Introduction: Colored Glass Window
A good friend had some remodeling done and one of the results was a new office space with a window. He was thinking about a stained glass panel to dress it up, and I jumped at the chance. He and his wife had no specific ideas or expectations, so the only design constraint was size.
I wanted to use glass I had “in inventory”, that is, left over from other projects. I had some odd pieces of colored glass. I also had rather a lot of non-colored glass, a lot of wavy and a fair about of glue-chip( bankers glass). I also had some beveled glass. So all this helped dictate the design. As it turned out, I used all colors of the rainbow except one. Sadly, I had no blue in inventory.
Supplies
Tools
- Glass cutter with oil reservoir
- Glass cutter with steel ball for cracking glass curves
- Glass grinder
- Tiny fine tooth chop saw for cutting lead came and zinc
- Horseshoe nails
- Soldering iron
- Flux brush
- Wooden board for assembly.
Supplies
- Colored glass, non-colored glass, beveled glass
- Lead came
- Zinc edging
- Solder (40% lead, 60% tin)
- Solder Flux
- Window glazing (putty)
- Whiting compound (calcium carbonate powder)
- Black Patina
Step 1: Design
I drew some designs full sized to see how they looked. I came up with a simple enough design, without too many difficult glass cuts, but with enough variation to be interesting. The lines of the design are drawn in Sharpie, and the width of the Sharpie lines is about right for the space that will be taken by the lead. Very large or hard-to-cut pieces are made in segments. The result is a detailed full-sized template called a cartoon. I number the pieces as I cut them and put that number on the design.
Step 2: Cutting the Glass
Making a Scratch
The way I try do it is to lay the glass on the design, use a strong light to look through to see the lines, and run the cutter along the lines, making a visible scratch the entire way. The scratch is where the glass will crack and separate. This is easy for the straight lines and I use a ruler to keep them straight. But for curved lines it’s free hand and it’s easy to stray from the lines. Note that if the glass is opaque or too dark, you can’t see through it to cut. You’ll have to make a paper cut-out (template) of the piece and trace onto the glass.
Cracking the Glass
After there is a definitive scratch on the glass, I use the steel ball end of the glass cutter to “whack” the glass behind the scratch on the other (non-scratched side). If you’re lucky, a crack will start to form at the scratch, and the crack will grow along the scratch as you continue to whack the glass. Trial and error determine how hard you need to whack. Some types of glass crack easily and predictably, and some take a lot of hard whacking. Eventually the glass comes apart. Sometimes there will be undesired breakage.
For straight cuts, I lay the larger side on a table, scratch positioned over the table edge, then use a glove to grab the smaller side and force it down until it breaks.
Smooth and Textured Sides
Colored glass often has a smooth side and a textured or bumpy side. It’s easier to cut the scratch on the smooth side and do the whacking on the bumpy side. I try to keep smooth sides up when fitting to the pattern. The bumpy side is more interesting, and that will be the “front” or more visible side of the final panel.
Glass Grinder
A glass grinder is essential. It’s possible to adjust the edges by crunching the glass edge with pliers. But this is messy and imprecise. Grind down rough edges or too-large parts until the part fits neatly within the lines on the cartoon.
Step 3: Assembly
There are two popular types of stained glass: There is Tiffany style, where each piece of glass is edge-wrapped with copper foil, assembled like a jig saw puzzle, then soldered together. The other method uses pre-formed H shaped strips of lead, called “came” between the pieces. This usually makes a stronger result, and it looked more appropriate for the size of pieces in my design. I opted for this second method.
I started by cutting the zinc edging to size and soldering it together. That way I was guaranteed that I’d end up with the required size. I then started at the left side, cutting and fitting, and holding the partial assemblies together with horseshoe nails.
Why horseshoe nails? They’re a convenient size, and their wedge shape tends to press in on the lead came as you pound the nail into the support board.
I try to get the lead came pieces to fit snugly together so they’ll solder neatly later. To fit the final pieces inside the zinc boundary, it was necessary to partially lift previously assembled pieces to provide some space for the final pieces to fit in. This wouldn’t be necessary if the zinc border were left “open”.
Step 4: Final Steps
Soldering
This is the fun part. Brush some flux onto a few joints, the solder the came together. After all joints are soldered, turn the whole thing over and solder joints and the other side. The panel is pretty fragile at this point so I slide a piece of plywood under it to lift it to vertical. Then I move the plywood to the other side to ease it down.
Glazing
After all zinc and lead joints are soldered and look good, it’s time to glaze. This is simply squishing window glazing (putty) into all the voids between glass and lead came. It’s messy and I use my fingers to push the putty in. Turn it all over and squish putty into the other side. The putty will have made a smeary mess on the glass. So this is when you use “whiting compound”, calcium carbonate powder to clean the glass and remove excess putty.
Black Patina
At this point the lead is a shiny silver color. I prefer a nice uniform black. This is achieved by brushing on black patina liquid. Re-apply as needed to get all the zinc and lead uniformly black. Rinse with water and buff dry with a rag. And you’re done.
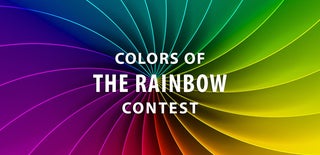
Participated in the
Colors of the Rainbow Contest