Introduction: Getting Started With Wood Turning. (tools, Techniques and Top Tips)
I thought it would be handy to create a beginners guide for people thinking about getting into wood turning,
or people who have seen some wood turning projects they like but felt that the demonstrator skimmed over some of the basics.
Wood turning an incredibly rewarding hobby, which is a gateway to other creative adventures and if you are creative and passionate enough it can pay for itself. (though its probably a good aim at first to just enjoy yourself and get to grips with a new skill)
This instructable is broken into sections so if there is a part you are most interested in you can jump straight to that section but if you are really new to woodworking it will be worth reading everything. (I will try to make is as fun of a read as possible).
Step 1: So ... What Is Wood Turning?
Wood turning is in its most basic form shaping wood whilst it spins.
The wood can be spinning at some speed and there are dangers involved, so its a great idea to think about safety first.
Step 2: Personal Protective Equipment (PPE)
Straight to the sort of boring bit.. (sorry)
I know that PPE (Personal Protection Equipment) can seem dull as all hell but it is super important. Also its not really that dull and the coolest kids have the best PPE.
The things I recommend everyone have are as follows + reasons why I recommend them:
Eye protection. (You only get two eyes and some people don't get two properly functioning ones to begin with.. Its a good idea to keep yours working as well as they can)
I wear a visor which gives a good deal of protection from potential accidents (actually a visor with respirator is best but I cannot currently afford one so its on my Christmas list) A visor is also a great option if you are like me and wear glasses.
The second best option to keeping your eyes nice and safe are safety glasses. (Its best to make sure you can see out of them.. I remember at school there was a pair of safety goggles which were full of CA and other things.. this made them less than useless- slightly more dangerous to use them)
Foot protection
This one isn't as obvious but would become obviouse quickly if you dropped a sharp tool.
Sturdy footwear will protect your feet from falling tools. Often these tools are sharp. with tool vibration your skews and gouges might migrate and there is a fairly good chance that if your wearing adorable bunny slippers their comfortable fuzziness will prove to be useless at saving your foot.
This isn't to say don't buy awesome bunny slippers.. just don't wear them in the workshop. Good work boots or something with a steel toecap will do a much much better job at keeping all your toes where they're suppose to be.
Lung protection
This is a somewhat overlooked aspect. But really important.
According to HSC.gov.uk Wood dust can cause serious health problems. It can cause asthma, which carpenters and joiners are four times more likely to get compared with other UK workers.
I would recommend a respirator with good quality filters. A good respirator will not be uncomfortable to use and will keep your airways functioning as well as possible. I swap out my filters fairly regularly and would recommend this as best practice.
I would also recommend a dust extraction system (though they are noisy they keep the air around you a bit cleaner. I have mine hooked up to all my big machines)
The really good thing about dust extraction systems is you can hook them to different shop machines to quickly and efficiently remove wood dust and partials from the area, making the whole thing more pleasant. You can buy spechal hoods with clamps to extract dust from closer to the area your working which makes things even better.
Step 3: Lathe Safety
I'm sure you know this already.
Wood turning has the potential to be dangerous. Unlike most tools in a workshop where the thing cutting the wood is the bit that moves, when wood turning the wood is moving and this needs you to think about safety in a slightly different way.
We can reduce the dangers. But it's always going to be there so always be sober around power tools, or scary tools and try to think ahead about what you are about to do and what could go wrong.
Speed
I would always recommend starting turning at a low speed and working your way up.
If you are turning something which is out of balance it is likely to cause your tool to vibrate. the larger and more out of balance the more obvious this problem will be and the more likely that the wood will brake away from the lathe and damage the visor you put on after reading the first bit of this instructable.
If you have something large and out of balance you can start slow rough out and make the work more balanced before increasing speed. (reducing the amount of vibration is also likely to save the bearing in your tool so you can enjoy turning for a lot longer without having to think about repairs)
Tool rest position
The tool rest is the part of the lathe where you rest your cutting tools, (skews, parting tools etc). Ideally you want the tool rest to be as close as possible to the wood without touching it. It is best practice to check the wood by rotating it before turning the lathe on. If you turned the lathe on and the wood hit the tool rest you could damage your tool or risk injury.
having the tool rest close to the wood also means the tools are less likely to be damaged, will work better and the wood turning will be more of a pleasure because you will not be fighting with your tools.
Step 4: The Tool Thing
Wood turning requires a few tools as well as a lathe.
I would recommend a beginner getting a fairly modest kit at first, learning how to use the tools they have and then adding to your collection. (there are a lot of turning tools out there and a lot of different grinds or modifications you can do to effect the performance of your tools, don't worry if you don't have them all , they're not like pokemon- you don't need to catch them all.. (unless you really love your lathe and want to give it presents). You can normally get the result you're looking for with a kit of around five turning tools in your collection. I will add an extended list of tools and their uses later as well as some advanced techneques.
To make it easy for readers to skip to the tools they are interested in and use this intractable as a reference I will talk about the main tools and how to use them in separate steps.
Step 5: The Lathe
I have created an image pointing out the different parts of my lathe for you to refer to whilst reading this next part.
The big one. This is the one that turns the wood.
All the component parts of this tool are important. But perhaps the most important is the on off button. I have personally had to quickly hit the off button to avoid an accident, It is a good idea to know exactly where it is.
Head stock- where all the power comes from
Drive center- there are different types they help to hold work when spindle turning (Spindle work is turning between centers- (the head and tale stocks)
Tail stock- the tail stock holds a live center -similar to a drive center but has a bearing to allow it to rotate with the wood.
Banjo and tool rest- The banjo holds the tool rest and allows it to be moved to the most appropriate position for
turning- The tool rest allows purchase for your turning tools to work. you rest the cutting tool on this when turning. Without the tool rest your tools would slam into the lathe bed and have a high likelihood of hurting yourself or damaging your workshop.
Lathe bed- the bottom part of the lathe where the tail stock and banjo can travel and be locked into place as needed.
Step 6: Chuck
A chuck attaches to the head stock and holds wood. Often the wood being held will have a chucking point or spigot turned into it to allow for a better grip from the tool. You would use a chuck or a drive center and swap them depending on the turning operation you are planning to do.
Step 7: Spindle Roughing Gouge-
The big tool that shifts most of the weight. It can leave a decent finish to the work but tends to be used to create a rough shape. Its the tool of choice for taking a square blank and turning it round. Its typically fairly wide (sometimes ridiculously wide and tends to have a straight grind) Word to the wise. Never use this on a bowl. the tool has a weak point going into the handle if you were to use this tool on a bowl you would risk the tool breaking.
Roughing out
I have known some people to ruff out or turn to round using a number of different tools but the best one for the job is the roughing gouge (AKA the roughing spindle gouge.
Making sure your tool rest is in a position where it can support your tool introduce the bevel of the gouge before angling the handle up and introducing the cutting edge. It is highly recommended that you "work downhill" meaning cut from high points to low points. I would recommend using a stance where you can move easily allowing your body to move the tool rather than just your arms.
Step 8: Spindle Gouge- Sometimes Known As a Shallow Fluted Gouge.
This is the go to tool for making details such as beads, coves and can be used to shape spindle work without much fuss.
Spindle gouge
If you mastered the roughing gouge this is the same thing only much much smaller . The introducing the bevel thing still applies. But with this tool you might want to think about putting in some pretty details like beads and coves.. To make a bead work out where you want the top part to be and where you want the bottom part to be. as you move the tool along the rest and the wood rotate your tool and cut the shape. (this is somewhat difficult to describe in words but the great thing about instructables is I have pictures to help)
Step 9: Skew Chisel
Skew chisel- Tends to be used mainly as a tool for planing the wood. it gives a really good finish from the tool with virtually no sanding. It can be used to create very fine details and depending on how adventurous you are it can be used for most jobs. (This tool has a reputation for being difficult and scary. Once you know what your doing with it it is a very useful tool.. it just demands a little respect.. Always give it your full attention.. I have only had one injury whilst turning and it was a result of not using the skew properly.. It wasn't a bad injury but it still happened.. now I am more aware that the skew needs complete concentration.)
When using the skew to make planing cuts it is important to use the middle part of the blade and avoid the end parts.. If you hit the moving wood with the end parts you are likely to get a catch .. This isn't the end of the world but can be a little scary if your not expecting it.
Skew
The skew chisel can be used to do a number of different things but tends to be known for its ability to give planing cuts. I like to raise my tool rest and approach the wood as flat as possible . Again approaching the cut with the bevel (This is likely to become a little boring I will recommend approaching the cut with the bevel again soon .. It makes sure you're cutting the wood rather than just scraping the wood. It gives a much nicer finish and is kinder on your tools) try to cut with the middle part of the blade. If you catch the wood with the pointy end of the blade or the other pointy end you're likely to get a catch. Chances are nothing too bad will happen but it's likely to be scary enough to make you want to change your pants.
I love making super fine detail with the skew. To do this I use the pointy end like a knife. (what do you know i'm not talking about introducing the bevel first... ) making sure the tool is supported I introduce the pointed end and make a cut. I then come in from the sides of this cut to neaten the whole thing. (I have made people who have been turning for a long long time scratch there heads in disbelieving at the fineness of detail which can be achieved this way.
Step 10: Parting Tool
Parting tool- the clue is in the name it parts wood. When working between centers it is safer not to part all the way through work instead part most of the way and finish the job with a saw. (turn the lathe off before using the saw)
I have been known to use the parting tool for jobs its not designed for like being a scraping tool. It is to me an ideal tool for making a spigot for a chuck to hold onto. (I also like to use a small skew for this)
No introducing the bevel with this fella. This is pretty much the tool that you introduce and watch it cut.. it will not give you a nice finish and its not really meant to. I would recommend making 2 cuts with this tool rather than cutting all the way through. This will reduce friction. If you are parting off I would also recommend not parting the full way with the parting tool instead finishing the job with a saw and maybe making everything look pretty using a gouge afterwards. A lot of turners who know the dimension they want and the position they want will use this tool to cut down to the this depth measuring with calipers
Step 11: Bowl Gouge
Bowl gouge- also known
as a deep fluted gouge.. the channel running down the gouge is much deeper then with the spindle gouge. (I sometimes use some of my bowl gouges for spindle work. mainly because they are easy to grab and I have a variety of grinds) it is ideally suited to shaping bowls the dish shape as well as the outer shape.
Bowl gouge
There isn't anything stopping you from using a fairly aggressively ground bowl gouge as a spindle gouge but in my opinion the bowl gouge comes into its own when turning dishes.
Used in a similar fashion to the spindle gouge to cut the outside profile and a tenon for the chuck to hold onto once mounted in the chuck with this tenon the bowl gouge can be used to easily form the dish. I tend to work from the outside edge inwards when using a standard bowl gouge, I tend to introduce the cutting edge in a line from where the bevel would be rubbing if the bowl extended far enough and cut in towards the center.. eventually the cut will lead to the bevel rubbing as well and make everything feel a lot safer.
Step 12: Swept Back Grind Bowl Gouge
Swept back grind Bowl gouge-
pretty much the exact same tool as a regular bowl gouge but with a different grind.. A bowl gouge will tend to have a straight grind a swept back grind is more of a U shape and allows the wings of the tool to become exposed as cutting edges.. This makes the tool very versatile allowing for a greater range of cuts. It is my favorite grind.
Swept back bowl gouge AKA the best bowl gouge.. (my opinion only its very subjective)
With this bowl gouge you have a few more options mainly because of the wings.. when I am making a dish with the swept back bowl gouge I will use the wings to cut and then drag back towards the edge of the bowl. If you don't rub the bevel you might risk a catch or the tool might cut a little more aggressively than you were initially expecting.
Step 13: Scraper-
Scraper- these come in different profiles and act in a similar way to a cabinet scraper. There are some turners who really love them and some who really don’t. The main drawback in using a scraper is preparing the tool with a cutting burr. I have watched wood turning videos where the turner only used a scraper. The tool is really for finessing rather than doing the heavy lifting.
Step 14: Sharpening Your Tools
I think the one thing that really pays off when turning is making sure you have really sharp tools. Sharp tools make wood work into wood fun, it takes away all the hard work and gives you much much better results.
There are a lot of sharpening systems out there with associate jigs to ensure you can reproduce specific grinds.
I personally use a slightly adapted Tormek sharpening system which uses a wet grinding stone running at a slow speed. This system is hard wearing and reduces the risk of changing the properties of the metal.
(I tend to to keep a few diamond honing pads handy to touch up a cutting edge- for me this feels like I can extend the time between proper sharpening the tools and works with the hollow grind to give a micro bevel)
I would recommend learning how to use your sharpening system for your tools- each system will be slightly different as a result I cannot go into huge detail here. The information should be relatively easily available
Step 15: Two Type of Turning
There are two main types of turning. The techniques used are somewhat interchangeable but there are differences to bear in mind.
Spindle work is working between centers.
Face plate work involves holding the work on the drive center- this can be done using a face plate and screws or the work can be held in some form of chuck
I will start talking about spindle work and then talk about Face plate work.
Step 16: Preparing for Spindle Work
These are not hard and fast rules but recommendations which would suit beginners- once you are comfortable with the turning you might want to experiment to produce something with design features could would go against these recommendations (As long as you are safe and have considered possible dangers all should hopefully be fine).
When working between centers it is a good idea to find the middle part of the wood, (the centre- the part which is most balanced and will require the least amount of wood removed to turn to round). I like to make a mark or dint in the wood at this point which helps me to locate these points before compressing the wood between centers on the lathe.
I would recommend working with the grain in the direction of the lathe (this makes everything a little easier)
Check the work rotates freely and doesn't hit the tool rest before turning. Make sure the wood is securely held between centers and the tail stock is locked in place.
(Its super important to make sure the peace is being held securely).
When you are happy that your tool rest is at the tight high for you and at a distance appropriate for the blank you should be ready to work.
Step 17: Face Plate Work
Unlike spindle work where the wood is held between centers face plate work is held on the lathe by one point- the chuck, or screwed onto a face plate.
If you are using a chuck a good first thing to do is create a spigot for your chuck to hold onto. I tend to do this by turning between centers.
once you have your work chucked up- you would typically shape the outside of an object before re positioning your tool rest and using a bowl gouge to remove the wood you don't want taking care not to cut too deep.
I would recommend working from the furthest point from the chuck first- this way the remaining wood supports the work you are doing. if you don't think ahead you could undermine the whole project.
Step 18: Sanding and Finnisheing
The good news is sanding on a lathe is super easy.
This part is dusty so hopefully you will have been wearing a dust mask and using a dust extractor already but this is the bit that throws a lot of dust into the air so double check now...
Sandpaper
Sanding on a lathe is super easy.
The do's
Work up the grits.. The lower the number on a peace of sand paper the more aggressive it is. depending on our skills with the tools you might want to use very aggressive paper to hide mistakes but even if you haven't you might have some transitions that might want a little easing.
Work from the low numbers to the highest you have, you might want to remove dust between sands with compressed air or a cloth.
Change Directions.. You might be tempted to let the lathe do all the work but this might not give you the best results. The grit of the sand paper might make stripes , to stop this from happening stop the lathe after each grit to work in a different direction, this will break up all the un wanted lines.
Slow your lathe.. you can sand using the lathe speed to assist. just make sure you are doing it safely. eg don't wrap it around your fingers (something might happen and fingers are hard to replace) slowing your lathe speed will reduce heat which will reduce the chance of cracking and warping to your work.
Finnishes
so this is a really subjective thing and I know lots of people who have lots of contradicting advice.
The main thing is to think about how your object is going to be used.. If its going to be handled a lot you might want to think about a melamine/ plastic or even CA finish,. If it will be used with food or is a toy you might want to look for a toy safe or food safe finish. or if you just want it to be as easy to apply as possible you might want to think about an oil finish like danish oil or even a wax.
You might also want to think about coloring with spirit stains depending on the project.
I tend to finish most decorative turnings by applying sanding sealer after sanding knocking back the sealer with a final sand and then I apply a nice wax.
For turnings which are likely to be handled more I tend to sand to at least 600 and then apply thin CA / super glue instead of a sanding sealer and apply a number of coats before sanding and polishing the CA. (this process is called rubbing out… rubbing out has been known to get a giggle with non-woodworkers due to its double entendre)
Step 19: Showing Off
Here is just a short list to introduce you to some of the tools techniques and projects you might want to explore once you have gotten to grips with the basics.
Each one of these is probably an instructable on its own but its worth knowing some of the words for the advanced techniques to get an idea of what can be possible.
Box making – this requires fairly tight tolerances for the lid and the box to come together in a satisfying way.
Pyrography- this used to be called poker work and involves burning the wood in a very controlled way. I think this is the closest thing there is to tattooing wood
Inlay- this is including another piece of wood
Laminating- gluing up different pieces of wood to create your blank before turning
Piercing- using a drill or rotary tool to make holes in your woodturning
Staining- using stains to colour the wood
Carving- don’t think you cannot continue to shape the wood after turning, lots of artists have made amazing work by continueing after this process
Using a specialised lathe such as a rose engine- there are amazing lathes out there designed to do beautiful things. The tools themselves tend to also be beautiful.
Pen Making- There are a lot of pen makers out there- its a really fun introduction project and can quickly lead you into a world most people have no idea about. Really nice pens are amazing but its worth figguring out if you really want to know the difference between lots and lots of nibs and inks before devoting a lot of time into the hard core pen making.
Enter competitions and sell your work. – if you get into woodturning you will be happy to know there are competitions local, national and international, and there are artists who sell their work.
if you are looking to sell your work I would recommend not producing generic items and trying to offer your audience the best possible product you can in order to delight them. Woodturning can absolutely pay for itself but you might have to be creative in order to do this.
By the way... if you enjoy this Instructable and would like to take some of the ideas into projects feel free to check out my other indestructables or YouTube how to's.
Step 20: Fancy Words
There are a few specialist bits you don't need to know but its always impressive when you can talk the talk as well as walk the walk. I created a printable for when I gave demonstrations showing some of these fancy words and what they mean. Hope it helps.
Step 21: Additional Bits
It is often the case that when working on a fairly large text people miss some bits and peaces.
I will be refining this text from and adding extra bits, and I plan to create a follow up instructable talking about more advanced tools and techniques at a later date.
In the meantime here are a few things I missed out but will include in future iterations.
1. I would really highly recommend joining a local wood turning group if you can. sharing skills and experience makes everything a bit easier and more fun.
2. you don't have to buy the most expensive tools but defiantly don't buy the cheapest
My first set of wood turning tools you fail the basic requirements by law to be sold as tools, they were not fit for purpose.. I suspect rather than being made from high speed steal HSS they were made from some kind of hard cheese. The result was my first catch bent the tool 90 degrees. You might have seen skews or scrapers made from old files, this is also not ideal as the metal in files used in this way has been known to shatter. My first "proper" turning tools were a set from axminster, Not the most expensive but also not the least. I still use these tools in addition to the more expensive tools in my collection.
3. sharpening is really important, this kinda goes for most woodwork. i didn't mention burning the tools before but ... don't do that... u use a water cooled grinder called a tormek system and can recommend this.. there are others available but this is the one I use and it doesn't burn tools.
4. as well as wearing PPE remove jewellery and items that might get caught in the lathe.
5 . I know it might seem like theirs a lot of do's and don'ts but the most important thing is to enjoy what your doing. Wood turning is fantastic. it is super enjoyable and rewarding . just it can be a bit scary if you don't know what your doing so try to get into it safely.
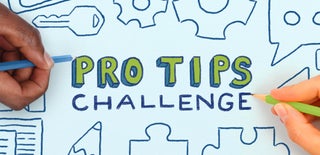
First Prize in the
Pro Tips Challenge
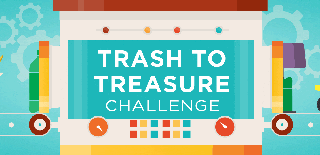
Participated in the
Trash to Treasure