Introduction: Branch to Box: Dice Tray Made From Firewood
Two or three years ago I had a tree taken down on my property, which meant I was left with a massive amount of firewood. I also began remodeling the house. Which meant the likelihood of having a fire (bon or otherwise) dropped down into the slim to none range.
I decided to grab a piece from the pile just to see what it would look like. Poplar is not known for it's beautiful grain or color so I wasn't expecting much. What came out from my table saw was some of the most gorgeous figure and pattern I've ever seen. I knew I wanted to so something more with it than just burn it. I make dice trays and deck boxes as a sideline business for Etsy, and I knew this would be perfect for it.
Tools Needed:
Table Saw
Sawzall
Mitre Saw or Mitre box and Saw
Router with Bit
Handplane
Chisel and Hammer
Xacto or Utility Knife
Belt Sander
Random Orbital Sander
Square
Tack Hammer
Respirator
Ear and Eye Protection
Materials:
Firewood (Needs to be at least 3"x3" thick and 6" in length)
1/4" Plywood
Microsuede, Suede, or Leather in color of your choice
Glue
Painters Tape
Boiled Linseed Oil
Paste Wax
Copper Tacks
CA Glue
Step 1: Important Caution
This wood has begun decomposing. It's covered in dirt, bugs and mold has colonized the grain (what is referred to as spalting). None of that stuff is good for your lungs. For most of the work, you'll want to wear a respirator.
Step 2: Choosing and Preparing the Wood
For a piece this small, figure is more important than anything else. Look for knots, bulges, lumps, twists or Y's (where a branch splits into two smaller pieces). This is where the wood grain will be most figured. This also makes working with the wood initially difficult.
The first order of business is to create a flat and stable face to reference from. If you're lucky, one of the split faces will be flat enough. If not, you'll need to make one using a hand plane, hammer and chisel, or a planer if you have one.
Hold the piece securely and go to town. Try to work across the grain at a 45 degree angle as this removes the most wood in the cleanest manner. Don't worry about finish at this stage. This is just to get a rough and workable surface for the following steps.
It only takes a few minutes to get a good face. From here we can move onto the table saw. You'll notice from the photos that the piece isn't level in all directions. This is not ideal but is okay. The major concern is if the piece racks and pinches the blade. That will either bind the blade or cause a kickback. Neither are good. In the photo above, the piece of wood won't twist perpendicular to the saw blade so there will be no binding. If it does twist, it's going parallel with the saw blade, which doesn't matter .
Step 3: First Cut and Decision Making
Now it's time to take the first cut and see what we're working with. My saw fence is broken, so I'm using a straight piece of wood with a few clamps as a makeshift fence. I'm comfortable working with my sawblade at full height from the beginning, but if you're not, make this cut as a series of passes. Each time just raise the blade another 1/4 to 1/2 inch.
The waste side is on the side away from the fence and the flat face prepared in the last step is down against the table. I was lucky to have a straight edge to run against the fence. If you don't, you'll need to flatten that face as well before making this cut.
My first cut went fine, but it wasn't deep enough to clear all the way through. What I should have done was use a sawzall to finish the cut. The table saw made a deep enough kerf that the sawzall blade would have followed without issue. What I tried to do was flip the piece and make a second cut with the table saw. This obviously did not go as planned. I removed my shame with a chisel and ended up with an edge that was perfectly square relative to the base.
There's a knot in this piece that should have some great figure surrounding it, but I wasn't sure what direction it would go inside the piece of wood. I could keep cutting with the knot facing up or with the knot laid to one side. After looking at all four sides, I decided to leave the knot facing up as it looked like that knot ran across the width of the firewood.
Thankfully there's... knot a wrong answer :)
Step 4: Bookmatched and Beautiful
The knot stuck up further than my sawblade would be able to cut through, so I decided to remove it. With three sides square, it was simply a matter of cutting as high as my blade would allow, flipping the piece and then cutting again.
Reposition the fence to 1/4" to 3/8" away from the sawblade, use a square to ensure the blade is 90 degrees to the table then begin making your cuts. I used a scrap piece of wood as a push stick and my other hand was keeping the wood tight against the fence to ensure a straight cut. As the piece gets smaller, use a second push stick instead of your hand.
Any slight deviations or scrap pieces can be cleaned off with a plane. What came off my table saw was gorgeous material. Spalting ran through out the piece and there was wavy compression patterns around the knot. By cutting four pieces from the same block of wood, you end up with what is called "bookmatched" grain. That means that two of the pieces are mirror images of each other and, if assembled correctly, the grain will run in a continuous pattern across all four pieces.
Step 5: Continous Grain, Stabilizing, Sizing and Mitering
Some of the cracks in the wood were deep enough that they needed stabilizing, and as could be seen in the last step, the knot worked itself out of the last two pieces. For small pieces like this I use CA glue. It's thin enough to be absorbed and it dries quicker than epoxy. Every crack was filled with glue. Where needed use a strip of painters tape to hold things together until the glue sets.
At this stage it can be difficult to see the grain pattern. Wet the edge with a little mineral oil or solvent of some kind (mineral spirits is a good one) to make the grain pattern more visible. The good thing about book matched wood is that there's only one way to orient them for continuous gran. That's also the bad thing about it. There's only one way to get it right. Take your time and write "OUT" in large letters on each of the outward faces.
There are almost an infinite number of ways to make joints for a box and all of them look beautiful. For this project we're going to miter the corners. Mitering means to cut a 45 degree angle on each edge. I like to size my work first before cutting the miters as I use the outside corner for a reference.
Sneak up on the cut, make sure the word "OUT" is always facing visible, and everything will be fine.
Step 6: Groovy
The last step is to cut a small rebate into the wood to receive the base. I used a router table for this step but it's equally possible to do on a table saw or by hand.
I'm using 1/4" utility panel left over from another project (shameless plug) for the base. It's a hardwood plywood that is inexpensive but has a nice surface, and I have 15 or 20 linear board feet laying around my shop right now. Set the router fence back the thickness of the plywood plus a little bit. This is going to be how far into the box the plywood will sit. Then set the height of the router bit to just under half the thickness of the box sides. Make a test cut in some scrap as a precaution. Adjust as needed until everything looks good.
Step 7: Sanding, Sanding, and More Sanding
I use a belt sander with a 120 grit belt to remove the saw marks and smooth everything out. There were a few deeper saw marks that I worked over with a hand plane and then sanded smooth again. After the rough sanding, I switched over to my random orbital sander and worked the wood up to 220 grit. I don't tend to go much beyond 220 on any project, but if you want to keep sanding up to 400 or 600 grit wait until after we apply a finish. The wood will absorb the finish better with a slightly rougher grit.
Step 8: The Glue Up
We're going to use the painters tape clamp method for this glue up. Before applying the tape, wipe the surfaces down with some denatured alcohol to remove any dust. It will let the tape stick to the wood better and make for a less stressful glue up.
After that, place a piece of table on the inside edge of each miter, as this will make cleaning up any squeeze out easy. Arrange all your pieces in order with the outside face showing and the rebates all aligned on the same edge. Tape the joints together and don't be stingy with the tape either. It's cheap and more is better.
Carefully flip the whole assembly over and apply glue onto each angled face. End grain likes to soak up glue, so I like to apply glue two times. The first time, I smear and press as much glue into each face as possible to help the wood absorb the glue. Then when I add a bit of glue the second time, it sits on the surface and bonds properly.
Carefully assemble the box and tape the last joint closed. Use a square to make sure the corners are at 90 degrees or close enough that you can't really tell and then set the box aside somewhere to dry.
Step 9: Sizing the Base
If you're careful, you can do this step while the glue is drying. Otherwise go and do something else for at least 20-30 minutes before handling your nascent dice tray. I'm a touch clumsy, and my chisels were dull, so I spent 30 minutes sharpening them.
Roughly cut a square of plywood and set the dice tray on top. Trace along the outside edge of the tray. Because of how thin the walls of the tray are, there's not a lot of room for error in the base. We're going to sneak up on a perfect fit.
Cut along the line and set one corner of the plywood into the rebate. Mark the excess material and make another set of cuts. Keep cutting and fitting until the plywood just barely drops into place.
Step 10: Time to Dress It Up
I decided to go with red microsuede for the lining as it complimented the warm tones of the wood. Oversize the piece of fabric by roughly and inch.
Spray adhesive will get everywhere and it stays sticky for months. Cover your bench with paper towels and carefully spray a light coat onto the back of the fabric and the back of the plywood. Follow the instructions for dry time and then position the fabric glue side up on the bench. Slowly lower the plywood onto fabric and press lightly down.
Flip everything over and smooth the fabric, pressing it firmly into the wood. If there are any wrinkles, you can try to carefully reposition the fabric.
Use an xacto or sharp utility knife to trim the excess fabric away.
Step 11: Fixing the Glue Up
By this point, the glue should be dry enough to remove the tape. Take a second to inspect the corners. Even if you're carefully sometimes things just won't line up properly.
If it's the outside edge, simply sand it flush and feather it out across the board. If it's an inside edge, use a chisel (maybe a recently sharpened one?) to remove the waste and then feather the edge out with a sander.
In either case, feather the sanding out over 2-3 inches to hide the transition.
Also take a second to clean off any glue squeeze out that might have happened as well.
Step 12: The Wow Moment
Now is the moment you've been waiting for. It's time to apply the finish! For something like this a combination of oil and paste wax is ideal. The grain will practically glow after just a few coats. I like to finish right on my bench with just a couple paper towels laid down to create a clean surface.
The first thing is to use denatured alcohol to clean the surface of the wood. This gets any dust and debris off which ensures a better overall finish. Use a shop towel soaked with alcohol and wipe down everything. It doesn't take very long to dry and once it's dried we're ready for the payoff.
I've found that using a shop towel soaked with oil and gently rubbing it into the wood results in a gorgeous finish that dries quickly. It's less messy and more enjoyable than the manufacturers instructions of flooding the surface and waiting 10 minutes before wiping off the excess. Just keep rubbing in more and more oil until the wood looks good to your eye. A small chip brush is perfect for applying oil into any of the rough or uneven live edges.
After the wood is dry to the touch, I apply a coat of paste wax. This is homemade material of beeswax and mineral oil, so it's safe to use without gloves and it smells great also. Just rub it in vigorously and then buff with a rag or papertowel
Step 13: THE MOST IMPORTANT STEP
Boiled Linseed Oil will spontaneously combust if not disposed of properly. As BLO cures, it generates heat. A bunched up rag will act as an insulator and trap that heat until it reaches the flash point of the linseed oil and then your house burns down.
My patio has these hideous, 60s aluminum trellis frames that I hang any rag soaked in a finishing oil from. This keeps plenty of air flowing around the rag, which keeps it cool. If the worst should happen, the trellis is aluminum so it won't burn.
If I'm feeling really frisky, or if I have a project that needed multiple rags to finish, I'll toss them into my grill or fireplace and set them on fire.
Step 14: Bringing It Together (The Okay Way)
Now we're ready to glue the base into the tray. Set the tray upside down on the bench, place the plywood fabric side down into the rebate and weight the plywood down. Add a bit of glue into the crack and smear it along with your finger so it gently fills the seam. Don't use too much, or else it will squeeze through and ruin the suede.
Let the glue setup.
This is not a strong glue joint, so we're going to reinforce it with nails. The nails aren't going to provide any holding power, they're just going to give a mechanical hold to keep the base from falling out.
Measure in from each corner 1-2" (your preference) and make a mark 1/8" up from the bottom. Using the smallest drill bit you can find (1/16" for me), carefully drill a hole. Try to angle the drill slightly away from the fabric side of the box. With the hole drilled, add a bit of CA glue into it and gently tap the nail into place.
1/4" plywood is hard to drill into because of how thin it is. I had a few nails blowout the bottom. These can be hidden by feet. I had a 1/2" wide by 1/4" thick piece of poplar that I cut into 2" long pieces, added a slight chamfer on three sides and then glued into place to hid the feet.
Step 15: Bringing It Together (THE BETTER WAY)
I slapped myself in the forehead when I realized there was a better way to glue the base into the tray...
Hot Glue.
Hot glue is easy to apply, doesn't run, and when it cools stays flexible enough to account for the natural movement of the wood. Using hot glue instead of wood glue means you shouldn't even have to use nails. Although they do add a nice touch at the end.
Step 16: Le Fin
This wood is gorgeous! The grain is incredibly and all the little details are amazing. This is a piece that is going to make all my friends jealous when we play games together. And that's really what this is all about!
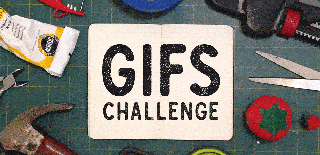
Runner Up in the
GIFs Challenge 2017
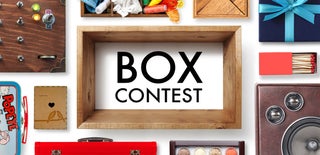
Participated in the
Box Contest 2017