Introduction: Arm Rest End Table??
So I needed an end table for my sofa. Problem is, we live in a small house and don't have a ton of extra room for traditional furniture options... Enter the Arm Rest End Table, with custom inlay to spice things up a bit!
By the way this is my first instructable so if you like it, vote for it please, it is entered in a 'first timers' contest... Thanks
Step 1: Supplies and Tools
Wood of choice
Pencil
Precision measuring device
Block plane
Dowel rod
Drill
Clamps
Dowel rod joinery jig
Sand paper (150, 220, 400)
Inlay materials (optional)
Dremel with precision router base (optional)
Laminate trimmer
Boiled linseed oil
Grain sealer
Protective finish
Step 2: Settle on a Design
Fortunately, the arm rest of my sofa is broad and flat, so the design that seemed to be most appropriate, effectively hugs the arm rest pretty tight.
I didn't want the top deck to be too cumbersome... It needed to easily slide out of the way, without having to store it elsewhere, yet be large enough to handle a glass of water, perhaps a phone and a snack or two.
The vertical sides taper inward as the sides fall away from the deck so you don't feel as though the Arm Rest End Table crowds your personal space.
Joinery would be butt joints with dowel rods to avoid the need for nails, etc.
Overall exterior dimensions:
11 5/8 W x 5 3/8 D x 5 13/16 H
Step 3: Choose the Wood
I happened to have a beautiful piece of Honduran mahogany laying around, already been through the planar so it is in pretty good shape, no warping or twisting, width works well, only need to chop it up with the miter saw.
I like to maintain grain thoughout a piece when possible so I cut the board with this in mind. On a mahogany piece with fairly predictable grain patterns it is not as critical but on a peice of wood with real distinct figuring it is a must!
Step 4: Joinery
I naturally have an aversion to any wood working joinery that involves nails or screws. That said, this project need not get too complicated so I opted for butt joints with dowel rods. Simple yet strong.
The trick is to get things aligned well. I have a decent jig I picked up several years ago that allows you to line up both pieces and drill at the same time to ensure good fit.
Precise measurements matter. Always double check. Nice wood is too expensive to allow for careless mistakes.
FYI. If I was using a very nice piece of wood I would want to choose a different joint, something that incorporates 45 degree cuts or perhaps dovetails so the grain is uninterrupted by the joint. If I was really feeling confident, perhaps double blind dove tails!!
Step 5: Glue It, Then Taper the Sides, Route Edges If So Desired
If you are ready to glue, it is always advisable to first go through a dry run. Make sure things fit like you intended.
If all is well, glue it up, clamp (not too tight), wipe up squeeze out, let sit clamped got about 20 minutes, then release the clamps.
Note on clamps: we have a tendency to over tighten clamps, potentially damaging the wood... So if you absolutely feel the need to clamp the hell out of the piece, use some clamping cauls (small blocks of wood) between the clamp ends and the piece, this distributes the pressure s bit. I prefer to use cam clamps, they are quick, easy and controllable.
Tapering the sides is optional, but I think it adds a nice hand crafted touch.
When drawing out the angle you will plane off, be mindful of the dowel rods you inserted and the drill cavities. If you are not careful you will plane right into them and then it is too late.
I simply set a spare piece of stock down on the edge of the work bench so my work piece floats above the bench, clamp down the stock and the work piece so the planing surface is all available, and go at it.
The good thing about mahagony is that it is real easy to work so planing goes quick. Don't get too carried away however, go slow and easy, plane in the direction of the grain or sightly angled into the grain direction, and always use a straight edge along the top surface to ensure the work area remains flat and true. Plane long deliberate cuts, put some muscle in to it, but be in control.
Lastly, you can sand down the edges or, as I did, use a laminate trimer/router to put a nice quarter round on all edges.
Note: routers are dangerous, be smart cut in the right direction (I won't tell you the right direction , forces you to go look it up!), be careful when routing down the edge of the taper
Step 6: Inlay (optional)
I am a fan of inlay. Small amounts of inlay. This Arm Rest End Table is primarily for my wife so flowers seemed appropriate. I drew a cherry blossom'ish design directly on the work piece, routed the pattern out with my dremel (and very handy Stewart McDonald precision router base) with a 1 mm router tip, straight cut.
Then I crushed up some white MOP (mother of pearl) and rhodochrosite crystals as a touch of pink accent for the flowers and some green MOP for the stems. Not too fine. Coarse pieces are best so you can see the shimmer. Use the find grains as filler after initial gluing.
Next I simply start to place pieces in the routed grooves and then add some thin, runny super glue. Let it set up a couple hours then come back and sand with some 150.
After sanding you will need to come back in and fill holes and gaps with some finer grains. Then again glue, let set, sand, inspect.
Step 7: Finish
Now time to finish the piece.
I am a big fan of the wood and its natural beauty with a little oil to really make that grain figuring pop.
Get a rag, wipe the piece down with some boiled linseed oil (my oil of choice) and let it dry. Don't need to put it on too heavy, just nice and even. Then I apply a second coat a few hours later then let if fully dry and cure. The bad thing about oil is the drying time. I live in Houston, so I dry one week minimum.
Then I rub the whole thing down with grain filler (crystslac works great, follow instructions). Use a good brush, then trowel off the excess (without scratching the surface). This step is only needed for open grain woods like mahogony. If you don't seal, you will see little holes and dimples in the final clear coat.
Lightly sand after the grain filler is dry, apply second coat if necessary, touch up oil a bit, let oil dry another week then apply finish of your choice, or none at all. If you are applying a finish, do your self a favor and buy a good brush, apply 2 to 3 light coats, sanding in between with 220. Then a final polish if needed.
Enjoy and be creative!
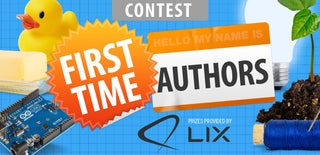
Participated in the
First Time Author Contest 2016