Introduction: Cross Cut Saw - Homemade
Machines are often expensive and take up a lot of space. Solution to both of this problems is to multi-purpose what you already have, saving money and space, so that's what my father did.
The idea is to build a cross cut saw starting from a big angle grinder. The cross cut saw has some advantages over the angle grinder:
- Can be operated with one hand
- No need to perfectly clamp what you are cutting
- Safer
- You don't have to lift a heavy (and dangerous) machine
- If you already have an angle grinder, it's way cheaper!
So now that you are convinced of the advantages, let's start!
Step 1: Materials
This is the list of materials we used to build our own. Obviously, infinite variations are possible!
- Angle grinder; the bigger, the better.
- Steel sheet and steel bars, for the structure. Also wood should work fine
- A strong spring, so that when you let go, the machine lifts from the table
- A switch, for, you know... do what switches do.
- A welding machine, if you choose the metal structure
The basic idea here is to save money, so before buying anything you should check what you already have or how to replace something you need with something else you have.
Step 2: Building the Table
For the table we used a 4mm thicksteel sheet. The dimensions are 35x60cm, also known as 13.6x23.6in. After cutting the sheet, my father welded on it's bottom side some square tubes, in order to have good planarity and a stiff structure. This was necessary in our case since the metal sheet was not really flat.
You will also need to raise the table from the surface on which it will lie, so that the blade can go through without destroying everything. We used four little legs cut out form a square tube.
Step 3: Angle Grinder Clamp
You are gonna need to build some sort of rotating arm that will have to sustain the weight of the angle grinder. On this step you will have to go fully custom, because no two angle grinders are made the same. With that said, our arm was built out of the same steel sheet we used for the table. Check the images for more detail.
The rotation is made possible by two heavy duty ball bearings mounted on the table. This kind of bearings are not cheap to buy, but fortunately you can get some very similar ones out of an old washing machine's motor. Those should be thick enough to grant stability and stiffness to the machine.
The bearings must be mounted coaxially! Take your time and do it properly, otherwise you'll have to re-do it again. Seriously.
Also, be sure to mount the machine perpendicularly to the table!
Step 4: Auto Lifting Mechanism
It's very practical to have a mechanism that lifts the machine once you let it go, making the "lifted state" it's idle position.
To achieve that, we used a pretty strong steel spring, considering that the grinder is pretty heavy. The spring attaches to the grinder's arm and a support, welded to the base. Check the pictures for more detail.
As a side note, you want the spring to lift the grinder, but a too strong spring may cause some problems, so you should choose properly. Anyway, you can always adjust the lever by moving the attaching point on the arm.
Step 5: Cut Guides
When using the machine, you will need some sort of reference, if you want to make straight cuts. So my father decided to build a guide, that can be mounted 90° or 45°. That is done by using two modified screws that screw on four different nuts welded under the table. This allows you to make consistent cuts.
Step 6: Handle
An important detail.
As a handle, we used a part of an old hand drill, that we found laying around, following the "low cost" philosophy. Is unlikely that you have one, so you'll need to get inventive on this. You may just build one from the same steel sheet, for example.
Anyway, we simply welded that handle to the grinder's arm, and that's it. A well welded handle is a seriously relevant safety feature.
Step 7: Style Is Also Important
At this stage, the machine was very ugly. So some masking tape and a bit of paint were required. The most important thing, is to keep the paint out of the bearings!
Seriously.
Step 8: Conclusions
In the end, the machine came out pretty much as expected. We've been cutting metals, wood and plastics (a bit of an overkill, but it works) with no problems.
It might not be the safer machine in the world, but that's pretty evident. However, if used with protections and precautions, it will cause you no harm :)
Hope you enjoyed
Making things like this is what really gives you some satisfaction :)
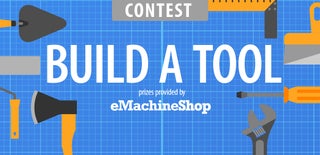
Participated in the
Build a Tool Contest 2017