Introduction: Configurable Dymaxion Wall Art - a Quarantined Art Project
I have been fascinated by Buckminster Fuller's Dymaxion Projection for years, and have always wanted a way to display it that does justice to its unique reconfigurability, and the ease with which it can be reassembled into an icosahedral globe.
I've had the idea in my head for a while of a map mounted by magnets to a steel plate, whose segments can be pulled from the wall and assembled into an icosahedron, as a sort of puzzle. The concept had been knocking around in my head for years, but it never rose to the top of my project list.
When the CoVID'19 lockdown started, I needed some way to keep busy and mentally engaged, but without my local maker space, I was left without any of my normal tools to work with. I decided it was time to take on a challenge. I decided to see how far I could get towards my dream Dymaxion map, without any access to tools, beyond those that I had in my apartment.
Of course, laser cutting was a key part of this project, so I had to shell out the money and order a cut from Ponoko. I am impressed by the speed and quality of the work, but I still would have preferred to run the job myself, where it would have been much cheaper.
Supplies
- 13" x 27.5" Custom laser-cut plywood from Ponoko.com
- 14" x 30" Stainless Steel Bulletin Board - Amazon.com
- Tung Oil
- 300-1200 grit sand paper
- 10mm x 2mm round neodymium magnets (60) - Amazon.com
- Cyanoacrylate (super glue)
- Baking Soda
- Water
- 1" Quilting Triangle and an old credit card (I'll explain)
- Scissors
- Ruler
- Stepped drill bit
- Cordless drill
- Cardboard (to protect surfaces)
Step 1: Source Design and Order Laser Cut
Originally, I had planned to generate my own projection using Blender, by projecting a textured globe onto an icosahedron and baking the textures, then exporting a wrap. Then I would have imported into Illustrator for final cleanup and vectorization.
On a whim, I ran a quick search on Thingiverse, before starting the modelling, and found a perfect existing svg in exactly the projection I was looking for. So, thanks to Thingiverse users KBST and Gav, I didn't have to do any modelling at all. I just had to turn off the layer they had added for screw holes.
I loaded the SVG into Ponoko. set the correct layers to cut, engrave, and area engrave, and set the size of the final piece to 27.5" x 13.5", to keep it slightly smaller than the steel bulletin board. I had it cut from 1/4" Birch plywood, which ended up costing me around $70, and took about two weeks to get to me.
If I had been able to use the laser cutter at my local maker space, this would have been MUCH cheaper and faster, but I was desperate for a project to work on, while at home.
Step 2: Oil, Sand, and Oil Again
When I received the laser cut pieces, they were unfinished, so I gave them a few coats of tung oil, to impregnate the wood and cause it to swell a little, protecting it to a minimal degree. The oil also raises the wood grain, as it soaks in, so after allowing the first three coats to soak in fully, I re-sanded the wood smooth, before giving it a final coat.
I could have gone for a more polished look with stain and polyurethane, but I wanted the engraved areas of the map to stand in sharp contrast, and I like the unfinished look for this application.
Step 3: Building a Magnet Placement Jig
If I'd had access to my local maker space, I would have built a jig out of scrap wood to clamp to a drill press, then I would have used a 10mm Forstner bit and the drill press's depth stop to carve an indent in each corner of each triangle, on the back, so that I could epoxy a magnet to each corner, so that it would sit almost flush with the surface.
Unfortunately, working from home I had no way to carve these indents accurately. So I decided to build a jig to place the magnets accurately on the surface of each triangle.
While searching through my junk drawer, I found a 1" quilting triangle, which was perfectly sized to become a jig. I measured the center point of the triangle, marked it, and used a step drill bit to make a hole just slightly larger than 10mm in the center. Then, I attached edge-guides made from an old rewards card, to make a jig that I could easily place tight to each corner of the triangles while attaching the magnets.
Tip: To find the center of an equilateral triangle, stand it on each edge in turn, and use a ruler and pen to draw a line from the raised corner to the base that is perpendicular to the surface. Once you've done this for each edge, you'll have three lines that intersect at the center of the triangle.
Step 4: Placing the Magnets
This was the most tedious part of the project.
- I first marked one end of my stack of magnets, to ensure that I always knew which pole was facing inwards.
- Then I moistened the wood surface with a mixture of water and baking soda (used to improve the bond and cure time for cyanoacrylate), and put my corner jig in place.
- Next, I put a dot of cyanoacrylate on the bottom of the last magnet in the stack and inserted it into the hole in the jig.
- Lastly, I lifted the jig out of the way, to prevent it from bonding to the wood, and waited for 60 seconds for the glue to cure.
- Then I moved on to the next corner.
I also screwed this step up, and managed to glue magnets on the corners of 5 triangles, before realizing that I hadn't removed the protective backing from the wood... d'oh.
Step 5: Current State and Thoughts
- Although the superglued magnets aren't as durable as inset epoxied magnets would have been, i like the look of the wood floating a couple of millimeters above the metal. If I end up redoing these glue joints, I'll make the inset shallow enough to try to keep this effect.
- Originally, I had planned to use a dark hardwood laminate on the steel bulletin board, to hide the metal, but I ended up liking the birch on steel look too much.
- The map pieces are very hard to align properly on the metal plate. I'm thinking of scoring and hammering a repeating triangle pattern into the steel, to make alignment easier.
- It's not my style, but it would be really easy to drill a hole behind each map piece and string RGB LEDs to provide a programmable underlighting effect. I am really tempted to do it, just for the cyberpunk awesomeness factor.
Step 6: Next Steps: How to Convert to a Globe
Eventually, I really want this map to be convertible into a handheld icosahedral globe, but that process has enough complexity that I'm leaving it until life gets back to normal. There are several potential approaches I could take to this problem, each with its own pros and cons.
I'll detail the current options in the last few steps, so you can get an idea of the many ways to potentially solve this issue.
Step 7: Globe Option 1: Hinges and Recessed Magnets?
This option involves routing the underside edges of each triangle and concealing hinges on all adjacent edges. The remaining edges would either be served by slip-pin hinges, or a set of recessed magnets embedded in the edges of the triangles.
PROS
- Very easy to assemble/disassemble
- self-contained
- relatively invisible in map mode
CONS
- The map cannot be reconfigured to highlight different countries/continents any more
- Not a challenging puzzle, more of a desk toy
- Requires a lot of routing and hinge work
- Connecting the non-hinged edges is an outstanding problem
Step 8: Globe Option 2: 3d Printed Corner Supports W Embedded Magnets?
Once I have access to a 3d Printer again, It would be pretty easy to print 12 vertex supports that would hold a magnet in each face, to connect with the existing triangles
PROS
- Simple Assembly
- Sturdy-ish
- Maintains puzzle complexity
CONS
- Doesn't match the aesthetic of wood/metal.
- Expensive/Slow to manufacture.
- Corner supports need to be stored somewhere.
- Requires precise magnet placement
Step 9: Globe Option 3: Laser-cut Steel Corner Supports?
A third option would be to laser cut corner supports from carbon steel, and fold them into the correct shape. I would have to order the pieces since I don't have access to a laser that can cut metal.
PROS
- Very Sturdy
- Doesn't require exact magnet placement
- Might be possible to add hinges to store them flat
- Metal design matches the existing aesthetic
CONS
- Requires lots of precise folding/hinge work to assemble
- Can only get in Carbon Steel for magnetic, which may rust
- Where to store is still uncertain
Attachments
Step 10: Globe Option 4: Ball Bearings?
The simplest solution would be to use ball bearings to support the corners, but the math required to size the necessary bearings is pretty complex.
PROS
- Doesn't require manufacturing
- Metal ball supports match the aesthetic
- Ball Bearings are plentiful
CONS
- Working out the proper size requires trigonometry and geometry, and I'm not sure my calculations are correct
- Ball bearings may be too bulky to not interfere with each other.
- Ball bearings are hard to store
- Edges may be unstable since magnets only make point contact with ball bearings
- Large ball bearings can be expensive
Step 11: Final Thoughts
This project was a very easy way to kill a couple of afternoons at home, and I love the way it turned out. I'm very tempted to move forward with the idea of adding RGB lighting, even though it's not my style.
As it is, the Dymaxion map draws comments from everyone who sees it on zoom, and I love the space it has taken on my wall.
I can't wait for others to be able to see it in person.
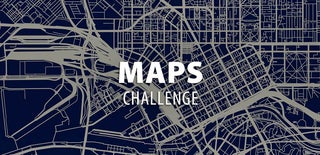
Participated in the
Maps Challenge