Introduction: GrappleWave2 Large Scale 3d Printing Using Formed Wire
This is a follow on to my prior Instructable about this idea.
The Big and Small contest inspired me to share more about this invention, what it is, what it can do, and how I made the prototype parts.
The relationship to size comes from the extreme scalability that this form allows. I have made the first prototypes from .030" (.79mm) wire but I would estimate that this shape could be applied to wire from 1/2" (13mm) down to .001" (.03mm) this would be an estimated 500 fold difference in wire diameter that could be utilized.
The micro scale would be envisioned for critical custom shapes such as surgical stents or micro prosthesis.
The large dimensions would be applicable to buildings and bridges.
What is small is the basic concept: A fastening technology based on one shape and one connection.
What is big is the infinite array of shapes and sizes that this can be used to create.
Attachments
Step 1: Understanding the Form
For me the holy grail of design now, apart from information architecture, is large scale 3d printing of metal.
Most existing metal printing is limited to very small, very expensive parts. One emerging technology has been used to create bridges and art forms, but requires the metal to be melted in place in a slow, energy intensive process.
What this new idea allows is the rapid creation of steel truss forms without any lost curing time. Thus the process can proceed as fast as the print head can form the wire hooks. This would be done by a machine similar in speed to a sewing machine, only the wire is bent instead of thread. Like a sewing machine, the process allows the continuous use of the source material, with wire hooks formed instead of threads tied. The various geometries are obtained by simply varying the length between
Secondary operations could include spot welding the joints and adding various coatings to the mesh, such as concrete.
The core concept is a formed hook, made by deforming straight wire into a form that can snap into place on an adjoining wire. The hooks are arrayed in opposing pairs at regular intervals. The hooks are formed to snugly engage the straight wires with a built in preloaded spring to retain the form. Detents in the straight wire would ensure exact registry prior to welding or adhesive coating.
The webs are thus able to be snapped onto the straight wires, using a ratio of 2 webs for each straight wire, any number of trusses can be conjoined together to form panels of any number.
Step 2: Using CAD to Visualize the Initial Concept.
Initially I drew the parts in 3d cad and this allowed me to visualize the ideal form for the wire to be bent
Attachments
Step 3: The Prototype Array
The first photo shows the original prototype I bent by hand from wire.
The rest of the photos show the second iteration of attempting to make the prototype using the device describe below.
photo two depicts the 2 web one straight wire initial combination.
The third photo shows how the new combination is added to the existing trusses.
Subsequent photos show the completed project.
Step 4: Making the Prototype
The first ones I made were by hand and not regular at all, so I set about to make a tool to form the hooks evenly, if still somewhat slowly compared to what a production device would need to do.
I used the vice and chuck of my milling machine to position the tools, and the hand downfeed to press the part, closing the wings with my hand.
The first photo shows the mounted forming tools, the second with the wire initially captured, the wings then close and the press comes down to form the hook. These are nowhere as regular or as quick to form as I would like, but they demonstrate very well the proof of concept.
Step 5: What's Next
Technically, the next step for me would be to create a roller based prototyping tool that would quickly spit out very regular webs, and thus allow for the construction of straight trusses and flat panels.
For the development of the concept, I am looking to involve interested makers, industry and academia in moving this from prototype to product.
The final shots I took of the Watts Towers built by Simon Rodia, always a great inspiration to me as a maker, by a man who had big ideas and made them real.
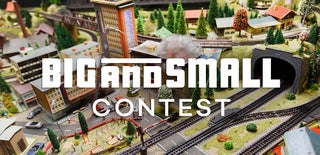
Participated in the
Big and Small Contest