Introduction: Build an Underwater Robot
Sea Perch is an innovative underwater robot. Building an under water robot is very cool. Of course, it takes lot of time. But, you can operate it with a remote. You can buy an sea perch kit, which is available online for $155. Building a Sea Perch ROV teaches basic skills in ship and submarine design and encourages students to explore naval architecture and marine and ocean engineering principles. It also teaches basic science and engineering concepts and tool safety and technical procedures. Students learn important engineering and design skills and are exposed to all the exciting careers that are possible in naval architecture and naval, ocean, and marine engineering. VIDEO
Materials:
• PVC pipe
• Polyethylene
• 2 Pool Noodles
• 15 Cable/Zip Ties
• 6 Tie Wraps - Motor Mount
• 3 12V DC Motor. 0.7 A
• 3 Film Canister
• 3 Propellers
• 3 Propeller Shaft Threaded Coupler
• 3 Threaded Insert Tee Nut
• 3 Nylon-Insert Hex Locknut 4-40 - Stainless Steel
• 1 Stranded Cable
• 1 Velcro Cable Tie
• 1 Sea Switch Control Box Kit
• 1 Speaker Wire
• 1 Alligator Clips
• 1 Black Alligator Clip Insulator
• 1 Solder
• 1 Butyl Rubber Tape
• 1 Alcohol Wipe
• 1 Electrical Tape - Black – Roll
• 1 Wax Bowl Ring
• 1 Sealed Lead Acid Battery
• 1 Battery Charger Cable
• 1 Sealed Lead Acid Battery Charger
Step 1: Gather the PVC Materials and Cut Them in Appropriate Lengths.
Measure and cut the pieces listed below from lengths of ½” PVC pipe. Cut the longest pieces
first, in case a mistake is made (smaller pieces can be cut from a mis‐cut longer piece). Try to cut straight across the pipe, but don’t worry if they are not perfect.
Two pieces - 6.5" (16.5 cm) long Four Pieces – 5” (12.7 cm) long
Two Pieces – 4½” (11.4 cm) long Two Pieces – 4” (10.2 cm) long
Two Pieces – 2½” (6.4 cm) long Two Pieces – 4” (10.2 cm) long
Step 2: Drill the Drain Holes
1) Place an elbow on the end of a 6"‐to‐12" length of ½" PVC pipe, to use the pipe as a handle while drilling, or secure it in a vise or clamp.
2) Drill from the interior of the elbow outward. Drill a ¼" hole in thecorner of the elbow,
3) Repeat Steps 1 and 2 for other PVC elbows.
4) Drill Thruster mounting holes in two of the 5” lengths and one of the 4 ½ “ lengths as shown in Figure 1.2‐3. Be sure to carefully center the thruster‐mounting holes on that pipe so that the thrusters will be straight when mounted on the vehicle.
Step 3: Assemble the Vehicle Frame
1) Assemble the frame using the PVC parts as shown in the picture. No glue is used for any of the connections. Orient the elbows that are near the top of the vehicle with their holes pointing upward, to let air escape when the SEAPERCH is placed in the water. Orient those at the bottom with their holes pointing downward or to the side, to let the water flood in and out easily.
2) With the frame placed on the floor or on a sturdy tabletop, push down hard on all parts of the vehicle frame, turning and pressing from all sides, so that the PVC fittings and pipe sections all fit together very tightly. Be sure to press HARD, or use a rubber mallet to firmly tap on all elbows until the ends of the pipe sections bottom out inside the pipe fittings. Adjust the sides and the bottom of the frame as needed to square up the vehicle, as shown in Figure 1.3‐2 (or tilt the sides at an angle if you wish!). It is important to do this before installing the bottom payload netting.
Take a look at 1.3-2 image, it is very cool!
Step 4: Attach the Payload Net
1) Place the payload net underneath the vehicle frame, and trim it to size if necessary.
2) Attach the net to the frame using about 8 small black tie wraps. Pull them tight using pliers. Make sure the net is tight and flat on the bottom of the Sea Perch.
3) Trim off the ends of the tie wraps using wire‐cutting pliers (as flush as possible), as shown in Figure 1.4‐1.
Step 5: Seal the Motors So That Wax Cannot Get Inside
1) 1. Find the red dot on the white part of each of the motors, near its electrical terminals. The red dot marks the positive (+) terminal. Mark the (+) terminal (nearest the red dot) with the marker.
2. To keep the tape on the sides of the motor thin enough to fit into the housing, it's best to
first cover both ends of the motor, then trim the end tapes flush with the sides, and cover the sides last. Use five, short, 1” pieces of tape on the ends, such as in the process below. Figure 2.1‐1 shows the initial taping steps.
On the terminal end, gently push a piece of tape over one terminal to poke it through the tape. Carefully place the edge of this tape up along the side of the motor‐shaft boss (raised area in the center).
Continue doing this for all five tape pieces, overlapping them around the terminal end of the motor to fully cover it.
Then trim off all tape that extends past the edge of the motor shell (cut with scissors tilted toward the motor end to get a clean, flush edge).
3) Repeat this taping process on the other end of the motor. Be sure to cut the tape pieces flush at the edge of the motor as before.
4) 4. For the sides, wrap tape around the motor. Start at one end with the edge of the tape extending about 1/16” (~2 mm) past the end of the motor, so that it can stretch over the end to form a good seal. Pull the tape tight as you wrap. IMPORTANT: Tape only a single layer around the motor (so that it will fit into the thruster housing canister with space left for the wax, Press it to seal the edge as smoothly as possible.
5. Repeat Steps 2 and 3 for the other motors. The sealed motors should look like the one in Figure 2.1‐2.
6. Ensure that ALL of the holes in the motors are sealed well by pressing, rubbing, and squeezing the tape over the entire surface of each motor shell.
7. Verify that the sealed motors all fit into a thruster housing with space remaining around it for the potting wax.
Step 6: Drill Holes in the Thruster Housings
1. Before drilling, the caps and thruster housings, scrape off any plastic lumps that may be in the drilling area, using your fingernail or a small tool.
2. Using the 3/32” drill bit, slowly drill a hole through the center of each of the three thruster housing caps, as shown in Figure 2.2‐ 1.
3. Very carefully drill a 3/32” hole through the center of each thruster housing. Make sure the drill is held straight so that the hole is not on an angle.
4. Remove any plastic burrs from the holes in the bottoms of the housings that may be left after drilling. Do this by removing the 3/32” drill bit from the drill and passing it slowly by hand straight through the holes, from both directions, a few times, without twisting.
Step 7: Connect the Tether Cable Wires to the Motors
1. On the end of the tether cable that has no connector installed, use scissors to slit open the outer jacket and expose the first inch of wires as shown in Figure 2.3‐1
2. Then pulling the brown pair of wires tear the jacket back about 15” (38 cm) as shown in Figure 2.3‐2 and Figure 2.3‐3
3. Trim the torn cover off being very careful not to nick any of the wires as shown in Figure 2.3‐4
4. Thread about 2” (5 cm) of each pair through the hole in a thruster housing cap, and tie a knot on the inward side of the caps, as shown in Figure 2.3‐5.
5. Strip about ¼” (7 mm) of insulation from the end of each wire, for the green, blue, and orange pairs.
6. Select a pair of wires and one of the taped motors. Attach the solid color wire to the positive terminal marked in step 2.1. The striped wire attaches to the other terminal. Bend the stripped end of each wire through the terminal, and squeeze the wire tightly onto the terminal using needle‐nose pliers.
7. Solder the wires onto the two terminals of the motor, as shown in Figure 2.3‐6. 8. Repeat Steps 5 and 6 for the other motors and their tether wire pairs.
Step 8: Pot (Waterproof) the Motors With Wax
1. Roll an acorn‐size ball of wax in your gloved hands for a minute or so until it is softened, as shown in Figure 2.4‐1
2. Push and flatten the hand‐warmed ball of wax across the end of the motor, about 1/4" thick and the diameter of the motor, as shown in Figure 2.4‐2.
3. Insert the coated motor into the thruster housing, until the shaft pokes through the hole in the bottom of the housing, as shown in Figure 2.4‐3.
4. Press firmly on the back of the motor to slowly move it to the bottom of the housing while the wax in the bottom pushes up around the motor until the shaft fully protrudes from the bottom, as shown in Figure 2.4‐4.
5. Coil the wires into the end of the housing and press a marble‐sized piece of room‐ temperature wax on top of the coiled wires to hold them in place, and then press the wax down to fill in any remaining space around the sides of the motor. Adjust the amount of the wax to fill the remainder of the area at the top of the housing, leaving just enough space for the cap to go on, as shown in Figure 2.4‐5.
6. Move the lid onto the housing, as shown in Figure 2.4‐6, and press hard to seat it into place. Then use a paper towel to wipe all wax residue from the outside of the housing and the motor shaft.
7. Repeat steps 3 through 12 for the other thrusters.
Step 9: Mount the Propellers Onto the Shafts
1. Wipe the shaft of each motor using an alcohol pad (or a paper towel dampened with rubbing alcohol) to remove excess wax that may be left after the potting process, as shown in Figure 2.5‐1. Then use a small piece of sandpaper to roughen the surface of each of the motor shafts (this can be done by spinning the shaft against the sandpaper while turning on the thruster using a pre‐made control box). Then wipe each thruster shaft again with another alcohol pad (not the one used to remove wax above). Cleaning the shaft is critical in order for the adhesive to stick to it!
2. Use a vise or pair of pliers to hold a threaded coupler, as shown in Figure 2.5‐1.
3. Thread the tee nut all the way down the threaded coupler. A pair of pliers may be required to get the tee nut starten on the threaded coupler, as shown in Figure 2.5‐2 and Figure 2.5‐3
4. Look closely at a propeller and note that one side has a slot (groove) in it, as shown in Figure 2.5‐4. This is the side that must be placed nearest the motor. Place the propeller onto the threaded coupler with the slot side to the tee nut, as shown in Figure 2.5‐5.
5. Thread a lock nut onto the threaded coupler, as shown in Figure 2.5‐6.
6. Using pliers or ¼” nut driver, drive the assembly together by tightening the lock nut. A finished assembly is shown in Figure 2.5‐7.
7. Repeat Steps 2 – 6 for the other propellers.
8. Place a drop of Super glue in the hollow end of
the shaft coupler and on the tip of the motor shaft, as in Figure 2.6‐1. Push the hollow end of the shaft coupler onto the motor shaft. A completed thruster is shown in Figure 2.6‐2.
9. Repeat Steps 1 for the other two thrusters.
10. Put your thrusters aside and allow the adhesive to harden, undisturbed, for 10 minutes to reach handling strength. Do not apply power to the motors or otherwise stress the glued connections until that time has passed.
11. After 10 minutes, turn each motor by hand to free up the newly intsalled asemblies.
Step 10: Mount the Thrusters Onto the Vehicle Frame
1. Thread a large, heavy‐duty tie wrap through the two thruster‐ mounting holes at each of the three thruster locations, as shown in Figure 2.6‐4.
2. Place the appropriate thruster in the loop formed by each tie wrap, and tighten the tie wrap around the thruster, as shown in Figure 2.6‐5. Refer to Table 2.6‐1 for thruster placement. Be sure to mount the vertical thruster with its propeller pointing upward.
3. Install a second heavy‐duty tie wrap around the first tie wrap, between the thruster and the
pipe, at each of the three locations, and tighten each securely to hold the thrusters in place.
4. Cut off the tie wrap tails as flush as possible to avoid leaving sharp ends.
5. You can now use a screwdriver, inserted through the angle‐adjustment holes, as shown in
Figure 2.6‐6, to gently turn the PVC pipes on which the thrusters are mounted so that the thrusters are oriented in the directions that you want.
Step 11: Waterproof and Mount the Tether Cable
1. Using a ½” (1.5 cm) piece of butyl rubber tape, stretch the tape to about twice its relaxed length and wind it among and around the four wire pairs where they emerge from the outer jacket of the thruster end of the tether cable. Press it over the jacket opening so that it extends at least ½” on each side of the opening, as shown in Figure 2.7‐1. Knead and work it in between the wires well so that it seals both around and between the wires and forms a smooth seal over the jacket opening to prevent water from getting inside the tether cable.
2. Wrap electrical tape over the butyl rubber tape to keep it from sticking to anything.
3. Install two crossed tie wraps to capture the tether cable where it passes over the center of the pipe at the rear of the ROV, as shown in Figure 2.7‐2.
4. Coil the brown wire pair out of the way and tie‐wrap it to the payload net. 5. Pull all tie wraps tight with pliers, and trim the ends flush.
Step 12: Gather the Parts for the Control Box Assembly
1. Gather, identify, and inventory the parts needed for the control box, as shown in Figure 3.1‐1
1. Some parts, such as the switches, may look a bit different, but all types of items shown should be in the kit. If any are missing, notify your instructor who may have spare parts.
2. Locate the two toggle switches. If they have nuts and/or washers installed on their threaded mounting shafts, remove all nuts and the washers; use pliers to loosen the nuts if needed.
3. Gather the eight small screws and put them in a safe place (such as taping them to the inside of the vehicle storage tote bag or bin) to prevent them from being misplaced during the assembly process.
Step 13: Assemble the Power Cord
1. Find the power cord wire, and determine which of its two conductors will be positive and which will be negative. For this project, we will call the copper side the positive (+) wire, and the silver side the negative (–) wire.
2. On each end of the wire, carefully separate the two conductors for a length of about 3 inches (7.6 cm).
3. Strip 5/8 inch (16 mm) of insulation off of all four ends of the power cord wire. Twist the strands on each of the ends (individually, not all together) tightly to prevent fraying.
4. On one end of the cord, slide the red alligator clip cover (small end first) onto the positive wire, as shown in Figure 3.2‐1. Slide the black alligator clip cover onto the other (negative) wire of the power cord.
5. Attach the two alligator clips to the power cord wires by
pushing the wires in through the backs of the clips and up through the holes near the screws. Loosen the screws, wrap the wires around them tightly in a clockwise direction, and then re‐tighten them. The connected alligator clips should look like the one in Figure 3.2‐2, with most of the wire captured under the screw's head.
6. Move the covers over the clips (insert a pencil or other small object into the "mouth" of each alligator clip to make it easier to push the covers over the rear part of the clip). The finished power cord should look like Figure 3.2‐3. Its other end will be connected to the PCB later, in Procedure 3.4.
Step 14: Install the Printed Circuit Board Components
1) Review Figure 3.3‐1, and refer to it as needed during the following assembly steps. The parts will be installed in order according to their size, smallest first. DO NOT INSTALL COMPONENTS UNTIL IS IS CALLED FOR IN THE INSTRUCTIONS
2) Locate the fuse socket. Place its two pins through the holes at the location on the board labeled "F1," as shown in Figure 3.3‐2 (remember, all components go on the side of the PCB that has the white lettering). Use a small piece of electrical tape to hold the socket in place. Flip the board over and place it on a tabletop. Press down on the PCB to hold the socket flat against the board, and solder the two connections. Melt only about 1/4" of solder into each connection, let them cool for a few seconds before moving anything, and make sure that there are no solder bridges between the connections. (Remove excess solder if needed by touching the solder bridge briefly with a clean, hot, soldering iron tip.)
3) Place the pins of the two pushbutton switches through the pads in the PCB at the locations labeled "SW3" and "SW5," as shown in Figure 3.3‐3, after making sure that their pins are all straight (perpendicular to the switch body). [You may have larger switches than shown, which fit instead into the other set of three holes at the "SW4" and "SW6" locations.] While holding the switches in place with a piece of electrical tape, flip the PCB over and place it on a tabletop. Press down on the PCB to hold the switches flat against the board, and solder all connections on each switch.
4) Find the two toggle switches and the control box lid. Place the switches in the "SW1" and "SW2" locations on the PCB, as shown in Figure 3.3‐4. It is also important to keep these switches flat against the board while they are soldered into place, so that they will be straight when the control box is finished. A good way to do this is to use the control box lid to hold the switches while soldering. Put the toggle handles through the two center holes in the control box lid (they may be tight). Then, while holding the PCB against the back of the switches, turn the assembly over and place it across the open top of the control box, as shown in Figure 3.3‐4.Hold the PCB down flat while soldering the first of the 12 switch connections, to make sure that it will be tight against the switches.
5) Solder the remaining 11 connections, taking care not to overheat the switches (wait a few seconds between connections, or alternate between the two switches). Then remove the nuts and the lid. 12. Check the small pins on the bottom of the RJ45 connector jack to make sure that they are not bent, and then carefully put them through the PCB holes at location "J1," as shown in Figure 3.3‐5. Press on the jack to snap it into place.
6) Check the small pins on the bottom of the RJ45 connector jack to make sure that they are not bent, and then carefully put them through the PCB holes at location "J1," as shown in Figure 3.3‐5. Press on the jack to snap it into place.
7) Place the PCB back on top of the control box, and solder the eight pins, being careful not to use too much solder, which might create solder bridges between the very‐closely‐spaced connections.
8) Re‐examine all of the solder connections on the PCB as a final check for solder bridges or connections that don't seem to have enough solder. Re‐solder them if needed. The soldered side of the completed PCB should look similar to the one shown in Figure 3.3‐6. The completed PCB should look like Figure 3.3‐7.
Step 15: Connect the Power Cord
1. Twist the strands of the two power cord wires, and pass them through the cord hole in the control box lid, from the top side. Then tie a knot in the two wires, about one inch from the ends, on the underside of the lid, as shown in Figure 3.4‐1.
2. Re‐twist the strands of each of the two wires so that they can pass through the PCB's solder pad holes, and place the positive (copper) wire into the "+12V" (RED) power wire hole, and the negative (silver) wire into the "–12V" (BLK) power wire hole, both entering the holes from the component side of the PCB, as shown in Figure 3.4‐2. Bend the wires over to help hold them in place during soldering.
3. Solder the two power wires, using enough solder to make good, solid electrical connections. Then snip off the excess wire beyond the solder joints.
Step 16: Conduct Tests and Finish the Control Box
1) Locate the fuse. If its leads are longer than about ¼" (6 mm), cut both leads to that length, as shown in Figure 3.5‐1
2) Install the fuse into the fuse socket, as in Figure 3.5‐2.
3) Locate a multi‐meter with an "ohmmeter" function (measures electrical resistance) to conduct a few quick tests. These tests will tell you if there are soldering problems on the PCB (which can cause the fuse to blow and stop your ROV from working) or a switch problem. DO NOT connect the battery until the electrical testing in the following steps has been successfully completed.Set the meter to measure resistance (ohms), and make sure you can tell the difference between a "short" circuit (~0 ohms – touch the probes together) and an "open" circuit ("infinite" resistance – probes not touching). Some meters have a “beep” to indicate continuity, such as caused by a short circuit.
4) To test for shorts, connect your meter's probes to the two alligator clips on the power cord (the polarity of the leads does not matter). Leave the tether cable unconnected.
5) Now activate each of the four switches individually and in all combinations. At no time should you get a low resistance reading (any continuity). Try all switch combinations and make sure there is no combination that shows a short circuit. The meter should read infinite resistance at all times.
6) Then test the switches with the tether cable connected. You should see a low (NOT zero) reading of about 5 to 15 ohms whenever you activate any switch, as the meter shows the resistance of the coil of wire that is inside each of the motors. If you do not see such low readings for any engaged switch position, you may have either a poor solder connection, a bad switch, a damaged wire or connector in the tether cable, or a thruster problem.
7) Once you are sure that there are no short circuits and that the thruster motors show proper readings, you can finish assembling the control box. Place the PCB into the control box, passing the pushbutton switch actuator buttons carefully through the two holes in the front of the box, and secure the PCB into the box using the four small silver screws, as shown in Figure 3.5‐2.
8) Press the two pushbutton switch caps onto the actuator buttons, as shown in Figure 3.5‐3.
9) Install the lid onto the control box, carefully folding the power cord wires inside the box as the lid is lowered into place. Secure the lid with the four black screws.
10) Connect the tether cable's RJ45 connector plug into the RJ45 jack on the control box.
Step 17: Done!
CONGRATULATIONS, you have finished your Sea Perch ROV! Now it’s time to try it in water!
Step 18: Bibliography
http://www.seaperch.org/
Step 19: Final Prototype of My Robot With the Controller Soldered!
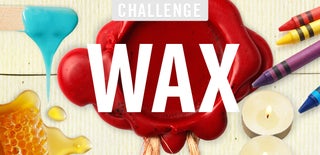
Participated in the
Wax Challenge
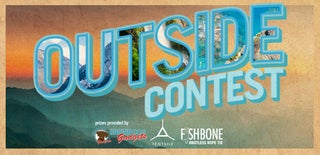
Participated in the
Outside Contest