Introduction: Dragon Skin and Valyrian Steel Ring (Inspired by Game of Thrones)
I wanted to make a Game of Thrones themed ring with some cool new materials and I took the opportunity to film the process in my new workshop!
New workshop, new series of Game of Thrones, new materials ... living the dream!
The materials I used were...
1. Juma Golden Dragon by Elforyn - this is a cool acrylic style material that looks like snake skin/dragon scales. It machines like a dream and when it's polished it looks amazing! You can find it in the link below. https://www.elforyn.de/en/juma/?p=1
2. Stainless Damascus steel (Blue Tongue pattern by Damasteel labs). This is a very unique pattern and I imagine that's what "Valyrian Steel" would look like!
Valyrian steel doesn't exist in real life but Damasteel make some damn cool materials and it made sense to use up this core I had laying around from an old project.
Want To See More Of My Work?
If you enjoyed this Instructable then please subscribe to my Youtube channel and watch more of my ring making videos in this playlist (there are 23 videos in there for your viewing pleasure!):
Step 1: Cutting Down the Dragon
So this ring started life as a 25mm wide round bar of Juma Golden Dragon. It's a pretty cool material and I was super keen to make a ring with it - however at 60cm long it was a bit to big to fit on my lathe!
To sort that out I cut a piece on the bandsaw (it was about 5cm long).
Step 2: Drilling a Hole
I had a ring blank made with the Damascus steel from Damasteel left over from an old project and I wanted this to form the inside/core of the ring.
The next step was to make a hole in the dragon skin material that was a tight fit for the Damascus blank. To do this I mounted my 5cm piece of round material into my chuck jaws and used a few drill bits to drill a hole with the metal lathe.
I used 5mm, 10mm, 15mm and 20mm HSS drill bits.
Step 3: The Boring Bit
With my hole drilled I just needed to clean up the face of the Juma (probably should have done that first). I did that quickly with a cutting tool just to make sure the face was flat and even.
Next I used a boring tool to make the hole just slightly bigger and kept checking it until the Damascus core could squeeze into it. I needed it to be a tight fit and thankfully I got it right first time (there's nothing worse than over cooking the hole and having to start over!).
Step 4: Parting Off
This step is fairly self explanatory ... I used a parting tool to cut about 9mm off the blank I just drilled.
I had both parts of my ring ready to glue up!
Step 5: Gluing and Squishing
To glue both pieces together I used a two part epoxy resin adhesive (Araldite) and a tapered wooden thing I turned on y wood lathe.
I lathered the outside of the Damascus and used the taper to squish both pieces together.
Step 6: Cleaning Up the Edges
With both pieces glued up and the epoxy cured I used a disk sander (a DIY version I made for my wood lathe) to sand the edges down flat.
The ring was finally taking shape!
Step 7: Polishing Round 1
Time for the fun bit: making the ring all shiny!
Polishing the inside of the ring:
To polish the inisde of the ring I mounted it in Pin Jaws on my wood lathe and used a few grits of progressively finer sand papers to finish the surface and round over/taper the edges.
This isn't the safest thing to do - I wouldn't advise doing it at home but I had the lathe running slow and maintained concentration to avoid a finger injury.
Grits used: 240, 400, 600, 800, 1200, 2000
Polishing the outside:
Polishing the outside was pretty eas as Juma is a very nice material to work with. I mounted the ring on to a wooden spindle on my wood lathe and wet sanded the outside through a series of grits. When I'd worked up to the finest grit I used a burnishing cream from Chestnut Products to bring out a nice shine.
Grits used: 240, 400, 600, 800, 1200, 2000 + Chestnut burnishing cream
Polishing inside (again)
Before I could etch my Damascus steel to bring out that cool pattern I used a felt buffing wheel on my rotary tool to polish the newly sanded inside of the ring. I just used a brown polishing compound at this stage.
Step 8: Etching
To bring the cool pattern of the Damascus steel to life I used Ferric Chloride to etch the ring.
I cleaned all of the polishing compound of the ring, put in in an ultrasonic cleaner for 4 mins and then submerged it in the acid for about 45 minutes.
When the time was up I neutralised the acid with baking soda.
Step 9: Polishing Round 2
With the etch done and those patterns popping I went on to the final polish.
For the inside of the ring I used my rotary tool and worked through Brown, Green and White compounds (cleaning the ring in between each one and using different polishing wheels).
I gave the outside a final buffing with a Blue compound on my bench polisher.
The end result was insanely shiny!
Step 10: Fin
What do you think of this ring? I love the materials and the finish but I feel like theres something missing from the design (who knows maybe it's just my self critical artists eye!).
Anyway ...
If you enjoyed this video then please subscribe to my channel and watch more of my ring making videos in this playlist:
https://www.youtube.com/playlist?list=PLLAA74zbZzz...
See you in the next one!
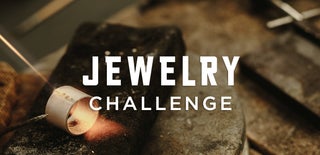
Participated in the
Jewelry Challenge