Introduction: Build a Pirate Ship Wreck
Each year my wife and I enjoy Halloween with the neighborhood by getting everything all decked out (excuse the pun) in pirate fashion. We tend to lean towards making all of our own props for Halloween and generally any store bought items are usually modified in some fashion to suit our own needs. As the years have gone by and additional props have accumulated, we decided to delve into a much larger prop, a pirate ship wreck. This is my second pirate ship wreck. The first was only used once and the design was poor. I learned a lot during both builds and hope you enjoy this tutorial.
Fortunately for us, our yard is a corner lot that is comprised essentially of a rounded hill with two very tall palm trees. It sort of looks like a desert island. This is not to mention that we are on a well-traveled road so we always know there will be plenty of treat-or-treaters stopping by Halloween night. We thought that in order to accentuate the look of our yard and play along with our pirate theme, we’d build a full scale pirate ship wreck.
Halloween is kind of a fun day for us and I have been making things for Halloween since I was about eight years old. We really enjoy the happiness it brings our neighborhood considering not many people decorate at all for Halloween anymore. This ship too about eighty hours to complete, most of which was crunched into the last few days of the build. I had a few friends who gave us a hand and probably would not have made my own deadline if not for them. Their assistance was much appreciated.
Step 1: Materials Needed for the Project
Now you might be wondering what this ship is made of. Most people think we made it out of wood but
seriously, wood is just too darned heavy and storing this ship would have been a nightmare. So we used the following:
- R-Tech ½ inch foam board
- R-Tech 1 inch foam board
- Foamular 150 1 inch foam board
- Foamular 150 2 inch foam board
- Great Stuff expandable foam
- 1.2 inch round steel tube .065 thick
- 1 inch round steel tube .065 thick
- 1 inch square steel tube .065 thick
- 1/8 inch wire
- 3/8 inch wire
- Various mis-tinted paints
- Masking tape
- Hot glue
- Bailing wire
- Plastic fluorescent light covers
- Various foam skulls and bones
- Various creepy cloth sheets
- Small wooden dowels
- Various plastic skulls
- Precut wooden lettering
- Various sized lengths of rope
- Various diameter pvc pipe
- Various diameter pvc sewer pipe
- 3 rough cut fence board (for ships wheel)
- Various hardware (hooks, screws, bits of wood, u-bolts, eye bolts, etc.)
A word about the foam board. The R-Tech foam board is the white foam board and is usually described as a high performance rigid foam board. It’s not really rigid, especially if you purchase the ½ inch thick stuff, which makes it ideal for skinning your pirate ship. The Foamular is high density foam board and it is rigid. There’s no bending that stuff which makes it perfect for any details on the ship like crow’s nest types of pieces.
With that all said, let’s build this thing. By the way, I am new here, so any votes and likes as well as words of encouragement are greatly appreciated. If you have questions, please ask. They will tell me if you’re enjoying yourself with my first instructable.
Step 2: Tools Needed for the Project
I guess you ought to know exactly what I used to make this ship. I used all hand tools as you can see by the pictures. You’ll probably have most of this stuff already if you’re into making things. If you’re working with steel, I highly recommend getting a small welder and learning to use it when you have the means to do so. If not, you’ll have to find a friend who can weld for you.
As far as the foam is concerned, I use the Hot Wire Foam Factory foam knife kit for almost all of my cutting. If you do not have one of those kits, they are well worth the investment as well. The other odd tool you’ll see in my pictures is the little flat, shiny metal pieces. These originally were double the length you see in the pictures with four holes, but for my purposes, I just cut them in half and gained two tools for the price of one. I think each complete one was seventeen cents so the final price for each one I ended up with was eight and a half cents. More about those later. Again, the rest of the tools are pretty standard.
Step 3: Design Your Pirate Ship
My pirate ship is actually made up of five separate pieces. A bow, two mid sections, a stern and a galleries. I did this because transporting a thirty-five foot long ship through town would have posed many issues as well as permitting problems. This is not to mention, storage issues later. At least now, I can transport them to my home a piece or two at a time and then I can take these pieces back to my warehouse (work) and hang them on the walls where they are out of the way. The frame, which we will talk about next is very light weight and sturdy and even more so because the ship is made of smaller pieces.
I also had to consider assembly of the ship with my design. Let me tell you that installing the masts looks easy, but they get very top heavy with rigging and length, so placement of the masts within the various ship sections is crucial in your design. I start by setting up the bow of the ship first. Then I install the bow mast because I can stand right alongside of it while doing so. Reaching into and over a ship section to install a mast is too risky. You might accidentally fall into the ship as you install the masts and damage it.
Then I place the next mid ship section. Now my design always called for installing a section, then a mast, then another section so as you can see, I made a slight mistake with my second mid ship section. The main mast should have been installed on the rear of the first mid ship section and no mast on the second mid ship section. Mine is backwards but luckily the section itself is very low to the ground so installation of the mast is tricky but not too difficult. Then the stern is installed. After that, the galleries are installed and finally the rear mast. The rear mast is light weight so reaching in and installing is not too difficult either. Just take your time and plan properly.
Step 4: The Ship's Frame
I use only .065 thick steel tube because it is strong, easy to bend and easy to weld. The one inch diameter tube is used for the frame that sites on the ground. The half inch diameter tube is used for any major frame area on the sides or deck where I need strength. All of the various sized steel wire is simply used to add additional structure for attaching foam boards. The more wire you use, the more shape you get out of the frame, but that comes at a cost. The more wire you use, the heavier it gets. I try and shoot for a one foot grid of sorts.
Start by making the ground frame. The bow ground frame should be triangular in shape to accommodate how the very front of the ship both tapers in towards the front and tapers in from top to bottom. The ground frame for the mid ship sections are almost rectangular and the stern will have a more rectangular shape that tapers towards the back. Now because my yard is smaller than the ship I wanted, I had to model in forced perspective. So my ship has a severe bend in it on the port (left) side and it tips towards the port as well. You’ll see this in images where you look directly at the rear of the ship, for example. It is a really odd looking shape, but because you are never looking directly at the rear of the ship when it is set up, you never notice. Instead, the ship looks normal when viewed from the angle I want you to view it from and subsequently looks longer than it actually is. Remember, forced perspective – Disney and Universal are masters at this.
The galleries of the ship were the trickiest. I used three-eighths inch wire for the window frames and one-eighth inch wire for the window dividers. Cut fluorescent light fixture plastic by scoring it into the shape you need for the windows. Make them slightly larger. Drill small holes in the edges of the plastic so that small wire can be used to wire tie the windows to the frame. Eventually those wires and the spray foam will be what holds the windows in place.
As far as the frame sections that contain masts are concerned, you will want to create square holed frames in the deck and then a receiving square hole or other receptacle in the ground portion of the frame to accommodate the mast. This way when the mast is installed, it will slide into place through the deck and lock into place at the ground level.
If you noticed, my yard is not flat. Yours probably will not be either. It's best to build the basic frame without and wire welded in and test fit it before you go through the trouble of undoing all of that work. In my case, my ship pieces would have had large gaps at the top and no gap at the bottom where they joined. I knew this and ended up taking measurements between each ship section before finishing all of the cage work. Of course then nothing at the shop lined up on a flat floor anymore, but that is how it should have been. When it was back in the yard all of the pieces fit perfectly.
Step 5: Skinning the Ship
Take a close look at the white foam board. You’ll notice that it will most likely have a white printed plastic sheet on one side and a silver, reflective plastic sheet on the other side. Do not peel anything off of the foam yet. The silver reflective side will be placed so that it is on the inside of the ship. Lights and other flashy, blinky effects are accentuated by this reflective surface. The plastic sheeting provides strength for the foam. So you will leave the silver reflective sheet attached and in the end, peel off the white sheet on the outside. Now if you look at the foam board you’ll also notice a grain to the material. That’s right! It looks like wood grain. What a benefit for a task like this, right? So make sure when you are applying the foam boards that the grain at least sort of follows the length of the ship for the planks and deck and then follows the direction of any other area that the foam is being applied to.
Remember those little metal rectangle tools from the tool section? Those are what you will use for attaching the foam. Sometimes I use masking tape, but almost always use these little metal plates. Basically, with assistance from someone else, you will poke a hole through the foam board in a pattern that matches the two holes in that little metal tool AND is on either side of any portion of the wire or tube frame. Then you use a length of twist tie pushed through the metal tool and the foam where the twist tie is ultimately twisted on the inside of the ship. This holds the foam board in place while you glue it permanently to the frame works. In some cases, you might have to use the little metal tools on both sides of the foam board so that the twist tie does not cut through the foam board thereby not allowing you to fasten to the frame. You will have to be the judge of that.
I run as many full sized pieces of foam board as I can and trim after they have been glued in place. Always keep the spare foam for use later. The foam board is not always going to follow the compound curvature of the ship so you may have to slice it here or there in order to get it to flow better. Do not stress about the initial look of this as it is a ship wreck and once all is complete and painted, areas like this look like additional damage.
I have tried many types of adhesives such as, spray adhesive, liquid nails, silicone, etc. None of that stuff worked. I felt stupid the day I called the manufacturer of Great Stuff spray foam and asked them what glue is best for gluing foam board. They told me that their spray foam was originally intended to be used as an adhesive and that I should use that. What a great idea.
So that’s what I use. I spray the foam on either side of the frame wire or tube and if needed cover the frame completely. Do not try and build up too much at one time as it will expand and if too much is put on it will weigh too much and fall off. You can always add more once a first application starts to set up. Let me interject here and tell you that I built my stern and galleries as one piece and then cut them apart to ensure a good, snug fit. That foam pulled on various areas of the frame and literally mis-shaped it to some extent. In the end I had to really play with the attachment of both pieces to get them to fit again. That’s how strong that foam is.
Once the foam has cured at least four to five hours, you can remove the little metal tools attached. Simply snip the twist tie on the outside of the ship and pull the metal piece off. Then use pliers to grab hold of the twist tie on the inside of the ship to pull through and remove them.
Once they are all removed, the outside plastic sheeting can be peeled off. Grab a corner and start to peel. It’s a bit tricky, but it comes off easily. Peel it all off and the wood grain effect will look great once painted. Use the hot foam knife to trim off all of the unnecessary foam as needed. Remember to trim away the foam that is now covering the windows in the galleries as well. Take care to make sure and only trim inside the area of the window. I made the mistake of cutting outside on my ship and made a hole. Remember though, this is a pirate ship wreck so extra damage that is shoddily repaired always looks good anyway.
Step 6: Adding Detail to the Skin
The next step is to get the planking and pegs carved into the ship hull and deck. The first thing I do is use a sharpie to draw my planks onto the foam. Look at some pictures of wooden ships to get the correct look for laying the planks out. If carved incorrectly, it cannot be undone and will be a distraction to the finished piece. I use a ¼ inch metal grinding disk to essentially saw in my planks. Do not be concerned with the lines being 100% perfect but instead making sure that they all flow in the proper direction. Do not saw these in too hard or too deep otherwise you will ruin the skin. Remember that silver shiny plastic sheet on the inside of the ship? Not having that there during this procedure would make this task almost impossible because the foam would crumble.
Once the planking lines have been carved in, carve a few vertical plank lines to simulate where two planks meet. Again, you do not need a lot of these but rather just enough for effect. Now where you have just carved in the vertical lines, you need to add pegs to the foam. Use a hole saw and gently by hand, twist the saw into the foam just enough to create a circular cut. These will be the pegs in the planks. Once again, only put these where you carved in vertical plank lines. You only need enough of them for effect.
Finally, use the foam hot knife to carve in wood splits between planks. Heat the knife up hot and barely touch random areas of the planks with the flat side of the knife and let the heat weep away some of the foam. The plank will now look pretty aged and damaged. Be careful though. Too much of a good effect is too much and will be a distraction. You want the viewer focus to be on the ship as whole not the pieces.
Step 7: Adding Trim Pieces
Remember all of that foam you just trimmed off of the ship? Use that for creating trim pieces for the deck and such. Make sure to cut everything with the grain for a more realistic look. Remember that I said spray foam was originally intended to be used as an adhesive? This is where that takes place. Now you can’t just apply spray foam to a trim piece and stick it to the ship. This spray foam happens to be gap filling which means it expands as it sets up. So if you spray some on a part and stick the part in place, a few hours later the piece will be sitting two inches higher than you intended. That’s not a good look.
I have a solution to that though. You will need a plastic spreader, the trim piece and some spray foam. Wear gloves for this because that spray foam is very sticky and tends to get everywhere. Spray a small amount of foam on the trim piece along the entire length. Use the spreader to smear the foam around and work it smooth. This action essentially keeps the foam from expanding to its full potential. Yes it will still want to expand, but not nearly as much as normal. So if you use masking tape to tape the piece in place, the foam will set up and act only as a glue. In any areas where you do not use tape, the piece may rise up a very small amount, but in my opinion that makes the trim just look warped and unkempt which again is perfect for a pirate ship wreck.
Step 8: Painting the Pirate Ship
Constrast, contrast, contrast. I cannot say it enough. The key to the most realist looking paint jobs come from multiple contrasting colors. Dark colors for the base and contrasting light colors as highlights. Speaking of paint, I always hit up the local paint store for mis-tinted paint. At five dollars per gallon, you can’t beat the price. With that said, they will almost never have the colors you want. Just ask the paint rep which ones can be tinted towards the shades you need. He or she will be happy to tell you and if you ask nicely, will also be happy to tint those to something useable for your ship.
All the paint in my picture cost me about eighteen dollars. Some had been sitting there so long, I was getting fire sale deals. Those chip brushes are the cheapest brushes you can find. Normally I would avoid them but for a ship wreck project, they are perfect.
The base color I use is always dark. Not black, but dark. I generally go with purple because I know I’ll have orange trim pieces at some point. In case you did not know orange and purple are a paired color set. That means they look good together. So paint the entire ship with the base. I sprayed my ship because it cuts the work time down to virtually nothing in comparison to trying to brush the paint on. The base color needs to be good and solid. Let the base dry for a day.
Use the brown or whatever color you chose for the outside planking of the ship. You might have to try a little out before ultimately deciding on a shade. With my ship, I chose a brown that I thought would look good, but ultimately it ended up being too dark. I just lightened it and continued on. Now when I say use the brown to paint the planks, I do not mean paint this like you just painted the base color. Use a dry brush technique to brush the brown on. If you do not know what dry brushing is, I’ll give you the fifty cent tour, but you ought to look that up and see how it is done. I am sure Instructables has a tutorial for that. Essentially you dip your brush into the paint and then wipe all of the wet paint off of the brush. Then you lightly brush against the grain on the foam to highlight just the high areas of the foam. In doing so, the grain will stand out and look like real wood.
Continue to do this for the outside planking. Switch to an alternative contrasting color for the decks and do the same. Once all is dry, use another contrasting color for the pegs on the outside planks and another contrasting color for the pegs on the deck.
Now dry brush all of the trim. I used a third color for the trim on my ship. I think it gives more character. So basically, I used, purple, brown, light brown, bone, gray and orange. Those are pretty good Halloween colors too!
Step 9: Building the Masts and Bowsprit
I used to use those cardboard tubes that carpet comes rolled on for various Halloween projects, but most of the time they get damp and sag over time. I don’t care how well you think you waterproof them, they just do not do well outdoors in bad weather. So I switched to pvc pipe. You might be thinking that pvc pipe is pretty heavy. It is, but pvc sewer pie is not. In fact it is only a small fraction of the thickness of normal pvc pipe. That’s what makes it ideal to be used as masts. Plus you can screw things into it as well. Carpet cardboard tube does not handle screws very well. I will mention that the main mast lower piece is made of cardboard, but it is the cardboard tubing that is used as forms for concrete. Those can take moisture and water well.
Basically you will want to decide how many masts your ship will have. I chose three masts because I had plenty of time to get them all done. Bear in mind that with each mast comes rigging which essentially makes the masts top heavy. Also if your ship is built in forced perspective like mine, then the rigging will not be symmetrical, so do not build both sets of rigging for each mast copying one to another. They will not fit in the end.
Cut a length of mast you find to be suitable for your ship. Use a slightly smaller piece of pvc for the next higher section of that mast and cut it to length. Slide a short piece of 1x2 wood into the lower mast at the top end screw it into place. Use drywall screws.
Now before you attach the upper mast to the lower mast, get some of the rigid foam board. You’re about to make the floor of a crow’s nest. Cut a circular shape from the foam board and then use the foam knife and the end of a pen to carve in wood grain. The rigid foam board does have a grain but because it is not as apparent so you will have to add to that with the pen tip or other slightly sharp but blunt object. Now place the foam piece on top of the lower mast and position slightly off center. Trace around the end of the lower mast onto the foam. Use the foam knife to carve that piece out.
The new foam crow’s nest piece should sit down on top of the lower mast so that the top of the lower mast protrudes above the foam crow’s nest piece by at least 8 inches. Mark on the lower mast where the bottom of the crow’s nest will be and then drive four drywall screws into the mast. Drive them only half way. Use the spray foam to coat the foam crow’s nest and the lower mast and slide the piece in place until it rests on the drywall screws. Stand the lower mast up straight and let that set up for a few hours. Use the hot knife to carve the foam that expanded out during curing process.
Mark the crow’s nest for the upper mast that will that will top the lower mast. The upper mast should sit in front of the lower mast when it is situated facing forward on the ship. You can easily slide the upper mast through the new hole in the crow’s nest and drive a screw through the end of the upper mast into the lower mast and into the wood block inside it. Use a larger drill further up on the upper mast to make a hole to drive a screw through it and into the top of the lower mast. This way the upper mast and lower mast are connected at two points.
Use spray foam to inject foam into the gap between the crow’s nest and the upper mast. Stuff a piece of wadded paper into the top of the lower mast and bottom of the upper mast and use spray foam to fill in the ends of the masts. Trim the excess off later after the foam has set up.
Paint and dry brush the mast and crow’s nests using the same base coat/dry brush techniques explained earlier. How many tiers you have in each mast will ultimately be up to you. Study images of wooden ships online in order to get a feel for how they normally look. Use rope and hot glue to wrap the masts so they look like they are tied together. Follow the same procedure for each mast you need.
Step 10: Building the Channels
The orange block like pieces on the sides of the ship are called channels. You can see then circled in yellow in the first image. They are used to attach the rigging from the masts. Basically, they hold the mast in place from a side to side angle. On my ship, you’ll notice that I welded some ½ inch steel tube where the channels were going to be. That way when I did get the rigging cinched in place any extra pull from winds or the natural leaning of the ship would not cause undue stress on the channels. This also allows the channels to be used as hand holds only if needed. I specifically asked my assistants not to use them as handles unless there was no other choice. I might as well try and preserve them from damage as long as possible.
Step 11: Rigging the Ship
Rigging blocks usually take the shape of either a deadeye or a pulley block. These are easily made of foam as well and Google images has all sorts of picture examples of various blocks. Try to stick with the era of the ship but be creative. Speaking of creative, most galleries on a ship had supports under them. You can see these just under the edges of the galleries that hang over the side of the ship. Be creative with your design work with these as well. A friend of mine once asked me why I put so much detail into this ship. I told him it is because I know what it should look like and others will too. If it looks accurate (even if you have embellished) the end result will be pleasing to those who do recognize what a ship is supposed to look like.
The foam block that would become the channel would need a channel cut into it so that it would fit over the frame work. Use the hot foam knife to cut into the foam and carve out a channel. I caution you to pay attention though. Do not cut all the way through the foam block or you risk cutting and burning your hand. Apply spray foam inside the block and then press the block into place. Use masking tape to hold it in place until the spray foam cures. Once cured, you can drill the holes needed through the block to fasten the rigging.
The rope you choose for rigging should be sort of soft. I by large spools of nylon anchor rope which brand new looks very out of place for a pirate ship wreck. That can easily be remedied by randomly spraying black and forest green all over the rope to dirty it up. When tying the ends of rope to blocks and such, use bailing wire to wrap the ends of the rope. This way the ropes ends stay a little frayed and you do not have to spend a ton of time tying real knots.
Step 12: Skulls and Bones
Let’s face it. You can’t do a pirate theme and have too many skulls and bones. I purchase a fair amount of foam skulls from craft stores and this year I was lucky to find a bag of foam leg and arm bones as well. I used the hot foam knife to split the bones in half lengthwise and was able to adorn my ship with bones as some pretty nice trim pieces. Use the spray foam glue technique that I described earlier to attach them. You can see them on the galleries in the third image.
Step 13: Building the Ship's Wheel
My ships wheel is made of foam and replacement wood pieces for chairs. I just purchased a bunch of these pieces as they will also make good belaying pins once I get around to that. The ships wheel housing is made from those three pieces of fence board. Fence board is usually pretty rough and if based coated and dry brushed like the rest of the ship will blend right in. The frame on the ship has a support framework built in specifically to hold the weight of the ships wheel. Remember, foam and a few pieces of wire will not hold that thing up. My ships wheel is animated as well, which adds to the stress of the ship’s frame underneath. This is another reason why the frame in the ship section has to be stout.
Step 14: Building Deck Grates
All wooden ships had grates on the decks to allow air to circulate below decks. I used the white foam board for the grating and the pink foam board for the trim around the grates. Measure and draw out the grid system on the white foam board. Mark every hole you will cut out with an X. Trust me, if you do not you will make mistakes cutting out the wrong pieces. I marked them and I still cut the wrong pieces out on a few. Hey, it’s ship wreck though, right? So who cares? Once the grate is cut out you need to apply spray foam to it and set it on the deck. I used old steel weights to hold it down until the foam cured.
Next you have to make the trim. Because my deck bows and a ship wreck should, the trim pieces for my grates had to be cut where they would attach to the deck. It was like cutting out rocking horse legs. Use the weights to glue them in place as well.
Step 15: Displaying Your Pirate Ship Wreck
Now that you have all of that hard work done, all you need to do is get it displayed. My ship took me about two hours to transport and get situated in the yard. A lot of that time was transporting the pieces at 30 miles per hour. Use plenty of bungees and cargo nets. They will hold everything together.
The rest of the details took me about one day to set up. I always adorn my ship with a good hearty skeleton crew, ready to repel boarders at a moments notice! No wait, they all look drunk. Never mind. In any event, get some good lighting and foggers and your ship wreck will look the part. By the way, I added ship creaking noises inside my ship on a 60 minute loop. It really added to the effect.
Thanks for taking a look at my instructable. Again, comments are welcome and if you have questions, just ask.
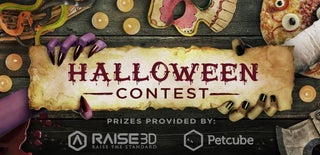
Grand Prize in the
Halloween Contest 2017