Introduction: Drop-down Crafts Table W/ Storage (No Hinges and No Leg Supports Needed)
I recently had a request of a drop down table with storage. The client also wanted it to look like art hanging on the wall when it folded up, making the table appearance unrecognizable. The client will be doing a painting on the face of it, that's why it still appears unfinished
I could've made this easier but I wanted to do something unique. There are a ton of drop-down tables, but all of them have unsightly legs that need to be folded out. These are usually covered up by additional doors and legs get in the way at times when sitting at them.
So I went at it with a different approach. I wanted it to lower and go back up with ease, similar to a murphy bed. The client wants this to have frequent use and it needed to be able to be used by children.
It came out better than I imagined. It gets use as a standing desk (I'm using it as that now actually), grocery drop off, homework desk, reading area, and much more.
I started with getting supplies. This needed to be cheaper than the ones you can simply buy online (about $100-150), even though this is 4 times bigger and provides a ton more storage.
I picked up a panel-less solid wood door at a local Habitat for Humanity for $10. I figured this was way easier and cheaper than building a table top myself and it would definitely be flat. If I had to do it again I would not! This is strictly due to the fact that after about an inch from the bottom and top of the door, it is no longer solid, it is packed with solid wood chunks. You will see why that was an issue soon.
Then I went to the local home improvement store and picked up the cheapest cabinet grade plywood. All products required in this build are as follows.
- 1 x Door ($10)
- 1 x 4x8 cabinet grade plywood ($30)
- 1 x 16 gauge structural strap ($4)
- 1 x 2 pack of table leg brace ($7 Amazon)
- 2 x gas struts ($18 eBay)
- 1 x 1/2 in metal rod ($3)
- 1x 12 pack of 1/4 in. Strap Toggles ($8)
- 2 x 6 pack of 1/4 in. washers 1 1/4 in. diameter ($2.50)
Total Cost = About $82.50
Step 1: Basic Prep
I started by sanding and sealing the door. Then I cut my plywood to size using a table saw. I wanted this drop down to have storage so I built the basic cabinet box 8" deep. Since my door was 80"x32" I wanted the opening to be 80 1/4" by 32 1/4" to allow 1/8" gap around the edges. I am using a french cleat system to easily get the cabinet on an off the wall during construction and moving homes.
- 1 x 5"x80 1/4" board (1 side cut at 45)
- 2 x 8"x32 1/4" boards
- 2 x 8"x81 3/4" boards
- 1 x Smooth 80"x32"x1 3/4" table top
Step 2: Layout, Pre-drill & Attach
I then laid out the pieces on the floor, as I do not have a big enough workbench. I wanted to make sure the best grain was visible from the outside of the cabinet. Seeing how this was the lowest quality cabinet-grade plywood, it had a lot of warping in it. Don't worry though, as the top and bottom back boards as well as the shelves added later will fix this issue. Using a Kreg Jig borrowed from a friend (Thanks Josh) I put a bunch of pocket holes in the sides and back boards. No pocket holes were drilled into the top or bottom cards. Then I assembled everything ensuring a flush edge at all times. That took all the warping out of the boards.
Step 3: Table Pivot Point
As mentioned there are no hinges or legs supporting the table. It pivots on a 1/2" rod going through the sides of the cabinet wall and into each side of the door/table about 15". I used a door hardware install kit with a 1/2" auger bit and a 1/2" drill stop to fill the void in the hardware install kit. DO NOT DO IT THIS WAY! I later ran to Harbor Freight and picked up a dowel jig for a few bucks, this is the way to go. It will guide the auger better than a drill stop and hardware install kit, plus its about $20 bucks cheaper. Also the 3 pack auger bits at Harbor Freight are cheaper than a single bit at "the other stores." That's also the way to go!
Since my cabinet is 8" deep and had a board on the backside I drilled the hole 6 7/8" from the end and centered. This allowed for the pivoting action without hitting the bottom or back of the cabinet.
Step 4: Cabinet Pivot Point
After getting the table done I need to drill holes in the sides of the cabinet. I started by putting the cabinet on top of the door/table. This allowed me to ensure the face of the cabinet would be the same as the face of the table bottom when in the folded up position. Then I used spacers to ensure all 4 sides had an even gap. Next I marked off where to drill the hole. This needs to have very little to no error, so I went from underneath and used the door to measure over 6 7/8 in. Afterwards I used a gauge to measure the exact thickness of the table/door on each side and drilled holes at half that thickness on each side respectfully. Then I hammered the 1/2" rod in and checked that everything fit and had clearance.
Step 5: Reinforcing the Cabinet
I found these 16 gauge structural supports that conveniently have a 1/2" hole on each side. So I used a rotary tool and cut the section I needed. Sparks go flying, use PPE! Then I fed the rod through the hole and clamped the plate in place so I could trace it. I traced it using a razor blade not a pencil. This prevented tear out when I came back a chiseled the section out. I needed to have this steel reinforcement lay flay to maintain proper clearance of the table/door.
Step 6: Installing Gas Struts
You have 2 options. Skip this step or don't use a door as a table top. If you do this step It must be going in to solid wood and you must use a strut system that has a multi-contact ball instead of the single ball bolt I bought. I tried reinforcing it with a wooden dowel and T-nuts I had to special order because the bolt was metric. Nonetheless the table part failed. Not the cabinet part which used a 2 contact solution. Also measure twice, you can see my mistake there. If you got nice solid surface all you have to do is chisel out the space for the ball and strut motion. It's pretty simple.
Step 7: Shelf Layout
The whole reason for this thing is so it has shelves right?
I started by supporting the table on an elevated surface and then swung the cabinet up so the table and cabinet were perfectly perpendicular. Then using masking tape I scored a line at the exact point where the top of the table was exactly 90 degrees. This would become the bottom of the bottom shelf.
While I was at it I also installed these table leg brackets. These fit in the 1/8" gap and allow me to lock the table in place once it's in its down position.
Step 8: Top Shelf Layout
Then I marked where the top shelf would go to allow clearance of the gas strut.
Step 9: Assemble Shelves
After careful measuring I cut pieces for shelves. I cut them 6" wide to allow for the door to sit into the cabinet. The top 2 torsion blocks were cut 5 1/4" to sit flush with the face of the other shelves but also but up against the back board and later the wall board. These were measured and were designed around the gas struts being used. If you don't use struts simply fasten a board all the way across at the line created earlier. Either way here's what I cut.
- 1 x 6"x80 1/4" board
- 2 x 5 1/4"x12 1/4" boards
- 2 x 6"x11 1/2" boards
- 1 x 6"x10 3/4" board
- 1 x 6"x77" board
Then I predrilled some pocket holes and some countersunk holes. Afterwards I attached the shelves to the cabinet. Then using 3/8 flat wood plugs and wood filler I plugged all holes except the pocket holes. After allowing times to set and dry I sanded it all down using 220 grit on an orbital sander.
Step 10: Finishing
I stained the cabinet using Varathane Kona colored stain. Then lacquered it, it took 4 coats of lacquer sanding lightly with 320 grit flexible sanding sheets. This ensured a smooth to touch glossy finish.
I also primered the table/door and then painted it.
Step 11: Final Assembly and Install
It was as simple as placing the cabinet on the door and sliding the 1/2" rods through the holes. Then hanging it on the wall using 1/4" Strap Toggles and the french cleat system.
I stated by finding out the height I wanted the table. I decided on a bar height, about 40". Then I measured from the bottom shelf to 2" below the top back board. This was about 17-18". Now after finding 3 studs I marked a line at the center of each stud and 56" high. I then put my french cleat board on the wall lining it up with the 56" line on the wall and predrilled into the 3 studs using 5/16 in bit. Moved the board to install the strap toggles and then installed the cleat. Once that was attached, we lifted the whole assembly onto the cleat, predrilled into the studs, then removed it. Installed the strap toggles again and then hoisted the whole assembly up again. Installed it with the 1/4 bolts and there you have it.
The table is supported by the force downward from the shelf and the 2 rods. I even caught a 8 year old 60 lb child on top of it. Purely awesome.
Again, the face of it will sport a unique painting which will have the appearance of a large piece of art in a bold frame.
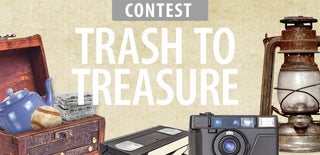
Participated in the
Trash to Treasure Contest 2017
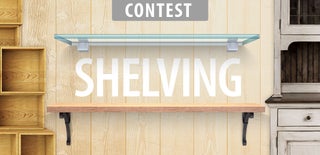
Participated in the
Shelving Contest 2016