Introduction: DIY Pottery Wheel (Using Treadmill Motor)
I set out to build a pottery wheel for my 7 year old daughters Christmas present. She saw a toy pottery wheel at a local craft shop and had to have one. Knowing that these "toy store" units do not actually work properly, I did not want her to be disappointed. Now we have a quality pottery wheel that the entire family can use and enjoy..
Step 1: Step 1 Acquiring a Motor
I did some online research and learned that treadmill motors work well for powering pottery wheels. The motors on most treadmills are DC motors which are able to operate at variable speeds. After asking friends and relatives if they had or knew of any old treadmills, I resorted to Craigslist. I was able to purchase a used treadmill for $35 . I'm sure I could have found one even cheaper, but I was in a time crunch to be able to complete this project in time for Christmas.
After bringing the treadmill home, the first thing I did was to disassemble the unit and remove the motor and all wiring and electronics that were needed to operate the motor. On the treadmill control console was the speed control knob, ( I purposely bought an older treadmill that used a rotating knob to adjust speed, versus push buttons ). Inside the base of the treadmill was a circuit board and a coil (referred to as a choke in the manual). I also removed the on board circuit breaker that was used in the treadmill. Once all the parts were removed , I tested them to make sure everything was still operating properly.
Step 2: Step 2 Preparing the Motor
The treadmill motor had a pulley/flywheel in place. The pulley had several grooves in it to accept a serpentine type belt. Serpentine belts are more expensive and harder to come by than a traditional v-belt. I also did not want the flywheel portion of the pulley either, I wanted the pottery wheel to stop when the power is turned off, the flywheel would have allowed the wheel to continue spinning after powering down. The pulley was threaded onto the motor shaft with a left handed thread. I was able to hold the motor shaft with a pair of vise-grip pliers and spin the pulley off by hand, turning the pulley clockwise ( righty is not tighty in this situation). I used and electric angle grinder to cut the threaded portion of the motor shaft, ( a hacksaw could have been used instead). The remaining motor shaft was just over 5/8" in diameter. I purchased a 1 1/2" diameter v-belt pulley from my local tractor supply store for $9. It came with a 5/8" hole in it. I had to bore out the hole slightly larger to slide onto motor shaft properly. A set screw included with the pulley secured it to the shaft.
Step 3: Step 3 Building the Base Frame
I cut the top surface of the pottery wheel base out of an old piece of 3/4" thick Melomine salvaged from a previous project. I cut it in a triangular type shape, wider at the rear of unit to hold tools and a water bowl , narrower in the front to allow the user to get as close to the wheel head as possible. I built a 2 x 4 frame around the perimeter of the top surface for added strength. Side pieces were cut out of some leftover Maple plywood. I first made a little "mock up" to determine how tall to make the sides , trying to keep the overall height of the unit as low as possible to allow my daughter to use it comfortably, while allowing enough space to accommodate the motor. I made the plywood sides stick up 2" higher than the top surface to keep tools and whatnot from falling off . I also rounded the top and front edges of the plywood using a router. Before attaching the sides, I laminated a piece of old Formica to the top and trimmed the edge with a router with flush trim bit installed.
Step 4: Step 4 Wheel Head Support Bearings
Originally I purchased 2 sealed ball bearings with flanges and pillow blocks to hold the bearings. The total cost for these was over $60. I saw another post online where the person used a automotive wheel bearing (hub) assembly. After some thought and research I returned the bearings that I previously purchased. I went to an auto part store and bought a hub-assembly for a 1988 Buick Century for $35. This was the cheapest hub assembly I could find that has a flange for mounting to the top surface of the pottery wheel base. This hub in particular fits almost all General Motors front wheel drive vehicles manufactured between 1986 and 1989 ( Buick Century, Pontiac 6000, Fiero, Oldsmobile Cutlass Sierra, Chevy Celebrity etc.) making it very easy to locate and inexpensive. Sure I could have salvaged one from a junkyard vehicle and saved maybe $15 , but again , time was a factor and it was nice to have a brand new (re-manufactured) bearing free from grime rust and grease. Using the wheel bearing assembly really simplified the mounting and supporting the wheel head.
Step 5: Step 5 Making Main Shaft
I turned a piece of 1 1/4" round stock on the lathe. I reduced the diameter of a 2" long section of the shaft down to about .900 to fit snugly inside the hub assemblies center hole ( where the automobiles c.v. shaft would go). I turned the tip of the shaft down smaller to fit tightly into splined section of the hub assembly. I then cut the shaft to approximately 4" long and drilled and tapped a hole in the opposite end to accept a 1/2" diameter bolt that will hold the pulley on. Next I inserted the turned down end of shaft into the hub assembly. Although it fit very snugly, I added a couple of welds to tack it in place just to be sure it does not slip.
Step 6: Step 6 Mounting Bearing Assembly
I determined where I wanted the center of my pottery wheel to be located on the top surface of base. I then positioned the bearing assembly over that location and traced its shape onto the top . I used a jig saw to cut out the hole for the wheel bearing. I used three 7/16" bolts to solidly secure the bearing assembly to the top surface.
Step 7: Step 7 Building the Main Pulley
Looking at other peoples projects, I determined that the main pulley , under the wheel head, needs to be around 12" in diameter. Some people have used smaller diameter pulleys, sometimes using a original pulley from the treadmill. The pulley that was inside my treadmill was only about 6" in diameter. Some treadmills use up to a 2 1/2 horsepower motor. Since the treadmill I have only came with a 1 horsepower motor, I decided to use a larger pulley to offer a mechanical advantage ( more torque from the lower rated motor). I could have ordered a metal pulley from my local supply house for around $35. Instead I decided to make one myself. I constructed the pulley out of Masonite and Corian (solid surface counter top material) . First I cut the 1/2" thick Corian into a circle 11" in diameter. Then I cut two 12" diameter circles out of 1/4" thick Masonite. I used my router table to cut out perfect circles. I drilled a 1/8" hole in the table , 6" away from the edge of the router bit. I then drilled a 1/8" hole in the piece I wished to cut. I inserted a 1/8" diameter steel pin through my work piece and into the hole drilled in the router table. Turn on the router and rotate the work piece around the pin and a perfect circle is created.
The 1/2" v-belt is actually just a little wider than 1/2". to accommodate the belt, I sanded a taper on the inner edges of the top and bottom masonite disks. To hold the three pieces of the pulley together, I drilled and bolted them with 5/16" diameter bolts and nuts.
* A note about the Corian*
I used Corian for the center of the pulley for a couple of reasons. First, it was the correct thickness I was looking for (1/2"). Second, it was smooth and of uniform density, as opposed to plywood. And finally, it was free, and it seemed like an excellent material. I obtained the Corian from a local cabinet shop that sells and installs solid surface counter tops. I asked if they had any sink cutouts left over. They directed me to the back of the building where they had many left over pieces...JACKPOT..They leave them out for people to salvage rather than throwing in the dumpster. I also found a 3/4" thick piece to use for my wheel head.
Step 8: Step 8 Attaching the Main Pulley to Wheel Shaft
To attach the pulley to the main shaft, I used a 6"diameter circle that I cut out of a piece of 1/8" thick mild steel. It is held on to the pulley with the four 5/16" bolts mentioned in the last step. I then used a 1/2" bolt, installed through a hole drilled in the center of the plate, to mount the pulley to the main shaft ,which was drilled and tapped earlier. When determining the length of the main shaft, I tried to keep the pulley within 1-1/2" below the bottom of table.
Step 9: Step 9 Mounting the Motor
Now it is time to mount the motor. Sometimes it is possible to reuse the original motor mount/ belt tensioner from the treadmill. My treadmill did not have anything to work with. The motor does have a mounting bracket attached to it, The bracket has 2 flanges with 2 holes in each. On one flange I bolted one side of a 4" heavy duty door hinge. The other side of the hinge got screwed into a block of wood that I mounted on the inside wall of the base. The second flange got an elongated 3/4" diameter hole drilled in the center of it. I made a jack screw out of a 5" piece of 5/8" threaded rod. It goes through the elongated hole down to a block of steel, which is welded to a plate and fastened to the wood block mentioned above. A slot has been machined in the block and a hole drilled for a bolt to attach the threaded rod. The threaded rod can pivot to adjust for the angle of the motor flange as belt tension changes. Two 5/8" nuts and washers are added to the threaded rod. One below the flange and one above the flange. The lower nut can be turned either way to adjust belt tension. The upper nut is then tightened to lock the adjustment in place. I used a 1/2" v-belt that is 48" long.
Step 10: Step 10 Building the Wheel Head
I made my wheel head out of a piece of 3/4 " thick Corian. I cut it to a diameter of 11". Then I laid out the bolt pattern of the bearing assembly . I drilled and countersunk the 5 holes for the mounting studs. I cut out the center of the wheel to allow it to fit properly over the wheel bearing. I also had to shorten the length of the mounting studs that came with the bearing assembly. I first purchased metric nuts that fit the studs. Then I cut the studs to length with an angle grinder, leaving the nuts in place on the studs until after the studs are cut. Removing the nuts after the cut helps clear the burrs from the freshly cut threads. I also drilled and tapped 2, 1/4"-20 holes that contain socket head cap screws to act as pins to hold pottery bats in place.
Step 11: Step 11 Splash Pan
I had to do a little searching to find the right container to use for a splash pan around the wheel. Not to say that the containers are hard to find, quite the contrary. I ended up using 14" oil drain pans from the auto parts store. They cost $3 each. I used 2 pans to make the splash guard. I wanted it to be in 2 pieces and be easily removable for cleaning. I cut the oil pans easily with a pair of tin snips. Cutting them also allowed me to discard the section of the pan that contained the pouring spout. They are cut in a way so that the bottom of one overlaps the other by about 3". The oil pans work very well, and if you mess up cutting one, another is only $3 away.
Step 12: Step 12 Wiring It Up
I mounted the circuit board and choke module from the treadmill on the underside of the pottery wheel base. I thought it would be a good idea to have the pottery wheel protected by a ground fault circuit just in case, because water is involved. The simplest way I could think to do this was to use a GFCI receptacle, like you would find in your bathroom or kitchen. I mounted it in a "old work" style electrical box which attached nicely to the plywood base side. I used the original power cord from the treadmill. I ran the power cord into the GFCI receptacle. Then I ran power wires from the GFCI receptacle , one to the AC input on the circuit board, the other off to my on/off switch and back to the circuit board. The treadmill also had a 15 amp circuit breaker installed. I thought it would be a good idea to use this also. I drilled a hole in the side of the GFCI receptacle box and installed the breaker and wired it into the power circuit. I mounted a duplex " old work" electrical box also on the plywood base side. This box contains the on/off switch , speed control dial and a light that indicates when the power is turned on. I used a duplex switch plate and cut out one side of it with a dremel tool to accommodate the speed control knob. I secured the knob in place with some " shoe goo" silicon type sealant.
Step 13: Step 13 Finishing Touches
I added a thin plywood panel on the underside of the pottery wheel. It covers the main pulley , and guards against anything coming in contact with the spinning pulley and belt. I also brushed on 4 coats of clear varnish on the plywood base sides. The last thing I did was to cut out a couple of Corian bats. I drilled the underside of the bats to accept the locating pins on the wheel head. When working with the Corian bats, be sure to sand down the edges after you cut them. They can be extremely sharp
Step 14: Conclusion
Christmas came and the Pottery Wheel was a big hit with my daughter. She tried it out that morning and the wheel worked great. I centered the clay for her and she took it from there. When turning on the pottery wheel, there is about 10 second delay before the motor starts up. . It also starts up slowly then ramps up to the desired speed. This is because of the treadmills speed control circuitry It is important to turn off the power switch when it is done being used. Even though the wheel speed dial is turned to the off position, a small amount of current continues to flow to the motor which could damage the motor if left on. This is why I mounted an indicator light , to remind user that the power is still on. I plan on coming up with some type of foot pedal for " hands free" wheel speed adjustment.
Thanks for looking at my Instructable, I hope this inspires others to create cool things. I look forward to your questions and comments.
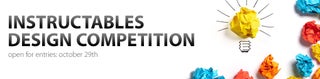
Finalist in the
Instructables Design Competition
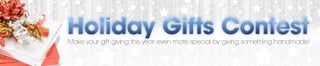
First Prize in the
Holiday Gifts Contest