Introduction: Design, Model, and 3D Print an Optical Illusion Name Plate Using AUTODESK Fusion 360
Welcome! In this Instructable I will show you how to model and 3D print an optical illusion name plate! The name plate shows a single phrase when you look at it head on, but when you view the plate from the side a new phrase appears while the other disappears!
In this Instructable I provide step by step instructions for designing and modeling the illusion using AUTODESK Fusion 360. Even if you have never used Fusion 360 before you will be able to follow along and 3D print a sweet custom optical illusion name plate for yourself.
I printed my own name plate, as shown in the second GIF, using the same principals I show here and it has been a big hit at the office.
Before you begin you will need to gather your materials:
AUTODESK Fusion 360. This CAD/CAM/CAE software is free for hobbyists. It will allow you to model and export your name plate illusion. Download the full trial version for free forever from AUTODESK.
3D printer or printing service. If you don't have access to a printer try 3D Hubs to get a print made locally! I am printing my nameplate using a Rostock Max. A dual head 3D printer capable of printing with model and soluble support material would be ideal, but not required. I printed my model using PLA plastic for both the model and supports.
Slicing software (if you are printing yourself). I am using Slic3r simply because that is the software I spent the most time with, perfecting my print settings.
- Stencil font pack. You can download a free Stencil font here if you don't have one.
I hope you enjoy this Instructable and amaze everyone with your own name plate!
Step 1: How It Works
This illusion is very simple. All you need to do is figure out which two phrases you want to show, and cut one phrase out of the other diagonally at 45°. There are three tricks to getting the Illusion to work:
The phrase you choose to be solid must be printed thick enough so that you can't see any gaps when you look at it from 45° to the side. This is shown in Figure 1.
The phrase you cut out must be in a stencil style font. This allows every piece of the solid letters to maintain a connection to the body after the cut. This is illustrated in Figure 2.
You must connect all the letters together with a small base rectangle also shown in Figure 2.
If you are an expert 3D modeler and printer you have probably figured out what to do already. Get to it! If not, don't worry! Follow the remaining steps and you'll be an expert in no time. Every step of modeling with Fusion 360 and setting up a print with Slic3r is explained below.
Step 2: Open Fusion 360 and Sketch the Solid Font Base
In this Instructable, you will be modeling everything in Fusion 360 because it is free for hobbyists. If you are using a different Computer Aided Design (CAD) software, simply try to apply the same principals shown here and everything should work just fine!
Open Fusion 360. Click the arrow to the left of "Origin" in the design tree as show in Figure 2.1 (From here on, all figures are labeled in the bottom right corner of the image). As noted in Figure 2.1 you will want to change your units at this time by clicking the "Units" icon in the design tree. Most 3D printing slicers default to millimeters. I think best in inches so I chose that instead. Note: Slic3r always imports models in millimeters so you will change back to them prior to saving the final model.
Choose a plane to start a sketch on. In my example I chose to sketch on the XY plane because it ends up being the same plane as the build surface of the 3D printer. By choosing the same plane as the build surface you will not need to reorient your model in your slicer. As illustrated in Figure 2.2, select the XY plane, click the drop down on the "Sketch" icon of the toolbar, and select "Create Sketch." Fusion 360 will now show the sketch interface on the XY plane.
Sketch a line and dimension it to be the desired length of your name plate. Again, click the drop down on the "Sketch" icon of the toolbar, but select "Line" (Figure 2.3). Draw a horizontal line through the origin. Click the drop down on the sketch icon of the toolbar and, and select "Sketch Dimension" (Figure 2.3). Click the line you just drew to dimension it (Figure 2.4). In my example, I set the line to be 8 inches long, since that is about as large as I can print on my 3D printer. Remember that the name plate must fit on the 3D printer's build
surface, so make sure your line is at least a bit smaller than the printer's capacity.Select the line and set it to be a construction line by clicking the "Normal/Construction" icon in the sketch palette (Figure 2.5). It will turn into an orange dashed line as shown later in Figure 2.7. This will serve as a guide line to attach and size your font, but it won't show up in your final model. If you would like, center the line on the origin by holding the Ctrl key on your keyboard, selecting the line and the origin, and clicking the "Midpoint" icon in the sketch palette (Figure 2.6).
Insert your base text by clicking the drop down on the "Sketch" toolbar button and selecting "Text" (Figure 2.7). As shown in Figure 2.8, select the start point of the construction line to begin your text there. This will bring up the text edit window.
Select the font style you want to use for the solid base from the drop down (Figure 2.8). Keep in mind that your font must have continuous characters, meaning each individual letter must be made up of only one piece. As an example, in nearly all fonts, the dot on a lowercase "i" will not be connected to the body of the letter. If you were to print this the dot would not be attached to anything. This means, for your solid base text, you DO NOT want use a stencil-like font where the characters are broken up into pieces. I wanted my name plate to make an impact so I chose the "Impact" font and set it to be 1.125 inches tall.
Type the word, phrase, or name you want to be printed solid in the text box using all capital letters to keep the text height consistent. The text will display as solid blue in the graphics window (Figure 2.8).
Click and hold the top of the text editor window to drag it out of the way so that you can see your whole phrase and construction line as shown in Figure 2.9. You can see in Figure 2.9 that my text doesn't reach the end of the construction line. That means it won't be the full 8 inches long like I wanted. Use trial and error to adjust your font height until the last letter lines up with the end of the construction line. As shown inFigure 2.10, 1.28 inches tall worked to remove the space between the last letter and the end of the construction line for my particular combination of requirements.
Finally, click "Stop Sketch" in either location shown in Figure 2.10 to accept and exit your sketch.
At this point, you should be happy with your base phrase, font selection, font size, and orientation.
Step 3: Make a 45° Mid Plane
Before we turn our flat text 3D, we need to make a 45° mid plane so that we can view the thickness of the text from the perspective of the future cut out "illusion."
Click the drop down for the "Construct" toolbar icon and select "Plane at Angle" as shown in Figure 3.1.
Select the green Y axis either in the tree or in the graphics window as shown in Figure 3.2. If the default planes or axes are not visible you can click on the arrow next to "Origin" in the tree as shown in Figure 3.2. Clicking the light bulb next to an item in the tree will toggle its visibility on and off. If the light bulb is yellow the item is visible.
Enter 45° in as the angle of the plane (Figure 3.3). If the plane isn't oriented as shown you may need to enter 135° instead to rotate the plane 90°. TIP: Once the model is printed perhaps you want viewers to see the solid letters, or maybe you prefer the cut out letters to be visible initially. This will dictate which way your plane faces. Think about how people will approach and pass your name plate most often and align your new plane in this direction.
Click "OK" to accept the 45° mid plane when satisfied (Figure 3.3).
Your model should now have your base text and a mid plane.
Step 4: Create the Text You Want to Cut Through the Solid Base
You will now create the text that will eventually be cut through the solid base text.
Select the drop down on the "Sketch" toolbar icon then click "Create Sketch" (Figure 4.1). Select the 45° plane in the graphics window or design tree under the "Construction" group (Figure 4.2). The view will now change to the sketch interface and be oriented normal to the plane you just made. If the view doesn't change, or you move your view by mistake, you can orient it normal to the plane again by clicking "Look At" at the bottom of the window and then selecting the plane (or anything on the plane)(Figure 4.3).
Select the text tool from the sketch toolbar as you did for the base text (Figure 4.3). Since you defined the size of the name plate with the base text you don't need to make a construction line.
Click within the base text where you want the cut out text to begin (Figure 4.4). Drag the text editor window out of the way as you did for the base text.
Select your favorite stencil font and type the text you want to cut through your base text. (Figure 4.5). If you choose not to use a stencil font there is a strong chance there will be detached pieces of text after we cut out our letters. This could cause your illusion to be illegible. Since stencils are designed to hold all the cut out pieces of font together in two dimensions this property certainly helps out when we add our third dimension.
Adjust the font orientation if needed. In my example, the new text was running vertically. To fix this I entered an angle of 270° (Figure 4.5).
Toggle the visibility of Sketch 1 by clicking on the arrow to the left of "Sketches" on the tree (Figure 4.5). Click the light bulb next to Sketch 1 in the tree to hide it (Figures 4.6 and 4.7). If you select Sketch 1 it will turn black as shown in Figure 4.7b. This contrast will help you distinguish your texts from one another.
Adjust the height of the new text (Figure 4.8). In my example I liked an even 1 inch. Keep in mind that the bigger your cutting font is, the more likely it is that it will cut all the way across a character of the solid base. This will create a detached body. If this happens and you print it, it won't be connected to anything. The piece will fall off or even ruin the print entirely! We will be checking for this in Step 9.
Position the text where you want it by selecting it in the graphics window and dragging it into position. I like to center the text horizontally and vertically as shown in Figure 4.8. You don't need to dimension or constrain the sketch because there is a good change it will need to be adjusted in the future.
- Click OK when you are happy with your font selection, position, and size (Figure 4.8).
At this point your model should now have the base text and the text to cut out oriented at 45° as shown in Figure 4.9.
Step 5: Orient the Model Normal to the 45° Plane
In order to help you visually determine how thick to make the solid base text you need to look at the model from the perspective of the cut.
Click the "Look At" tool near the bottom center of the screen as shown in Figure 5.1.
- Select either the 45° text or plane as shown in Figure 5.2.
You should now be looking at your model from the perspective of the cut you will make later. This should look like Figure 5.3.
Step 6: Extrude Your Solid Base Text
You are now ready to make the flat base text into a solid 3D model.
Click on the "Create" toolbar drop down and select "Extrude" (Figure 6.1). Alternatively, you can hold a right click with the mouse and select "Press Pull" as shown in Figure 6.1b.
Ensure you are still looking at the model from the perspective of the future cut. If not go back one step to Step 5.
Select the sketch for your solid base text by clicking on it in the graphics window (Figure 6.2).
In the Extrude menu, set the direction to "One Side" (Figure 6.3). Click and drag the blue arrow in the graphics area to pull the extrusion and add thickness (Figure 6.3). Remember we don't want any gaps showing anywhere in the solid base text. Figure 6.4 shows an example of a gap in the base text which we don't want. Figure 6.5 illustrates a nice solid, gap-less, base text. You want to extrude slightly past when the gaps disappear to have some wiggle room for deviations in your 3D print. TIP: To better see any gaps you may want to toggle the visibility of the sketch for the cutting text (Sketch 2) by clicking the light bulb icon next to it in the design tree.
- Click OK when you have a nice solid base with no gaps.
Your model should now have a 3D body for the base text with the flat text you will be cutting out in the next step, as shown in Figure 6.6.
Step 7: Cut It Out
It is now time to cut the illusion text out of the solid body text.
Click on the "Create" toolbar drop down and select "Extrude" or, as shown in Figure 7.1, you can hold a right click with the mouse and select "Press Pull".
Select the text you will cut out in the graphics window (Figure 7.2).
In the "Extrude" window, click the drop down next to "Direction" and select "Symmetric" (Figure 7.2). This will cause the extrusion to have equal thickness on the front and back of your text.
In the "Extrude" window, click the drop down next to "Operation" and select "Cut" since you are removing this text from the solid base (Figure 7.3).
Rotate the model so you can view the depth of the cut (Figure 7.4). To do so, click and hold your middle mouse button (or wheel) and drag to rotate the model.
Drag the blue arrow in the graphics window to add depth to the cut. Pull the cut until it passes completely through the front and back of the solid text as shown in Figure 7.5. Click OK when you are done to complete the cut (Figure 7.5).
Use the "Look At" tool again to look directly at the cut by selecting the 45° plane (Figure 7.7). Make sure the cut is all the way through and you are happy with the placement. Pay attention to how much of the solid text is visible to the left and right of the cut. Since the cut text was placed prior to the base having thickness it may not look centered. You can go back to the sketch for the cut (Sketch 2) and adjust the placement. To edit the sketch, double click it in the design tree.
Your model should now look similar to Figures 7.6 and 7.7.
Step 8: Connect the Base Text Together
Right now, all your letters are floating in space. That isn't very practical for a name plate. We need to connect the letters together with a thin strip of material at the base (or anywhere else if you are feeling creative). This could have been done in the same sketch as the base font. However, you may need to make adjustments toward the end of this step and keeping the connector as a separate sketch can simplify some situations.
Start a sketch on the same plane as your base text. You should now be looking directly at your solid text (Figure 8.1).
Use the "2-Point Rectangle" tool in the Sketch toolbar drop down and under the "Rectangle" tool to draw the strip that will connect the letters (Figure 8.1). As seen in Figures8.2 and 8.3, I put the first point of the rectangle on the outermost edge of the first letter of the base. The second corner was placed on the bottom center tangent point of the "S" and the end of "INSTRUCTABLES" as illustrated in Figures8.4 and 8.5. By connecting the rectangle like this it visually blends in with the letters more than if the rectangle extended past them. Figure 8.4 shows the layout of my rectangle. TIP: If your first letter is round on the bottom like a "C" or a "J" you might want to snap your rectangle to the bottom tangent point of the character just like I did for the "S". Also note that, because I chose the "Impact" font, certain characters are taller than others as is the case with the "S." Therefore, you want the bottom of your rectangle to be in line or below the letter that sticks down the most so that the name plate will sit level.
Create the dimensions and relations you want for your connecting strip. You can get to the dimensioning tool as we did in Step 2 part 3, or as shown in Figure 8.6, right click with your mouse and hover over "Sketch" at the bottom of the fly-out menu. When the menu changes, click on "Sketch Dimension" as shown in Figure 8.7. Click the top and bottom of your rectangle to create a dimension between the two. I chose to make mine 0.05 inches tall so that it has enough strength to hold the letters together well, but also doesn't look intrusive (Figure 8.8). If you would like, you can fully dimension your rectangle, or use geometric constraints from the Sketch Palette on the right of the screen (Figure 8.8).
Once you are satisfied with your connecting rectangle click the "Stop Sketch" button to accept your sketch (Figure 8.9).
Bring up the Extrusion tool by right clicking and selecting "Press Pull" as shown in Figure 8.10. The last operation we extruded was a cut, so you need to change this. In the Extrusion window click the drop down next to "Operation" and select "Join" since you are joining our rectangle with the bodies of the letters (Figure 8.11). You want your rectangle to line up with the front and back faces of the solid text. Since you started the sketch from the same plane as the back face of the text, you can select "To" under the "Extents" drop down to allow the extrusion to terminate at the front face (Figure 8.12). Click anywhere on the front face of the base text to tell Fusion 360 the extrusion will extend "to" there (Figure 8.12).
Click "OK" when your rectangle extrusion settings are correct (Figure 8.12).
Your model is almost finished!
Step 9: Hide the Bodies...
This is the trickiest step of the whole process and may require some extra brain power and patience. Unfortunately, with the infinite combinations of words, fonts, and sizes there isn't a way to make sure your particular name plate is one piece. You must analyze your model for disconnected bodies and remove/fix them.
Click the arrow next to Bodies in the design tree to show all the individual bodies (Figure 9.1). Each body that shows up here is not attached to any other body. Select a body in the tree by clicking it to highlight it in blue in the graphics area (Figure 9.1).
Carefully check your whole model. You don't want any significant portions of your letters to be separate bodies. Those parts will fall off of your print and could render your text illegible. Click through the different individual bodies in the tree and look for large pieces as shown in Figures 9.1 and 9.2. If you have large individual bodies see the tip below. You also want to check for places where the connections to letters are small. Examples of thin and missing connections are shown in Figure 9.2. You will be printing with plastic so there must be enough of a connection to support the pieces of the letter it connects. This is tedious to sort out as you may have a thin connection (or no connection) on one face of your text, but a nice solid connection on the other. As long as there is a thick connection somewhere to the rest of the letter, it should print fine!
Hold the Ctrl key on your keyboard and select all of the bodies you wish to remove in the design tree as illustrated in Figure 9.2. Right click on one of the selected bodies in the tree and then select "Remove" (Figure 9.3). Note: Do not use the "Delete" Option. Deleting removes the entire geometry that created the body and will likely destroy your model.
Fix any issues. After removing all of the disconnected bodies, use the "Look At" tool to view your model from the front face of the solid text and then from the 45° plane. You want to check that all the profiles of the letters still look correct now that some pieces are gone. If you have problems see the tip below.
Your model should now be finished as shown in Figure 9.4. You should also now have a basic understanding of modeling in Fusion 260. Well done!
TIP: Fixing Problems
- If you have large chunks of letters missing: Rotate your model around and look for places where the cut out text is cutting all the way across a solid letter. Remember you also want to carefully check for places where there are small connections on the main body so you can fix those as well.
- Edit your text sketches. Double click on them in the design tree to edit their respective sketches. It may be helpful to rotate the model when editing your sketches so that you can get a better visual of of the changes affect the cut.
- Some things to try in the sketch for your solid base text (Sketch 1) are:
- If you have room on your 3D printer you can make your solid base text bigger.
- Choose a thicker font.
- Make the font bold.
- Extrude the sketch out further.
- Some things to try for the cut out text (Sketch 2) are:
- Move the text away from the problem area.
- Make your cutting text smaller.
- Find a thinner stencil font.
- Some things to try with your connecting rectangle are:
- Make it taller.
- Add another (maybe at the top of the solid font or like a "strikeout"). This make the illusion less magical in my opinion.
- Change the angle of the plane to be more acute with respect to the base plane. The cut out font won't extend as far across the base with angles less than 45°. Doing this means you will also need to make your base extrusion thicker to hide the shallower cut.
- Every time you change your sketches you will want to redo this entire step (Step 9). Until you have no more disconnected bodies, or you only have small bodies with no effect such as those in this example.
Step 10: Save
Your model should be finished at this point. It is time to save it (although it is good practice to continually save along the way).
Remember earlier when I said most Slicers use millimeters as their default units? Slic3r only uses millimeters (unless you want to scale your inch import by 2540%), so now is the time to change your units. Simply click the "Units" item in the design tree as shown in Figure 10.1. Next select millimeters from the drop down in the menu as shown in Figure 10.2. Lastly click "OK" as shown in Figure 10.3. The model will stay the same physical size with converted units.
Save your part as a CAD file. This will come in handy if you have to modify things after printing. As shown in Figure 10.4 click the "File" drop down on the top toolbar and select "Save As." Save your file to the built in cloud or your favorite spot on the computer. As seen in Figure 10.5 I saved to the cloud. Fancy.
You now need to save a ".stl" file. STL's are stereo-lithography files (made up of triangles) and just happen to be what the 3D printing world decided to standardize as the file type for slicing software. Select the "File" drop down again and click the 3D Print option (Figure 10.6). Click the arrow next to "Refinement Options" in the 3D print menu to bring up the STL settings (Figure 10.7). Also click the arrow next to "Output." Make sure that the box next to "Send to 3D Print Utility" is not checked (Figure 10.8). While it is deselected we will be able to save our STL so we can open it in a slicer.
Check the box next to "Preview Mesh." The mesh wire-frame will display so that we can visually verify the STL resolution is high enough for a good print. As you can see in Figure 10.8, I went with the default settings for "Medium" refinement. As noted in Figure 10.9, Pay particular attention to the density of the mesh on curved surfaces. You will want enough triangles on a curve that it will actually appear to be a curve once printed, but you don't need so many that your mesh looks like it's solid black around a curve.
- Accept your STL changes and save your STL file by selecting "OK" (Figure 10.9). Save the STL to a location where it can be opened by your slicing software (Figure 10.10).
You are now finished with your model in Fusion 360.
TIP: Fix slow Slicing.
If you find your slicer is running too slowly later, you can return and save an STL again with relaxed deviation settings. Because text can have lots of round edges, which take a lot of triangles to smooth out, your STL file size can be huge! These large files take a long time for slicers to process. The smaller the file size of your STL, the faster the slicer will run. To save a smaller file return to the 3D print refinement settings as detailed in Figures 10.6, 10.7, and 10.8. Adjust the deviation sliders to make your mesh more coarse. If you adjust the settings to be too coarse, however, your model will look polygonized. For parts of a more artistic nature where fit isn't an issue, such as this illusion, you can use a large deviation without noticing changes to your finished part. After all, what is a few thousandths among friends?
Step 11: Slice
Now it's time to convert your STL model into something a 3D printer can interpret. Slicing software will accomplish this by "slicing" your STL file into layers. Each layer will be filled with paths for your printer to follow. These paths will be saved as gcode, which is a text language that your printer can read.
Open your slicing software. I am using Slic3r simply because I spent the most time tweaking my print settings in it.
Load your model by clicking the "Add" button (Figure 11.1). Navigate to your STL file location and click "Open" (Figure 11.2).
Position the model on the plater (build surface) to your liking by clicking the model and dragging it (Figure 11.3). I like to print on the back surface of the text so that the perimeters of the letters are drawn smoothly by the printer (Figure 11.3). To rotate your part, right click on the part, select rotate, and type the desired angle of rotation for the corresponding axis of rotation (X is red, Y is green, Z is blue). If you modeled the base text on the XY plane, as done in this example with Fusion 360, your part will already be facing the correct direction.TIP: If you print with the letters standing how they are intended to sit on your desk the perimeters of the letters will be layered and not look as crisp. Printing on the back also helps avoid the need for extra support material. Since our cut was made at 45° each new layer of the cut has enough material below it to stick and is typically printable. If we were to print the letters standing up, characters like "T" would need support in order to print the overhangs accurately. TIP 2: To avoid having to guess the angle of rotation for your model in a slicer, model it in Fusion 360 in the orientation you want it to print. Most printers build platforms correspond to the XY plane.
Adjust your print settings. In this example PLA filament settings are shown in Figures 11.4 through 11.9. Since this print is ornamental, I used a 40% infill to save plastic and time (Figure 11.5). As seen in the Figure 11.6, I chose to print a 5mm brim to increase the surface area of the print on the heated bed. A wide print like this tends to warp and detach from the print surface so a brim is cheap insurance against a failed print. This print ended up sticking very well and I wished I didn't used a brim because it was frustrating to remove it from between letters.
You must choose whether you want to print support material at this point (Figure 11.7). There will likely be overhangs which have no underlying surface on which to print (detailed later in Figures 11.13 through 11.17). If you have this condition and don't print support there will nothing for the plastic to stick to on these layers. This will ruin your print or, at best, create flying-spaghetti-monster-like strands you will need to grind off. However, unless you have soluble support or really good model material support settings, there will probably be some picking and grinding to remove the supports anyway. As seen in my settings (Figure 11.7), I chose to print support with a threshold of 0° which allows Slic3r to decide when and where supports are needed. Slic3r did a good job with the support (this time anyway) as you will see later. I have printed the illusion acceptably without support (the example of my name had no support), but I did have to grind some "spaghetti" from the bottom of overhangs.
Wait for Slic3r to finish computing (if auto-compute turned off, click "Export to G-code and save in order to compute) and click on the "Preview" tab at the bottom of the window (Figure 11.10). You will now see your print paths modeled in 3D. Figure 11.11 shows what a pillar of support looks like. The skirt and brim are detailed in Figure 11.12. You can use the slider on the right side of the graphics area to move through the layers of print paths (Figure 11.13). Figures 11.13 through 11.17 highlight where and why support material was needed. For this print the case shown in Figure 11.7 would not have printed without support because it is so close to the last layer. Since the small bit of model shown there is detached from the rest of the body, the remaining few layers will have nothing to bridge to.
If you don't like what you see after investigating your paths, go back and change your print settings, or load your CAD model in Fusion 360 and adjust your model.
When you are satisfied with the print paths, export your file to gcode by clicking the "Export to G-code" button shown in Figure 11.18. Pick where you want to save your file and click "Save" (Figure 11.18).
Now you should finally be ready to load the file onto your printer!
Step 12: Print
It is time to take your illusion from the digital world to the real world.
Load your gcode file onto your printer. I put the file on an SD card and run the printer stand alone. This printer is on an large uninterruptible power supply so running stand alone allows the print continue for a few hours if the power goes out.
Make sure your printer is calibrated. Every once in a while it is good to check that the leveling and Z axis zero height are still proper. It is especially important on a wide part like this so that the first layer has excellent adherence to the bed. In the first time-lapse GIF I am changing from ABS to PLA filament and calibrating the Z zero height.
Heat the build surface. On this printer the center of the build surface reaches temperature before the outer regions, so I let the heat soak in the bed a while to help the first layer of plastic stick. I use an infrared thermometer to check when the outer edges of the build surface are up to the set temperature.
Print. It is a good idea to watch the first layer go down to make sure there aren't clearance issues and everything is sticking.
Wait. The second GIF of this step shows the printer moving about for 3 hours as it prints. TIP: Hobby grade printers aren't always refined machines. If you value your house don't leave your printer running while you are not home and keep a fire extinguisher handy.
Admire your finished print as it magically sits on the printer (Figures 12.1 and 12.2). There was nothing on the build plate before the print. Now there is an illusion. Was printing itself the illusion? Is this an illusion within an illusion?
- Pop your print off the build surface. I highly recommend plastic razorblades if you print on a Polyetherimide (PEI) build surface as shown in Figure 12.3.
Full disclosure - this was the 3rd print attempt. Figure 12.4 proves I am not trapped in "limbo." If a print comes out perfectly first try with this printer, I must be in a dream. You can see from the picture the previous two prints failed a little past 50%.
Step 13: Do the Pick, Pluck, Sand, and Grind
This is the worst part (unless you have soluble support).
Get out your favorite picking, plucking, sanding, and grinding tools. Gloves and safety glasses are a good idea as well.
Pick, pluck, and grind away from yourself. I have often thought "I might stab myself while trying to pick off this piece of support." I then proceed to stab myself with the pick. Don't do that.
Grind with low RPMs. I bought a flexible shaft rotary grinder just for cleaning up prints because it can run very slowly with high torque. This will keep the plastic from melting while you grind resulting in nice clean plastic chips. These aren't food chips. Don't eat them.
Dream about soluble support. Figures 13.1 and 13.2 show increasing levels of part smoothness where I stopped to wonder how I can get a machine of my own with dual heads and soluble support.
Make your final touch ups. I like to remove the last bit of lip left over from the 5mm brim with a deburring tool. I decided to sand the printing marks off the top face of the print. I rough sanded with 80 grit and finished with 200 grit as shown in Figure 13.3. TIP: I forgot I was using PLA when sanding. Therefore I couldn't use acetone to melt the matte surface back to shiny. I suggest you don't sand if using PLA, as sanding makes the cut out text surfaces stand out due to the different color. You can see this by comparing Figure 13.2 and Figure 13.4.
Can you believe your eyes? You are done!
Step 14: Amaze Your Collegues and Friends!
Put your hard work on display! You earned it for making your way though this entire Instructable!
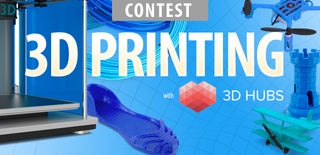
Participated in the
3D Printing Contest 2016