Introduction: Cube Lamp
I am a first year Design student and NC State's College of Design in the Industrial Design program. In my first studio, as a final project, we were instructed to create a light source and left with free reign of what that meant and what to do with it.
I went though multiple designs and settled on what appears to be a very simple shape, a cube, that emits light. However, when you really get down to it, the simplest shapes are often the most complicated to make. This project turned out to be one of the hardest projects I have ever worked on, yet was the most rewarding by far.
I wanted to share this with others to receive as much honest feedback and critique about my design as possible. I would love to hear from anyone who decides to tackle this project and I would be more than happy to hear your changes and share my input with you. Please enjoy.
Step 1: Materials
For this project I really wanted to showcase my experience with woodworking and create something that was not only beautiful to look at, but something with a tactile quality. After a trip to a nearby hardwood supply warehouse, I found a beautiful piece of one of my favorite woods, Wenge.
Wenge, for those who have not worked with it before, is an extremely dense wood and creates a very fine dust; with that in mind, precautions should definitely be taken to prevent inhalation. Sanding wood that is as hard as Wenge can be very time consuming and patience is a big part of this project, yet the end product is more than worth it.
As for the clear sections, there are a few choices of materials, I did some testing with clear polycarbonate sheet, yet discovered that Cast Acrylic allows for more light to be directed to its edges and worked better for my application.
To bond everything together I used a clear, two-part epoxy. Wood glue isn't helpful in this project because there isn't actually anywhere that you bond wood directly to wood without acrylic between. Be sure to invest in the box that comes with the two bottles instead of the syringe system. It's not quite as convenient, but you will use a lot of epoxy in the final construction.
Step 2: Ideation and Sketching
As you should with any good design, I went through multiple ideas and designs before settling on a final one. In the end, I decided that a simple design that focused on my love of joinery and fine woodworking would mean the most to me in the long run. The hardest part of this build is the number of complex and compound angles that play into every corner. Not only do you need to focus on the outer layer, but the way the angles play together all the way inside. It will become clear later where the problems arose. Lots of sketching is the key to success here. Since I was working on a college budget, I did not have any spare materials, meaning I only had one shot at the final product. I can honestly say that without the amount of sketching I did, I would not have been able to make it work.
Step 3: Testing
This is the point where I had to find out if my theories would work in the real world. Although prototyping is not required for those following along, it was crucial to my design process.
The first test was just a piece of polycarbonate epoxied between two pieces of plywood. I was thrilled to see that this accomplished my goal even better than I thought it would.
Next I mocked up a little experiment out of hot glue and cardboard to see what it would look like three-dimensionally. At this point in the process I was still playing around with other shapes so the end result was a pyramid for this test.
Finally it was time for a scale model with all the little details. I used MDF and polycarbonate, following essentially the same steps that I used for the final. At this point, I was working with a simpler design, with only the corners illuminated. Once I created the scale model it became apparent that there needed to be more visual interest and complexity. This is one of the most important aspects of scale models and where it helped me the most. After this point, I cut out the intersecting lines and devised a method to create them.
Step 4: Cutting
As I mentioned before, I had exactly the right amount of material and I followed the method of "measure 6 times, cut once." I had purchased a 3' x 6" x 1" board of Wenge and I had a sheet of cast acrylic that was approximately 1' x 2' x 1/4".
I purchased the material before I had finalized a design or I would have picked up some more of each and I recommend that for anyone else doing the project because it would have saved me a lot of trouble.
I cut the Wenge into 6" squares on the mitre saw then moved to the table saw to cut my 45* angles because I knew that I could run them through multiple times to ensure that they were perfectly square. The end result was a stack of 6 very consistent squares cut at the angle measuring slightly under 6". I was fine with it not being a full 6" because there was nothing else relying on the size as long as they were equal to each other.
Here comes the tricky part. Since the light source is inside the box, the acrylic edges must be created by sheets that fit between the mitered joints of the Wenge that create a box on their own. Not only that, but the three edges that come together in the corner must touch from outside to in. If that wasn't complicated enough, I didn't want to leave a little triangle of openness, so the edges of the acrylic also needed to be mitered on the short ends. This is a lot to take in all at once so in the next few steps, this will be explained in more detail.
Let's take it one step at a time. If you take one segment of wood that is cut at 45º and take a look at the face that has been ripped on the table saw, you will notice that the angle that creates the flat face is not 45º. Instead, it is much closer to 35º.
Now that you know that angle, you want to rip some acrylic at approximately 2". This is not something that needs to be precise because you will overhang it in a future step then grind it off, however it helps if they are consistent. You will need 12 segments at a length somewhere around 7 to 8 inches.
On the mitre saw, cut the acrylic at 35º with the long to long ends at 6 1/2" inches. They should look like elongated trapezoids as pictured. These will eventually sit in the middle of each edge and meet up with each other in the corners.
This step required a bit of creativity and a steady hand. 1/4" Acrylic isn't something that you can run through the table saw at a compound angle to accomplish the small corner needed on the end of the angles we just pictured (its easiest to understand this by looking at the pictures) so I set the 12" bench disk grinder at 30 degrees and slowly bumped the acrylic edges I just cut against it, flipping it regularly until the top edge of the edge resembled an arrow. Make sure that the new faces you created are all as even as possible.
Practice on a scrap piece and make sure you are comfortable with it before you move on to the final pieces, it isn't a technique often used and takes a little practice.
These steps are ones you should make sure to take your time on, the more accurate you are here, the easier the rest of it will be and the better the final product will be.
This step is hard to explain in words so please make sure to look at the pictures, as they help to further illustrate the process.
Step 5: Painting
Here is where things start to really come together. As I mentioned before, I used a two part epoxy and had great results, however in my testing I was reminded that smooth surfaces do not bond well so you must sand the acrylic first so the cube does not fall apart. I used a 220 grit sand paper, however anything heavier will also work.
One thing I discovered after gluing the few first pieces on, is that once you apply epoxy to the acrylic, it becomes clear again as it fills in the little gaps. Because of the imperfections in my craft, you could see the little bubbles through the edges once it was lit from behind. The best solution I found was to paint the acrylic black on the faces. The two things to be carful masking off are the short side (they end up inside the box and must collect the light) and the 30* edges we sanded in the last step. Those edges touch other acrylic and would show up more if they are painted. In the final two pictures of this step you can see my small scale tests, the first one has visible bubbles in it, the second one was painted before assembly and looks nearly perfect.
I used a matte black paint however anything black or dark brown will work. If you are using a lighter colored wood, I would aim to match the color of the wood.
Step 6: Gluing
The assembly of the edges and faces is by far the most time consuming and stressful part of the project, however none of it is too difficult. Make sure that you wait the full 5 minutes when gluing pieces for them to set, if they move, you will be causing yourself a lot of extra problems. One of my last sides shifted before it was completely dry and ended up causing me a few extra hours of work where it would have only cost me 30 seconds to hold it together.
The following steps explain how I glued my faces together. If you come up with a better method to do this, please let me know, I would love feedback.
Once you have picked which of the six sides you want to be the primary bottom, you will glue 4 of your acrylic pieces to it. The one thing to keep in mind here is that this is a very temperamental puzzle, if one piece doesn't seem quite, grab another. Because you ground the edges on the bench grinder, they're all slightly different and that works to your advantage.
Once you have found four that fit together well, mix up enough epoxy to cover one face of a piece of acrylic and then glue it to the wood. The acrylic should overhang on the two long edges, however you want the short edges to be as perfect as possible. You should be sure to wipe any extra epoxy from these corners and make sure that both of the angles meet together as evenly as possible.
Slide it around as you put it in place. This accomplishes two things, it makes sure you get epoxy everywhere as well as helps you make sure you have it as well lined up as you can.
After that one has set (5 minute epoxy means it should be set in 5 minutes) you should work your way around the rest of the base repeating the process, this time though, one edge will bump up against the first piece. The final piece will lock in like a key stone and your base should be done for now.
I unfortunately have very few pictures of this step because my hands were covered in epoxy at the time. Your acrylic pieces should also be painted here.
Step 7: Gluing Part II
I should note, I added aluminum foil to the inside to help reflect light. I'm not sure that it did anything useful and I would most likely not repeat it in the future.
From here, you will be making the rest of your cube, the first wall is the most difficult because it must stand on its own. After applying the epoxy to the acrylic on one face the base, set your first wall on. The process for this one is nearly identical to the first gluing step, it's just a little more difficult because you must hold up the piece of wood. From there, work around in a circle, alternating acrylic and wood. The acrylic in the bottom corners should meet together and not leave any gaps.
Leave one of these four sides off, it will be how the lights go inside. The one you leave off will be one of your two rear faces.
Attach the three pieces of acrylic that go on top of those walls next. The top will then get glued on followed by the final piece of acrylic. If you prefer, the acrylic can be wedged in before the top piece goes in if you think that is easier for you. I did that and it worked for me however I don't see one major benefit of one method. (Once again, I would love to know how any other methods work for you.)
Step 8: Lighting
I knew that due to the clean look I was going for with this lamp that I wanted it to be sealed shut, that meant the light had to not get hot and wouldn't be able to be replaced. I quickly settled on LED light strip. After I did some testing I found that I liked the warm white lights. It does however look really cool with a cool/blue white light as well as red. You can see a very cold white light I used from a flashlight in my scale model. The cooler light gives it a more futuristic look and is all personal opinion.
To mound my LED lights, I attached them to wooden circles and put those circles on each face. This allowed for the circles to be as close to the acrylic as possible and give me even lighting on all edges. I tried squares as well however it gave me very dark corners.
I cut the circles with a hole saw. Because of the spacing of the LED's on my strip I had to wrap tape around the circle to make it a little bigger and help the most lights fit around without overlapping. I cut using a bit that was 1 1/4".
I wired the lights together using pre-made connectors to the manufacturer's specifications.
I had to remove the plug on the power cord so that I could fit the cord in the side of the box (explained in a later step) so I just wired the power cord directly to the first connector and then used heat shrink tube to ensure that it would never come off.
We cannot glue the light discs in yet because running the cube through the table saw again to create the crossed pattern is extremely risky for a number of reasons. You don't want to break your lights or cut your wiring, you don't want to short something out, and most importantly, if you are using a "saw stop" saw like I was, it would trigger the blade safety and cost you a few hundred dollars in blade replacement. (Side note, if you are using a saw stop or something similar, do not use the aluminum foil, I was fortunate to have access to another saw to make my cuts because I had already glued the foil in.)
Step 9: Cutting Part II
This is the point where we make the cuts for the crossed lines on the top and bottom of the cube. You can do whatever configuration of lines you like on this as long as you pay attention to where your light discs will fall on the inside in the end.
At this point, there should be no lights inside the cube and one side should still not be glued on. All of the edges of the cube's acrylic will be sticking out about a quarter of an inch. I used a combination of a disk grinder, a Dremel grinder wheel and a palm sander to bring all the edges down flush to the corners of the box and round them over. If you stick a flashlight inside you will get your first glimpse of the glowing edges. The goal here isn't to get it to a finished edge, but instead let the box sit flat on its wooden faces. We are about to run the whole cube through the table saw and you want to make your cuts flush to the faces.
Now, off to the side, laminate two pieces of acrylic that are about 3"x7" together with acrylic, then paint the whole thing black just as before. This can be a rectangle. You will want 4 laminated rectangles in total. After they have cured, cut out a 1"x4" segment as shown in the drawing. In the end, this will match up with the inside of the box and allow the light in at the inside surface level. Use a band saw or a Dremel cutting wheel for this.
Make these cuts as smooth as possible and sand it with about 220 grit sand paper. Depending on how much you sand the outside after you finish the box, you may be able to see these cuts through the acrylic. Looking back on it, I wish I had made my cuts a little cleaner.
I made a few minor mistakes at this point that turned out to not be a big deal, however I would avoid them if doing it again. So be sure to make the cuts in the correct order
The first two cuts to make are going to be opposite each other without cutting through the open side.
Set your fence at 1 1/4" (this is what I chose, however if you change the pattern, you will need to adjust accordingly) and slowly run the box through with the blade set 2" above the table. Slowly move the fence over a little at a time until your laminated acrylic fits snugly where you can press it in but not force it. When I tried to put my first piece in, I thought I could hammer it in and eded up snapping of a segment of the Wenge. This was definitely a panic moment for me, but a little wood glue fixed it right up.
Coat the inside of this grove with epoxy and slide in one of the rectangles of acrylic in each one. After these have cured. Grind them down just as you did with the corners.
Next, set the 6th side of the cube in place and make sure that the edges are sanded so that it is as flush as the rest of the faces. Keep in mind which face is the bottom and where the front and back are, if your cube is well made you may lose track so masking tape wit labels are a great help.
Now, tape the loose face onto the box using masking tape. Be sure to use enough that it is snug on the box, without moving, yet not to overlap so much tape that the box sits unlevel.
Make the two perpendicular cuts through the box on the table saw cutting through the acrylic you just sanded down. You should wait to insert the final pieces of acrylic until after the next step. The final pieces will lock everything together and make sure your cube won't fall apart.
Step 10: Adding the Lights
To me, this was one of the most exciting steps. This is where all the lights get put inside and you really get an idea of what the final product is going to look like.
The first thing to do is figure out where to locate the power cord. I settled on a location in the rear next to the corner. I'll explain what I did, but you can put the power cord anywhere you think looks good.
I wanted the cord centered in the corner between the acrylic that runs up the side, I used a Speed Square to mark an "X" and find the center. I found a drill bit that was exactly the size of my power cord and drilled right in the middle of the "X." The tricky part here is that your hole won't pass all the way into the box so I used a Dremel to grind a little trough in the corner that lead to the middle (pictured.) This method worked great for me and I would do it the same way again.
Once the Power cord is run through the final face, wire it directly into the first light and heat shrink over the joint if you wish. I put epoxy all around the cord to make sure it wouldn't pull out in the future. Make sure that the cord sits far enough down in your trough that it won't effect the joint in the corner.
Next, glue each of the light discs onto the faces with your Epoxy (or wood glue if you would like) try to route your connection wires so that they won't sit against any of the acrylic, if it does, it could create shadows in the final product.
Next, glue on your final face of the cube when you are confident that you will not need to fix any of the wiring. At this point the cube will be sealed forever.
The last part to be glued in is the final acrylic strip on both the top and bottom. Do exactly what you did on the last step.
Step 11: Finishing
At this point, your cube is in it's final stages. I first used a palm sander and got it as smooth as I could and then moved on to hand sanding. After I worked down to 220 grit, I decided that I wanted to keep my acrylic surfaces as frosted as possible so only focused on sanding the wood here.
When it was time to finish the acrylic, I decided that the best approach to this would be to give it all a linear appearance. I masked off everything but the acrylic and sanded along the length of it giving it a sort of "grain" With the acrylic on the top and bottom, I sanded the one that had been intersected by the other one first, then masked it off and sanded across it so it looked as consistent as possible. This is a very minor thing and you can do it however you like, but this worked for me.
After I was done sanding, I used "Teak Oil" that I had laying around letting multiple coats soak in. I followed the directions on the package doing one side at a time then buffing the whole thing with a rag.
Step 12: Done!
Congrats, now all you have to do is show off your lamp.
I am really happy with how this project turned out and I hope that you can take what I have done and improve on it. I would love to see what others can do to make this better so please let me know if you decide to try it too.
Thanks for reading,
TJ
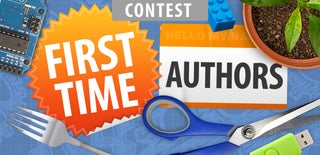
Participated in the
First Time Authors Contest 2016