Introduction: An Belt Sander to the Size of the Palm
my mini sand belt
Step 1: Mini Belt Sander From Scratch & Custom Sanding Belt
For those like me who need a low power, high precision and fine grain sanding belt, there is no such cheaper way than building it yourself from scavenged parts and materials.
The total cost for this project was below 10€, mostly the price of fine grit sandpaper.
Step 2: What and Why?
Hi, this instructable is about sharing how I made a new tool for my bench.
In fact, I use to sharpen knives for me, my friends and for those who want to help me pay for my studies!
That's why I get knives 12 by 12 and I need to have efficient tool to work.
I could have bought a belt sander, but I didn't for two reasons:
1) They are too big for the knives I sharpen until they are razors
2) I don't have the money for it.
The process goes as follow:
1) find a sanding paper that suits your needs (in terms of grain)
2) find the dimensions of the belt you will be making from this sheet.
3) build the machine around it!
Step 3: Make 2 Rollers
The criteria for the rollers are:
a minimum diameter for not braking the sandpaper while bending
a width corresponding to the belt size you chose
a slight camber for the belt to be stay on track
A) Cut a piece of cylinder
B) Find the centre.
Use a straight angle and a 45° indicator.
trace a line, rotate and repeat, you will find the center.
C) Drill it Straight
Step 4: Shape Your Rollers
As the holes WILL be Off-centred, we need to rectify the roundness of the roller.
A) use a threaded rod, engaged in your drill press AND a support with a ball bearing
B) insert the roller, and Turn it
C) camber the roller
D) adjust the bottom and top surfaces
Step 5: Find Your Motor and Adapt It
The motor I used was scavenged a long time ago from a printer.
A) remove all unnecessary parts ( belt tensioner replaced by a motor adjustment )
B) remove the old axis
C) reinforce the gears to fit the new axis (threaded rod Diam=8mm)
D) adapt the motor mounting plate to the new specs. Flatten it, drill a 8mm hole.
Step 6: Mechanical Pieces Need a FRAME
You have your custom rollers and your custom belt (have a look to the "make a belt" step)
Therefore, you have a custom distance between axis, and a custom thickness for the whole tool.
You then have all the dimensions you need to design the frame.
A) Get the axis to axis length
B) Get the belt width,
C) Estimate how much you want to adjust the belt tension (1 chose +- 5mm so a 1cm room for the bottom roller)
D) Mark the dimensions and the guidelines on the plexiglass and where to drill and cut.
Step 7: Round the Ends of the Frame (fillet)
Video
O) wrap a round objet with coarse grain sandpaper under your press drill
A) drill a small hole in the center of the fillet
B) drill a corresponding hole in a plate under you press drill
C) using a pin position the two holes one over the other. It will keep the fillet at constant distance from the sandpaper
Step 8: Belt Tensionning - Adjusting System
The belt adjusting system is supposed to put in tension the belt and compensate for variations in belt length
It should push the bottom roller downward.
But we only have access to the sides of the belt sander.
So I used a 45° sliding mechanism to transfer the movement from the side to the bottom.
This system will be sandwiched between the top and bottom plates. (next step)
Step 9: Top and Bottom Plate
Between the rollers, the belt has to be supported by plates.
The top one will be adjustable in height
A) cut a piece of plexiglass to the maximum dimensions between roller
B) adjust the thickness of the ends so that it follows the curve of the roller.
C) the best way to do it, is to wrap the roller with coarse sandpaper, and make it spin under the drill.
D) you just grind the plate down on this roller.
Step 10: Make Room Removing Matter
There is too much matter to have a convenient access to the belt while running.
So I made a chamfer using a grinding wheel.
A) mark 2 support lines
B) remove matter
Step 11: Secure Roller to Axis
For the axis to engage the roller, there are different solutions:
gluing, fastening it betwenn nuts or blocking it mechanically.
I chose the third option.
A) Drill a slightly off-centred hole in the roller.
B) make room for the screw head
C) screw the screw so that it blocks against the side of the threaded rod axis.
Step 12: Stand and Switch
Step 13: Safety Advice
A) Stop working when you're tired
it makes you do stupid things (like B) )
B) ALWAYS keep your hands off spinning things
And use a vice to hold pieces you drill, this prevents it to block to the drill, and spin damaging your fingers.
Step 14: Make Sandbelt & Polishing Belt
A) Take a vinyl tape and wrap it around your new tool, sticking side outwards.
B) Don't make a straight cut. Cut with angle so it more smooth when running on the tool. the angle orientation depends on the direction of the belt movement (upward for me) AND the side you'll be using (right for me)
C) do the same kind of cut with sandpaper, and stick it to the tape.
D) Adjust the ends
E) Glue the ends together
F) once glued, remove excess glue and you're done!
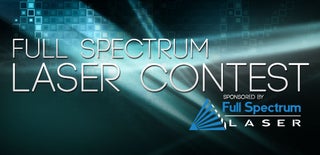
Participated in the
Full Spectrum Laser Contest