Introduction: Building a Plastic Injection Press
This is the basic Gingery plastic injection press which I figured I could improve, handle linkage is from Rick Sparber, with my contribution being the piston rod clamp and using a gas strut for injecting the plastic.
I was planning on using it to recycle all my failed ABS prints from my 3D printer, but initial trials indicate it might be easier to just buy the granulated plastic.
Supplies
All prices in ZAR ( South African Rands)
- 32mm ID nozzle heater UHNS3BO-HNY1044A Nozzle D32X40/220W/230V,T=500,BrassR725
- K4046 gas strut https://mcnaughtans.co.za/?product=500mm-gas-stay-4000-series R120
- 2M 40mm x 3 equal angle R78
- 2M 30 x 5mm flat bar R78
- 100mm x 35mm dia aluminium and 100mm 25mm square bar both R145.
- Rex C100 PID temp controller kit at Mantech R575
- M8 threaded rod
- 140mm x 60mm 8mm thick flat bar for the clamping table
- bicycle seat post clamp
Step 1: Gas Strut
A gas strut has an almost mirror smooth inside bore and I thought that it would make a good candidate for plastic injecting if I could disassemble the spare one I had lying around.
Do not cut or puncture the pressurized assembly.
The safest option is to take them to the supplier for degassing.
That said, I figured that this sealed unit could only be gassed through the seals and cut a small section from a coke can to slide between the rod and seal.
Bear in mind that this must be done with the rod in the upper most position or you will spray your surroundings with an oil mist.
I used a block of wood to protect my hand and gently pushed down on the rod end until I heard gas hissing, the rod slowly sank down and after leaving the shim in place for 20min, checked to make sure all the gas was evacuated before using a pipe cutter below the crimped section which incidentally houses the seals and guide blocks.
I needed to deburr the rolled over end before I could pull out the piston assembly.
The piston end is notched around the circumference and unsuitable for my needs, so I cut off the peened over rod tip in order to make my own piston from teflon bar scrap I had left over from an earlier project.
Lastly, I drilled out the M6 mounting stud on the barrel with a 3mm drill bit in the lathe which will function as the plastic discharge nozzle.
Im using a M6 brass acorn nut to act as the interface between the nozzle and mold injection point, which I will mill using my 10mm ball nose end mill bit.
A better/higher temp piston would be either aluminium or brass. Dont use steel as it will scar the tube bore over time inducing leakage past the piston.
I suspect a very serviceable piston could be made pouring molten aluminium using the scrap off cut tube piece for the mold.
Step 2: A Basic Frame
The Gingery version was mainly bolt together, but I opted to weld everything.
All measurements in mm in the attached dxf file.
The handle is 400mm long and the piston rod attaches 70mm from the pivot yielding a stroke length of 135mm.
If one applies 20kg of down force on the handle, the combination of tube ID (15.85mm)and 70mm pivot mount offset yields a pressure of 800psi which is lower than the 1400psi of the Gingery version due to his use of a 12.7mm ID bore.
The handle to frame links are 2 pieces of 3mm x 25mm flat bar 120mm long, 100mm between hole centers.
I should probably mention that Im not using pop rivets to hold the handle on, it pivots on 10mm printer bar which has been drilled on either end and the pop rivets act as retainers.
I originally drilled the frame handle pivot 15mm in from the back edge, but then decided I would need shorter slot in the front angle iron leg in I moved it further forward. (50mm in from back edge)
Once I received the heater nozzle, I could determine where the heater block cross brace would be, as well as the length of the clamp mount.
Attachments
Step 3: The Heat Block.
The nozzle heater is a 220W model and 40mm in length. This needed to hang below the cross brace to reduce frame interference and heating.
Smaller models with an ID to match my gas strut werent in stock and also had reduced wattage, hence my need for the spacer.
The spacer was machined on the lathe, 33mm OD and 18.8mm ID.
Unfortunately the spacers walls are too thin to accommodate the thermocouple, so it had to be mounted in the clamp block above.
Once I knew the max stroke(135mm), I could cut the tube leaving enough space to insert the plastic. (120mm)
FR4 pcb pieces were used to reduce frame heat creep.
Once everything functioned well mechanically, it was time for the electrics, which was simply a matter of wiring up the K type thermocouple, solid state relay and Rex C100 PID controller.
Step 4: Final Thoughts
I thought that a 2 part heater block/clamp would be easier to mill, lathe and assemble.
However, the fact that the thermocouple isnt next to the nozzle or heater leads to considerable lag resulting in actual temp overshoot.
This causes much higher temps in the lower tube section until the thermocouple catches up and burns the plastic.
I kind of mitigated this issue by using thermal compound between the 2 mating faces, but ideally they should be thermally coupled by making them a single unit.
The other issue is that, because my heat blocks have an effective heat zone of 65mm as opposed to the tube length of 120mm, I can only inject 12.8cc of plastic instead of the 23cc that I originally intended.
This could be remedied by using 2 x 100w cartridge heaters on each side of a 120mm block, but at the time they werent available and were twice the price of the single nozzle heater.
My other option if these issues become problematic, is to re machine the heat block as a single piece and move the thermocouple closer to the brass heat band.
Step 5: A Day Later
I decided to reposition my thermocouple and pulled apart the heater assembly.
Free space between the 2 band clamps was 5.5mm but the temp probe nut was 10mm across the flats, so the nut was milled down to fit the band clamp spacing.
The spacer was drilled and tapped, temp probe installed and then the nozzle heater and clamp block slid back on.
At least I can now use the auto tune feature of the controller, seeing that the temp probe is in very close proximity to the heating element, there is very little temp lag.
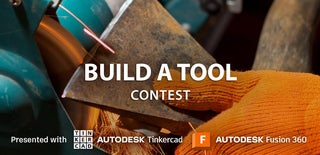
Participated in the
Build a Tool Contest