Introduction: Basic Leather Half Mask Tutorial
Welcome!
Here you will find a tutorial about making a basic leather halfmask ( as show in the 2nd photo).
I have been working with leather for over 18 years, and just wanted to share a basic walk through on how to make a good mask of your very own :)
Feel free to join us in our adventures on Facebook or check out our Store !
Or Watch me Live on Monday/Wed's at 6pm cst on Twitch.tv
-Quinn ( Parkers and Quinn)
Step 1: Materials List
Choosing what thickness of Vegetable tanned leather can be tough at first. This tutorial uses a piece of 4oz leather.
The smaller the number, the thinner the leather. It's a balance of thin(accepts detail well, but flimsy-can lose shape over time) versus thick (strong and durable/ridged but hard to shape and mold fine detail)
Personally, I prefer using 5-7oz Veggie tan for most of my work. 4-5oz for small super hero type masks, or 8oz if I am Tooling/carving/stamping- or making a helm/mask combo.
With time and practice you will figure out what thickness of veggie tanned works best for you. All veggie tanned leather is a pink-pale skin color, due to the tanning process, this leather is great for water molding/forming, and is undyed so we can finish it or paint it however we want.
Basic needed parts:
- A piece of VEGETABLE TANNED leather. (4 oz-6 oz)
- Piece of printer/computer paper (for stencil)
- Ballpoint Pen/Pencil (pen preferred for marking on leather)
- Scissors (use leather shears if you got em!)
- Ribbon or elastic (for ties)
- Head form (Basic Styrofoam/wig heads or sculpting busts * Important* Make sure you headform looks like a real head. Those cheap 4.99 heads that look like a tiny alien face are great for wigs, but won't give you the proper fit in the finished mask!)
Optional:
- Spray bottle
- Mallet
- Carving/stamping mat and hard surface
- Hole punch
- x-acto or precision cutting instrument
- Leather Edge beveler ( this is the only optional item I use in this tute)
Step 2: Making the Template/Stencil
I use a piece of computer paper for all my pattern drafting. It's cheap and easy to fold.
Once you have a good tested/working pattern that you like, it's a good idea to trace the flimsy paper pattern on to something thicker, like cardstock, manilla folders or some other heavy weight paper/thin plastic.
- Fold the paper in half
- Working "in from the fold" draw an eye shape, starting about 3/4" in from the fold. The eye should be a couple inches long. mine are 2.25" long and 1 inch high.
- Next, draw one half of the mask. you can start with a basic shape, or go for something with a little dimension. this is all about trial and error, experimenting and improving. start simple, and add on as you make the next, and the next.
- Keep that nose and bottom cheek line fairly close to the eyeline. since this is just a halfmask, you are going to want it to come up a bit at the nose, like in the 3rd photo. this makes it easy to fit many faces, and more comfortable to breathe in.
Step 3: Cut Out Your Template
Cutting from the fold line, keep both sides together and cut around your lines. Remember, you can always trim off and slim things down, so going a bit oversize is better then needing to add on (and restart the pattern)
- Cut out the basic pattern, keeping the 2 halves together while you cut on the lines
- Unfold and cut out the 1st drawn eye.
- Fold together again and draw the line for the 2nd eye, following the hole you just cut
- Unfold and cut 2nd eye.
Your Template is complete!
Step 4: Transfer Your Pattern to the Leather
There are 2 sides to a piece of Vegetable tanned leather. The top/Grain side ( the smooth skin side) and the bottom/flesh side ( the fuzzy side)
- Flip your leather piece so it is Fleshy/fuzzy side up.
- Put your paper template down and arrange so it fits with some margin around all sides.
- Hold or weight down in the center.
- Starting with the eye holes, trace your pattern on the flesh/fuzz side, taking care to go slow and not move the pattern. I find that using a ball point pen works the best for this, hence why we are tracing to the back/unseen side of the mask.
Step 5: Cut Out Your Leather Mask!
Taking care, cut out the leather with your scissors. Sometimes it can be helpful to very lightly mist the flesh side with water *spray bottle* but be careful not to saturate the leather, as it will distort if you pull/push while cutting!
Once the outside is cut, you will have to cut out the eye holes. It helps to wet the area you will be cutting, but again, take care not to overcut,mark up or stretch out the holes as you cut. Some people prefer an x-acto or similar tool for this.
I find using scissors works best for me with this Oz/thickness of leather. If I am using thicker leather its about 50/50 x-acto to scissor ratio personally. If you wet the leather (just the eyehole) then lightly fold the mask, then snip a starter slit in the center of the eye, it is much easier to get your scissor right on the line and make a nice edge.
Optional:
Use an edge beveler that is the correct size for your leather thickness. This is not required, I just find the piece finishes out nicer if you do this, especially on masks over 7 oz+.
Also as this point you would tool lines/stamp if you were going to do that, but this is a basic mask, so we are skipping ahead, now on to shaping!
Step 6: Wetting Your Leather (without Cooking It!)
Get a pot ( I use a cheap enamel one that is NEVER used for food) and put a good amount of water in, alternately if you have no pots that are suitable, you can use your sink, if you run the hot water to the point where its steaming and as hot as it will go- then plug up the basin and let it fill. It really important that the water be as hot as you can stand, but NOT SCALDING/BOILING.
Ok, this is super important. DO. NOT. OVERHEAT.
*Ideal temp is 120*
If your pot o' water is boiling, you are going to boil that leather. Leather is just skin, so if the water would burn your hand, it's going to be too hot for leather.
It is better to err on the side of caution, hot water is best, but you can do with room temp water if you want to - it just takes longer to dry and is a less rigid final product.
- Once you have your hot(but not scalding) water, place your mask (part or all if it fits) with the fleshy/fuzzy side up and let it soak some water! it will bubble and make noises and all that fun stuff.
- After about 20 -60 seconds, the bubbling should be minimal, pull that mask out and plop it on the face/headform with the GRAIN(Smooth top) side facing you.
On to molding and shaping the leather!
Step 7: Shaping/Molding
This is the creative part, and sometime it can be frustrating, but just keep at it and you'll see results. Think of the wet leather as clay (kinda) if you push, or pull or stretch it, it effects the fibers and shapes it if you are persistent. You have about 10 min of good working/shaping time. Each piece of leather is different tho- and working times may vary.
Be wary of your nails, you can mark up the grain side while you pinch and pull. Just a heads up!
- After the wet mask is on the face form, start at the nose/eye area and work your way out.
- Push the leather in to the crease, and pull the leather up for areas that you want ridges formed.
- Pinch and push and squeeze to make brow ridges, eyelids, nose bridge and such.
- Be creative! if your mask has dangley bits, pull on them or twist them and roll them up.
- Be persistent. sometimes the leather doesn't want to do what you want it to do. keep going back to the problem area, and re-twisting or pinching, as the leather dries you will notice it stiffen and hold its shape better.
- As it is drying, it is the perfect time to refine detail, but lay off trying to make major changes.
- Let it dry over night. you can use an oven at a very low temp(under 160) to "bake" a semi dry mask, but if these are your first masks, its really best to just let them dry on their own!
Working with leather will dry out your hands, so don't forget, once you are all done shaping/sculpting and it is off to dry for the day- put some lotion on your hands! This is something I wish I had started doing from the beginning, many years ago :)
Step 8: It's Dry, Now What?
Paint!!
You can use pretty much anything to color your mask, but leather dyes/gels, and any water-based paints are the best!
- Airbrush
- Hand paint with brushes
- Sponge paint/faux metal and stone finishes
- Rub n Buff (keep in mind this seals the leather since it is a wax, so you can't add color over top)
Ties:
Make a hole a half inch in from the edge, at or a little above eye/ear level, and tie on your ribbon, elastic or leather strapping. You can always use a strap and buckle- and is recommended for larger or heavy masks (like the orc masks, etc).
Topcoat/Finish:
Seal your leather mask using a spray on(spray can) matte or glossy acrylic, or leather sealant. You can also seal the inside of your mask using:
- acrylic resolene
- tan-kote
- liquid latex
Step 9: It's Done! (aftercare)
With your mask finished and sealed, it requires very little care. You generally want to avoid water on your mask whenever possible, since that is how you shaped it in the first place! No oiling needed. Just keep it dry and cool.
A little sweat or a sprinkle isn't harmful as long as you sealed your piece properly. Remember tho, it's not waterproof!
If it gets really wet, just place it back on the headform to dry, or tie the straps so it retains it's shape as it dries. Easy!
Now that you have a working/successful basic template, you can go back and make changes and all sorts of new mask shapes, improving and elaborating on your starter shape. The sky's the limit!
I'm happy to help with questions and such, just send me a comment /inbox me here or shoot me a message on my Facebook, below!
hopefully this will help some of you out there make a new leather mask and fall in love with crafting in leather!
-Thanks and Well Wishes,
Quinn (Leatherworker)
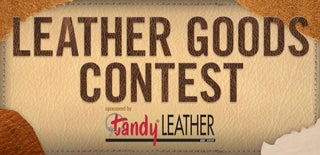
Participated in the
Leather Goods Contest