Introduction: Deathly Drinks Tray (Designs Included)
Here's a little engraving project I've come up with, that's very cheap to do and providing you have an inkjet printer; the designs are available for you to use.
Step 1: Tools and Supplies
Basic Stationery: Ballpoint pens, Charcoal Pencil, Hair spray, Ruler, Rubber, Masking Tape etc.
Finishing aids: Polyurethane Varnish, Sandpaper
An inkjet printer
A Sacrificial Tray: This could be a cheap tray from your local home ware store. I used a photo frame with a sheet of pine glued/screwed into it.
The Design: I’ve thrown in a PDF file for the skull I designed, along with an Illustrator file for anyone who’d like to edit it. Open it, hit print and it’s ready to use.
Drawing a Skull of your own (Image 1)…
Using CAD to sketch a skull was a drag! Don’t get me wrong, there’s some plus points to using CAD, like the mirror/symmetry tools (which can add a little realism) and the linear pattern tools. As a skull is around five eyes wide, I sketched a horizontal line (to resemble the width of the skull), and plotted points on said line at intervals of a 1/5. This gave me two slots for the eyes to fall in, and the process of establishing proportions went on until I had a basic framework. For more info on human proportions, here’s an article that I used.
Step 2: The Transfer Process (Part One)
All you need for this is standard A4 paper, a charcoal pencil and a ball point. Have you ever had those moments where you've pressed a little too hard on a sheet and found scratches on the desk below? The idea of this method is to smear the underside of a sheet with charcoal, so when you press on the sheet, it’ll force charcoal into each little crevice on your work piece.
Image 1: It looks a bit rough but it’s for a good cause! Flip the print out over, then (with the help of a light box) apply charcoal to where you imagine the lines of the skull to be. You don’t have to be precise, shade loosely and consistently.
Once done, flip it back over, pull it tight and tape it to your work piece. I marked a line from the top, central point of the skull to the edge of the canvas; which allowed me to line it up proportionately.
Step 3: The Transfer Process (Part Two)
Image 1: Apply ink with a good quality ball point that’ll allow you identify the lines that you've already done, and press firmly here! I love to sketch, and in my view this is one of the only moments where it’s acceptable to be heavy handed in your approach.
Image 2: Worked out nicely. If you’d like the lines to be a tad bit clearer, or if you’d simply like to pick up the project another day then you can use hair spray to ‘set’ the lines. A floor heater or hair dryer will dry the spray in no time at all.
Step 4: Engraving
I’m pretty new to this so I won’t claim to be an expert. Buut, here’s a few pointers, albeit controversial, that might be helpful:
1) If it’s your first time, practise on a few pieces of scrap wood. Get a feel for the gun by experimenting with horizontal, vertical and curved lines.
2) Experiment with line thicknesses, ensuring that the important, defining lines are clear to see.
3) I find that an ‘Ultrafine’ marker is good for inking up a design. Apply it, sand thoroughly then apply again if the lines are disjointed in some areas. Varnish well to preserve the detail.
Image 2: Soldering iron stands are reaaally cheap over here. By removing the base, they can make good little holsters for engraving guns.
Step 5: The Help of a Jig…
Here’s a little jig I put together. Nothing fancy, but it’s good for clamping work pieces at a 45 degree angle so I can engrave comfortably at my desk. Those popsicle-like sticks (Image 1) allow the jig to ‘sit’ straight in a vice.
Note: The wing nuts are spinning on Coach Bolts (or Carriage bolts as they're otherwise known). Standard bolts are likely to spin when you twist the wing nuts. As long as the bolt you choose has something to stop it moving once it's fully inserted, you'll be alright.
Step 6: Clean Up
Sand it thoroughly, clean then apply any finish you like. I’ll leave the latter up to you guys, because how you go about cleaning something can very much depend on what you’re working with. For me, I set about cleaning unfinished wood with equal parts white vinegar and water i.e. nothing that’ll discolour it. Wipe it down with a damp cloth afterwards so it doesn't smell like a foot.
Step 7: Finish
A thin layer of polyurethane varnish and it was good to go!
As always, feel free to comment or message me if you have any queries. Ta
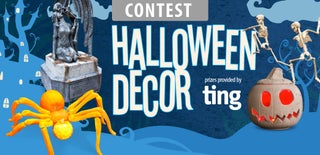
Participated in the
Halloween Decor Contest 2016