Introduction: Glazed Penny Table
The purpose of this Instructable is to show how I turned Trash into Treasure!
Please vote for 11th hour entry!
I took a trashed wine table and turned it into a beautiful piece of furniture that is sure to be valued as a family heirloom. A little bit of finish work, pennies, and glazing does the trick.
Years ago I acquired this table from my grandmother. At one time it had a leather top. My first intentions were to have it "professionally" recovered in a faux leather to bring it back to it's original beauty and style. . Since it was a family heirloom I wanted it done RIGHT!
That plan crashed at burned horribly. I took the table to what I thought was a professional. Apparently a professional upholster is not the same as a professional in leather table tops. When I received the table back from the professional I was deeply disappointed in the workmanship of the piece. The bottom line was that the edging on the material cuts were terrible. The overall condition of the table was worse and less presentable than when I left it with the "professional" with a bare wood top. After a long discussion with the professional and disagreement, I was refunded the cost of labor. But, I was still out $75 for the materials. Bummer!
I was very close to trashing this table all together out of frustration and the money lost on the first attempt to have a professional refurbish the table. After calming myself, I decided to give it new life and an entirely new look.
Step 1: Supplies and Tools
SUPPLIES
• Table: used a vintage wine table that was TRASHED by a "professinal" that claimed they could refurbish the leather table top. The "professional" failed. They transformed a nice table into TRASH.
• Lots of Pennies. Used about 800 pennies for this project.
• Protective Gloves: Used to work with the Goof Off, Tarn-X, Super Glue, Stain, and Glaze. FYI... Goof Off also appears to work its way through the 7mil Nitrile gloves I used from Harbor Freight.
• Clean lint free rags: Used to apply adhesive remover and stain.
• Goof Off: Used to remove adhesive left by leather top that was torn off.
• Tarn-X: Used to remove patina and grime from pennies. Makes them shiny again!
• Glass Jar: Used to clean pennies with Tarn-X
• Stir Stick: Used to handle pennies in Tarn-X
• Wood filler if needed to fix wood imperfections to ensure flat surface for applying pennies.
• Stain
• Clear Poly Coat Finish
• Sand Paper: Remove any old finish and sand first coat of poly coat finish on wood.
• Calibrated Measuring Cups: Used to measure resin and activator in equal parts and mixing.
• Glaze solution: Used as the glass-like clear coat on top of pennies.
TOOLS
• Screw driver to remove table top from legs.
• Nylon brush to work Goof Off into grime of drip trough of table.
• Electric Sander: optional if you choose to use muscle instead.
• 80, 150,220 grit sand paper for removing old finish and work out imperfections of wood.
• Paint Brush: Used to apply clear coat to wood table top.
• Homemade penny application tool.
• Metal cutting too: Used to cut pennies to size as needed.
• Heat Gun: Used to work out bubbles in glaze.
• Razor Utility Knife: Used to repair glazing drip oops.
Step 2: Original Top Condition
Sorry I forgot to take pictures before I started to show the horrific leather work. What you see here is what was left on the table top after tearing off the shoddy leather workmanship. I have also removed the veneer dividers with a putty knife scrapper that separated the table into different sections of leather. This would have looked awesome with a burgundy leather top don't you think?
What was left was lots of adhesive, faux leather material backing, and finish lines where the top veneer dividers were.
Where do we go from here? Trash it or Create a Treasure?
Step 3: Remove Adhesive
First thing I did before working on the top was remove it from the legs. This proved to be a great idea that allowed me to work with only the table top very easily. This top came off easily with removal of 6 wood screws.
My first idea was to see what an electric sander would do with a 80 grit sandpaper. Immediately I found this would be a waste of time and energy as the paper was just getting gummed up with the old adhesive.
After research on adhesive removers, there were many suggested. While it was not one of the remedies that I read about, I went to my own cabinet where I found some Goof Off.
Goof Off worked great to remove the adhesive and grime in the drip trough of the table.
I simply used a rag to apply the Goof Off in a circular motion while continuing to use a clean part of the rag. After about an hour of continuous application and wiping the adhesive was removed.
A small nylon brush was used to remove years of grime collected in the drip trough.
Step 4: Sand and Fill
My next step was to try to sand out some of the imperfections in the table top. I wanted to be sure I had a nice smooth surface to work with when applying the pennies to the table to keep them all flat.
As you can see from the pictures, the center veneer ring was glued pretty well to the top. Upon removing the veneer I damaged the wood. Bummer!
- First thought was to take some 80 grit (course) sandpaper to sand out those areas. The damage was too deep so had to fill them.
- Next filled the low spots with some stainable wood filler.
- After filling the gouges, sanded the entire table top and bottom side with 80, 150, and 220 grit paper. This combination removed original finish easily. But you could still see the marks where the old veneer once was.
Step 5: Stain and Finish
Since the legs of the table were in near perfect condition I had saved some work on refinishing, but needed to match the stain color for the top. I took the legs to a local paint store where they were able to create a very close matched stain color for the top.
Process below was done to both top and bottom sides of the table top.
- Apply a coat of stain with clean lint free rag.
- Wipe off excess stain.
- Stain also hid the veneer lines.
- Let dry for 24 hours or whatever is recommendation of stain manufacturer. I used an oil based stain.
- Apply a clear coat finish of your liking. I used a water base satin clear coat.
- Let clear coat dry for recommended time by manufacture, then sand lightly with 220 or higher grip paper. This will allow for the next coat of finish to be even.
- Use damp cloth or tack cloth to remove sanding dust.
- Apply 2-3 more coats of clear coat to both sides.
- While letting the last coat dry, you can get started prepping your pennies. Pennies will need to be cleaned and let dry.
As always, be sure to read and follow the directions of the manufacturers when using stains and finish coats.
Step 6: Cleaning Pennies
Make your Pennies Shine!
Before cleaning pennies, I did a dry fit of pennies on the table top to estimate how many pennies I would need to completely cover table. My estimate was about 800 pennies.
For this step, have all your materials handy as you will need to work a little on the fast side.
- Gather your pennies. Again, the dry fit step should be followed so that you do not need to go through this process of cleaning more pennies later to finish your project.
- Place a couple handfuls of pennies into a clear jar.
- Cover the pennies with Tarn-X or some other patina/tarnish remover.
- Stir pennies to ensure Tarn-X works on all the pennies.
- As soon as you see a shine on your pennies, rinse the Tarn-X off.
- Repeat process until all pennies have been shined.
- Let pennies air dry on a dry towel.
NOTE: Do not over clean/soak the pennies. You should only have to let the Tarn-X work for about 1-2 minutes while stirring. Actually you will see immediate results as soon as you pour the Tarn-X over the pennies. Longer than 2 minutes of cleaning will create discolored pennies, almost a tie-dye of reds due to the metal composition of newer pennies that contain less copper than older pennies. Work quickly to get the Tarn-X rinsed off as soon as you see pennies shine. This will stop the process of the Tarn-X.
Step 7: Glue Pennies to Table
Going back to my penny estimation, I figured out that the penny size would not allow for perfect placement of pennies without making some cuts to some pennies. So with that said, there will be some penny trimming to make this all happen.
- Find a place that you can work comfortably for a few hours. Gluing the nearly 800 pennies took about 3 hours.
- Create a penny pick up tool. Found this little technique on another instructable. I used painters tape over a pencil with sticky side out to pick up pennies, apply glue, then set on table. About half way through the project I had to apply another piece of applicator tape.
- I used about 7 tubes of crazy glue. All you need is one liberal drop on each penny, but 800 pennies is a lot of drops! Home Depot sells 4 packs of crazy glue for less than $2 in my area.
- Pick up penny with penny tool then add one drop of glue to penny.
- You have about 1-2 seconds to get penny exactly where you want them before the glue dries. Little room for error when applying the pennies.
- Apply to table. And repeat around entire table.
Once you get to the end of a row, unless you are really lucky, chances are the last penny will not fit perfectly to complete the row. Trim it!
Trimming Pennies
- Place penny in vice.
- Use small metal cutting wheel on Dremel or similar tool to cut penny to size.
Stagger your cut penny placement. Every row on my table needed a cut penny. I always planned so that the next cut penny would be on the opposite side of the table from the last. Continue steps above until you cover entire table with pennies.
Step 8: Glaze Prep and Application
There a many Glaze products on the market. I used one that can be found at Home Depot for about $25 for my project.
- Purchase glaze solution. Many products are available that can be found at craft stores and the big box DIY stores like Lowes and Home Depot. I purchase mine from Home Depot.
- Read and Understand the directions from the manufacturer. Once you start working with this stuff, you really have little to no time to adjust your process or work space.
- Get all your tools and work space ready so that you can go from start to finish with no hitches.
- Place your project LEVEL. Do what you can to make your project as level as possible. The glazing is somewhat self leveling and will move with gravity. So and uneven surface can leave undesirable results.
The glazing is a 2 part solution. One part is the clear resin, the other is the activator. Once the two are mixed the activator begins the hardening process.
- Use calibrated measuring cups to use equal parts of resin and activator. Or whatever your manufacturer advises. Based on the size of my project I estimated 10 oz. I intentionally overestimated to ensure I would have enough to cover in this one time application.
- Pour resin into the activator.
- Stir for at least 3 minutes.
- Pour solution onto the penny table top starting from the center and working your way out to the edges.
- Use squeegee to work out the coverage and get an even coat.
- Use heat gun to work out bubbles from poured glaze.
Use heat gut at low heat about 12-18 inches away from project while constantly moving the gun to avoid rippling or burning the glaze. Stop using heat cut as soon as all bubbles are gone.
- Let set for 72 hours before handling.
Step 9: Fix the Oops!
So, in my last step I emphasized being certain that your project is level as the glazing will move with gravity! I swear I really did this!
Something I forgot about with this table, either by design or time, it did not have a flat planed surface! The table was either bowed/arched by design or had warped over the years. FYI.. this table is about 50 years old. So after walking away from the project to let the glazing cure, the glazing moved to the low points of the warp/bow. This left two spots where glazing was not as thick in the drip trough of the table. Or the high points of the warp/bow. Therefore, when I returned to check the project I notice the uneven coverage and table top was "glued" to the work surface.
After prying the table top off the work surface I had a little repair to do.
Used a razor to cut back the flaking area where table adhered to the work surface then used a fine sandpaper to feather the edge of the glazing. Since the blemish is on the underside of the table top, good enough for us. :-)
Step 10: Replace Top
After repair was made to glazing drip, I turned table over and replaced legs with the original 6 wood screws.
Step 11: Done!
Overall a very satisfying project. What nearly ended up in the trash has been turned into a treasure. Would be interesting to find out which of my two children inherit this.
Step 12: Spare Resin Glaze
Since I over estimated the amount on resin, I had a couple ounces left in the cup. I placed a handful of pennies in extra glaze. Still waiting for it to completely cure as it is about an inch thick. Hope I can cut the cup away from the glaze.
Look forward to any comments or questions. Really was a cool project to turn something that has been trashed into treasure. VOTE if you like it!
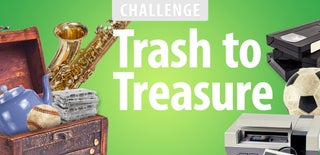
Runner Up in the
Trash to Treasure Challenge
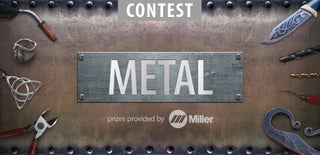
Participated in the
Metal Contest 2016