Introduction: Classic Cooler Salvaged From Dumpster & Restored!
I was taking some trash out to my apartment complex dumpster when I saw this little fella'. The inside was decently clean; however, the metal was severely rusted--including small areas where it rusted through entirely.
I noticed similar models at my local REI for $130, so I thought it worth a shot to try to restore it. The process was super simple and the result was amazing. As soon as the paint dried, we loaded it up and went camping--as if it were brand new!
I highly recommend giving this a shot if you come across a vintage steel cooler in need of some TLC.
Supplies
Basic Items:
- Angle grinder (or a lot of elbow grease!)
- Flap disc attachment (I used an 80 grit for fast stripping) - $9
- 3M Bondo plastic metal - $6
- Metal primer/filler (example) - $5
- Metal spray enamel (example) - $4
Consumables:
- Shop towels and painters tape - $5
200 grit sandpaper - $1
Other Recommended Items:
Wire wheel attachment (for finer rust removal) - $5
- Respirator to avoid dust inhalation
- Safety goggles
- Protective gloves
Step 1: Remove Hardware From Cooler and Clean Everything
Use a common screwdriver to unbolt all of the hardware. It all comes off pretty easily (hinges, handle, locking mechanism, etc.)
Using soapy water, water with baking soda or common household cleaners, clean the cooler. In my case, the white plastic bottom part was the dirtiest part. I had to let it soak before and after a few rounds of scrubbing. Be sure to get all the dirt and grease off of the cooler components.
Pro-Tip: organize the hardware so you'll know how it all comes back together.
Step 2: Remove the Rust
Using an angle grinder with a flap disc attachment to tear through the rust and make quick work of the stripping process.
!Be sure not to remove too much or tear into the metal! Flap discs can remove a lot of material.
After you take off most of the rust, change the angle grinder attachment to a wire wheel and slowly strip the metal siding. Use sandpaper and a wire brush to do a final sweep and hit those hard to reach places. You don't have to remove all the paint, but you want to remove any loose paint and rough up the remainder.
When you're finished, but sure to clean off the metal. I used a damp shop towel to wipe away any fine particles or debris.
Note: you can do this manually with a combination of wire brushes and sandpaper, but the angle grinder really does make this a breeze.
Step 3: Repair the Metal Surface
After Step 2, I noticed that the surface was pockmarked. The rust had caused tiny cavities to form across the surface. Worse, there were a couple small areas where the metal surface had entirely rusted through, exposing the foam insulation beneath.
The easiest way to fix this is with basic automotive filler. I used some basic 3m bondo plastic metal filler. You don't have to mix it, and it's super easy to work with.
Filler Directions: squeeze some out of the tube onto the work surface and spread the filler across the metal surface using a piece of plastic or credit card. Add more bondo as needed. You just want a thin layer that fills all the gaps. In areas with more severe rust damage or small holes, you need to layer on thicker passes--making sure to gradually blend the edges of the thicker areas.
Step 4: Sand the Filler and Prime the Surface
The next step is to take some abrasive and sand down the bondo filler until its even, nice and smooth.
Next, use a moist shop towel clean the surface.
Use the blue painters tape around the surface edges to delineate where you want the primer/paint to be applied and protect the areas that you don't want to paint.
Finally, take your metal primer (follow instructions for use on can) and apply even coats from approximately a 10-14 inches away in broad sweeping motions.
Note: Sometimes the appearance of bondo looks uneven after you sand it--even when it is evenly smooth. Be sure to inspect the surface carefully to discover areas that aren't evenly sanded down.
Step 5: Apply Paint
After the primer has fully dried and with the blue painters tape still protecting the areas that you don't want to paint, apply an even coat of metal enamel in the same manner.
After the enamel dries, you will need to apply a secondary coat and hit areas with a little extra spray until the surface is even.
In the second video, I decided to apply a very light layer of white plastic paint that I had around. This is not necessary, but will help make the cooler look clean.
Note: In the video, I finished the cooler lid first, then repeated the process on the metal sides. The order that you do it in doesn't matter.
Step 6: Clean Hardware and Reassemble the Cooler
This step is easy: just sand off any rust from the components using sandpaper and polish up the steel.
Reassemble the hardware onto the cooler.
Pro-Tip: to ensure a long-lasting protective coat on the steel hardware, apply a furniture wax finish to the metal.
Step 7: Done! You Got Yourself a New Cooler!
Enjoy your like-new cooler!
I went on a camping trip and immediately put it to good use.
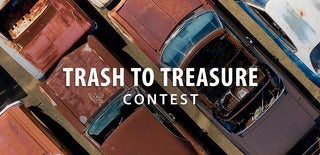
Participated in the
Trash to Treasure Contest