Introduction: Custom Iron-On Artwork Using a 3D Printer
Printing 3D objects is a fascinating thing. Still, many people don't realize that standard 3D printers can be useful also for tasks which you might think of as being "2D". In this instructable, I'll show you how I make use of my 3D printer to create custom iron-on artwork, useful to create custom bags, t-shirts or the like. It's easy (no 3D design needed!), it's much faster than printing 3D objects (just 2-5 minutes print time), and it's fun!
I will try to describe the process in detail. When you do this the first time, it will probably involve installing some stuff and take a little longer. But trust me: once you have everything set up and done this the first time, it's dead simple.
On the day I write this instructable, my daughter has been invited to a friend's birthday -- 7 year old Malte, from her clarinet class. The party is going to start in about one hour and we still need a present. We want to create a custom felt bag for his music scores, with his name and a clarinet on it.
DISCLAIMER:
1. Please note that some people see good reasons for not giving a 7 year old child a bag with his or her name on it, as strangers might take advantage of knowing the name ("Hi Malte, remember me? Your father told me to pick you up here ..."). Our Malte is mature enough to carry this bag :)
2. I'm not responsible for any damage to your washing machine, which might arise for example if you wash these fabrics too hot, or to your electric iron because you forgot using baking paper. Just take care and all should be fine!
And please: If you have any corrections or questions, tell me, and I'll try to make this better.
Let's see what we'll need:
Step 1: Things You Will Need
- a 3D printer: any printer that can print PLA or your filament of choice will do
- filament: PLA is a good start as it get's soft beginning with 70°C. However, it's pretty stiff, so it is better suited for things like bags, while printing large PLA artwork on a t-shirt might be uncomfortable to wear. Although I haven't tried it yet, you might want to try flexible filaments like NinjaFlex for t-shirts
- some fabric to iron your artwork on -- I found felt bags to be a fine ground to do this kind of thing. Keep in mind that you can not wash this fabric at temperatures where the filament will get soft, so you might think twice befor printing panties!
- a pressing iron
- baking paper. Sandwich paper did not work that well for me, sticking to the plastic later and making colors bland. Baking paper is made to withstand high temperatures and keep things from sticking to it, so it's perfect for the task!
- you might want to use a glue stick to make the artwork temporarily stick to the fabric when laying everything out, so things don't get out of place. However, I mostly found this not to be necessary
Step 2: Find a Suitable Illustration
Of the illustrations above, two are definitely not suited for what we want to do, two are perfect.
So what's a suitable illustration for your artwork? Keep in mind that we'll iron this on, so there's no sense in printing 3D surfaces, we'll just create a plastic sheet that will melt and bind with the fabric. And as with most 3D printers as of now, it'll have to be in just one color. So, you'll look for black and white, silhouette-like illustrations. Black and white drawings like inked sketches are not a good idea as single lines without an adjacent solid area will tend to loose their shape when you take them off the build plate. Depending on the quality of your printer, very fine details might pose a problem. And finally: keep in mind that different parts of your illustration that are not connected will have to be placed separately -- like for example every letter of a text and even every dot of every letter "i" in your text.
If the illustration you want to use happens to be in SVG or another common vector graphics format, this also makes your life easier -- you can then skip the next step, the vectorizing of a bitmap. A good place to find free SVG cliparts is openclipart.org, where I got the example pics used above. See the comments to understand why some illustrations are a bad idea.
If you want to try all this out without going through some of the hassle in the next steps, here you will find some STL files from animal pictures that already have been prepared by thingiverse user elk to be ironed on. If you don't want to prepare your own but just use one of those, you can continue with step #5 from here.
Searching for "clarinet" in a famous image search engine quickly led me to a suitable silhouette for my project. Please, if you plan on selling this kind of things, get the rights to use the picture commercially first!
Step 3: (optional) Create a Vectorized Image From a Bitmap
A 3D printer doesn't print like an inkjet or laser printer does: it doesn't draw pixel by pixel, but the print head moves in lines, straight or curved. This means your picture also has to exist in the form of lines and curves, not as rastered image. The process of converting a "normal", raster image (like PNG, JPG or BMP) to a vector format is called "tracing".
If your silhouette is already in some standard vector format, like SVG, you can skip this step. If not, there are several software packages you can use to transform your image to a vector format. If you are the lucky owner of commercial software like Adobe Illustrator, you might want to use them. I'm not, so I use the open source software Inkscape, a free (as in "free beer" as well as in "free speech") vector drawing program available for all major operating systems (see http://www.inkscape.org). In this program I not only vectorized the image but also added the text, "MALTE".
I will give a short description of how I vectorized the image I used -- depending on your image, you might need to use a different vectorizing method or different parameters. If things get tricky with your image or you just want a more detailled description of this step, please refer to this tutorial about tracing bitmap images in Inkscape:
Using Inkscape, I first imported my black and white bitmap using "Import ..." in the "File" menu -- the default import options normally will do fine. I then selected the imported bitmap and chose "Trace Bitmap ..." from the "Path" menu. You will be offered different tracing methods and parameters; with many silhouette bitmaps, the default method "Brightness cutoff" will do fine. You can try out different values for "Threshold", seeing the results in the preview area on the right, after clicking "Update" or activating "Live Preview". When you are content with the results, click OK to trace the bitmap. After that you will have the traced vector shape on top of the imported bitmap (you can see that after clicking and moving the vector shape). Just delete the bitmap if you want.
If you don't manage to create a decent vectorized shape, you can try out different tracing methods and parameter values, or refer to the above mentioned tutorial -- there are too many options to tracing to explain them in this instructable.
Step 4: Make That a 3d Printable STL-file
Now, you can't just print any vector image on a 3D printer -- your printer wants a three-dimensional object, so what we'll create is a representation of your image as an 0.2mm high object. There are several softwares you can use for this, for example the MatterControl 3D printing software offers an image plugin to make this extremely easy ("Image Converter"). But if you just use a standard software, you'll have to do this manually. I did this using the Inkscape vector drawing application already mentioned in Step #3, and another free software, the OpenSCAD parametric CAD application. Ok, this step requires installing some things and at first might look intimidating, but it really isn't hard.
Here's how:
- install dnewman's OpenSCAD-Converter, an extension to the Inkscape software: see here for the latest version of the converter, and here for how to install it
- restart Inkscape and open your vectorized image
- now select your image and scale it to the size that your iron-on artwork should later have -- you should do this now, and not later in the 3D printing software
- after installing the OpenSCAD-Converter you will now find in the "Extensions" menu a "Generate from Path" sub-menu -- there you choose "Paths to OpenSCAD ..."
- in the resulting dialog, give a folder and file name (ending in ".scad"); for the height parameter, enter 0.2mm height; then click OK
Now open the resulting "filename.scad" file in the OpenSCAD application, which you can download here. The code you see here looks intimidating. But there's really not much to do here, just:
- click F6, so everything get's rendered
- after that, select "file" menu, "export", then "export STL ..." to save your object as a 3D printable STL file
Step 5: Print!
Now the fun part starts. Print the resulting STL file in your 3D printer and with your 3D printing software of choice. It will not take much time as you'll only print one layer. But take a look at your filament and at your slicer settings:
- I used PLA filament which has a melting point that makes ironing on easy. However, it's stiff -- perfect for notebook bags, but if you want to iron this on clothes, you might want to experiment with flexible filament like NinjaFlex or similar products. However, I have no experiences with this and not every 3D printer is suited to print flexible filament
- use 0.2mm layer height and make sure you don't have a differing setting for the first layer, so only one layer will be printed
- better print slowly; no need to rush, as printing only one layer will only take few minutes anyhow, and printing slow means better quality
- remove your print from the print bed with caution -- if you're using a heated print bed, let it cool down first; this makes it easier to remove the thin print without damaging it
Step 6: Iron On
We're almost there: heat up your electric iron (I use full heat, but with different filaments you might need less heat) and place your parts where you want to iron them on. If you have a lot of small separate pieces, you might put some glue stick on them so they don't get out of position too easily. If you use lettering, like I did here, it helps to print out the text on paper once, as an example for the right spacing of the letters.
Put a sheet of baking paper over it, with caution so nothing get's out of place. Iron over the baking paper; after a while, cautiously lift the paper here and there to see if you heated enough and the plastic has really bonded with the felt. Take care not to touch the plastic with the iron, only iron over the baking paper!
Then finally, remove the baking paper. You're there!
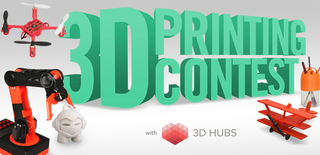
Participated in the
3D Printing Contest