Introduction: Float Tank DIY!
There are so many distractions that swirl about us that make us feel like we are sinking beneath the weight of them all.
So many things that are vying for our attention that string us out with questions, fears, and anxiety that feel like we are drowning in them.
Now more than ever there is a need to be able to take a few steps back to recollect ourselves and to cut through the noise. This could be in the form of a walk through nature, leaving your electronic devices in another room for a few hours, spending the time reading a paper book, or having a deep conversation with someone close to you about how each of you are doing. However sometimes the tried and true and ways of being able to decompress might not be possible to do because of the weather or distance between people or maybe they even get a little monotonous and so with some extra time on my hands working from home I decided to build a float tank or sometimes called a sensory deprivation tank for a completely different way to disconnect.
You may have seen them on various science fiction shows like Fringe or Stranger Things or seen coupons and advertisements for float tanks around asking you to pay by the hour for the chance to float. First, you buy the coupon and then wait for the float spa to open and drive there and go through the whole process and experience in someone else's space. What if for the cost of about 10 float sessions you could build your own compact tank and float at your leisure?
Why would anyone want a float tank in the first place? That is a good question to start with. It is a great place to relax and unplug to get out of the noise and collect your thoughts. You may even drift off while you are floating and get a real power nap! Some say they are a vehicle for interstellar travel but I am pretty sure those trips are powered by psychotropic drugs so I will not make any promises that you will have a repeat of the Dr. Strange movie while using your tank.
It can also be good to help you make creative breakthroughs! It is an environment with probably the least amount of distraction possible and since it is such an different experience it can be a great place to come up with ideas that are just as far out there or break out of a creative rut.
One other reason and then we will get to it is that Epsom Salt is supposed to be really good for your skin and hair so you have that added health and aesthetic benefit in addition to the mental and emotional health you could gather from floating.
To make this project like you are going to need a list of materials to make your own serviceable float tank along with a few tools
Now if you are not keen to build your own but want an off the shelf solution I would suggest checking out Zen Float Tank. FTC Disclaimer: I earn a percentage of the sales through the affiliate link to Zen Float Tank (It helps me build more and bigger projects)
http://zenfloatco.com?tap_a=4802-f1563f&tap_s=1355...
FTC Disclaimer: I earn a percentage of the sales through the affiliate links provided through Amazon.
Supplies
Materials
- 4'x8' 19/32" Plywood (To make the base to mount the whole tank to)
- 2x 4'x8' 3/8" Plywood (To line the inside of the tank)
- 3 1/2 - 4x 4'x8' 1/8" paneling (To cover the outside of the tank)
- 6x 2"x6" 8' Studs
- 9x 2"x4" 8' Studs
- 6x 2"x3" 8' Studs
- 2x 4'x8' Corrugated Plastic Sheet (Covering the inside of the lid)
- 2x 4' Continous Hinges
- 8x 4" Heavy Duty Casters
- 6'x10' Shower Liner
- Filter capable of keeping 100gals clean preferably with UV
- Hard Side Water bed heater with digital controller Digital Thermometer
- Digital Thermometers (Optional: Double check the water heater thermometer)
- Hydrometer (Battery tester matches the range very well)
- 3x 4'x8' 2" Pink Extruded Foam Insulation (To insulate for sound and temperature)
- 1 1/4" screws
- 3" Screws
- Velcro Tape (Connecting some removable panels and some of the liners but there are other solutions)
- Caulk
- 10' of 3/4" ID clear tubing
- 4' of 1" ID tubing
- 4x 1" PVC Elbows both ends threaded
- 3x Tube Clamps
- 40x 1/4" Metal Washers
- 2x Metal Handles for the Lid
- ~400lbs of Epsom Salt (As you can see in the pictures I went with Dr. Teals which provides a cost effective USP grade Epsom Salt)
- ~80 Gallons of Water
Tools
- Miter Saw (Cutting Studs to length and cutting the 45 degree angles. You could also just use a circular saw.)
- Circular Saw or Table Saw (Cutting the Plywood and Paneling to size)
- Jig Saw (Cutting the hole to recess the Water Filter)
- Drill (Pre-drilling holes for screws and starter hole for jigsaw)
- Impact Driver (Optional but very helpful for putting in all of the screws
- Carpenter's Square (Marking the boards for cutting and drilling and lining up studs)
- Tape Measure (Measuring the boards to cut to length and pre-drill holes)
- Safety Glasses
- Ear Plugs (I like to use shooters ear muffs so I can hear if someone is talking to me)
- Utility Knife
- Caulk Gun
- Large Clamps
Step 1: Cut Everything!!!
If you are like me and you have not been able to build out the shop of your dreams yet and are wanting to have a float tank to be able to visualize that glorious place you might not have daily access to tools that are needed for cutting up the wood for a project like this so I planned out all of my cuts and I made them all in one afternoon. Here are the cuts you are going to need to make to the boards and panels that you obtained.
First lets start with the 2"x6" boards.
- Two of these boards will need to be left at full length of 8'
- Seven 45" sections will need to be cut for the cross studs between the 8' boards
- This will take four 2"x6" boards and you will have some scrap and a 51" section leftover.
- 19" of this 51" piece are used to make a small adjustment to my original design in Step 4
- ~22" of the 51" section are used in Step 9 to prepare for an upgrade I plan to do in the lid.
- These are used in Step 2.
- This will take four 2"x6" boards and you will have some scrap and a 51" section leftover.
Next we cut the 2"x4" boards. These have the most complexity of all of the boards that are are dealing with, but I tried to keep it as simple as possible using only 45 degree angles so that if you have a Miter Saw you will only have to set the angle once!
- Two of these boards will be left at full length of 8'
- Two or Three 45" sections will be used as the cross studs for the top lip of the bottom portion of the frame and to help frame in the basin at the head of the tank.
- Set aside two 2"x4" for this part because while my design deviated from my plan to try and improve access to my filter you may want to stay symmetric and have a 45" section as the top lip of both ends of your tank while needing the additional support on the bottom head of the tank.
- I cut one of these pieces shorter to 32" for the top lip at the foot to allow better water filter access.
- Fourteen 10 1/2" sections for the upright supports for the angled tank sides around the whole tank.
- Set aside two 2"x4" boards. You will have a little left over because you can get 9 of these per 8' board
- You can decide if you want to cut these to 9 1/2" or 10 1/2" like me. I went with 10 1/2" because it would give me a like bit of a lip above the sloping tank basin to be able attach the liner to something more sturdy and not have to search for the supports. It also helps to add a little bit more height to the tank basin to allow for more water or to make it harder to splash water out.
- Ten Angled sections that look like the hypotenuse of a triangle. See the second picture above. The measurement between the two tips of the board is 18 3/8" which gives you a rise and run for this board of 13". These will be the primary supports for the sides of the tank and be placed on top of each of the inner 2"x6" studs.
- Set aside two 2"x4" to make these pieces.
- The way that I cut these was I set my Miter Saw to 45 degrees and took the square end off of my 2"x4" so that the resulting edge was at 45 degrees. I then measured 18 3/8" from the tip of the board and marked it. The next step to be able to keep the same Miter setting is to roll the board over to the other side so that the 18 3/8" mark is closest to the fence. Then you run your cut and double check to make sure that the longest edge of the board is 18 3/8". I then took my first board and laid it on its side to make sure that the rise and run that this angled board created was indeed 13".
- Now that you have done the first board you keep going by marking, flipping, and cutting the next board.
- Four Angled sections where both of the long edges are the same length which also happens to be 18 3/8" because we are trying to accomplish the same rise and run of 13". This is the third picture in this step.
- Set aside one 2"x4" to make these pieces
- If you are making these pieces right after you other angled pieces your Miter Saw should still be set to 45 degrees. Again we start by taking the square end off to create a 45 degree angle at the end of the board. We again also measure 18 3/8" from the tip of the board and mark it. I suggest measuring from the tip because it was the easiest to find it with the tape measure. Then you just slide the board down to your mark and cut again. NO rolling since these cuts are both in the same direction.
We are wrapping up our Miter Saw use but we have one more set of boards that will make the lid of the tank.
I decided to use 2"x3" because they are lighter than 2"x4" and they are cheaper and since the lid does not support any weight other than its own and I will have to lift it to get in and out I wanted something lighter to work with. So onto cutting those 2"x3"
- Two of these boards will be left at full length of 8'
- Five 21" sections will be used for the flat top part of the lid
- Set aside two 2"x3". There will be a lot left over of the second board because four of these pieces will come from the first board.
- This is a simple measure and cut straight across the board to create your 21" sections
- Note: You could move some of the angled pieced we are going to cut next to this board but it was much easier to just have straight cuts on both ends of this board and save the angles for the other boards
- Note: I used some of the remainder of the second board to cut some ~22" sections to be used as additional bracing at the very top of the lid.
- Ten Angled sections that are cut similar to our last 2"x4" cut so that they will look like the the third picture in this step but the measurement of both of the long edges is 17". This gives a rise and run of 12" so when two of these are connected together with the 21" piece it will be 45" long which is exactly what we need.
- Set aside two 2"x3" for this because you can get 5 of these pieces per board with a bit leftover.
The result for the lid will be tunnel with no 45" cross brace at the bottom. I am attempting to not need this piece by using continuous hinges to keep the flexing down and the paneling that will enclose the top should add some rigidity.
Now we are moving to the table saw or the circular saw whichever you have available to cut our panels for the tank basin and for paneling in the lid. We will start with the lid because a majority of the these cuts are straight across keeping the full 8' length of the board.
This is going to take three of the 1/8" paneling boards. Depending on how you want the fit and finish to look you will need an extra 4'x4' section or two extra 2'x4' sections for the end pieces.
- Cut two 21" sections that are a full 8' in length
- These will be used to cover the top of the lid on the inside and the outside
- Cut two 18" sections that are a full 8' in length
- These will be for covering the outside sloped sections of the lid.
- Note: It might have been nice if they were maybe a 1/4" wider.
- Cut two 17" sections that are a full 8' in length
- These are for covering the in the inside sloping sections of the lid
- Cut two 4' sections for the end covers from the leftovers from the board you cut the 17" sections from
- Ideally these sections would be 15" tall and you can get a full extra board to grab these sections but 14" tall can still work
- These cuts will be much easier with a Jig Saw if you have one.
- In the bottom corners you should draw the outline of a 2"x3" board then 3/4" in from both sides draw a line that goes up at a 45 degree angle. If your board is 15" tall this line will measure 18" long to match that slope of the lid. If you are using the 14" leftover section it will be more like 16 1/2" long.
- It might just be more helpful to look at the to be able to help translate what I have written. Check out the fourth picture help clarify the shape.
Next we are cutting the paneling for the basin. This is using 3/8" 3-ply plywood since is was a good balance of weight, strength and cost. This is going to take two of these 3/8" plywood sheets.
- Cut one panel down to 80" long and then cut two sheets 18 1/2" sheets
- These will serve as the paneling for the angled sides of the tank.
- This will leave a 16"x48" section we will use and a 11"x80" section that we will not use
- Cut the 16"x48" section down to the following dimension 13"x45"
- This is for the end of the tank at the head.
- Cut one sheet that is 19" wide from the second sheet and then trim it down to 80" long
- This is will be the center/bottom of the basin.
- The remainder of this sheet will be used to cut our last two major pieces.
- Taking the remaining ~29"x96" section of the board we need to cut out a 19"x 18 3/4" section of the sloped foot of the tank
- Using part of the left over 29"x75" section of the second board I cut two triangle pieces of the compound angle sections at the foot of the tank that are used to create the compartments foe the water filter and other operations of the tank.
- These triangles are equilateral triangles that are 18" on each side so these are pretty easy to cut. You can take a 18"x27" section of the leftover piece so I would recommend cutting off 18" off the 75" dimension of our largest leftover board.
- Taking a measuring tape starting from the corner mark at 9" and at 18". Then from the 9" mark measure ~15 9/16" up then using a straight edge connect that last mark with the corner of the board you started from and the 18" mark. The result should be a perfectly drawn equilateral triangle.
- Do the same from the opposing corner making sure to draw both triangles out first before cutting to make sure you are going to be able to get both of them cut.
- Now with both drawn cut away!
Wow! What a mouthful. This project involved a lot of cutting and it took me a few hours to get it all done between purchasing the wood, loading it up, unloading it, figuring out my measurements, and then finally cutting it all. With all of the boards cut we should be ready to tackle with project with a drill a whole bunch of screws and a little bit of space.
Step 2: Check Everything Fits in the Footprint. Assemble Lower Frame
This project has gone through so many iterations on paper trying to find the right parts and then once the parts were selected trying to get everything to fit in such a way that the final result would be a compact and movable float tank.
I really wanted to make this tank movable for two reasons. The first is that it is nice to be able to move it out of the way when I am not using it and the other is that it helped me meet the design goal of integrating the water filter which was a little too tall so having the solution up on casters allowed me to recess the water filter through the bottom to help everything fit. That part will be clear in clear in Step 6.
I started by using a 19/32" 4'x8' base piece of plywood and then laid out the support base studs with two major factors in mind.
- I wanted to make sure that the structure could hold the weight of the water, salt, and me which will make this whole project very heavy. Unless you have a spot in your garage or basement where you can build this project on a concrete floor you might want to reconsider making it or if you make it consider not using the casters in your design because you will want to spread out the weight as much as possible. Be sure to double check that wherever you plan on building this project that it is capable of holding the static load that this thing will generate because it could easily over 50lbs per square foot.
- I needed enough space to integrate the water filter which I accomplished by using 2"x6" studs for the base to get that extra 2" of height over a 2"x4" and by making a 13"x13" compartment in the corner of the tank with a slopping top. This created a whole host of challenges making me wonder if not integrating the water filter or getting a smaller filter would have been better. If you decide to make this it would be great to see how you accomplish this. Maybe a pool filter? I will get to explaining this more in Step 6.
The result of making this compartment is what inspired the symmetric layout of the bottom studs, While they are symmetric they are not evenly spaced. Here are the on center measurements I used for the placement of the 2"x6" studs along an 8' section of 2"x6". See the second picture.
- 3/4" (This is the end stud so that it is flush with the end of the 8' section)
- 14 1/2" (This gives a 13" section between these first two studs)
- 30"
- 48"
- 66"
- -14 1/2" ( I am using a negative measurement to indicate that you measure from the other end of the board)
- -3/4"
With the bottom frame laid out I drilled two pilot holes on each end of each board 1 1/2" from each side using a 1/8" drill bit. Then using 3 1/2" screws I put this lower section of the frame together. See the third picture.
Note: When you are attaching these cross pieces do your best to have them line up flush height-wise with the 8' board. My 8' boards had a little bit of bowing in them since I am using stud grade lumber so I had to hold the 45" boards a little off the ground to line up with the edges of the 8' boards. (This will make your life easier when it comes to attaching the base and the casters)
All told there are seven 2"x6" that are cut to 45" across this system which is critical for supporting the load that we will have between the ~80 gallons of water which is over 700 pounds and ~400 pounds of Epsom salt or more not including the weight of the frame itself and then there is the weight of the user. Since all of this intended to sit and move on casters I wanted that weight evenly spread as well so that is why this design uses eight casters capable of holding 250 pounds each.
You may see in my pictures that I waited to attach the two end most studs thinking I would need to access to that section. That was not the case so I would recommend just finishing this section up and moving on.
Step 3: Attach the Base Board and Casters
If you look closely you can see that I did a lot of other work before putting on the casters but in hind sight I would attach the 19/32" base board and casters at this point in the project so that you do not have to flip over anything larger than you have to. So for now ignore anything else in the pictures and just focus on attaching the 19/32" base board and casters to the 2"x6" frame we just made.
With the 4'x8' base sheet sitting on top of the 2"x6" frame I spaced the 8 casters out around the base to help me know where I could screw the 4'x8' to the frame without interfering with the caster mounting. I put a caster in each corner and a caster at each end of the 30" and 66" studs since this gave me the best spacing of the casters while still putting them at key points under the frame.
I used a handful for 1 1/4" screws to attach the 4'x8' sheet to the frame with 3 screws between each of the casters on the 8' side and 5 screws spaced between the casters on the 4' side.
Now with the base board securely attached it is time for the casters. I am using 3 1/2" screws and 1/4" washers to increase the head size of the screw so that they do not go through the large holes in the caster mounting plate. Based on the framing pattern I was only able to get 3 screws in per caster because I wanted my mounting screws to go into a 2"x6". Lining up the casters so that the rectangular mounting plate is facing a perpendicular direction to the 4'x8' base I lined up two of the mounting point to be 3/4" in from the side so that the screws would go solidly into the 8' section of the 2"x6". The third mounting hole I lined up so that it would be centered in the 45" cross beam. See the third and fourth pictures.
Using a 1/8" drill bit I made 3 pilot holes for each of the casters.
Note: Using the water filter that I did required a little bit of modification of one of the casters which is easiest to do before you put it on. I need the size of the caster to be a little bit smaller which I accomplish by removing the brake peddle. This was easy to do with a small metal file to take the rivet out and pull off the brake apparatus. See pictures 7 through 13.
OK, if you have all of you pilot holes drilled and screws and washers apportioned then you can go about the business of attaching your casters and flipping the base back over so we can get this project ROLLING.
Step 4: Attach the Angled Basin Supports
With the base fully setup with the base panel and casters attached it is time to start installing the angled braces to help round our tub out! Going with the mantra of measure twice and do what ever comes after that only once I walked around the base frame on each of the 45" studs and I measured in from the outer edge of the 8' board 14 1/2". You could also measure from the point where the two studs meet in 13". This mark on each of these boards will be our marker for where the edge of the angled support will be placed when it is screwed in. I then placed the 10 angled braces that we cut around one on each side of the five inner studs. See the first picture.
Then using some large clamps to hold the brace in place I drilled a pilot hole that was in the middle of the board and 2 1/2" up along the board in the middle so that the 3 1/2" screws I used would still make good contact with the stud below. Once those 10 angle braces were attached at the bottom I moved to the end angle braces. See pictures 2 through 4.
Now taking the other angled 2"x4" we cut, it is time to install the angled braces for the ends of the tank. This is where I encountered my old nemesis again, I have the hardest time taking into account that boards like 2"x6" are actually 1 1/2" thick and not 0" thick. So as I was laying out the angle braces for the end of the basin it became clear that if I went forward with the exact plan that I had cut the boards to that I would have my head and feet touching the ends whenever used the tank and that was unacceptable.
(You can see this more clearly in the pictures where I went from a symmetric design that I liked to call emerald cut to the more pocket design where one end is a more open and the other is tapered. See pictures 5 - 10.)
So while the foot of the tank needed to stay angled to leave space for the water filter and other elements in the ongoing evolution of the project the other end of the tank did not need to be angled in the same way for any other reason than symmetry of which I am a big fan or for the sake of reducing the amount of water and therefore salt needed. However none of that matters if I do not fit so installing the remaining angle braces at the head and foot of the tank will be a little bit different from one another.
Starting with the angled braces at the foot of the tank where the water filter and other storage will be. Measure another 1 1/2" inward from the edge of the angle braces that we just attached to this stud. This will give us a guide for how to position the edges of the angled brace. The brace should be flush against the side of the 2"x6" stud with the angle of the brace coming right off the top of the stud. This will mean that this angled brace will not be resting on the 19/32" panel at the bottom. Thankfully I do not have 3 hands otherwise shopping for clothes would be difficult so instead I used one of the large clamps and used that as a small stand to help hold the angled brace in place then centering on the brace I measured 1" and 3" to drill my pilot holes with the top pilot hole holding a 3 1/2" screw and the bottom pilot hole holding a 2 1/2" screw. Now with these angled braces attached we can go to the head of the tank to finish up the bracing there.
The angled braces for the head of the tank are the same as what I used at the foot of the tank since I already had them cut and I would also not have a stud to work with. So using the same 13" mark that we we made at the beginning I used a small spare piece of 2"x4" as a stop to butt the angled brace against and then I clamped the stop and the angled brace to the frame like you see in the picture. I then spaced out three 2 1/2" (I did not want the screws poking through) screws into the angled brace. This process was repeated on the other side. Then using a 19" section of 2"x6" that I had left over that I talked about in the cutting step I filed the gap between the braces to strengthen things up and to give me a place to screw the bottom panel into at that head of the tank.
Step 5: Attach the Upright Supports and Upper Frame
Now by themselves the angled braces that we just installed with a single screw will not be enough to hold our tank together and they have also not given us any place to attach hinges and a lid so the next step is to finish the support system by closing up the final open side of those triangles and then attaching our upper lip to the bottom half of our tank.
This is where those 10 1/2" sections that we cut from our 2"x4" that seemed like we were just making scrap will come into use. Each one of our angled braces will get one of these pieces to help support it by connecting the top of the angled brace back to the 2"x6" base frame.
I marked the top and bottom of each of these upright supports at 1 3/4" so that I would know where the center is and then measured 1" from each of the ends to mark where I needed to drill my pilot holes. See the first picture. I did this marking and drilling for 10 of the 14 pieces. The two pieces for the head braces and the two pieces that are the edges of the compartment of the water filter I positioned these off-center so instead of marking them at 1 3/4" I marked them at 3/4" so that they would sit flush with the angled brace. Which side you measure this from depends on which brace you are working on to give it the most space.
Then with all of the marks made it was time to drill the pilot holes and put in the screws. I used 3 1/2" screws for all of these to ensure that a good purchase was made into all of the boards involved.
The result when this is all done and you place the 2"x4" boards along the top to finish out the lower frame there is a small lip that sticks up and this will be very useful for attaching out liner and giving just a little bit more depth.
I start with mounting the 8' sections of 2"x4" for the upper frame as these would be the most stable. I lined up the board with the ends of the tank and measured up 3/4" from the bottom of the 8' board to ensure that I would still be drilling and screwing into enough of the angled braces. I decided to wait to put the 45" sections on the ends to finish this section off because of how I wanted to mount the end panel for the head of the tank and I was still undecided if I would have the section at the foot of the tank only be 32" to leave a little bit better access to the filter for making servicing easier later on.
Step 6: Install the Water Filter
Most of the professional tanks that I have seen use some sort of combination of 1 micron filters with UV lamps and for the more expensive tanks or those at float studios that have lots of people passing through them they even use ozone treatments and hydrogen peroxide dosing systems. Since I am not planning on opening a float studio with my tank I did not think I need to go to this level of filtration and in large part if I shower well before going in it will help a great deal. However I keep Hydrogen Peroxide on hand to manually dose the tank from time to time.
I went with a pond filter that has some useful cleaning mechanisms and an integrated UV lamp to help disinfect the tank water. The filter medium is likely 200 micron so much larger than that the professional solutions but I can always look at fixing that later by adding another stage or changing the filter. The extra space in the foot of the tank beneath the angled sections is intended to leave space for storage of things like bottle of hydrogen peroxide to manually dose the water for disinfecting, extra salt to top off the tank, and if I ever want to upgrade the system by adding an ozone generator to help disinfect the water further, but I digress into feature creep (truly one of the worst creeps that there is much like analysis paralysis).
If you are interested in understanding a little bit more about UV sterilization and how it works check out my youtube video on UVC!
So I set my filter into the compartment that I am planning to use and even with all of the work I have done it is still a little bit too tall but one nice feature about this tank is that it is round and it has a small lip a few inches up from the bottom. I plan to use this to my advantage so I made sure that where I placed my filter in the compartment was clear of where the caster wheel would swing below and I traced an outline of the bottom of the filter onto the 19/32" board. Then removing the filter I drilled two starter holes and I put my Jig Saw into Tokyo Drift mode and did my best to power slide my way around my crayon drawing of an outline.
As the last few reciprocating strokes of the Jig Saw finished and I felt the crude circular plug drop to the ground my heart did the opposite and jumped up into my throat hoping that I had cut this right and that the filter would sit in there perfectly and not get cracked open by the caster. Lowering the filter in was one of the most satisfying parts of the project because it fit the first time and it really was feeling like this float tank was coming together. See the eighth picture. It was a little bitter sweet because it was still a hair too tall but that is something that I figured out how to deal with when I was putting in the basin paneling.
After I set the water filter in its compartment with the hoses attached it became clear that a little bit more modification would be needed to help the hoses get to where they needed to be. This involved the use of four 1" threaded PVC elbows. They let me bend in the intake path above the filter and the output path down into the structure so that I could run it to the head of the tank. See the ninth picture.
Step 7: Install the Basin Paneling and Final Basin Supports
I know that you have been eyeing the big stack of 3/8" plywood that you had set in the corner thinking when do I get to really start putting this together to make it look like a float tank instead of the worlds largest taco holder? Those same thoughts have been going through my mind as well hence why I wrote them but now is your moment to start putting the "in" on that base you have been making to turn it into a full fledged "basin".
Starting with the 19" x 80" section we place that on the bottom middle to form the floor of the basin. Make sure you are grabbing the correct panel since we have three panels nearly the same size. It should fit perfectly so that it almost touches the angled braces as the foot of the tank and ends right at the edge of the final 2"x6" stud so that it is still exposed. This is where that extra 19" section of 2"x6" that we put down between the angled braces really comes in handy. I used my large carpenter's square to help me know where the edge of the stud was and I drilled pilot holes and put three 1 1/4" screws into this base board for each of the studs. See the second picture.
With that panel put in it was time to put in the two sloping side panels that we cut that are 18"x80". Using the same technique as the bottom panel I positioned these two side panels to line up with the edges of the angled braces and rest on the panel that was just installed on the bottom. Then with the trusty carpenter's square to guide me along the edge of the angled braces I put three pilot holes followed by three screws into each of the angle braces. See the Third and fourth pictures.
The next section that I put in was the angled foot panel which measures 19"x18 3/4". Place this on the angled braces at the foot of the tank so that it is resting on the base panel that we installed first. Then since both of the angled braces are at the edge it should be pretty easy to rill the pilot whole and put three screws per angled brace.
The panel for the head of the tank is treated a little differently in that it is rested on the 2"x6" frame at the very end and pressed against the angled braces. I put one screw into each of the angled braces through this panel to help hold it in place. Then I took two 45" pieces of 2"x4" and I placed one at the top to close the upper lip of the tank on that end which I screwed to the two 8' sections of 2"x4" and than drilled 5 pilot holes into the top of the head panel and screwed it to this top 2"x4". Then resting the second 45" board on the 2"x6" base I screwed through the 2"x4" to sandwich the head panel between the angled brace and this bottom 2"x4" to ensure that the bottom of this panel was well supported and it would not blowout when water was put in. See pictures 7 and 8.
I then ran a bead of sealing caulk on the edges that I had between the panels to close things up and help smooth out rough edges on the panels to keep them from poking through the liner and causing leaks.
Now onto the other part of the project that I have dreaded which is figuring out how to install the triangular panels that have the compound angle in the foot of the tank. I took brain storming with a number of people to help me see that I could use some of the scrap pieces of the 3/8" paneling to create lips that the triangular panels could rest on and be connected to using Velcro to hold them in-place while the weight of the water that would be sitting on them would do the rest. Taking those weird 18" equilateral triangles I rested them on 2 1/2" lips that I had made out of scrap and attached to the angled panels. One really important point is that you need to make sure that you install these panels as a cross grain. If you have the grain pointing down towards the bottom point it will be a much weaker panel and well flex and possibly break. Give it a try by flexing carefully the triangle cut board from different sides. you will notice that when you try flexing the board perpendicular to the grain it is much weaker so there is just one more reason why it can be better to go against the grain.
This has two really great consequences (Good consequences because consequences are actually just a result or reaction to something and are not inherently good or bad but it just sounds ominous.)
- It gave me just a little bit more height so that the filter that I had chosen could fit.
- There were now small gaps at the bottom of the panel where I could send my cables for the waterbed heater and temperature sensor.
You may now be looking at your basin and be thinking, "Wow that is a sweet basin!" and you would be right to think so. Now it is time to heat things up and by that I mean installing the waterbed heater and starting to position the shower pan liner that will serve as our basin liner!
Step 8: Install the Water Heater and Liner
With all of the paneling installed you may be thinking that this project is really starting to float your boat and you would be right if you for some reason think of your physical body as a boat that contains who you are. Existential thoughts put aside for the time being because there is still a tank basin and a cover to finish.
The next step is to place the waterbed heater into the bottom of the basin like what I have in the pictures one and two and then run the cable for the power and temperature control to the water filter compartment. I am trying to follow general guidelines for installing a waterbed heater which is to place the temperature sensing element a little bit away from the heater itself. I then run the cable out of the small gap in the bottom of my triangular panel which is such a satisfying feeling.
The next stage is to layout the shower liner on top of the basin. I left mine unfolded for a few days to off gas because it had a rather rubbery/plastic smell and to try and let some of the creases to smooth out. The hardware store that I went to had a pre-cut 6'x10' liner and I do not think that I could go much smaller. After the liner had set out for a while I started to press it down into the basin to position the liner to guide my attempts at trimming the sides and adding my screws to mount the liner into the basin.
I am leaving the liner a little bigger in every dimension so that I can double the liner over for placing the screws and washers into the liner to help them hold better.
Once the screws and washers are installed along the basin the liner for all of the sides except that side that you plan to install the lid on you can go in and we can test to see how well the system holds water because without that it will not be worth its weight in salt. If this water is filtered you can leave it in there while we work on the next steps of making the lid and going through the finishing touches, but it is much easier to install the lid with the basin being dry because you will likely need to crawl inside to get at those middle screws of the hinge.
I am planning on attaching my liner up onto the lid a little ways to help and protect the hinges and the lower supports of the tank from getting wet in the case of either splashing or condensation dripping down. This will me done with velcro until I can think of a better way.
Step 9: Build and Panel the Lid
While I waited for the shower liner to off-gas a little bit I took the time to build out the lid of the tank using the 2"x3" boards that we cut and the 1/8" utility paneling. I started by putting the ribs of the lid together.
The lid is designed to be the top section of of hexagonal tunnel. This helped to keep the overall size down for storage and materials and has the added benefit of creating some slope in the "ceiling" to help with condensation dripping.
This process was made much easier by using the corner of a table to clamp both boards down to the table in the position that I wanted. Then making a mark on the straight piece of the rib 1 1/4" from the edge to be in the middle and then I drilled pilot holes for my screws so that they would go directly into the middle of the straight board. I then flipped over this combined board to attach the angle board on the other side in the same way. I then repeated this process four more times to build the 5 ribs that would make up the lid.
Then I measured and marked out the on center mounting points for each of the ribs on two of the 8'x2"x3" boards.
- 3/4"
- 24"
- 48"
- 72"
- -3/4" (This is measured from the other end to ensure it lines up well)
Then lining up the 5 ribs with these marks on the 8' board and making sure that the edge of the rib is flush with the bottom of the 8' board I drilled two pilot holes 3/4" of an inch in from each edge and put in screws to attach the ribs to the 8' boards. Be careful to not use screws that are too long and poke through. It is important that the bottom is flush otherwise the lid will not close properly.
Then wanting to reinforce the ribs and to give a platform to eventually mount a monitor at the head of the tank I placed a 2"x6" at the exact middle of the ribs at the head and to help firm up the other end I installed two 2"x3"s on the edges of the flat section of the rib.
The next step is to mount the angled panels to the outside of the lid. These are the 18"x8' panels. They should reach all the way down to the 8' long piece of 2"x3" and come all of the way up to the edge of the flat part of the rib. Using the same carpenter square trick to help me find the rib I put in three 1 1/4" screws per rib to hold the panel in place. The fit and finish on this left a little bit to be desired but I will work on that when I insulate and paint.
Installing the outer top panel of the lid was very easy. Using the 21"x8' section rest it on top of the lid and using the carpenter square trick I kept track of where the ribs were and put three 1 1/4" screws into each of the ribs.
Now it was time to install the weird paper hat shaped end pieces. These should fit perfectly in on the ends if the cuts were made correctly using a piece of panel that was 15" tall. I then used the drill and made pilot holes and put in screws along the rib on the end to ensure good contact and to help add more rigidity to the lid frame.
With all of the outside covered it was time to flip the lid over and start covering up the inside of the lid. This would give a 2 1/2" space between the panels that I plan on filling with spray foam or some form a insulation to help with temperature regulation and sound damping.
One thing that I noticed trying to put these interior panels in is that the space is just a little bit short than 8' so I ended up having to trim my 21" and my two 17" panels a little bit shorter to be able to fit snugly into the inside of the lid. With my pieces trimmed a little bit to fit I started with the 21" center panel and drilled pilot holes for each of the ribs and put 1 1/4" screws to hold it in place. I repeated the process for the sloping panels but it was important to use some clamps to keep them from sliding down and touching the flat panel because this gap at the top will be useful in the future for pushing some airflow through the top of the tank to keep condensation down and improve the internal environment.
We now have a finish and completely paneled lid that is ready to have the continuous hinge installed so that it can go to its proper place on the top of our tank.
EDIT: 7/15/2020
I have since swapped out the interior particle board panels for corrogated plastic sheets for a number of reasons.
- Waterproof
- Waterproof
- Waterproof
- Lighter
So you might get the idea that they are water proof which is an important factor since the inside of the lid gets wet with condensation especially before the lid is insulated which I will talk about in a different step.
I ended up cutting a similar 17" wide piece for the center of the tank and a ~22" piece for each of the sides of the tank to eliminate that gap between the sides and the top.
I also added a considerable amount of water proof caulking around the seems of the corrugated plastic to help keep the water that condenses inside the tank and to keep dirt and dust from the outside or the insulation from falling into the tank.
One other element that I added was a clear sheet over the head of the tank for being able to work on a future project of installing a 4k screen to test turning this thing into a theater.
Step 10: Install the Hinges and the Lid. Place the Lid Liner.
I am not very good at lining things up which is one of the many reasons why I have such a terrible short game which is one of the many reasons I stay off the golf course and stay in the workshop. I wanted this system to have a good connection between the base and the cover that would seal well and that would not flex when I opened it even if I did so from a corner. So I am using two 48" continuous hinges to help remove any wiggle and to spread out the force of lifting the lid along the whole body and they actually ended up being a pretty good deal.
I used a carpenters square with a lip to help me drag a 3/4" line on the top lip of the base of the tank and on the edge of the lid that would hold the hinges. Then laying the continuous hinges out of the edges I marked the spots where all of the mounting screws would go and proceeded to drill pilot holes for each of them.
I decided to install the hinges on the lid because it like that would be easier. Then getting someone else from my household to help with the lid made the total installation onto the base a snap!
The other benefit is that they are easy to attach to the base and the lid and make it easy to put a sealing strip along the whole length of the edge. Now that we have the top and the bottom fully attached it is time to turn this thing into a functioning float tank by adding our water and salt!
Once the lid was attached I added my two handles to the front side of the tank. They are just standard 4 point mounted handles. I lined these up with two of the cross supports in the lid and attached them by drilling pilot holes and screwing them in.
I also finished attaching the base liner which goes up the side onto the inside of the lid to cover the hinges. I ended up using some industrial strength Velcro to hold this on since it will be covered by the inner lid liner.
The inner lid liner is simply black painters plastic. I cut a 6'x10' sheet from the roll and positioned it on the inside of the lid using more of the industrial Velcro so as to not put holes in the liner and to make it easy to remove for modifying the lid for future projects.
Step 11: Filter and Prepare the Water and Prime the Filter
It is very important to start with very clean water in your system because the cleaner your start the easier and cheaper it will be to maintain in the long run. All told I used 80 gallons of water to fill the basin and the prime the pump and filter. I also added from Hydrogen Peroxide to treat the water right from the beginning.
Then once the system had about the desired amount of water in it I turned on the heater to help warm the water up to ease the mixing in of the Epsom Salt which took a long time to add and dissolve measuring along the way. All told it took about 400lbs of Epsom Salt to get into the desired range for the Specific gravity.
The testing of the water was one of the most satisfying parts. You can get an expensive glass for testing the Specific Gravity of the water OR you can get a super simple and inexpensive lead acid battery tester brand new. Make sure that it is new! This has a Specific Gravity range that is perfect for testing float tanks between 1.2 and 1.3.
The filter that I am using came with a submersible pump which was not me ideal scenario but it will work for the time being. This pump will sit in the foot of the tank when it is going through a filtering cycle. I will nee to decide if I will keep it in the water full time to keep it from drying out and getting clogged with crystallized salt or if I can keep it in a bucket in one of the compartments at the foot of the tank.
Then I gave the filter a run to test it all out and it worked so well that I got really pumped that I had a great solution on my hands.
Step 12: Insulate the Tank for Sound and Temperature.
EDIT 7/15/2020:
I decided to use a 2" pink extruded foam insulation for a few reasons.
- Easy to work with since it can be easily cut with circular saw or utility knife
- Very moisture resistant
- Good insulation value
- Fills most of the space available
I started by insulating the lid which meant I had to measure the dimensions of every compartment. While the width of the compartments turned out to be very consistent because I worked hard to cut all of my boards to the same length that widths are sort of a mish mash of dimensions and yours will likely be as well because I was only so accurate when I was installing the ribs of the lid.
Taking the 4' x 8' pieces of foam I cut 8' long strips of them that matched the width of each side and the top with the intention of cutting each piece to its bespoke length. This took some time but after measuring at least 3 times and cutting twice in some case I had all of my insulation pieces finished. I made sure that they fit and then pulled them out because if you are reading this step I also have replaced the inside panels of the lid with corrugated plastic.
Now that I had the insulation finished but removed I went crazy by putting caulk on every seem inside and outside of the lid. You can see in the pictures that I have black painters plastic covering the water. This is for both debris and to keep the moisture away from the lid as the caulk is curing to be able to withstand the moisture.
The bottom of the tank was a different story. The supports that hold up the bottom lip of the tank narrow the path to get access to the spaces where I wanted to put the insulation. This was relatively easy to handle though due to how easy the insulation is to work with. I cut all of the the bottom pieces to the desired sizes which were even more bespoke than the lid and then I cut them in half along their length so that I could feed them in one at a time. This worked well and resulted in getting a fully insulated tank with the exception of the panel above my face and the contoured panels at my feet.
Step 13: Adding Lift Assist Pistons
EDIT 07/15/2020:
Every single person that has seen this project in person has commented, "Wow, Ryan that looks like a coffin." Well it can feel like one too since when I first made the thing it had a very heavy lid that was difficult to lift from the inside so you needed someone outside of the tank to help. This just would not do so I picked up some very large lift assist pistons that are likely designed for a dump truck or probably just a tail gate cover.
I struggled more with trying to design how to put these in than I did with lifting the lid but it was important to figure out how to do this. There are two dimensions that are given for a lift assist piston and those are the minimum and the maximum length. I learned a few things.
- Your design needs to be able to move out to the maximum length because I could not compress these 80lb assist pistons by hand
- Your closed position needs to be a longer than the minimum length of the piston or else it will never close
Ok so Ryan how do I make that happen???
After weeks of wanting to eyeball this thing I realized that was not going to happen and that I needed to see this thing as a geometric problem. What do I mean by that? Well I solved it using something called a "cord". What a cord is a line that intersects a circle at two points. This maters because the lid opens and closes with the hing as the center of the circle and the lid as an arm that follows along a set circumference. With that in mind I set my radius to 10" initially but I had to drop it down to 9" because my lift assist pistons were too strong to let the lid close.
Step 14: Float!!! Iterate for Future Improvements
The future for this float tank is vast I have so many interesting projects that I want this to branch off into.
The first project will be to add insulation to the base and the lid to improve the thermal properties of the system and lower operating costs and reducing the exterior noise that comes in. The other part of this improvement will be to look at how air flows through the tank to address any issues with condensation. (DONE See step 12!)
The second one is to install some speaker exciters and a 4k monitor to test making a float tank into the most immersive theater experience ever where you are floating weightless and the only sound and sensation and visual stimuli is what you are watching so stick around for a future instructable to see how that turns out.
The other is to testing using EEG sensing technology that I am planning on making in a future project to see what biofeedback can look like while in sensory deprivation.
There is so much potential for what this project can be used for from the comfort of your own home and it will have much lower cost in the long run than most other tanks out there because of the optimized water volume reducing the amount of heating and salt needed.
Let me know if you have ideas for what this could be used for in the comments and if you have ideas to improve it or questions about how to make it or how it works let me.
Also give my video on YouTube where I talk about making and using this project a watch, like, comment, and subscribe it would help me a lot. It should be posted shortly! Thanks!
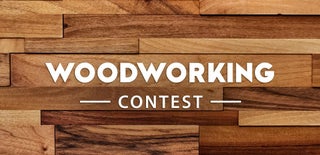
Participated in the
Woodworking Contest