Introduction: Design Dust Control Adapter
Problem
I need to sand lead paint inside with my belt sander. LEAD IS TOXIC so I need to reduce its ability to become air born. Long wanting to find a better way then duct tap for attaching my vacuum to my tools. Now having a 3d printer making a better attachment is far more practical. So this is how I did it.
LEAD IS TOXIC DO NOT DISTURB UNLESS ABSOLUTELY NECESSARY.
SAFETY IS YOUR RESPONSIBILITY, USE PROPER PERSONAL PROTECTION EQUIPMENT, INCLUDING THE BIT BETWEEN YOUR EARS.
Personal note
This is the first time I've been able to document predictions, failures, and possible solutions effectively. Also this is a one day build concept to use including creation of the instructables.
Supplies
You may need (I used)
• dusty tool (belt sander)
• vacuum with filtering ability
• measuring tools (tape and calipers)
• pen and paper
• CAD program and computer (fusion360)
• slicer program (cura)
• 3D printer (ender 5 pro)
• tough filament (carbon fiber petg)
• cleanup tools
Filament Note
PETG is great for tools, tough instead of brittle like PLA. use PETG for tools and structural parts.
Step 1: Measure a Few Times.
Take and record measurements with doodles of the parts you're fitting to and duplicating. Remember when recording some parts need to fit in others and may have geometry that should be considered (the clip system on the sander and taper on the vacuum hose)
Step 2: CAD Time
Images follow numbered steps
1. Sketch each end so it aught to fit in the appropriate location taking into account for space needed for snug taper fits and clearance for mobile fits. (These parts are all round so it was drawn to be revolved.)
2. Create your basic shape using the suitable tools for your parts.
3,4. You may need other more complex aspects. (A retaining device was needed on the sander end so I created a tangent plain on the revolution and used that to create a compliant ball latch. )
5. Don't forget to use fillets to reduce stress concentration points.
Repeat steps as necessary and you may need steps I didn't.
Should any of you have one or both of the vacuum or sander I'm using I am including the fusion360 file for you to edit as needed.
Vacuum craftsman model 113.176120
Sander porter cable model 362VS
Step 3: Slicer and Orientation. Remember This Step.
Use parameters
This part is going to be abused and will eventually break. If we can print the part in a way that will probably break in a way that can be repaired quickly with tape to reduce down time in the shop. You can replace the part later.
Slicing suggestions
To get a part strong but likely to break in a predictable way, we must consider the layer orientation. Because layer lines and inside corners are most likely to fail we can rotate the part at some angle that causes the layers to bisect known stress multiplying areas, instead of in the same plain.
Print settings
Lots of perimeters and at least 30% infill.
Support, yes please. (As needed)
Step 4: Print Clean Up and Test
1. Printer is finished (remember to level your bed)
2. Clean up as needed.
3,4,5. Test fitting. Good enough but the retention system could be better (try multiplying the ball latch).
6,7. Working test. Better than expected. All the fine particulates were sucked up, leaving a easily sweep able collection of large sand like paint.
BUT SOMETHING HAPPENED.
Step 5: DESIGNED FOR REPAIR.
What happened?
1. As predicted in step 3 the adapter failed at a layer line. (I stepped on the hose)
• In a quickly repairable way with tape.
2. Fixed with tape. Job completed.
Design changes needed.
• reinforcement of vacuum end. possibly with groves for zip ties to fit in.
• add multiple ball latches
• adjust print angle from 30° to 15°
I'll reprint the part later with these changes.
Keep Making, Repairing and Modding
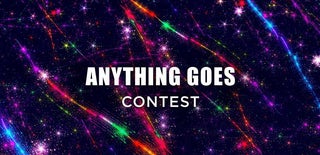
Participated in the
Anything Goes Contest