Introduction: Design and Prototyping of the Skelequill Start to Finish
Sometimes there's just nothing out there that suits your particular needs. Maybe those other things are too heavy, too expensive, too small, too big, etc. They just don't fit how you want. Well, the best thing to do in that situation is to make your own thing! But where in the heck do you start?
This guide is roughly the process I went through (good and bad) to design and prototype the Skelequill pen concept. The idea is to capture the overall process from start to finish, all hiccups included. Hopefully it will help give some insight into the trials, tribulations and rewards of the design process. To give some context, lets start with a video of the final solution:
Step 1: The Problem
I carry around a pocket note book with me everywhere so I can jot down important notes for work or any nifty ideas I come up with. The notebook is made by moleskin and has good grid paper that's fantastic for quick sketches and notes throughout the day.
However the pen I use to take notes is not very convenient for a lot of reasons:
- It isn't compact due to the way it clips to the notebook.
- If the pen is attached to the front of the notebook it will protrude into my leg, make my pocket look strange, get knocked off or otherwise cause some sort of problem.
- Since it's so obvious, people steal the pen (I'm just as guilty. I am pretty sure I have a cup of work pens kicking around that I should return to work, but never will).
So what am I to do?
Step 2: Identifying What You Want and Looking for Some Solutions
Well, the first thing to do is figure out what I want out of the Pen. Then we should see if anyone has done anything like it!
So what exactly do I want out of this new Pen? Well it needs to be:
- Compact
- Comfortable
- Stays attached to my notebook
- Easily recognizable as not anyone else's property.
- Nifty!
I start looking around for what others have done to solve this. The Internet is a great place to find solutions and get inspiration for many things. I found a whole slew of interesting pens that solved many but not all of my needs. There were telescoping pens, flat pens, folding pens and all sorts of other fantastic designs.
However they were all either too clunky, heavy, expensive, plain looking, hard to find, uncomfortable-looking or just plain didn't look like my style (in case you are wondering I am a nightmare to Christmas shop for).
So if nothing out there suits my needs, I guess I'll need to design something myself!
Time to make design something!
Step 3: Creating the Initial Concept Through Iterative Sketching
The blank page. The most intimidating part of the entire process. The easiest thing to do is just start sketching. Get creative with how to solve the needs that you want, but you don't need to focus on solving them all at once at first.
This is where the really broad strokes of creativity come into play. I try not to spend more than 15 min drawing each iteration of a solution that I have for an idea. Otherwise I tend to get narrow sighted and may lose out on a more promising solution. The process looks like this overall:
- Start sketching some part of the project out. It's best to start with overall shape/form first and nail down details later.
- Spend 15 minutes minute or so trying to flesh out the idea.
- Start another sketch to get more concept ideas or start working on smaller details of the overall concept.
The point is to let your all your ideas make it onto the page. You can always cull them later!
For this problem I came up with a fair number of compact pen ideas. As I was sketching, I was thinking about utilizing the flexible properties of a cheap ballpoint pen cartridge. During another sketch I thought of a very complicated double action mechanism that made the pen go from a flat state to a equilateral triangle prism by pressing on the sides. The last main idea was to have the pen unfold so that it was curved.
All these concepts ended up making me settle on the idea of a folding quill. There was something always alluring about quills. They seamed elegant, though very cumbersome and impractical. I felt it was time to try and take this archaic beauty into the new age.
This stage is all about letting your imagination run loose.
Step 4: Start Making Quick and Dirty Prototypes
The next stage is to figure out whether your imagined idea makes sense in reality. The easiest way to do this is to built quick and dirty prototypes out of whatever you have laying around. The key here is to quickly test the parameters of your design. In this case, I was really concerned about the following:
- Basic function
- General shape
- Size
- Immediate obstacles to overcome
So what did I have lying around? Paper. Paper is great for prototypes!
I cut out a few pages and started doing some folds. I would fold up some paper, see how it fit my requirements, fold again and continue iterating like that until I had something that I was happy with. This is a matter of just trying to get a 3D sense of what your concept was.
In the case of the Pen, this was my line of thought.
I tried various different types of origami folds and eventually came up with what I figured was a simple but effective folding action. In order to get a feel for the mechanism, I just taped a pen cartridge to the paper. This gave me a good feeling for the general size of the pen and how it would feel in the hand. The mechanism happened to fit into my size and shape requirements, so things were starting to come together.
It really doesn't look like much at this stage, but this stage really helps cement your idea as a real thing. From here on in, I had a very good idea of how to design the rest of the Pen. Next we get on to the details!
Step 5: Refine Your Sketches and Build a Better Prototype!
In the last step we got a very good idea for the general design parameters. Now it's time to start chiseling away the bulky broad idea and refine it into a final concept.
This step requires much more thought and detail than the previous steps. You are no longer in the imaginative part of the creative process. You are now engulfed in the practicality of the core functionality and aesthetics of the project. It's time to be pragmatic.
The key to this step is to work out all the fine details. In the case of the pen I needed to answer the following questions:
- How many pieces was the pen going to be?
- How exactly was it going to fold? What kind of hinges did I want to use?
- Could I use the flexibility of materials like I thought I could?
The first two points could easily be solved by better sketches. The third, well, the only way to be absolutely sure is to build another prototype based on the refined sketches. I needed something stronger than paper, so I built one out of cardboard. In doing so I also made some discoveries.
- The folding method I originally envisioned during the paper prototype stage could be reversed with a more desirable action.
- The mechanism could have a over-center function keeping the shape of the pen as desired.
After this stage, the prototype was completely functional. It will work. Now the focus will shift to doing up the final design and adding in some aesthetics!
Step 6: Distill the Design
Now that the core functionality is done, it's time to distill the design. Chisel, tone and refine. Make it repeatable. Add real tolerances. That's what this stage is about.
I booted up my 3D cad software and started putting my sketches into the software. I start with 2D layout sketches and then produce the 3D model from those. It takes a bit of time to do the layout sketches, but it's worth it if you ever need to look back on or change the design. Some of the key parameters I had to define were:
- Size of the pen catridge to use
- Exact location and angles of operation for the hinges
- Spacing and orientation of the nib/feathers
- Material
At this stage I had envisioned the pen being made of very thin sheet metal with soldered on hinges. Later I would find out I couldn't make it that way due to time constraints (all part of the fun!).
I find that it's best to use general tolerences at first, only tightening them when really required. I used .01" all around just to get a reasonable baseline, but I knew I might to do some adjusting yet depending on the material.
Finally, we're ready to get our first real prototype made!
Step 7: Gathering Materials and Tools!
It turns out to build a prototype, you need materials. For this project I wanted a thin metal that would be easy to cut, but wouldn't break the bank. For small projects like this, hobby shops and hardware stores really work wonders.
With that in mind, I went on my way. At my local hobby shop I found a brass tube that my selected pen cartridge fits into very nicely. My local hardware store had some brass kicker plates that looked like they would work well for the feather sections of the pen.
Since all I needed for this project was a soldering Iron and I already had one, I was good to go! If you don't have a specific tool, sometimes you can improvise. The internet is great for this.
On to the first cut!
Step 8: First Real Prototype
Now that I had my materials, I realized I had to make some quick changes to the model. Good thing we spent time on those layout sketches! I changed the thickness and tolerances of a few sections and was good to go.
I decided to utilize a local business nearby that does water jet cutting to cut my parts out of the brass kick plate. I gave them my cad files and materials and I had my first cuts done in a few days.
The parts looked fantastic so I started bending and...
UH OH... THE BRASS KICK PLATE ISN'T ACTUALLY MADE OF BRASS.
The darn thing was just made of brass plated aluminum. for those that don't know, depending on the grade of aluminum it doesn't generally like to be bent. it usually forms stress cracks and fails. Also I am now trying to braze brass to aluminum, which can be done, but not easily.
Well shoot...I guess I have to find some brass plate.
so I went back to my hobby store and hardware store. Both options turned up bunk.
... How am I going to make this thing?
Step 9: Alternative Manufacturing Methods
I needed to find another way to get this pen made, but I was running out of options and time.
Luckily a friend of mine has an old reworked thingomatic 3d printer that he was willing to let me print on. I just needed to rework my model to be printable on his machine.
His machine's build area was significantly smaller than my part size. I had to shrink the model down to fit in the printable area. His machine was also not nearly as accurate as a water jet cutter so I had to up my tolerances to .5 mm all around. upside was that I could print the hinges into the part and print the parts relatively quickly.
Bah, why won't it print?
We were up until 4 am one night printing and just couldn't get it to print nicely enough to make a functioning model. It was soo close. just not close enough.
At this point I was running out of options. I had to get this thing done. But how?
hmm. ... maybe shapeways could do it.... Yeah and I might be able to print it all in one go if there machines are accurate enough and i might still be able to make the deadline.
Step 10: Utilizing Shapeways
I adjusted the model to print in one piece, I converted it to an stl and sent it off to shapeways.
I really should have looked at the lead times for shapeways. According to their lead times my part was barely going to make it in time for the deadline.
so I waited, and waited. checked the progress twice a day. things were going as per expected and then production took 2 days longer than allowable for me according to the shipping eta's.
QUADRUPLE CRAP!
The part didn't look like it was going to arrive in time!
what the hell do I do now? ( so much for third times a charm)
Step 11: Getting Desperate (hey It Happens)
At this point I am all out of luck. I don't know how I can get the project done. I'm toast. kaput. cest fini.
so what do I do now?
hope for the best that shapeways pulls through?
Try and Jerry rig what I have?
stick with my crummy cardboard prototype?
one day at work I over herd that another company we deal with often had recently got a makerbot replicator.
This could be my last chance. maybe they will run the part for me!
I phoned them up and they were willing to lend a helping hand.
YES!
Step 12: Moment of Truth
now let's hope it can print it!
first attempt...
nozzle clog right off the bat.
Second attempt...
nozzle clog after the raft just finished.
Third try...
SUCCESS! A little stringy in some spots but still a success!
so I printed a second. just in case
All I needed to do was drill out the hinges to fit the pen cartridge. then lastly drill out the hinges to fit some 1.75mm filament for a pin. oh yes... and remove a copious amount of raft material as well as supports.
Step 13: Testing the Functionality
The folding action turned out just how I wanted it too.
It works well as a pen but it is a little small due to me trying to fit it on a reworked thingomatic. i will probably lengthen it in a future revision.
The assembly took less than 10 min.
Over all I am happy with the design and can't wait to revise it further despite all the hardships I encountered.
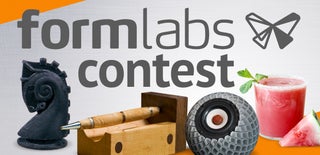
Participated in the
Formlabs Contest
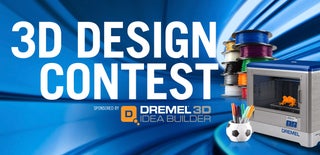
Participated in the
3D Design Contest