Introduction: 3D DLP Printer Kit Assembly and Calibration
This 3D printer is a result of intense testing and developing by a group of serious 3D printing enthusiasts. We love instructables, that's where it all started so no more than fitting we post our manuals right here. This is after all you main source of how to.
Be sure to check out our Facebook pages for the latest prints and updates:
Everything we’ve tested. Every setback we’ve encountered. Every part we’ve designed. Every print we made. It all has led us to this moment. It all helped us create the 3D printer from the ground up. This is a printer like nothing you’ve ever seen, and it’s going to rock the 3D print world!
Most of the steps are pretty easy but some extra attention is needed on some specific steps. You will also need some basic skills like soldering, gluing wood and (in case you like it) painting the wooden parts to your personal preference.
If you have any question about the manual or the printer, please feel free to contact us through the email address provided with your kit.
Tools and materials:
- 1 Set of metric Allen keys with rounded heads
- 1 Set of metric wrenches
- 1 Small flat head screwdriver
- 1 Cross head screw driver (small size for electronics)
- 1 Hot melt gun or super wood glue
- 1 (digital) calipers
- 1 Pair of scissors
- 1 Pliers
- 1 Knife
- 1 Soldering iron
- 1 Cigarette lighter (or something else to shrink the sleeves)
- 1 Spring rule
- 1 Level
- 1 Set of Sand paper of different grits
- (optional) 1 Set of tools to apply paint to the wooden parts
Materials:
- 4 large glue sticks (2 plus some extra) for your hot glue gun
- 1 Soldering tin
- 20cm of Red shrink sleeve
- 20cm of black shrink sleeve
- 20cm of green shrink sleeve
- (optional) Paint, in your favorite color(s).
Notice
All instructions, warranties and other collateral documents are subject to change at the sole discretion of Atum3D.
Meaning of special language
WARNING: Procedures, which if not properly followed, create the probability of property damage, collateral damage, and serious injury OR create a high probability of superficial injury.
WARNING: Read the ENTIRE instruction manual to become familiar with the features of the product before operating. Failure to operate the product correctly can result in damage to the product, personal property and cause serious injury.
This is a sophisticated product and NOT a toy. It must be operated with caution and common sense and requires some basic mechanical ability. Failure to operate this product in a safe and responsible manner could result in injury or damage to the product or other property. This product is not intended for use by children without direct adult supervision. Do not use incompatible components or alter this product in any way outside of the instructions.
This manual contains instructions for safety, operation and maintenance. It is essential to read and follow all the instructions and warnings in the manual, prior to assembly, setup or use, in order to operate correctly and avoid damage or serious injury.
Safety precautions and warnings
Read and follow all instructions and safety precautions before use. Improper use can result in fire, serious injury and damage to property.
Components
Electronic components can become hot while in use. Do not touch parts until cool. Should any compatibility questions exist, please refer to the product instructions or the component instructions.
Projector
Inside your 3D printer is an Acer H6510BD FHD projector. Always follow the manufacturer’s instructions before operation.
Small Parts
This kit includes small parts and should not be left unattended near children as choking and serious injury could result.
Safe Operating Recommendations
- - Inspect your 3D printer before every use.
- Always remove the printed object from the build platform when the printjob is finished.
- Do not place the 3D printer in direct sunlight.
- Always keep the room well ventillated during use.
- Do not look into the projector’s lens during use.
- Be aware of other activities in the vicinity of your path that could cause potential conflict.
Important Safety Notes
Select an area for assembly that is away from the reach of small children. Some parts in this machine are small and can be swallowed by children, causing choking and possible internal injury. PLEASE USE CAUTION!
The resin supplied should be kept out of children’s reach. Resins are harmful, should be treated with care and are not intended for human consumption! Always wear gloves and safety glasses when working with resins and solvents. Repeated exposure to certain resins can cause increased sensitivity and allergic reactions.
Exercise care when using any hand tools, sharp instruments, or power tools during construction.
Carefully read all manufacturer’s warnings and cautions for any chemicals, glues, or paints that may be used for assembly and operating purposes.
Age Recommendation: Not for Children under 14 years. This is not a toy.
Always inform yourself to the fullest, read the MSDS documents, if these are not supplied with the resin search out the manufacturer and ask for the Material Safety Data Sheets (MSDS).
And at all times use your common sense, if you are not sure inform yourself.
Step 1: Different Printers
On our first batch of 3D printers we offered the following kits:
- "standard" machine with 300mm Z-axis and TR12 spindle
- "XL" machine with 600mm Z-axis and TR12 spindle
- V1 "standard" machine with 300mm Z-axis and ball spindle
- V1 "XL" machine with 600mm Z-axis and ball spindle
The 3D computer images show the "standard" machine with 300mm Z-axis and TR12 spindle.
The photos show the "XL" machine with 600mm Z-axis and TR12 spindle. As the printer design is modular most parts of all printers are the same or similar.
Some steps in the manual are different, depending on your choice of printer. Please check the relevant part of the manual.
On our first batch of printers, we offered an option to receive a fully assembled and calibrated machine. This manual can be helpful in case of trouble shooting and better understanding the machine.
Step 2: Assemble the Brain Part 1 of 5
We start with the assembly of the "brain" of the printer. For every type of printer the brain is the same. The brain will be a box full of electronics which will take control over the printer's actions.
Parts list for the entire Brain assembly:
- 8 Cylinder head bolt M3x35
- 13 Nut M3
- 21 Ring M3
- 3 Bolt M3x8 countersunk
- 2 Cylinder head bolt M6x14
- 2 Ring M6
- 2 Bolt M3x10 countersunk
- 3 Cylinder head bolt M3x10
- 2 T-nut M6
- 1 Wood 3mm B1
- 1 Wood 3mm B2
- 1 Wood 3mm B3
- 1 Wood 3mm B4
- 1 Wood 3mm B5
- 1 Wood 3mm B6
- 1 Wood 3mm B7
- 2 Fan 80mm
- 1 Banana Red M
- 1 Banana Red F
- 1 Banana Black M
- 1 Banana Black F
- 1 Arduino Mega
- 1 Ramps
- 1 Stepper driver
- 1 Cooling fins
- 1 Power supply
- 1 On/Off switch
- 1 Power inlet
- 1 Power Cable
- 1 USB cable
First start with the assembly of the wooden parts B1, B2, B3, B4 and B5 and glue them together. Use the included photo's to get the right orientation of the parts. You can either use wood glue or a hot glue gun.
Move on with the banana connector on one of the 80mm fans. Mount a male banana connector on the red wire and a female connector on the black wire. Please see the photo's for further detail.
The second 80mm fan is mounted on wooden part B6. Use four cylinder head M3x35 bolts, M3 washers and nuts to do so. Check the right direction of the fan's flow. The sticker of the fan should be mounted on the wooden parts. Please see the photo's for further detail.
Check if the glue is dry and (if so) press the ON/ OFF switch into the wooden frame. Also mount the power inlet into place using countersunk M3x10 bolts with washers and nuts.
Step 3: Assemble the Brain Part 2 of 5
Unwrap you Arduino Mega, RAMPS and stepper driver and start with the Arduino. Bring it into position and mount it with three M3x10 cylinder head screws, 3pcs M3 washers and 3pcs M3 nuts.
Prepare your RAMPS board with two 35 cm long wires (red and black) and mount them in the sockets of the RAMPS as shown in the photo. Bend the wires 90 degrees to make the next step a bit easier.
Push the RAMPS board on top of the Arduino Mega gently.
Gently push the stepper driver onto the RAMPS in the Z-motor location. Notice the correct orientation in the photo's.
IMPORTANT! Make sure all pins are aligned correctly and gently press on the boards! Blunt force in combination with pin misalignment may lead to structural damage to both of the boards!
With the same precaution, press the stepper driver on the RAMPS board. Please align the pins correctly and pay close attention tot the related photo. The power supply will deliver the power to the Arduino (through the RAMPS) and the two fans.
Step 4: Assemble the Brain Part 3 of 5
Next step is to do the wiring. You'll need the usual soldering equipment to complete the next steps.
- Solder a 20cm black wire to the Neutral connector tab of the power inlet. Solder the other side to one of the connector tabs of the ON-OFF switch.
- Solder a 20cm green wire to the Ground connector tab of the power inlet
- Solder a 20 cm red wire to the Live connector tab of the power inlet
- Solder a 20cm black wire to the second, yet unused connector tab of the ON/OFF switch
We recommend to use shrink sleeves to prevent the possibility of a short circuit.
Step 5: Assemble the Brain Part 4 of 5
Unpack the power supply and check whether the input voltage is set correctly for you region (220/ 110V). If the power supply's input voltage is not set correctly for your region it will be damaged when power is put on the device. You can set the voltage by the switch on the side of the power supply.
Place the brain on a table with the power inlet facing upwards and towards you. Place the power supply next to it on the right hand side of the brain with the connection tabs facing upwards and towards you.
Make the connections as shown in the pictures and make sure all the wires go through the bottom section of the brain. The wires with the connectors on it will go through the wooden panel with the power inlet.
Before making the connection to the power supply we recommend to tin them to make a proper connection.
From left to right:
- - Red "live" wire from the power inlet
- Black "neutral" wire from the ON-OFF switch - - Green "ground" wire from the power inlet (in the pictures this is a black wired with blue labels)
- - Black "neutral" wire from the Arduino-
- - Black "neutral" wire from the brain's fan
- - Black "neutral" wire with the male connector
- - Red "live" wire from the Arduino
- - Red "live" wire from the brain's fan
- - Red "live" wire with the female connector
Step 6: Assemble the Brain Part 5 of 5
Bring the wooden part with the fan mounted into position.
Turn the power supply on it's side and put all the wires inside the brain while moving the power supply into position.
Insert three M3x8 countersunk bolts into the holes corresponding with the mounting holes in the power supply. Lift the power supply a bit and tighten the three screws to keep it into place.
Recheck all wires are inside the brain and no wire's stuck or damaged in the process.
Take the brain's side panels into position and use a rubber band to keep the assembly together.
IMPORTANT: Don't use glue for the side panels! You'll need to open the brain to connect the motor and the home sensor to the RAMPS in a later step.
The electronics are done (at least for now).
Step 7: Assembling the Z-axis Part 1
Clean your workspace and set the brain aside since we'll need some space to assemble the Z-axis. There are some differences between the standard and XL machines. The basic principle will be the same for both machines.
Differences between standard and XL machines are:
- - Aluminum beam
- - 40x40 L=350mm for the standard machine
- - 80x40 L=600mm for the XL machine
- - Linear guide
- - 350mm for the standard machine
- - 600mm for the XL machine
- - Amount of bolts and T-nuts to mount the linear guide
The photos show the assembly of an XL machine's Z-axis. Again, the process for a standard machine is not any different.
Mounting the linear guide
Start by mounting the linear guide on the aluminum Z-beam. You can recognize the Z-beam on the ends of the beams because they have has 4 M6 threads on each end of the beam.
Place the Z-beam horizontally on a table to make the assembly a bit easier. Make sure you are facing the long side of the Z-beam (see photo's)
If you're assembling the XL kit make sure a 40mm wide side faces upwards.
There are two ways you can mount the linear guide onto the beam. Please feel free to read both options and use the method you personally prefer.
Option 1)
- Insert six (standard machine) or ten (XL machine) M6 T-nuts on the upwards facing side of the beam.
- You can align the T-nuts in the slot by pushing them around with your screwdriver or a small Allen key using the linear guide as a reference.
- Take the linear guide with the recessions facing up.
- Place the linear guide over the aluminum beam with the inserted T-nuts.
- Put an M6x22 cylinder head bolt in each hole of the linear guide and loosely screw them in. There's no need to fully tighten the bolts yet since you will have to align the linear guide to the beam. We'll do that in a later step.
Option 2)
- Put an M6x22 cylinder head bolt in each hole of the linear guide
- Partially screw T-nuts on the bolts just enough for the bolt to hold on to the T-nut
- Slide the entire linear assembly on the Z-beam. Make sure to align the T-nuts properly.
Tighten the bolt on the left end so that you can no longer slide the linear guide over the Z-beam. Give the other bolts a few extra turns up to the point where can just slightly rotate the linear guide on the Z-beam.
Aligning the linear guide with the Z-beam
Align the linear guide by eye as parallel and in the middle of the Z-beam as you possibly can.
Take your (digital) caliper and measure the distance between the linear guide and the beam. This distance should be equal on all positions throughout the entire length of the Z-axis.
Check that both ends of the beam and the linear guide are flush
Gently tighten all the bolts in the linear guide bit by bit, dividing the pressure evenly over the linear guide. For your last round of tightening you can fasten the bolts in a manly sort of way, but not as if you where the Hulk. In a manly way, but don't over do it.
Now your linear guide is aligned parallel to the Z-beam.
Step 8: Assembling the Z-axis Part 2
For the assembly of a Ball Spindle Z-axis please continue to Assembling the Z-axis part 3 Ball spindle
Loosely mount the Bottom plate on the bottom of the Z-beam using four cylinder head M6x14 bolts. Loosely because the entire Z-axis will have to be aligned to the linear guide.
WARNING: BALL BEARING DISASTER APPROACHING!!
The carriage is filled with tiny ball bearings these are all held in place by a black piece of plastic.
DO NOT PULL THIS PIECE OF BLACK PLASTIC OUT
Really don't do it. We have tried this (once or twice by accident) for you and from our own experience we can say, you will never find all the balls again. Did you know steel balls can bounce almost a meter high after falling from the table?
This is a two man (or girl) job. Have 1 person hold the linear guide while the other person can now push the carriage on to the linear guide. Using the linear guide to gently push the plastic out of the carriage. Make sure you do this in one smooth move and what ever you do don't pull back.
Once you have assembled a few, its not such a big deal, quite easy actually. The only problem with the kit is, that you only get one go.
Unless your kit has the ball spindle option, which has the same principle this should be just one of very few stressful moments in assembling the kit.
Placing the anti-backlash spindle nut on the spindle
Take the spindle and notice the difference in the spindle's ends. The end with the short modification is the "top" of you spindle. The end with the larger modification is the "bottom".
Take the pre-assembled, white anti-backlash nut and have a look at this part. The anti-backlash nut consists of:
- - A thinner part with a flange and the two mounting holes
- - A thicker part that screws over the the thinner part
- - A bolt
About the anti-backlash nut
Both white parts have a coarse TR12 thread which grabs on to the spindle. They hold on to each other using the fine thread. By rotating one in relation to the other you can vary the distance between the two ends of coarse thread. In order to screw the complete nut onto the spindle this spacing needs to be just right.
Turn the white nylon anti-backlash nut on the spindle, with the mount holes towards the "top" side of the spindle. This takes a while and some fiddling so take your time. Once you have your spindle nut on the spindle you can adjust this spacing again to remove any backlash (slack) the spindle nut might have.
Take care not to overdo it though! If the anti-backlash nut puts too much pressure on your spindle, the whole thing locks up and won't turn. Once you are happy with your setting you can tighten the small M3 screw in the side of the nut to fix the position of the two spindle nut parts.
Assembling the end plates and bearings
Insert a 26x9x8 ball bearing in the aluminum bottom plate and insert the "bottom" of the spindle through the bearing. This end of the spindle should come all the way through the bottom plate.
Slide the aluminum bridge on to the spindle. The spindle goes through the large hole in the bridge. Continue by putting a pink ring on the top of the spindle followed by a bearing. Depending on the length of the Z-beam you might have to use two pink spacer to remove excessive play. You can place the extra pink spacer on either side of the bearing.
Place the second bearing on top of the pink ring and slide the top plate over the top bearing. Loosely fix the top plate on the Z-beam using four M6x14 cylinder head bolts.
Use two M5x16 cylinder head bolts, four M5 spacers and two M5 nuts to loosely fix the bridge to the spindle nut.
Mount the bridge to the linear guide's carriage with four M8x10 cylinder head bolts and four M8 spacers. After fixing the bridge to the carriage you can tighten the two M5x16 bolts that hold the spindle nut to the bridge.
Motor, pulleys and timing belt
Place the motor on the bottom plate and loosely fasten the motor in using four M3x14 cylinder head bolts and four M3 rings. Screw a M3x6 grub screw in each timing belt pulley.
Both your spindle and your stepper motor have a flat face. This is where the screw in the pulleys will hold on the the axis.
Mark the location of the flat face on both axis and place your belt over your pulleys. Slide the pulleys with the belt over the axis, both axis at the same time. Move the motor to get more room for the installation of the pulleys and belt.
Now rotate the axis so that the flat face is aligned with the grub screws in the pulleys and tighten the grub screws. You can use a bit of man force to make sure they are tight (girl power will also work) and make sure each pulley can rotate freely.
Push it back to put some tension on the belt. Just so the belt is tight but no need to make it so tight that when you twang it like a guitar string only bats can hear it.
Step 9: Assembling the Z-axis Part 3 Ball Spindle
Loosely mount the Bottom plate on the bottom of the Z-beam using four M6x14 cylinder head bolts. Loosely because the entire Z-axis will have to be aligned to the linear guide.
WARNING BALL BEARING DISASTER APPROACHING!!
The carriage is filled with tiny ball bearings these are all held in place by a black piece of plastic. DO NOT PULL THIS PIECE OF BLACK PLASTIC OUT Really don't do it. We have tried this once by accident for you and from our own experience we can say, you will never find all the bearings again. Did you know bearings can bounce almost a meter high after falling from the table?
This is a two man (or girl) job. Have 1 person hold the linear guide. The other person can now push the carriage on to the linear guide, using the linear guide to gently push the plastic out of the carriage. Make sure you do this in one smooth move and what ever you do don't pull back. Once you have assembled a few, its not such a big deal, quite easy actually. The only problem with the kit is, that you only get one go.
Ball Spindle
Twisting the ball spindle on to the ball spindle is a lot less difficult than mounting the trapezium spindle nut. Again there is a BALL BEARING DISASTER very near so take care and preferably do this with two persons just to be sure. Your ball spindle nut is delivered with an aluminum tube inside, held in place by two O-rings. This small piece of aluminum tube has the same function, as the piece of plastic in the carriage. IT HOLDS ALL THE BEARINGS IN PLACE. So what ever you do, don't pull it out. The ball nut holds 96 very small, 2mm balls, guess how we know that? If they fall out, they have to be placed back one by one with a pair of very fine tweezers. It took us over 4 hours and a small order of extra bearings to get them all back in the nut. We tried this for you so you don't have to. (If they do fall out, let us know we have a few on stock just in case)
Gently remove one of the O-rings, place one side of the spindle in the aluminum tube (gently hold the tube in place). Gently twist in the spindle and at the same time keep some pressure on the aluminum tube so it does not accidentally fall out. Twist the ball nut all the way to the middle of the spindle, just to be safe. The ball nut moves extremely smoothly over the spindle, if you hold the assembly upright by the nut the spindle will rapidly start to turn and can fall out.
We really feel like warning you in this case because it was a real pain to get all the balls back in the nut, we even had to order extra because we lost a few. Or on the more positive outlook, we recovered about 92 of them. Did you know that tiny balls are great at retaining momentum? When rolling from the table they can travel distances of over 4 meters on our tiled floor in any random direction.
Continued assembly Ball Spindle
Insert a 26x9x8 ball bearing in the bottom plate and insert the long, "bottom" end of the spindle. This end of the spindle should come all the way through the bottom plate. Continue by putting a pink spacer on the top of the spindle followed by a second 26x9x8 ball bearing.
Depending on the length of the Z-beam you might have to use two pink spacers to remove play. The pink rings are made out of polypropylene, a very tough and springy plastic. This is to ensure that the spindle has no room to move up and down in relation to the z-axis. Place the second bearing on top of the pink ring and slide the top plate over the top bearing.
Loosely fix the top plate on the Z-beam using four M6x14 cylinder head bolts. Place the carriage under the spindle nut, take the spindle nut mount and place it over the spindle nut. The spindle nut mount has a slot in it to accommodate the grease nipple. Fix the spindle nut mount to the carriage using four 'special' M8x45 cylinder head bolts (DIN7984). Slide the spacer plate that comes with the spindle nut between the mount and the nut. Take care not to block the adjustment screw in the spindle nut.
Bolt the mount to the nut using four M6x14 cylinder head bolts. Now you can slide the bridge over the mount. Use four M6x14 cylinder head bolts (in some models m6x10 is used, both options work well) with four M6 spacers to fix the bridge to the mount.
Final step in the Z-axis assembly is to attach corners to the bottom of the Z-axis assembly. On a standard machine, two of these corners are needed with two M8 T-nuts and two M8x16 socket head bolts. On an XL machine, with a 80x40 beam, you'll need four corners, four T-nuts and four M8x16 socket head bolts.
Step 10: Assembling the Home System
The home system consists of four basic parts:
- a red PMMA L-shaped part
- a red PMMA spacer
- the optical switch
- the home finger
Remove the protective film from the PMMA parts.
Assemble the L-shape, the spacer and the optical switch and stack them as shown in the picture. Use two M3x16 cylinder head bolts together with two M3 spacers and two M3 nuts. The bolts will go through the optical switch, the spacer and then the L-shape's long slots. Put a M3 spacer over the back of the bolt and fasten the it loosely with a nut. Loosely because you will still have to align the home switch with the finger. We'll do that in a later step.
Use two M3x6 cylinder head bolts and two M3 spacers to attach the home finger to the bridge.
Everything you need to make the Z-axis movement is now assembled. We move on with the calibration of the Z-axis assembly. Before we can do the calibration we should setup the connection to the computer and install some software and drivers.
Step 11: Installing the Software (Creation Workshop and Arduino)
To install the software you will need to have a Windows operated PC. We're sorry to say there's no support for Mac and/ or Linux at the moment.
The software you need to use your printer consists of two parts:
- Arduino IDE (1.0.5)
- Creation Workshop (CW)
Arduino
Go to the Arduino website and download the Arduino IDE (Integrated development environment) to your PC. Please select a full install of Arduino to make sure your PC will be able to recognize your printer's brain. You won't use the IDE for programming.
Creation Workshop (CW)
The next step is to install Steve Harnandez's Creation Workshop for printing. Steve has written some amazing software and we are sure you will enjoy working with it.
We highly recommend to start printing with the stable and tested version of CW which is available in our Dropbox. Send an email to the provided email adress that came with your kit and we'll give you the access code to the Drop box files.
If you're already more experienced, you may want to try Steve's latest version with the newest features which is available on his website.
After downloading the ZIP containing the program you can extract CW to any location of your choice and you will be ready to go. Double-click on CreationWorkshop.exe to start the program.
CW's interface is pretty convenient and straight forward so feel free to click around and get used to the interface. We are not going to fully cover CW in this manual and just pick out the basics you need to do the calibration.
If you want more information about the program, we suggest you read its manual. CW's user manual will come with the installation in the same folder as the CreationWorkshop.exe.
DO NOT INSTALL ANY FIRMWARE ON YOUR BRAIN.
We have already installed the appropriate firmware that goes with your printer model. Once you have installed Arduino and CW on your computer you are ready to make a connection.
Step 12: Checking for First Life and Configure Creation Workshop
With all the software installed on your PC we can connect the printer to the computer. Start by inserting the power cable to your brain. If this is your first time, it might be a good idea to recheck you set the power setting on your power supply correctly according to the country you live in. To our experience the magical smoke will only come out once.
Use the USB cable to connect the Arduino's brain to your computer. The first time you do this Windows will install some software in order to work with the brain. This might take a few minutes. Once the installation is complete, Windows will give a small popup in the bottom-right corner (where the time is shown) that your Arduino is now ready for use.
Now start CW. Since CW won't automatically adjust the settings to your machine you'll need to do some first time settings.
Connecting to the Arduino
- Go to View -> Connection to open the Connection Setup dialog box
- Select the COM port, for example, COM3 (COM-port number will vary per computer). Click on Refresh if your COM port doesn't show up
- Set the Speed to 115200 from the selection list (Baud rate)
- Set # data bits to 8 (if it isn't already)
- Click OK to save your settings and close the dialog box
Connecting to the projector
- Go to Machine -> Properties to open the Machine Configuration dialog box
- Set the Build Platform Area to X96 Y60 and Z250 (Z500 if you have an XL machine)
- Go to Select Print Display device and hit Refresh
- Select your projector, most likely \\.\DISPLAY2
- Set the display resolution to 1920 x 1200 pixels
- Set the driver to eGeneric
- Set the Z Axis Feed Rate to 200mm/min
Click OK to save your settings and close the dialog box
Now that Creation Workshop is configured you can connect to the printer.
- Click on the Connect button to start the connection to you printer.
- Notice the log in the bottom of CW and look for good news: "Device Connected"
- Click on the View printer controls to open the Printer Controls dialog box and take control over the Z-axis movement. You can change the number in the center of the buttons to change the increments of the movement. We'd recommend a value of max. 1mm at this stage since your printer's not fully calibrated yet. We'll do that at the next steps.
- If you want to check the projector's operating as expected you can go to DLP -> Show calibration. A red, square grid will be projected.
At this stage the projector and the Z-axis should be operating as you'd expect: the projector should send out an image and the linear guide should be moving in the clicked direction.
Step 13: Trouble Shooting Creation Workshop and Windows
CW does not recognize the resolution of your beamer:
Pres refresh and see what resolution it finds, if it is still not 1920x1080 go to your desktop and set up the screen resolution. If you run windows on mac go to your NVIDIA controll panel and change the color depth. Windows has no idea what to do with so many pixels so we need to tone it down a bit.
Windows does not recognize the beamers resolution.
Go to your desktop and right mouse click.
Open your screen resolution
Set extend displays. click ok a few times untill all is fully accepted, only at the very end windows will recognize the beamer resolution.
Step 14: Calibrate the Z-axis and Stepper Motor
If all is right your Z-axis is now fully assembled. The end plates are loosely attached to the main aluminum beam. In this case you should be able to jiggle these a bit by hand but they should not be so lose anything threatens to fall apart.
Keep in mind they will rattle a bit during the upcoming calibration steps. This is normal (for now). The reason why we keep these loose is because they can pinch the carriage when not aligned properly and this obstructs the motor calibration. We need to have a calibrated motor in order to align the end plates.
The first thing to do is to make sure the home switch is out of the way. You can even just remove the home finger to be sure your alignments will not be obstructed by the presence of the home finger.
(Re)check free and light movement of the spindle
You can skip this step in case you choose the ball spindle.
First of all check that all pulleys are properly fixed and there's no power on the brain. You should be able to easily rotate your spindle with your thumb and index finger. If you can't, adjust the pre-load in the anti-backlash spindle nut so the spindle runs lighter.
Calibrating the stepper motor driver
- Turn on the brain so there's power on the motor.
- Connect the home switch and stepper motor to the RAMPS
- Connect the printer to Creation Workshop like we've done in the previous step.
You should no longer be able to rotate the spindle with your fingers. If you can rotate it and you hear a clicking sound coming from the motor this means the motor's power is set to lightly at the stepper driver.
Adjust the power output of the stepper driver by turning the small variable resistor. Rotating the variable resistor on the stepper driver clockwise will increase the power to the motor. Rotating the variable resistor counter clockwise will decrease the power to the motor. If you were able to rotate the spindle, you should increase the output power and thus rotate the resistor clockwise until you can't rotate the spindle anymore.
Leave the setup like this for about a minute. After about a minute check the temperature of the cooling fins on the stepper driver. If these are a bit warm it's ok, if they turn hot you have the power setting too high.
Use CW's Manual Z-axis control to travel in either direction. Start by traveling a small distance, say 2mm. This is a nice calm check to see if you have fastened your pulleys and belt properly and if you do not have too much friction caused by your spindle nut. Gradually increase the length of travel until you feel confident to increase the speed of travel and repeat this test.
350mm long spindles have a maximum travel speed of 300mm/min, 600mm ball spindles have a maximum travel speed of 900mm/min.
Repeat this test until you can comfortably travel 100mm at maximum speed.
If your motor stalls or clicks increase the power on the stepper driver ever so slightly. If it steps really hard and runs very loudly you should decrease the stepper driver's power. Meanwhile also check the temperature of the cooling fins with your finger (carefully it might get hot). If the stepper driver overheats your motor will stall and miss steps.
You have now made sure your motor functions properly and your carriage with the bridge travels smoothly, but your end plates are still loose and can jiggle around.
Calibrating the z-axis end plates
This is the first calibration to make sure your travel is smooth and unobstructed. Travel to the lowest possible position using CW's Manual control buttons. The lowest position is where the motor is attached to the spindle. Leave a small gap between the bridge and or carriage and the bottom plate of approximately 5mm. Once in position gently tighten all the M6 screws on the bottom plate. Evenly pally pressure to the bottom plate by tightening the screws preferably on a cross like order. For example (I am assuming you have the z-axis is on it's back laying on the table) the top left, next the bottom right, followed by the top right, finishing with the bottom left. Repeat this sequence until all screws are fastened nice and tight. Now use CW to travel all the way to the top, stopping about 5mm from the top. Now repeat the same fastening process.
(Re)calibrate the stepper driver
Travel the axis up and down a few times at maximum speed while checking the stepper driver's temperature and resetting the resistor when needed during the process.
As the motor is weakest when traveling at the highest speed this will be a good indicator if you have excessive friction on your spindle or need to adjust the motor power setting.
You've just completed the calibration of the Z-axis!
Step 15: Assemble the Frame
Put the brain and the Z-axis aside since we're starting the assembly of the frame.
The assembly steps varies per machine type. If you choose an XL machine, you can move on to the next step.
Start by laying out the two 450mm long 40x40mm profiles on a flat surface. Take the mirror plate, 4 M6 T-nuts, 4x M6 rings and 4x M6x10 bolts. Insert two T-nuts in each profile and connect the mirror plate to the profiles. It is important that the front of the mirror plate is flush with the faces of the 450mm long profiles. Check if the mirror plate is oriented correctly, standing in front of the machine the four holes for connecting the mirror support should be on the right back side.
Insert the two steel dowels in to the two aluminum beams with a hole. These are the 300mm long profiles with a single 14mm hole through each of the profiles. You may need some persuasion tools (aka hammer) to get it in. If you use a hammer to persuade the steel dowel in to the hole in the 300mm long profiles , please use a wooden hammer in order not to damage your aluminum profiles. Be sure the holes in the steel dowel are in line with the beam's T-slot, the steel dowels have two recessed holes in each of them. The head of the special M8 bolt fits in this recession. Make sure the recessed part of the steel dowel faces the long side of the beam.
Once the through profile connectors are in you can insert the slim head M8 bolts through the T-slot in the beam. Screw each M8 a few turns into the double holed T-nut. Slide each T-nut with a beam into a 450mm long aluminum profile. Leave these loose for now.
Take 4x M6 T-nuts, 4x M6 rings and 4x M6x10 bolts. Insert two nuts int to each 450mm beam, place the Beamer plate and fix the Beamer plate to the two 450mm long profiles. Make sure the back of the Beamer plate is flush with the back faces of the profiles. Now check your entire ground platform, the sides of the plates need to be flush with the side faces of your 450mm profiles as well as the front of the mirror plate and the back of the Beamer plate, other wise your casing will not fit over your floor platform.
Now tighten the two risers, the 300mm profiles which stand upright until they are jiggle free. You will still have to align these so don't over tighten them.
Take out 2x 90 degree angle connectors (corners), 4x M8 cheese head bolts, 4x M8 T-nuts and the 370mm long aluminum profile.
Assemble the corners, put an M8 cheese head bolt through each of the slots of the corner and loosely screw on an M8 T-nut. A few turns will do the trick. Now slide both corners on the 370mm long profile. Insert this assembly on to the two risers.
Add two more corners and two 320mm profiles pointing towards the front of the machine. The 4mm basin plate will sit on top of these two beams.
Use 4x M6 T-nuts, 4x M6 rings and 4x M6x16 bolts (in some kits these might be M6x14) to mount the basin plate on the two horizontal arms.
Upgrades:
Upgrade your printer by covering the aluminum profiles with matte black foil together with all aluminum surfaces. The reduction of scattered light improves your print quality. High speed resins are sometimes so sensitive that they will cure even with diffuse reflected light and might actually require you to blacken out every aluminum and wood surface below the basin.
Step 16: Assemble the XL Frame
Start by laying out the two 450mm long 40x40mm profiles on a flat surface. Take the mirror plate, 4 M6 T-nuts, 4x M6 rings and 4x M6x10 bolts. Insert two T-nuts in each profile and connect the mirror plate to the profiles. It is important that the front of the mirror plate is flush with the faces of the 450mm long profiles. Check if the mirror plate is oriented correctly, standing in front of the machine the four holes for connecting the mirror support should be on the right back side.
Insert the two steel dowels into the two aluminum beams with a hole. These are the 300mm long profiles with a single 14mm hole through each of the profiles. You may need some persuasion tools (aka hammer) to get it in. If you use a hammer to persuade the steel dowel in to the hole in the 300mm long profiles, please use a wooden or plastic hammer in order not to damage your aluminum profiles. Be sure the holes in the steel dowel are in line with the beam's T-slot, the steel dowels have two recessed holes in each of them. The head of the special M8 bolt fits in this recession. Make sure the recessed part of the steel dowel faces the long side of the beam.
Once the through profile connectors are in you can insert the slim head M8 bolts through the T-slot in the beam. Screw each M8 a few turns into the double holed T-nut. Slide each T-nut with a beam into a 450mm long aluminum profile. Leave these loose for now.
Take 4x M6 T-nuts, 4x M6 rings and 4x M6x10 bolts. Insert two nuts into each 450mm beam, place the Beamer plate and fix the Beamer plate to the two 450mm long profiles. Make sure the back of the Beamer plate is flush with the back faces of the profiles. Now check your entire ground platform, the sides of the plates need to be flush with the side faces of your 450mm profiles as well as the front of the mirror plate and the back of the Beamer plate, otherwise your casing will not fit over your floor platform.
Now tighten the two risers, the 300mm profiles which stand upright until they are jiggle free. You will still have to align these so don't over tighten them.
Take out 4x 90 degree angle connectors (corners), 8x M8 cheese head bolts, 8x M8 T-nuts and the 370mm long 80x40 aluminum profile.
Assemble the corners, put an M8 cheese head bolt through each of the slots of the corner and loosely screw on an M8 T-nut. A few turns will do the trick. Now slide both corners on the 370mm long profile. Insert this assembly on to the two risers.
Add two more corners and two 320mm profiles pointing towards the front of the machine. The 4mm basin plate will sit on top of these two beams.
Use 4x M6 T-nuts, 4x M6 rings and 4x M6x16 bolts (in some kits these might be M6x14) to mount the basin plate on the two horizontal arms.
Upgrades:
Upgrade your printer by covering the aluminum profiles with matte black foil together with all aluminum surfaces. The reduction of scattered light improves your print quality. High speed resins are sometimes so sensitive that they will cure even with diffuse reflected light and might actually require you to blacken out every aluminum and wood surface below the basin.
Step 17: Mount the Brain and Z-axis to the Frame
Remove the two side panels from the brain. You'll see the two mounting holes in the bottom of the brain's frame. Use two T-nut to mount the brain to the frame on the horizontal beam. Its position should be most left, towards the vertical riser. Bring the brain's side panels back in position and keep them together using a rubber band.
Before installing the Z-axis it is recommended the basin is still in it's package. If you follow these instructions it will still be there but that's not shown in the photo's.
Take the calibrated Z-axis and lay it horizontal on a table.
Standard height:
Add 2x 90 degree angle connectors to both bottom sides of the Z-axis using 4x M6 T-nuts, rings and M6x14 bolts.
Take 2 M6 T-nuts and bring them into the frame's horizontal beam and bring them into position for the Z-axis assembly. Now grab the the Z-axis assembly and align it with the T-nuts in the horizontal beam. Take 2 M6 rings and M6x14 bolts to mount the Z-axis to the frame.
XL height:
Add 4x 90 degree angle connectors to both bottom sides of the Z-axis using 8x M6 T-nuts, rings and M6x14 bolts.
Take 4 M6 T-nuts and bring them into the frame's horizontal beam and bring them into position for the Z-axis assembly. Now grab the the Z-axis assembly and align it with the T-nuts in the horizontal beam. Take 4 M6 rings and M6x14 bolts to mount the Z-axis to the frame.
Alignment of the Z-axis
Align the Z-axis to the center of the rectangular hole in the basin plate by sliding it along the horizontal beam. A ruler or calipers will help here. If everything's in place you can tighten all the bolts.
Step 18: Assemble the Basin
Now the Z-axis is in position you can mount the basin to the basin plate. The basin is hinged to the plate allowing it to tilt.
There are four pivot blocks provided in your kit. The slightly larger blocks (30x14x10mm) go on the basin plate with the 4 M4x18 cylinder head bolts. The smaller blocks (30x10x10mm) go on the basin itself with 4 M4x14 cylinder head bolts.
Use a M4x18 cylinder head bolt through the larger block on the basin plate into the smaller block on the basin on each side. Don't over tighten these bolts since this will prevent the basin from tilting. The basin should fall back from a tilted position by gravity only, so be sure this works correctly.
Mount two M4x18 DIN933 screw in the front two threaded holes in the basin plate. These are the mechanical limits of the basin's tilt. Set these up so the basin can tilt up about 2mm measured at the front of the basin.
Step 19: Setup Your Projector
With the basin in place we should now install the projector on the projector's plate.
Unpack your Acer H6510BD DLP FHD and remove all the packaging material including all the protective foil. Remove the bolt in the bottom of the projector.
Use this bolt to mount the projector to the projector's plate using the slot hole. Do not fully tighten the bolt before you checked the projector's level to the plate.
Once the projector's level, tighten the bolt. You will need to loosen it a few more times and change your projector's position since it's a very important setting.
Also attach the provided power cord and a VGA cable to the projector. You may want to consider buying an HDMI cable to improve the quality of the projector's image.
In Windows you should setup the projector to function as a second display, as an extended desktop configuration. Make sure you set it to a 1920x1200 pixel resolution in you Windows setup as well as in Creation Workshop.
On Windows 8 you can use the Windows + P shortcut to aces the display options. On Windows 7 you go to the desktop (Windows + D), click on the right mouse button and click Screen resolution.
We know Windows has some issues with setting up the projector as a second display. Unfortunately this is mainly Windows related and a lot of these problems differ per computer configuration so there's no such thing as a single solution for these problems. Things that may help:
- Click OK and go back to the display setting to check. Common issue is the resolution is resetting
- Restart your computer (we're really sorry to say but this helped quiet a few users already)
- Uninstall drivers of other displays
- Check the display connection
- Switch to an HDMI cable
If you still have problems with the projector's connection and setup, please feel free to ask and share the solution that worked for you!
Step 20: Assemble the Buildplatform
Unpack all the build platform's parts and start with the build platform itself. It's really important to clean the platform's surface. It should be free from grease, oil, dirt and other debris to make sure the first layer of your print will connect to the platform.
Your build platform is packed separately and should be touched with your bare hands or come in to contact with anything that is not clean and grease free. You can use a 50-50 mixture of water and Cillit Bang to clean the surface again if you dirty it up. Do so by rubbing with a gloved hand or by using a new clean brush. Scrub the surface several times and rinse the cleaned platform. You should no longer be able to see any greasy spots.
Continue with a mounting the cup ring (with 9 holes) to the platform. Use four M4x10 cylinder head bolts to do so. Since these are mounted into an aluminum thread please do not over tighten these bolts.
You can now insert the ball joint into the mounted cup ring and add the second, 5-holed aluminum clamp ring on top of it. Use a set of four M4 rings and the M4x12 DIN933 bolts to keep the parts together. Do not fully tighten the bolts yet.
Insert the M6x10 grub screw to the holder for a couple of turns and put it on top of the ball joint. Now give the grub screw a few extra turns to make the parts stay together but can still move freely.
Insert the M8x15 Star Knob into the holder to finish the build platform assembly. Make sure all parts just can move freely. The platform should be able to orbit in all directions and the joint and holder should slide. You may seriously damage your machine when the parts are fully tightened during the next assembly stages.
Step 21: Mount the Mirror
Mount the mirror Support on the mirror plate of the frame using two M6x10 cylinder head bolts and two M6 rings.
Place a piece of paper in the basin so you can see the projector's output.
Progress with the mirror but not before reading the following instructions first.
IMPORTANT: Be very, very careful with the mirror. It is a delicate and precisely made part and is essential for your printer to get the awesome results we promised. Always use gloves when handling the mirror. Avoid any contact to the mirror's surface and only touch the mirror on the sides. Even with your gloves only touch the mirror on its sides. The mirrored coating is very fragile rubbing this metallic coating will remove the coating from the glass even a soft tissue might damage your mirror beyond repair.
IMPORTANT: Never clean the mirror! It is very likely you will not improve anything by cleaning it. You will only scratch the surface.
Open the mirror's box and remove the first wooden spacer. Now gently touch the mirror on three sides with your fingers and turn the box over. The mirror will now fall out and land with its edges firmly on your fingers. Remove the second wooden spacer and remove the four tabs from the double-sided tape.
Other mirrors are either packed in special paper or have a special cover foil and are wrapped in bubble wrap. Same principle applies, unpack carefully and don't touch the mirrors front surface.
Align the mirror to the mirror plate while hoovering over it. Look into the basin at the paper to see the projector's output and lay the mirror down on the mirror plate when you feel the alignment is pretty good. You will need to refocus the projector during this stage. Use the projector's silver rings to do so.
The most important thing is to make sure the bottom of the image just falls slightly (about 3mm) above the bottom edge of the mirror. Once you have achieved this you can put the mirror in that position on the mirror support.
Later on you can align the image on your basin by moving the mirror support or by re-aligning the projector. One piece of advice is to do this step-by-step and check the output on the piece of paper. You may get confused in this process since you have to deal with quiet a few variables (projector zoom, projector focus, mirror position, mirror plate position, projector position and the alignment of all these parts). Slow and steady does the trick.
Step 22: Calibrate the Printer
For this step you will need:
- A set of Allen keys
- Plain copy paper
- Pen (no pencil, since it will leave a graphite contamination)
- Ruler
- Scissors or scalpel
- Gloves
- Sunglasses
- Spirit level or protractor.
Setting the printer X,Y resolution.
By now it is time to think about your printing demands. You should decide whether you want to print mostly tiny objects or use the printer's maximum print area and print very large things. If your interests lie in jewelry or small scale model making we would recommend a x,y resolution of 50 microns or less.
If you would like to print larger models, for example parts for your RC plane, vases, and toys we recommend to set the x,y resolution to about 80 microns. If your are just planning on printing big you can set up for the maximum 100 microns x,y resolution. The larger your resolution (100microns) the bigger your print area will be. You may also take into consideration that with a larger print area it takes longer to cure a layer resulting in longer printing times.
I would like to offer a note of caution here: Although we tried very hard to reduce the release forces these are still quite significant. Basically anything you print acts like a suction cup on the surface of your release layer. If your object is bigger, the force to pull it from the basin's build window will be bigger too. How large this force also depends on the shape of the object, the largest force is generated by a hollow circle, this is basically why the suction cups you use to attach your TomTom to your car window are also circular. Releasing with a lot of force can cause low viscosity resins to splash!
Please start printing small so you can get a proper feel for your machine.
The x,y resolution is determined by the distance between the lens and the build window. The closer you please your build window to the lens, the smaller the image will be, thus the higher the resolution will be.
This means the maximum x,y size is not really determined by the size of the build platform as with other 3D printing techniques. It is determined by the size of the projected image.
The projector (Beamer) projects an image that is made up of pixels. This is a fixed number of pixels, 1920 in the x direction and 1200 pixels in the y direction. Check how your windows together with your computer hardware recognizes the Beamer. On some computers it only recognizes the Beamer as 1920x1080p in most cases you should get 1920x1200 so your maximum build area will be 192x120mm at 100microns x,y
Now how to figure out your resolution? Simple:
That's the size of the image divided by the amount of pixels. So if you project an image of 192mm in the x direction and 108mm in the y direction your pixel size is 100microns or 0.1mm x,y.
As 192mm / 1920pix = 0.1mm (100microns)
Connect your Beamer to windows and verify the Beamer resolution. Now think of your ideal resolution and cut out a rectangle of white copy paper at the appropriate size.
First example
For example I want to print at 80 microns (good surface finish for larger functional parts), my computer recognizes the Beamer as 1920x1200 (I have a very recent PC).
I should cut out a rectangle that is 153.6mm (x) long and 96mm wide (y).
1920pix (x) * 0.08mm= 153.6mm (x)
1200pix (y) * 0.08mm= 96.0mm (y)
Second example
I want to print at 50microns because I am in to jewelry or fine mechanical parts.
My PC recognizes the Beamer to have 1920x1200 pix (x,y)
I will have to cut out a rectangle of approximately 96x60mm.
1920pix (x) * 0.05mm = 96.0mm (x)
1200pix (y) * 0.05mm = 60.0mm (y)
You do not. have to cut out this piece of paper with an accuracy of 0.01mm, even if you would be off by 5mm this will not influence your final accuracy. We will do a calibration print to really calibrate the printer, this is just your global rough setting up.
Wear gloves, to prevent the transfer of body grease to the basin and other sensitive components.
Wear some sun glasses to prevent staring directly into the Beamer.
Before you start move the build platform up and out of the way, make sure the build platform it's self can freely rotate on the ball joint and freely slide up and down in the holder.
Make sure your printer is placed on a level surface.
Place your paper guide (the rectangle you just cut out) in your basin, this is also why we use normal paper because paper is relatively soft the chance of scratching your coating is smaller. However paper is harder than your Teflon coating so do not rub the paper on the coating with any amount of force.
Turn on the Beamer and focus the Beamer on the piece of paper in the basin.
If your image is larger than your piece of paper, loosen the two arms that hold your basin platform in place and move your basin platform a bit closer to the Beamer. If your projected print area is too small, raise the Beamer platform away from the projector. Refocus your Beamer on the paper guide and verify the image size.
Also in this step there is no need to match the image size to the paper guide 100% perfectly.
Align the printer
Level the basin platform using your spirit level. Depending on your application you might want to use a more precise spirit level to set up your machine. The easiest way to level your basin is to fix one of the arms on tight and loosen the other. Now move the loose arm up or down to level your basin. If you want to be really particular about your leveling you can place shims between the front or back of the basin plate and the arms to level in the y direction.
Once you are happy with the setting of the basin mount platform it is time to set the position of the z-axis.
Slowly bring the build platform down until it is about 5mm from the minimum position on the z-axis.
Use your paper guide as a spacer between the build window and the build platform. While doing this make sure your z-axis is positioned correctly so the build platform lowers neatly into the basin. You can carefully move the z-axis to the left or right over the horizontal beam. If your z-axis reaches it's lower limit before the build platform makes contact with the basin you should move the horizontal beam downwards. Make sure you mount your horizontal low enough so that your build platform can slide about 5mm up in to the holder counted from the lowest position.
Once your build platform is correctly positioned in the basin you can tighten the screws on the corners that connect your z-axis to the horizontal beam.
Now we can level the z-axis.
Start by leveling the z-axis around your y axis (left right tilting). Loosen one side of your horizontal beam. One side should be loose enough to freely move, the other side side should make sure all stays in place.
Move the loose side up or down to level the z-axis around the y-axis.
Once you are happy with your leveling tighten the loose end far enough so the beam can not move up and down but loose enough to allow some rotational novae net on the screw that connects the corner to the vertical riser. Do this for both screws that connect the horizontal beam to the vertical risers. Now level the z-axis around the x-axis (tilting back to front). Once you are happy with your leveling tighten all the screws on the frame and recheck your leveling.
Step 23: Level Your Build Platform and Set Your Home Position.
IMPORTANT: Make sure your build platform is loose and can freely slide up and down in the holder as well as freely rotate on the ball joint. You can seriously damage your machine if the platform cannot move freely.
Place the sheet of paper in the basin (if it's not in there anymore). This paper is typically 0,1mm thick and should be a good starting point for the first layer thickness.
Move your build platform down with CW's manual control until it makes contact with the piece of paper in your basin. Once you made contact, move the platform down for 5mm. This will cause the ball joint to slide a bit further in the holder.
Now take the home switch assembly and place it so that the bottom of the home finger is in the optical sensor. This should turn the LED on the home switch OFF. Now move the home switch a bit further down until the led is on but dimmed. Fix the home switch to the Z-axis and check if the LED is still dimmed and the home finger floats freely in the switch. There should be no contact between the home finger and home switch.
Press "Home Z" button in Creation Workshop to reset the printer's Home position. This is always a bit of a scary moment. If you are less confident, you can move the platform up, remove either the build platform or the basin before doing your first homing.
Leveling the build platform
Now that your build platform is resting on your calibration paper in the basin and the Z-axis is freshly "homed' we can level the build platform. Grab the ball joint with two fingers and press downwards while tightening the grub screw in the holder. This takes light pressure, too much pressure will damage your basin.
Now gently tighten the bolts on the clamp, to clamp down on the ball joint. The trick here is to do this gently and evenly. Alternate between all four bolts every quarter turn and keep the clamp ring parallel to the cup.
Move the platform up for about 100mm and make sure it can't move anymore by applying normal human force. Grab the platform on both sides and try to rotate it. If it moves, you should repeat the process from the beginning of this step in order to get the platform setup correct and move on to the next step.
Step 24: Assemble the Casing
Congratulations! All the hard bits are done at this stage. All you need to do now is assemble the wooden casing.
These steps do take time but are not too difficult. Notice the correct orientation of all the wooden parts and have a close look on the 3D images.
Most of the parts are marked so you an easily see the part and it's orientation.
Use wood glue or a hot glue gun (whatever you prefer) like you did with the brain assembly.
Projector Air Bridge
We'll start with the Projector air bridge. This part has the function of directing the hot air generated by the Beamer out of the casing.
Air inlet fan casing
The air inlet fan casing goes on the back and inside of the case fan and prevents sunlight to come in through the opening in the fan. Screw the loose fan with the two banana connectors to the inside of the case. Make sure the fan blows air in to the case. Use 4pcs M3x35, 8pcs M3 rings and 4pcs M3 nuts.
Glue the cover over the fan, make sure the airflow is directed towards the roof of the case.
Most light sources come from above, that's is why the airflow is directed upwards because light has a hard time bending around corners. You can improve this light trapping system by painting the inside matte black.
Lower casing
The lower casing is just a ring of wooden parts, marked LC with two unmarked wooden strips. The strips are used for guidance of the upper casing. On the bottom of the lower casing there are six holes which will be used to assemble it to the frame. The upper casing will just sit on top of the lower casing. There is one wooden strip for the front of the lower casing and one for the back of the lower casing. These should be glued on the inside of the casing on the half way mark. Remember when assembling the lower casing, all part numbers are supposed to go on the inside of the casing.
Upper casing
The upper casing differs per standard/ XL machine. The parts on the XL machine are obviously larger but they do have the same marks/numbers. Use the triangular wooden parts without the window in the upper casing for the rear of the upper casing. The ones with the windows are supposed to be on the front, they are however universal so you can have a bit of creative freedom here if you like.
Left and right door
The left and right door are slightly different and so are the door's parts! Pleas check-double check the parts before gluing since the difference is just hard to see. Use the triangular parts with the window in the doors.
Paint
If you are skipping the beautifying of your casing please continue to the next paragraph for installing the windows.
With all the wooden parts glued you may want to paint it. There's no real need to do it but feel free to give it any color you like! We would recommend a matte, dark color for the inside of the casing to bring down reflections of the beamers images.
Use your paint as an upgrade!
Paint the entire inside of your casing matte black for a better print result. Less scattered light in the case means a higher print quality.
Installing the windows
Remove the protective foil before installing the windows. The easiest to install are the windows for the triangles with the cut outs. The windows for the triangles are slightly larger than the cut out in the these are simply glued to the inside of the triangle, here you can use some silicone sealant or hot melt glue. As far as we have tested now, hot melt glue holds them better than silicone. The large windows should fit exactly in the frame. The frame is 6mm thick but the window only 3mm, if you place the frame face (outside) down on a flat surface and insert the window the window will be flush with the window frame. Now apply a bead of glue to the inside edge of the window frame to fix the window in place.
Attache the doors to the upper casing
During this small step it is handy to have some extra hands present, ask a friend or spouse to hold the doors while you are marking, drilling and screwing.
Place the doors on the casing, take a ruler and pen and make a small mark on each door. 10cm from the top of the door and 15cm from the bottom. Make sure that your marks are on the side of the doors where they meet the casing.
Take a small hinge and a pen, place the hinge against the mark. Make sure the flat side of the hinge is against the casing and the hinging part of the hinge is centered over the meeting edges of the upper casing and the door. Use your pen to mark the center of each hole in the Inge on the casing. Take a small drill of 2mm in diameter or less (1.5mm will do too) and drill a small hole on each mark about 3mm deep.
Repeat this step for all four hinges, two for each door.
Once all the holes are drilled screw on the hinges using 4 small wood screws for each hinge.
Step 25: Mount the Casing on the Printer
Insert three M6 T-nuts on either side of the frame's lowest beams and align them with the distance of the holes in the lower casing.
Take the lower casing and bring it into position by taking it over the Z-axis and onto the bottom on the aluminum frame. It should be flush with the aluminum beams
Align the T-nuts with the holes in the lower casing. Use six M6 rings and M6x16 cylinder head bolts to mount the lower casing to the frame.
Take the upper casing and bring it into position by taking it over the Z-axis and onto the lower casing. It is not mounted to the lower casing and it just sits there. The two strips on the lower casing should guide the upper casing in the process.
Connect the fan to the brain.
Place the air bridge next to the projector and the holes in the side of the lower casing. It should just sit there, no glue is needed but you can secure it to the mirror plate with some hot melt glue or double sided tap if you plan to move your printer around a lot.
Step 26: Print Something
Finally the assembly is finished. Good job! You can now start using your 3D printer.
Before printing, we feel we should remind you of some very critical things:
- - Don't scratch the basin's bottom plate
- - Don't scratch the mirror (don't try to get dust off!)
- - Always wear gloves when handling resins
- - Always wear safety glasses when handling resins
- - Be sure there are no printed objects on the build platform before starting a print or "home" the printer
We'd also like to share our recommendations for your first prints:
- - Start with small object
- - Don't fill the basin with too much resin (small objects here)
- - Print a few things to get used to the workflow and get confident before going large and complicated
- - Start with the Fun to do resin and our settings to get going
- - Use the CW version from our Drop box
- - Take your time!
- - Enjoy watching the printer do the magic
- - Make photo's and/ or videos of the print in progress. It will be a moment to remember as "The day I made my first 3D print"
Now on to the fun stuff.
First you should clean the basin. The paper you used for calibration should be out and the basin's surface should be cleaned. Use ethanol/isopropanol and a sheet of kitchen paper to very gently clean the inner surfaces of the basin. You should use gloves in this process since your nails may damage the coating on the basin's surface.
Before getting the resin out, you should start with Creation Workshop to do the pre-printing routine.
Pre-printing routine
Open the model you want to print in Creation Workshop. Move, rotate and scale it until you're happy with the orientation. You may need to go back to the design software for more advanced options on this. Netfabb Basic and/ or Meshlab are free to use and can help repairing models or re meshing your STL file(s).
Add supports to the model to print overhangs. We feel the most efficient workflow is to have CW create supports automatically and move them manually afterwards. Please see CW's user manual to get help.
Now open CW's slicing options and put in your first resin settings, you can find examples for different types of resins and build areas in the drop box folder.
Click on the slice button to start the slice calculation. It may take a while for complex models but with the small objects it'll be finished in no time. Once's it's done you can preview the slices in Creation workshop. We do recommend to check the slices before starting the print job.
Now Creation Workshop is ready to go. Make sure no image is shown on the projector. If there is, turn it off through Creation Workshop's Show blank option in the machine control down menu.
Get your resin out of the package. This resin, by Fun To Do, should get you started. There's a liter in the package so there's enough for the upcoming weeks.
Make sure the resin's package is securely closed and mix the resin for approx. 3 minutes just like you'd do with paint in a can. This will mix the color pigments through the resin evenly.
Leave the resin on a table for 5 more minutes. This should be enough to prevent air bubbles in the resin (you seriously don't want air bubbles in the resin in the basin!)
Open the bottle and pour the resin into the basin. If this is your first time, you may consider taking the basin out to have a little more control over it. There should be at least 4mm of resin in the basin.
Home the z-axis by selecting the home Z button in the machine control menu. Again, this is going to be a scary moment since you don't really see if all goes fine. The build platform will move into the resin and disappear in the resin.
Next we will start the print in Creation Workshop but before doing that, please read the following instructions:
- - Don't turn off your computer during the print process
- Don't use your computer for other applications during the printing process - Make sure your screensaver is turned off.
- - In case you use a laptop
- - Make sure the power saving settings are turned off
- - Connect it to a power supply
Click on the Play button in CW to make the magic happen. Creation Workshop will start the printjob and take full control over the printer.
The printing routine should be:
- Project the first slice
- Stop projecting the slice
- Move the platform up
- Move the platform down
- Wait in the down position (about 1 second)
- Project the next slice
- Stop projecting the slice
- etc.
You can see the progress of your print job in Creation Workshop.
You won't be able to see any results for the first layers. Just sit down, try to relax and wait until the platform with your object reaches above the resin's level in your basin to see the result. Now you should wait until the print's finished and move on to the next step.
Step 27: Remove the Print From the Machine
Materials/Tools:
Ethanol/Isopropanol (IPA)
Razor blade
Paper towels
Gloves
Safety glasses
Cutting mat
Small container
Spray bottle
Forceps
The printer's finished and your object is hanging in there upside down. Now it's time to take it out.
Preparations:
Place a cutting mat or a sturdy piece of cardboard to be used as your work surface near the printer. Have some kitchen paper at the ready to clean up any spills.
Fill a small glass or polypropylene container half way with ethanol/IPA.
Fill a spray bottle with ethanol/IPA and put it next to your cutting mat.
Remove the print from the printer:
Open the doors of the case and loosen the star knob. Take out the whole build platform but be sure to pour excessive, uncured resin back into the basin. Optionally you can use a second polypropylene container or some kitchen paper to catch any drops. Place the build platform on a few sheets of kitchen paper on the cutting mat. Clean the build platform, the print and resin drops on the machine with some paper towels.
Take the razor blade and peel the printed object from the platform. This can be difficult so take your time and be very careful not to damage the printed object.
Clean the build platform and printed object with some kitchen paper. Make sure no solid parts of resin are still clinging to your build platform. You can now immediately use the build platform again for your next print. If you are done printing you should clean your build platform with some kitchen paper and ethanol/IPA.
Clean up your prints by dipping them in your container with ethanol/IPA, preferably agitate your print in the solvent to dissolve any excess resin. You can reuse your ethanol container quite a few times, no need to throw it out after every print.
Next rinse of your model with some ethanol/IPA from the spray bottle. Once your satisfied, leave the model dry.
When the model is dry you can do a finishing cure with an UV cure box or put your models in direct sun light.
Step 28: Cleaning Up
Tools/materials:
Funnel
Paper towels
Gloves
Safety glasses
Spray bottle with ethanol/IPA
Small container
If you want to stop printing you should remove the resin from the basin. It should not be in there for more than 8 hours depending on the resin. The first few times you may struggle a bit but after some practice this will be a very easy process.
To remove the resin from the basin you need to get the basin out. Remove the two bolts from the side of the basin and remove the basin from the printer. Be sure not to accidentally hit anything in the process. This is the hard part, its a large flat basin with a lot of resin in it.
If you are using a pigmented resin (such as the Fun To Do resin) you might have to agitate the resin to re disperse the pigments. Since you are wearing gloves and have some paper towels near you can use your index finger to stir the basin. Make sure to move over the bottom of the entire basin with a finger to search for any debris and mix the pigments through the resin. After stirring wipe your finger clean on some paper towels.
Now pour the resin back into the bottle with great care using your funnel.
Now the resin's out of the basin, close the bottle and clean the basin with a sheet of kitchen paper and some ethanol from your spray bottle. Just some gentle wipes should do the job, putting any force or pressure while wiping might scratch your coating. Don't mind using an extra sheet or two of paper towels if you feel you need to.
Use a dry sheet of kitchen paper to dry the basin and it's ready for the next print job!
Look closely on the printer to see any drops of resin that may be there and clean it.
IMPORTANT: Don't use anything else than ethanol/IPA to clean resin! Water and soap are useless and contaminate your future print jobs. Also don't try other cleaning products you may have at home. It might seriously damage your basin.
Now that everything is clean again, make sure you have turned off the projector and the brain. All is now ready for tomorrow.
Waste
This manner of 3D printing uses a lot of paper towels. Towels to wipe drops of resin of the bottle, the printer, your hands and work surfaces. Wet resin is considered chemical waste, on the other hand cured resin is considered plastic. Ethanol/IPA and contaminated forms of your solvents are also considered chemical waste. So please dispose of all solvents and paper towels accordingly as well as any left over resin.
Paper towels
There are a few ways to deal with this without producing tons of chemical waste though. You can leave your paper towels dry on a well ventilated area and cure any resin on them in the sun. Once dry and cured they can go in your normal household trash.
Solvents:
Collect all your used ethanol or IPA in a polypropylene or glass container and bring it to your city's wast disposal plant when full. Mark clearly on the outside whats on the inside and it should be no problem.
Left over resin and empty resin bottles:
If you ever have some left over resin but don't want to bring them to the waste management plant for what ever reason you can do the following. Take a large flat polypropylene bowl and pour a thin layer (1mm) of resin in it. Cure the resin in the sun. repeat this process until all your disposable resin is fully cured. Now you can chuck it in your normal trash.
Clean out your empty bottle with a bit of ethanol/IPA, repeat this cleaning at least three times. Collect your waste solvents. Now leave the bottle on a well ventilated area with the cap of for a day or two, once dry you can dispose of the bottle with the normal trash.
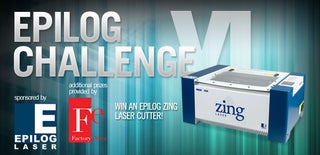
Participated in the
Epilog Challenge VI