Introduction: Flame Polishing Acrylic
As part of a new Instructable, I realised I would need to use a technique I haven't seen documented here before, and that is the flame polishing of thermo-plastics.
Its not hard to do, but requires access to some fairly special tools, ideally an oxy-propane or oxy-acetylene torch.Here, I am using a "Jewellers" scale torch which seems to be fine for my size of work.
Polishing works by locally melting (NOT burning) the surface, and the low viscosity of the melt and surface tension in the liquid plastic does the rest.
Step 1: Preparation.
You can see here how "frosty" the curved edge of my workpiece looks, after being routed out. Preparation began with a light sanding to remove the more egregrious saw and router marks.
Next, I take a "naked" Stanley knife blade, and use it as a scraper, to plane off the protruberances.
Step 2: Scraping
Just like the very finest wood finishing, scraping acrylic produces a very smooth surface, which is perfect for the final finishing. To scrape the edge, hold the blade perpendicular to the surface and drag.
The noise isn't pleasant, but the work gets the job done quickly. You can see in the picture, the snow like planings coming off the work.
Step 3: Flame Polishing
Step 4: The Final Result
Stages
- Preparation: remove saw marks
- Scraping: remove prep marks
- Flaming: remove scrape marks
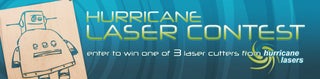
Participated in the
Hurricane Lasers Contest