Introduction: Custom War Maul
When it comes to making costumes and props, I prefer mine to be a little more... functional.
Step 1: Design
For the design, I wanted this maul to be original and unique, but it also needed to be simple enough that I could actually make it. Choices like the truncated ends and smaller mid connection created a dynamic profile (instead of a solid rectangle) without being too ornate. The large faces on the sides provided room for a detail that wouldn't impact the construction.
I drew out the rough idea to get a grasp on the number of pieces required and also the order of assembly. Putting this together in the right order was critical to success.
Using AutoCAD, I was able to lay out all the parts and get the exact numbers (accounting for ~0.10" thickness of 10 gauge mild steel) so that things would be assembled smoothly.
Step 2: Cutting
With the CAD file prepared, it's time to let the machine do the work! While an hour might seem like a long time on the water jet, I can't imagine how long it would take me to accurately create the 35 parts otherwise. And time was certainly in short supply!
Step 3: Tack Welding
The large assembly was broken down into three main components: the center body, middle connections, and outer heads. These were prepared in sections before attaching them to each other.
Step 4: Weld and Grind (round 1)
With all of the components tacked and ready to go, it's time to weld the length of all the seams. Grind all of the edges down smooth, and note that the components are still independent of each other.
Step 5: First Connection
Attach the middle connections to the center body. You'll notice that all of the welds were done on exterior corners. In order to keep interior corners clean (wouldn't be able to grind them smooth) the exterior corners of the middle section were actually inside the maul head, and dictated the order in which parts were assembled.
Did that make any sense? The outside is inside because the inside is outside, ya?
Step 6: Second Connection
Attach the outer heads to the middle connectors. Again, these welds occurred inside the maul, hence why the end needing to be open in order to gain access.
Step 7: Cap Ends
Cap off the ends finish the last bit of grinding.
...so much grinding...
Step 8: Collar
To attach the wooden handle to the maul head I needed a collar. I really lucked out on this one and found a scrap of pipe that was exactly the right size! I didn't even need to cut the length down, only clean up the edges. Since the handle was oblong in cross section, I squished the pipe ever so slightly with the arbor press. Now that I had a flat-ish side it was easy to put in the drill press.
Step 9: Sandblast and Powder Coat
Sandblasting! For when you haven't punished yourself enough in any given day.
After all the scaling has been removed, rinse and clean with either Acetone or TSP. Powder coating is the easy part, so it kind of feels like the reward for the previous monotony.
Step 10: Handle It!
I picked up a standard hickory wood replacement handle, which you can get at your local hardware store. Rough up the portion where you want to add leather and cut cut some small strips to go under the final layer of leather. Wrap the leather strips around the handle where you want a raised portion (I did three), securing them with super glue. The tacks aren't necessary, but I wanted to try for additional details that looked like rivets.
Step 11: Leather Wrap
The under-straps were spaced so that you had two options for holding the maul. Measure the leather wrap so that there is a 1/4" overlay and then soak it for 30 minutes. Start with super glue to hold the leather on. If you are working with a small piece, super glue will work for the whole thing, but in this case I used Sobo (heard wheat paste is good too) for the remainder of the handle since tying off took a while. Wrap the whole thing tight with string or twine. Ideally the string would be fully adjacent to itself the whole length, but I was short on time. Leave the string on for 24 hrs as the leather dries, which will shrink and hold (so I'm told).
Project was finished in ~25 hrs. It was a long day.
The process is there, but next time I want to cut the leather more accurately for a better finish. Unfortunately I was in a rush to deliver this gift to a friend and got there just in time. Barely had time for a shower and arrive "fashionably late". I also didn't get to see the finished handle without string since the leather was till drying, so hopefully I get to check the final results.
Sure hope it worked!
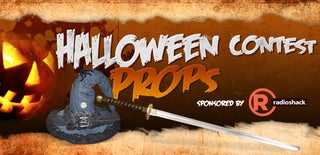
Participated in the
Halloween Props Contest