Introduction: From an Ikea Footstool to (Poang) 3D Printer!
Hello All,
This is my first Instructable and I wish to share with you the build process of my first 3D printer...
Yes, another one, but this one made from an Ikea footstool find in the trash can of my district, so I though: Why not retrieve the frame and try to adapt it for the purpose?
From the garbage I've recycled also smothed rods, support brackets and wood panels...
Now, starting from a I3Prusa Rework and adding an Ikea footstool; with some fix you can easily built this new model at home!
But let's start from the beginning:
All the Mechanical parts, Heated bed, Screws, Nuts and Washers and Electronics are the same of the standard model as described here: Prusa_i3_Rework_Bill_of_materials
You can find the Prusa Rework standard edition, for completeness, here:
Step 1: An Ikea Footstool 3Dprinter? It's Possible?
First of all I tried to arrange a new design with a 3D cad program, starting from a geometrical survey of the curves of the wood frame.
At the end of this Step you can download the 3d drawing resultant of the Ikea frame.
So I extimated in advance the entire geometry and design for the more efficient configuration of the printer (another solution foresaw to use the frame in horizontal). After verifying the parts involved, I modified the plastic parts downloaded for i3 Prusa rework for doing my customs parts.
You can download the entire set of custom parts in the next step.
- From the Bill of Materials you can observe that the motor suggested for i3 Prusa Rework are the Nema 17, so, for this 3D printer I've used Nema 17 but with the body of 60mm long. For the Z Axis Bottom file I foresaw the height of 60 mm (please adjust if your motors are of the nema 17 standard (height 48 mm): you must foresee a thickness under the motor of 12 mm). I've used exacly this model here: Robotdigg Nema17 - 60mm
- For the Step Extruder I've used this one: RobotDigg Step Extruder pre assembled.
- For the Smooth rod Ø8 I reused rods from old printers, almost all inkjet models have inside 1 or 2 Ø8 corrected rods of high quality (so you can save money and reuse an old component).
Attachments
Step 2: Gathering Plastic Parts and Components
You can download the entire (custom made) set of Poang 3D printer plastics at the end of this step, or alternatively from this link: 3D Poang on thingiverse.com
For the Heated Bed Knobs I've used this model from Thingiverse: Heat Bed Knob
For the rest of materials my list is here:
Smoth Rods:
2 Smooth Rod Ø8 - 370 mm for the Z axis
2 Smooth rod Ø8 - 370 mm for the Y axis
2 Smooth rod Ø8 - 360 mm for the X axis
1 Smooth rod Ø8 - 385 mm for the Display support
1 Smooth rod Ø8 - 370 mm for the Filament support
Treated Rods:
2 Threaded rod M5 - 350 mm for the Z axis
3 Threaded rod M10 - 210 mm for the Y carriage
1 Threaded rod M10 - 370 mm for the Y carriage (bottom rear, between the Ikea frame)
2 Threaded rod M10 - 395 mm for the Y carriage
Mechanical Parts:
7 Linear Bearing LM8UU
1 Bearing 624zz
4 Bearing 608zz
1 Belt GT2 - 760 mm
1 Belt GT2 - 900 mm
2 Coupling 5*5mm
5 Motor Nema 17 (60mm long)
2 Pulley GT2 - 20 teeth
Heated bed 1 PCB Heated Bed MK2B
1 Glass Plate (recicled from an old picture frame)
1 Kapton Tape
4 Binder Clip
1 Thermistor 100k
Electronics:
1 RAMPS Board 1.4
1 RAMPS LCD discount display with Sd socket
1 Arduino Atmega 2560
4 Stepstick A4988
3 Endstop w/ cables (mechanical)
1 Power supply w/ cables 12V - 30A max
Screws, Nuts, Washers:
41 Screw M3 14
3 Screw M3 24
4 Screw M3 30
2 Screw M3 60
6 Screw M4 20
1 Screw M8 30
53 Washer Ø3 mm
6 Washer Ø8 mm
34 Washer Ø10 mm
1 Grub Screw M8 20
5 Grub Screw M3 8
33 Nut M3
6 Nut M4
2 Nut M5
1 Nut M8
34 Nut M10
1 Nylstop Nut M8
Ok, all the components are on the desk, We can start!
Step 3: The Frame Fits?
For the Frame assembly you need to cut the Ikea wood panel (the seat of the stool) and straight parts of the frame:
Remeber, my 3d printer frame have a clear distance between the two curved legs of 370 mm (interior), so you must to cut the part of the Ikea frame as show in the picture. I used only a part of 370 mm at the top of the construction, but, for improve the stability you can add a second part in the bottom rear.
We will use the wood plane (the seat of the stool) for do the base of the entire printer, so we can to cut it to 250x495 mm.
Remember that we need an extra 220x220 mm plane for do the heated bed support, if you cut the plane carrefully, you can do all with the same footstool.
Step 4: Building the Y Axis
Mounting the Y carrier is much similar to all the Prusa Printers, all rods are M10 mm sized;
but, we have the treated rod (rear bottom) that is longer: 370 mm blocked to the frame with two frame mount.
Also we have 3 type of Holder Y printed parts, start with the middle (the smaller one) and mount it to the middle of the 2x 395 mm treated rods. This because the front part is directly supported from your table; the parts to the center and on the back are supported to the base plan of the printer instead.
Please verify that this is the correct Y Holder before continuing: the tallest one is for the FRONT side, the lower one is for the MIDDLE (the only one in white in the pictures) and the intermediate is for the REAR side of the Y carriage.
In the rear upper 210 mm treated rod you can insert the X Motor support with the Y Endstop, and in the front 210 mm treated rod you can insert the Y Idler and block all with 10 mm nuts and washers.
You now have the Y carriage quite completed: on the 220x220 wood plane you can measure the right distance of Y Carriage 370 mm smothed rods (on the top) and mount here the Linear Bearing LM8UU (3x) in their printed holders (3x).
You need also to make four holes in the corner of the 220x220 wood plate for the heated bed screws, the distance between the holes is 209x209 mm (diameter of the holes are 3mm). You can download a .pdf file for the holes reference below.
Attachments
Step 5: Z Axis and Frame Assembly
Now we can start with the Z axis.
First of all you can screw the plane to the legs with 4x M3 screws (25mm long), the distance between the rear end of the legs and the end of the plane is 60 mm
Screw the Holder to Y rear part of carriage (in black) to the legs when you are sure of the position of the Y Carriage, in my case this distance between the Y carriage mount (blue) and the end of the wood plane (rear side) is 50.50 mm
For the Upper support of the Z rods, you must measure the verticality of the smothed rod using a level and then screw the (black) holder to the frame in two points.
For thehorizontal part of the frame you can use the original hole in the leg for mounting the frame, for this screw (from ikea, of course) you must deepen the hole from the inside to the outside, another hole to do, as shown in the images, is the 4th: this is a new hole (only inside of the frame), use it for the plug for mounting the horizontal frame.
Step 6: X Axis Assembly
The assembly of the X axis is quite similar to the Rework instructions, here you can find the link:
The only difference is that the Stepstruder needs a special support (it is in the plastic parts).
Mount it to the X carriage, using the 3x Lm8uu linear bearings in the rear side (remember that 3x linear bearings works better than 4x)
Assembly the X Idler and X Motor support with two Lm8uu linear bearings (2x each side) and insert a 5 mm nut into the holder screwed on the 5 mm treated rods (from the bottom).
It's a good idea to use hot glue for block the nuts inside the holder (insert it from bottom).
For complete the assembly you can insert the 624zz ball bearing and the Gt2 timing belt on a 3 mm screw and nut; and glue it; on the other side you can mount the timing belt on the Gt2 - 20 teeth pulley as usual.
Finally you can screw the X endstop to the left side of the X axis.
Step 7: Wiring and Electronics
For the general information for Wiring I follow this guide:
Here my comments for the 3D Poang version, the position of the Electronics is on the top of the frame as shown.
Special wiring:
Remember to install all the jumpers for 1/16 microstepping mode (below the stepper driver A4988)
I used the free space usually used for drive the second extruder for doubling the Z motor driver, without divide the cables for Z motors in two legs: one single driver A4988 for each Z motor (the first is the usual Z axis motor driver and the second one is the driver for the second extruder).
For wiring I decide the position of the electronic board and I try to reach it with the minimum cable lenght.
It's a good idea to use a spiral cable wrap to arrange the cables, in my case I wrap together the following cables:
1) Y motor + Y endstop > Electronics
2) X motor + X endstop > Electronics
3) Extruder hotend + Extruder motor + extruder fan + extruder thermistor > Electronics
4) Z endstop > Electronics
5) Z motors > Electronics
6) Heated bed supply + Heated bed thermistor > Electronics
Step 8: Final Assembly and Notes
For the final assembly step you can mount the LCDDisplay on the 8 mm smothed rod (with two display support parts and two grubs)
Then you can arrange the power supply on the rear bottom legs of the 3D Poang frame, mounting it quite relieved using a L shape mounting bracket (also this one come from Ikea).
For the "Filament feeding station" you can use a 370 mm smothed rod and two filament bar holder (in the picture in black), with a filament support wheel (inside of the coil) as shown.
It can hold a maximum of 5 spools together. I used also a 3 mm screw to block the support to the top frame.
Step 9: Calibration and First Lap!
I use Marlin firmware uploaded to Arduino mega, here an overview: Marlin overview
For basic settings the firmware here you can find a simply guide:
General Settings and steps/mm
In the arduino/Marlin tabs choise Configuration.h, here you can see a small series of parameters for Poang model configuration:
#ifndef MOTHERBOARD
#define MOTHERBOARD 33
#define CUSTOM_MACHINE_NAME "Poang3D"
const bool X_MIN_ENDSTOP_INVERTING = true;
const bool Y_MIN_ENDSTOP_INVERTING = true;
Z_MIN_ENDSTOP_INVERTING = true;
X_MAX_ENDSTOP_INVERTING = true;
Y_MAX_ENDSTOP_INVERTING = true;
Z_MAX_ENDSTOP_INVERTING = true;
Z_PROBE_ENDSTOP_INVERTING = false;
#define INVERT_X_DIR true
#define INVERT_Y_DIR false #define INVERT_Z_DIR false
#define DEFAULT_AXIS_STEPS_PER_UNIT {78.5,78.5,4062,99}
#define DEFAULT_MAX_FEEDRATE {150,150,30,1000} // (mm/sec)
#define DEFAULT_MAX_ACCELERATION {600,600,100,50}
Testing
I used Cura software for slicing the .stl file, you can find thedownload here.
For now the Poang prints Pla filement (1.75 diameter) at 210°C for extruder and 60°C for bed.
Here the link of the .stl used for testing:
Fist of all I suggest you the essential calibration test, You can find the download here: http://www.thingiverse.com/thing:5573
Now You can try to launch a 3D print of a 10x10 mm or 20x20 mm cube and measure it after printing.
With the simply calculation you can determine the fine calibration of the steps/mm in each axis;
For instance with a 10 mm cube is:
NEW STEPS = OLD STEPS * (10/mm of the printed cube)
Here my test models, And now... Rock and Roll!
Yoda Head: http://www.thingiverse.com/thing:14104
Great Tie Fighter model: http://www.thingiverse.com/thing:1150625
Batman cookie cutter: http://www.thingiverse.com/thing:35796
Boat Calibrating test: http://www.thingiverse.com/thing:763622
Step 10: Recent Upgrade! Poang 3D Ramp 1.4 Case!
New step is added! May 22, 2016
Using two Ikea Bokis Book brackets we can add a Ramp 1.4 case,
So we can recycled two Books support as a Ramp enclosure!
Here you can find the complete instructable for Custom Ramp 1.4 Poang Case
Step 11: Recent Upgrade! Z Axis Top Rods Holder
New step is added! May 24, 2016
Here a simply upgrade: Z axis rods holder, to mount between 5mm treated and 8mm smooth rods.
It' s a simply way to control the movements of the 5mm rod in the top of the lenght.
Step 12: Recent Upgrade! Adjustable Z Probe + Stand for Bed Auto Leveling
New step is added! May 31, 2016
Here a simply update for add Auto Bed-Leveling system to my Poang 3D
The Probe is Adjustable and you can mount the stand part directly on the bracket of the extruder.
You need also a Hall magnetic sensor like this one from Dx.com
I've used in addiction 2x mini-magnets 5x5x5 mm and 3x 3 mm screws and bolts.
You can find the printed parts also on Thingiverse.
Enjoy it!
Step 13: Recent News! the Poang 3D Presented at Genoa Maker Fest 2016
News from the 1st Genoa Maker Fest (Italy) - June 11, 2016
Here some photos from the First Genoa Makers Fest - June 11, 2016;
The Poang 3D pinter are invited to present the 3D Poang refit project to the people, together with a lots of other projects involving Drones, Printers, Sensors and Robots, and lot of Speech in the morning.
In the Poster the People can find the QR code for this instructable and the text: "Build it you too".
With the link and an Ikea exagonal key... Enjoy it!
Here a video from Il Secolo XIX, main newspaper of the city (Italian speak)
(Extra Thanks to MadLab Genova for all the support, you can find more information here.
Step 14: Future 3D Poang's Improvements...
Yeah, for me it was a big test, and now i wish improve my design with (in random order):
- Better protection for the filament with a PTFE tube and Filament filter.
- Better Endstop holder for X and Z axis (may be adjustable like this one).
- A quick system for insert the filament (like this one).
- Enlarging the Y carriage to reach 30 cm printing size.
- Add auto leveling bed system, with Hall-sensor (in progress).
- ...?
And now... Are you ready for built your next 3D Poang printer?
Acknowledgements:
I wish to (Extra) Thanks to the boys of FabLab Genova (italy), here are their links:
https://www.facebook.com/fablab.genova
Without their help, (patience) and their passion in doing things I would not get this 3D printer working prototype!
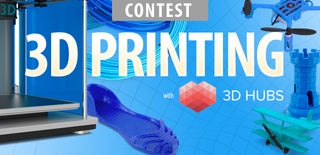
Participated in the
3D Printing Contest 2016
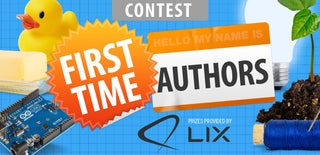
Participated in the
First Time Author Contest 2016
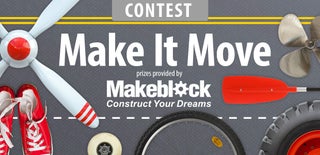
Participated in the
Make it Move Contest 2016