Introduction: Fixing Fan Blade
In this instructables, I am going to repair my old table fan. As the summer season is approaching in my home town so I have to make arrangements for it. I remembered my old mini table fan with broken blade hub. I found this fan in my junkyard. Now I have a 3D printer so I got an idea to repair my fan blades with a 3D printed hub. If you repair something then you are reducing waste and helps environment. So I started to repair my table fan and sharing this tutorial with you.
Supplies
Screwdriver
Digital Vernier caliper
Measuring ruler
Nose pliers
Cutting pliers
Sand paper
Detergent powder
Cleaning brush
3D Printer
PLA Filament
Soldering iron
Screws
Superglue
Step 1: Disassemble All Parts
You have to disassemble the fan. This will help you to check whether all other parts are in working condition or not and it will also help in cleaning the parts. When I disassembled the fan, I found that there is no damage to the body parts and the motor is in working condition. It makes my work easier and I have to repair only the damaged hub of the fan blade.
To disassemble a table fan, follow these steps:
Remove the Front Grill: Most table fans have a front grill that can be removed for cleaning or maintenance. Look for screws or clips holding the grill in place and carefully remove them. In some cases, you may need to use a screwdriver or pliers to loosen screws or pry open clips.
Take Off the Blades: Depending on the design of the fan, the blades may be removable. Look for a nut or bolt at the center of the fan blades. Use an appropriate tool, such as a wrench or screwdriver, to loosen and remove the nut or bolt. Once removed, carefully lift the blades off the motor shaft. In my fan, the blade hub is already broken.
Detach the Rear Grill: After removing the front grill and blades, you may have access to the rear grill. Similar to the front grill, look for any screws or clips securing it in place and remove them.
Access the Motor and Housing: With the grills and blades removed, you should have access to the motor and housing of the fan. Depending on your needs, you may need to further disassemble these components for cleaning or maintenance.
Step 2: Cleaning Parts
Clean and Inspect Components: Once disassembled, you can clean the individual components of the fan, such as the blades, grills, and motor housing. Remove grease and oily substance from the shaft of the motor with the help of sand paper. Use detergent powder and a soft brush or cloth to remove dust and debris. Inspect each component for any signs of damage or wear.
Cleaning blade hub: The hub of the blade consists of broken hole and their residue parts. So I have to remove these residue parts with the help of long nose pliers. Care should be taken while removing the residue parts as it may damage the blades. After removing the residue parts clean the hub with the help of sand paper.
Step 3: Prepare 3D Model
Dimension measurements: I used Digital Vernier Calliper and a measuring ruler to measure the diameter of the shaft of the motor, inside diameter of the hub and the depth of the hub. After taking measurements I prepared the 3D model on the Tinkercad. The dimensions are:
- Shaft Diameter = 5.50mm
- Inside Diameter of hub = 45mm
- Depth of hub = 12mm
Design the Blade: I used Tinkercad to design the blade. Consider the proper dimensions of the 3D print and factors such as balancing and the overall shape for optimal airflow.
Choose the Material: Select a suitable material for 3D printing, such as PLA or ABS, considering its strength and heat resistance. Make sure it’s compatible with your 3D printer.
Printing Process: Set up your 3D printer and load the design file. Adjust the printer settings for the chosen material and print the blade. Make sure to print with enough infill for strength, especially near the hub. The slicing software settings are shown in the images.
Post-processing: After printing, remove any support structures and smooth out the surface of the blade if necessary. You can use sandpaper or a fine-grit file for this step.
I have made an additional 3D model (Hello World), which is to be attached on the top of the front grill.
Step 4: Reassemble and Testing
Balancing: It’s important to ensure the blade is balanced to prevent vibrations and noise. So I added to screwed on the opposite sides of the 3D printed model. These screws not only help in balancing but also helps in fastening the blades to the shaft of the motor.
Assembly: Attach the printed part to the fan hub with the help of superglue. Depending on the design of your fan, you may need to use screws or other fasteners.
Testing: Once assembled, test the fan to ensure smooth operation and adequate airflow. Make any adjustments if necessary.
Reassemble the Fan: After cleaning and inspecting the components, reassemble the fan in the reverse order of disassembly. Ensure that all parts are properly aligned and securely fastened. Tighten any screws or bolts as needed.
Step 5: Working
Check the wires and the switch of the fan. Make sure that there is no cut on the cable and if the connections on the switch (it is found in my table fan) are broken then solder them properly. Once reassembled, plug in the fan and test it to ensure everything is working properly. Listen for any unusual noises or vibrations that may indicate a problem. My table fan is now working properly without any noise.
Hope you like this tutorial. if you need any help and have suggestions for me let me know in the comments section.
Thanks for reading.
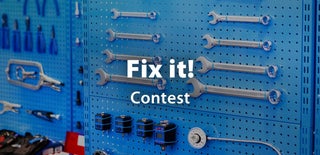
Participated in the
Fix It Contest