Introduction: Art Gallery With Moving Walls on Bicycle
The Art Pedaler is designed to be a pop-up art gallery that can situate itself anywhere. Artwork is to be hung on a motorized conveyor belt wall that spins slowly around the bicycle attracting the attention of passer-bys. Music will also be played from the bicycle and I can imagine serving free coffee and popping up a few beach chairs and encouraging people to hang out. I’m inspired by the multitude of ways in which people are democratizing art and subverting the conventional systems of art viewing and commerce and this project fits into that dialog. Enjoy!
I was hoping I could finish this before the deadline for the instructables Bicycle Contest but that didn't happen. But actually its a good thing because it is pretty far along but not too far to get some good feedback from the instructables community. Let me know what you think!
The video below shows my first and only test so far of the rotating display. As you see at the end, the belt falls off the cogs. I can envision a few ways of fixing this, but I'd like to hear any ideas ya gots. Also I have it rotating much faster than I had desired, I think I need to do some down gearing.
Step 1: Design and Material Considerations
This isn't going to be a step by step instructable because I don't think I could replicate this myself without another set of trial and error. So I'll just walk you through my journey from ideation to realization and the things I learned along the way.
I was originally inspired by bicycle commerce while spending 5 months hopping around South East Asia. There is a huge variety of bicycle businesses there and the best thing is all of the bicycles have this really rustic homemade quality to them. There is a picture below that's kind of case in point. After months of drawing out different concepts I settled on the drawing below and started thinking about how I could make this happen.
I put up a craigslist alert for a bakfiet style bicycle (pictured below) and found a really swanky one for a grand. This one goes for 3200 new so I got a good deal but I understand I could have saved money by building one or getting a less fancy one.
Then I figured my next step was sourcing the "gallery walls" which i figured needed to be a flexible light weight material that had some rigidity. I had a eureka moment during hurricane sandy (brooklyn boy here) when I saw all this plastic fencing that was put up. I tried to find that exact stuff but settled for a similar product that I found at home depot. Its just a plastic gardening fence. The grid of the fence got me thinking that I could use a cog to drive it around instead of a cable which was my original thought.
Step 2: Cog Development
I thought I could use a gear generator program to make a cog that would fit the spaces in my fence. And I'm sure I could but I couldn't find any free software that would work around my specific need. The problem was that the size of the tooth and space between each tooth needed to be different sizes to fit into my fence. The gear generator programs I was playing with were designed so that they could fit another gear of the same size. So I had to do a bit of math and make my file on illustrator because that was the closest thing I had to drafting software. I made it work but it was pretty painstaking.
I started by drawing a line, copying it and then rotating it a specific degree, and repeat until I had a bit of a section, and then centering all of the lines, and then copying that whole segment, and rotating it again and centering it with the last segment until I had a full circle of lines that looked like a dandelion. And then I made a circle that was the size of the outer dimension of the teeth and a circle that was the size of the inner dimension of the teeth. Then I put all those lines on lock and seriously traced each point with the pen tool with my zoom as far up as possible to ensure accuracy. After doing a bit of a segment I copied and pasted and rotated and strung them together until I got a circle. Then I made another circle that would fit the diameter of the wheel I was planning on attaching the cog to. Then I divided the circle in half so it could fit my school's laser cutter. Oh man that was exhausting to relive just now. If anyone wants my crappy file let me know.
So then I got the cog cut in cardboard first to see if it would fit my fence (tip: go to bicycle stores and ask for bike boxes for a good source of high quality large area cardboard). I glued two sheets of the cardboard together with the corrugation in opposite directions and it seemed sturdy enough to use cardboard as the real material. I was inspired by the cardboard bike and thought it might work. But then it started to warp and I knew it would be the death of me. But the teeth seemed to fit the fence so I threw down on some masonite and got my cogs cut.
Step 3: Making the Spools
As you can see in the last picture of the previous step, I made spools out of bicycle wheels that held the cogs. This looks simple but took a few tries to get right.
I used the "quick release" bolts that came with the wheels to attach it to a black pipe. I didnt get a good picture of the first part but I basically took apart the handle on the quick release to reveal a hole in the bolt. if you look at the second picture of a quick release bolt, you can imagine popping the pin out that holds the handle. After you pop that pin out and remove the handle there is a nice hole to work with that you can see in the first picture.
The idea is to make a hole in the pipe and insert the bolt into the pipe with the wheel on and a washer of course and then screw in another bolt through the hole in the pipe you just made and the hole in the bolt. Then you screw the nut on top of the wheel as tight as you can and you have a sturdy wheel on a pipe!
Hope that wasn't too confusing.
Step 4: Drive System
Oh gee this part was quite a headache.
I figured since this thing was kind of a conveyor belt I might as well get a treadmill motor. Bad idea. The RPMs were too high and the operating voltage was also too high. Since I'm a newb at motors I thought if I just gave the motor a low voltage it would just spin really slow. But actually there is a minimum rpm that all motors have and also a minimum operating voltage.
Anyway I then got a down geared motor that is way smaller and thus lighter and got the job done perfectly. I found the motor on ebay and it is a DC 24 V 200 rpm motor. I will definitely be able to work around this problem but I think 200 rpms was a little too high and maybe 150 would be more appropriate. Anyway it is powerful enough and is geared down low enough to work with so I went with it.
I'm not going to go into all the failed attempts at hooking the motor up to the wheels and cog, just know there were many and it set me back a bit. Actually one of the hardest parts and something I'm still struggling with is getting the gear to fit on the shaft of the motor. The motor shaft is round except for it has one flat side where I guess you are supposed to fit a pin in. to get the little gear to be perfectly centered on the shaft and perfectly perpendicular and not slide around has been a bit of a pain. Sounds simple and it probably is, but I'm definitely going about it the wrong way.
The gear that I have attached to the head of the motor is the smallest gear on a rear wheel cassete. You can take apart a rear wheel cassete in different ways depending on what kind of cassete you have. Anyway once I got that sucker attached to the motor shaft I took apart a bicycle chain and sized it so that the motor would be as close to the wheel as possible but not grinding gears. I didn't want the motor to be bending the shaft any more than necessary which is why I payed close attention to making it as close to the wheel as possible. Once I made a smaller chain out of my bicycle chain, I made a careful measurement of exactly how far back the motor needed to sit for the chain to be taught. This part would be easier if I had built something to adjust the motor's distance from the wheel but I didn't do it that way.. I built something really simple that had the motor sitting according to my measurement, the pictures are pretty self explanatory.
There are four wheels with toothed cogs on the bike and they are all free spinning. I only attached the motor to one of those wheels and was skeptical wether it would work or not. I thought it was possible that it would be spinning the plastic fence unevenly and not really work but it seems to be working okay and I don't think thats what caused the fence to fall off the cogs.
Step 5: Attaching Cogs to Bike
So the next thing I had to do was get these cogs attached to the bicycle. I originally had envisioned them sitting above the front and rear wheels. But then I decided it would be cool if I could raise and lower the fence so that I could lower it and be able to see if I wanted to ride around. So then I planned for them to sit in front of the front wheel and behind the rear wheel. This decision made the footprint of Art Pedaler increase a lot, since I haven't launched it yet I'm not sure it was a good or bad decision.
Two of the drawings show quick sketches of how I changed my idea of how I was going to attach the cogs to the bike and the last sketch is just notes on building the front attachment.
Step 6: Put on the Fence!
I ended up needing to buy a second roll of this fencing because 25 feet wasn't long enough. The Art Pedaler has 32 feet of wall space! To connect the fence into a ring I over lapped it a bit and tied them together with wire. I learned later that you can actually use a solder gun to melt the plastic together. So I think I'm going to re-do that part because it is a stronger and better looking seam than the wire method. But to measure I basically just wrapped the fence around the bicycle and then used some clamps to hold the ends together as I tied it together.
Step 7: Hook the Motor Up to a Battery and Give It a Whirl
I'll get around to making a classy control box but to test I just used aligator clips attached to a potentiometer and a 12 v battery. The potentiometer allows me to control how much voltage the motor is getting so before hooking it up to the battery I put the potentiometer to the lowest position. After hooking it up I slowly gave it juice and watched it go. I was so excited that it worked as well as it did my first go.
There is more to come! Please please please give me your wonderful thoughts!
If you're interested in wacky fun design stuff check out more of my work:
wastecog.com (for comprehensive)
&
wastecog.tumblr.com (for quick and fun)
And if you're in brooklyn I'd be happy to have you over for a chat/studio-visit/drink-a-beer. And any other inquiries please holla:
wastecog@gmail.com
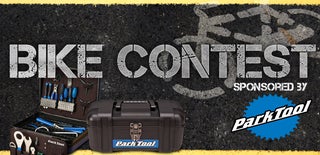
Participated in the
Bike Contest
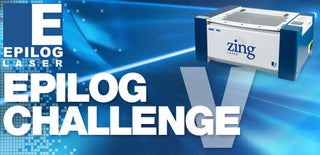
Participated in the
Epilog Challenge V