into the wall. This way we can take out the screws, take down the elements and put another element in, switch elements or simple leave an element out in the future.
When we were happy with how the four elements were positioned we made a last element, that filled the gap, since out elements were 1m in width but the wall space was a little more than 4meter.
The last step was to put lights behind the wall, which makes for really nice lghting.
And next up: how we made the holds.
Step 7: Wooden Holds
The easiest holds are those made of plywood pieces
they are just cut to a nice shape, then sanded to a have good angles and grip and then drilled two holes into them, a small 10mm hole all the way through for the screw and a larger 20mm hole so that the screw head doesn't stick out.
A disk sander is really nice for this work, especially if you can tilt the base plate.
You can glue several layers of plywood together to make larger pieces, in this case a bandsaw is good to make interesting shapes.
If you want even more complicated shapes some kind of craving machinery is good, like the arbortec stuff that I want to win with this instructable or chainsaw blades for the angle grinder.
Another way we made holds was on the lathe.
As you can see, we also decided to attach some holds to the panels directly and in the future we want to make large volumes attached to the panels as well.
We give all of our wood a light coat of thin oil. this doesn't make the holds slippery, but helps them stay nice for a longer time.
When the holds get dirty after some time you can wash them of or sand them off. sometimes we also reshape certain holds.
a side note: Wood is anti bacterial and I can really say they are great for barefoot climbing and even then don't start to smell. we also don't need any chalk!!!
Thats it, all you need then is a crushpad!!!
For any questions feel free to ask and hopefully videos about the project will follow shorty
Step 8: What Are the Costs?
So obviously this is a big question to consider.
Wood (21mm birch Plywood + construction wood): 1200€
Screws,T-nuts, etc.: around 250€
Chemical Anchors for the wall: 50€
Holds: 0€, we used mainly the leftover plywood as well as scrap
pieces of maple that we got from two instrument makers who live in our community.
Total Cost: around 1500€
Wall area: Height: 3.9m, length of left side: 1.2m, length of right side: 0.9m, length of central wall: 4.5m, total (6.6*3.9): 25.74 square-meters.
Cost per Square-meter is around 60€
Crashpads: 1000€ (you can make your own, but we needed some that can be
stored away easily and so bought two standard boulder-mats at first that we moved (as you can see in the foto), then later bought two more so that we can cover the whole ground and don't need to follow the climber with the mats)
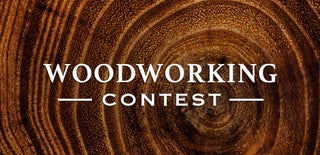
Participated in the
Woodworking Contest