Introduction: DeWalt Themed Mobility Scooter
While at the woodworking show in Indianapolis. My wife and I seen several mobility scooter at the venue. While holding all the stuff I bought and trying to find somewhere to sit to eat, one of these carts com rolling through with his products and a his food. I thought to myself that would be perfect for a place like this. So the next day, more out of curiosity then anything I looked on Craigslist for a mobility cart. I found a listing for $25.00, after reading the description I came to the conclusion that this cart worked and the owner just didn’t know how to fix the wiring. The owner just wanted to get rid of it. So I went after it. hints to the beginning of the build.
Social Media and other ways to support me:
Main YouTube Channel: https://www.youtube.com/user/mfwoodshop
Second YouTube Channel - https://www.youtube.com/channel/UCdRvBGv4Icdej48b...
Patreon - https://www.patreon.com/mfwoodshop
Istagram - https://www.instagram.com/mfwoodshop/
FaceBook - https://www.instagram.com/mfwoodshop/
Twitter - https://www.instagram.com/mfwoodshop/
Instuctables - https://www.instagram.com/mfwoodshop/
Lumberjocks - https://www.instagram.com/mfwoodshop/
Step 1: Lets Get Going
I started the video right here. To get you to the point I am now. I go back 2 days. I picked up the scooter for $25. The next day I had broken everything apart and cleaned and painted some of the main parts. That bring us to this point where I’m about ready to start putting things back together. I had to put things back together so I could find out if it all works.
Step 2: Front Forks
The front tire fork assembly. After everything got paint it was time to put this back together. The fork goes in first from the bottom. Then a bearing assembly, followed by a grease capped nut and a standard nut. On the inside a wedge shaped piece goes inside the steering neck get bolted on to that. The steering column gets a bolt and nut loosely tighten in order to fold down. One more hex bolt goes tors the front this bolt comes out if you want to fold the handles down.
Step 3: Motor Mount
The motor get mounted to the rear left wheel area. It is held on with 4 nuts, bolts, washers, and lock washer. The two hex screws push against the motor mount to apply tension to the chain. The chain need to be put on before anything else.
Step 4: Wiring and Handle Bars
Step 5: Floor Board
The floor board holds the batteries, the computer and the wires all start or end up there at some point. First I need to run the brake cable to the rear wheel. I won’t be able to do this after the components get put in. The cable runs from the left handle bar to the right wheel. It goes in though the front of the floor board pan and out the rear. I use 1/4″ grommets to protect the cable something the manufacture didn’t do. Grommets are good to have around the shop they come in handy. Next, I placed the board into the floor board the mount the computer. This board is held in with hot glue. The front two compartments is where the batteries go. I place two strips of weather tape to help with vibrations. Not completely necessary being AGM batteries it don’t matter to much.
Step 6: Frame Prep
The metal frame covered by wood. This made it easier to attach the floor board and other items. Strips of wood got cut to fit in there place. after fitting each piece I drilled a hole with an 1/8″ bit. The bit went through the wood and the frame to later be attached with a sheet metal screw. Counter sank the sheet metal screws head.
The same treatment as before to these to wire runs. Then I put together the main dashboard and headlight assembly
Step 7: Under Seat Box
This assembly goes under the seat. It provides a motor cover, a wire housing and over looks. I designed this part to emulate the looks of a DeWalt 20 volt battery.
Step 8: Trunk? Glove Box?
At this point I noticed I have been using a lot of the same tools metric allen wrenches, metric wrenches and slotted and phillip screwdrivers. I had this one compartment left over and decide to make a trunk,if you will, full of those tool. Kaizen foam by FastCap is a great thing to have is you shop you just never know when or how you’ll use it.
Step 9: Floor Board
The floor board is made one piece at a time. I was formed with two sides then a part in the middle. Then a few pieces around the middle to foam the secondary dash board. This holds the dual USB ports and battery indicator. This very useful two in one unit saved time and headaches.
The floor board lifts up and off to gain access to the components. It has a channel to hide the wires. It also hold the secondary dashboard with a quick disconnect. On the third picture you can see the little hole to maneuver the wires through.
Step 10: Wheelie Bar Wheels
The rubber wheels for the wheelie bar was just a bit chewed up. I mounted them to the lathe, cleaned and trued the tread. Then using my Texturing tool on the lathe gave it some new tread and life.
Step 11: Baggage
Step 12: Wrap Up
The switch put the scooter in reverse. The port on the right is a charger port. Headlight work but still need to be replaced with LED brighter bulbs. The turn signals also work and need to be replaced with yellow LED’s. Under the floor board holds two 12v AGM batteries, the computer and an extra area for tools. Added a DeWalt tool bag to the back of the seat. This stores the charger a 5mm hex wrench and a phillip screw driver. Everything you need to fold the scooter down and to get into the floorboard. The floor board is held down with four phillips screws. The handle bars fold down with a 5mm hex wrench. The charger plugs into a normal American 110v outlet, a plugs into a XLR female charger port.
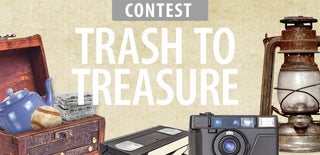
Participated in the
Trash to Treasure Contest 2017