Introduction: Guitar Tube Pre-Amp From Broken Audio Gear (JCM800 Circuit)
The situation:
Vaccuum tubes enjoy an extremely high reputation among audiophiles, audio engineers and musicians, but probably even more so among those who want to be. Some years ago, Behringer made the dream come cheap for the engineers, creating quite a hype about tube microphone preamps. As the devices are not as reliable and useful as we hoped, there must be quite a pile of old, broken, bad and abandoned gear waiting for you to salvage their juicy parts!
The end product of this Instructable:
We are going to build a guitar pre-amp, entirely from tubes, no semiconductors. The circuit is from the Marshall JCM800, one that is loved by many for the sweetness of its overdrive tone, at least when pushed by a boost pedal.
Omitting semiconductors was not an ideologic decision, however. At least some form of current amplification would allow you to plug in passive speakers like headphones. But the housing turned out to get smaller than hoped, so there was literally no room left for luxury. Now you need to plug an active device to the output, say like active PC speakers, an IR loader or other pedals, and/or a power amp for driving an actual guitar speaker.
Now tested: You can actually hear the signal in headphones, but the volume is really low.
Also the treble/mid/bass EQ ("TMB tone stack") was replaced by a single high pass capacitor in order to get around the potentiometers' space demand.
_____________________
You want toplay this amp but not build it? Guess what! The good thing about today being 2023 there is a quite usable open source project called Neural Amp Modeler (NAM) - Download here as a plugin or standalone and turn your PC into any amp. Download the models I trained to try this very amp build through a few settings by just a few clicks! Feel free to also try all my NAM models or search the wide web for tons of more user trained models. Let me even help you with a few guitar cabinet IRs I recorded for another Instructable.
_____________________
Please don't be fooled by the tube hype...
...and dont believe anyone without experiencing their evidence in the form of listening samples. People can seem to be very knowledgable when in fact they are just repeating complicated words from where they read them without verification.
Watch this extensive amp circuitry test by Jim Lill, there is nothing comparable. This video comes some 50 years late in my opinion, but now that it's there, it should be compulsory to understand for every single electric guitar player as well as audio engineers.
Still, much like the vinyl LP is still around, vacuum tubes have their very own vintage charme, glowing and heating - you can really feel and even smell them do the work, not only hear it.
Voltage Warning!
Please mind that vacuum tubes use elevated DC voltage (200-300VDC). Using DC/DC step up modules removes the dangers of high AC voltages, however the necessary DC voltage can still be enough to stop your heart and kill you if unaware or ignorant of safe handling requirements.
Please stick to well established safety codes:
- If unexperienced, seek guidance by a person well experienced with high voltage handling.
- Never be alone when working with high voltages - irrespective of experience level. When someone sees you getting a shock and cramping so you cant let go, they can disconnect power and take 1st aid measures if necessary. Be sure they know what to do.
- Always have easy access to emergency-power-off measures
- Never touch a live amp's interior. Always power off and discharge capacitors in a controlled manner before working on the circuit!
- If working on a live circuit is inevitable, use 1 hand only! Current needs to flow through your heart in order to stop it - prevent that by not offering that route of current flow.
- Wear shoes with rubber soles to prevent a hand-to-feet-via-heart route.
My story:
Back in the late 2000s I fell for Behringer's tube microphone preamps and bought one of each:
- Behringer tube ultragain mic200
- Behringer tube ultragain pro mic2200.
But the first got really noisy and unreliable over time and the other stopped outputting any audio after some years. Haven't really ever had an actual application for either, to be honest, but they helped me understand stuff and let me experiment with things a lot.
Only recently I noticed the tubes inside both were actually type 12AX7 (equivalent to ECC83)! Just the same as a variety of really sweet sounding popular tube guitar amps* use in their tone shaping pre-amps - then I knew I was in the game :D
*including the Marshall JCM800, whose circuit we will borrow here.
Your chance:
You might be lucky to find other dead-cheap broken or abandoned gear with alibi-tube-circuits off ebay or other forms of used market. Their hypey popularity from then should now make them a prosperous source of symmetric XLR and 6.3mm (1/4") jacks, some potentiometers, interesting housings and, of course, tubes!
It might be difficult, but necessary to identify the tubes used in low priced, devices before purchase, however.
Personal Computer Power Supply Unit (PC PSU):
PCs get outdated or break at times.
For those times where a vital PSU remains - even if it's hilariously underpowered with respect to modern PC power requirements - what you are holding in your hands might still be a highly valuable resource for electronics projects! Especially its +12/GND/-12V outputs are very useful for symmetrically powered audio applications, but with all the other outputs you also have a really versatile power supply for a broad range of needs.
You can use yours or a dead cheap one to power this project without any mods. Still, punisher_1211 authored an Instructable giving you important Information and even made his look pretty fancy. Be sure to leave the full 20 pin ATX connector, or at least have the +12V, GND and -12V Pins accessible!
Supplies
Apart from...
- 2-3* salvaged 12AX7 / ECC83 tubes (or devices to salvage them from - *3rd one is optional and can also be of higher frequency, lower gain type*) and
- power supply,
...you will still need some:
Additional components - some of which are *optional*:
- 1x 12VDC to 300VDC step up module (mine is actually only 230V, but seems to work)
- 2-3*x tube sockets with mounting ring
- 1x 20 pin solder strip - more and bigger would be better, however.
- 2x MOhm potentiometers (original schematic says 1M, mine are 2.2M)
- 1x *2-channel double-throw switch
- R's, 1W:
- 2x 10k 1W
- 4x 100k 1W
- *1x 220k 1W
- R's, 1/4W:
- 1x 10k
- 2x 68k
- 3x 470k
- 2x 1M (*one of those is optional)
- Trimmers, set to (values in brackets):
- 1x 1k (820R)
- 1x 2k2 (1k8) *this belongs to the optional boost tube
- 1x 5k (2k7)
- C's (must be 400V rated, axial types would be best):
- 1x 100pF
- 3x 470pF
- 1x 1nF
- 3x 22nF (*one of them is optional)
- 1x 220nF
- 1x 680nF
- 1x 1uF
- 2x 47uF
- 2x Input &output jacks (one each)
- 1x 20 pin ATX connector, or other power supply connector
- 1x Heat-insensitive, insulating board to mount tube sockets on
- wires
- Insulation layers
- Screws
Tools & other supplies
- Basic electronics equipment like
- multimeter
- soldering iron, solder, flux,
- pliers
- cutting pliers
- heatshrinks, insulation tape
- drill press / electric drill
- step drill head, various sized drill bits
- angle grinder or rotary tool, in case even hand tools for metal crafting
- Hot glue gun & hot glue
- Spray paint:black, gold, and transparent if you plan on mimicking my paint job
- active speakers for testing
- guitar and cables for testing
Skills
This is not a beginner project. I need to assume some basic skills in electronics, like...
- Acquiring, reading and understanding datasheets
- Finding a layout from schematics - I will give you mine but you can do better for sure!
- Soldering. The joints do not have to look pretty, they need to be reliably functional.
- Applying heatshrinks and insulation tape
- Somewhat faithfully estimate space requirements before choosing a housing
- Using drills and grinder power tools and/or saws on metal
- Mounting tube sockets
Step 1: Salvaging Tubes From Broken Tube Audio Equipment
Having the tube devices in front of you, the actual salvaging of the parts is rather simple. Even Behringer's devices are built to be servicable, and service personnel work time is expensive. Hence screws are accessible and dismantling procedures can usually be worked out even by a beginner (I guess). Sorry there is no actual photo-documentation of this step as by that time I didn't plan on releasing an instructable on that.
- Do not use excessive force, as not to break the glass tube or bend the housing, and you will be fine.
Some helpful advice I learned slow and the hard way:
- Make sure the first thing you do is take off the rotary knobs before pulling out the user interface board.
- Remove easiest accessible parts first, even if you dont need them. Having nothing in the way might play a critical role in getting out the larger parts later!
- Mind wires - if there are more than 1 board in the case, those are usually connected with multi wire cables
- Some of them might have connectors and you can unplug them.
- Others might be out of the way once you simply sort all the wiring in the case
- Again, others are hard soldered and hard blocking your work. Dont be afraid to cut them. The primary device is of no use already, right?
- The tubes themselves tend to have a rubber/metal mounting thing at their tip. This serves 2 tasks:
- Fix the tube against shock/inertia induced movement
- Reduce tube microphony (you can hear it in the output signal if you tap your fingers against the glass body).
But for us, these mounting things are just in the way.
- Remove them with greatest care, as damage done to the tube here will make it useless
- Once you have free access to the tube*, gently rock it back and forth, pulling it from the socket.
- !! Make sure there is nothing in the way in the direction of the tip - if the tube comes off the socket as a sudden surprise, you might slam it into whatever is in that direction. Don't break it in such an embarrassing way !!
- *Best practice will be to remove and disconnect the assembly holding the tube from everything else before grabbing the tube.
- Once "liberated", store the tube in a place that secures it against mechanical shock, falling to the floor, hard objects, etc.
- If you plan on using the housing, get everything out of there.
- If you plan on salvaging components soldered to the PCBs, there is a ton of instructables on exactly that. (Un?)fortunately, the approaches diverge very far. What helped me the most in the past was the one by geotek.
Potentiometers, switches op-amps, LEDs, Capacitors, transformers, power electronic components, etc. can be valuable rewards from that source.
Step 2: Tubes Datasheet Research
Once you freed the tubes from their questionable circuit, you need to test them. To be able test them, you need to know a few things about them. You can destroy them before first use if you don't.
There are a few bits of key information from you tubes' data sheet:
- filament voltage (can you supply correct voltage to your tubes?
- filament power/amperage might matter if you fear your supply might be too weak.
- the pinout pattern is something you must know under all circumstances!
- µ value (amplification factor) should be similar to that of the 12AX7/ECC83 if it's not exactly that type.
- curve plots are interesting to look at, important only if you're not sure whether your tube is compatible to be used in the circuit.
Knowing those, you can skip to the next step.
Most probably you are dealing with 12AX7 or their 1:1 equivalent: ECC83. There is also a possible Soviet replacement: 6N2P - or at least new-old-stock shops claim it to be. These have different pinout pattern, however!
If you learn that one of yours is an ECC82 or ECC81 (12AT7 or 12AU7), those are very different devices. They are capable of high frequency (HF) amplification, but offer less gain and are said to sound "colder" (more treble, less mids), even, or maybe especially when pushed to higher gain. Those are still very useful in the buffer stage, but there still are 3 other stages where 12AX7/ECC83 are important. So you still need 2 double triode 12AX7/ECC83 vacuum tubes to have enough of the correct type for the critical stages.
My design suggests to use 1 other tube for the buffer (mine is a super cheap UCC85 HF double triode from a local electronics discounter), so I have one more "true 12AX7 triode" system for use as an optional preliminary boost stage. But more on that later!
Step 3: Testing the Tubes' Working Order
Before piling up exaggerated euphoria about building a tube amp, you need to verify the tubes you just got from used equipment are actually OK.
First thing you need to know is the pinout. You think you have seen the pinout in the datasheet - well I hope you have - but personally I tend to get confused whether the pin chart is seen from above or below the part, which effectively mirrors/reverses the pin order.
--> Solution: Essentially all interesting tubes will have their filament between pins 4 and 5, often also involving pin 9. The filament is the only part of the tube where you can measure something without any other voltage applied.
Filament resistance value should be some 10's to 100's of Ohms. Occasionally even below 10.
Can be substantially lower than stated in the datasheet, as the paper values might be warm, steady-state values, while the resistance is less when the wire is cold.
- Lower single digit ohm values could indicate a faulty (shorted) filament, hence a bad tube.
- kOhm values are very high for filament wire too. Probably a bad one.
Once you found the filament pins, take the time to draw a 3D sketch with pencil and paper to make sure you have a definitive reference to the correct pin order!
Try applying datasheet specified voltage across the filament supply pins. Polarity does not matter, it really is just a heating wire. Well, actually I'm using 12V instead of 12.6V - thats not datasheet spec. at all, but close enough to work for my ears ;)
A soft reddish, up to at times bright orange glow should be seen after some seconds' time if your room is dark.
The photos also show purple-ish colors, that comes from the amount of infrared radiation that is emitted by the filament, but not removed correctly by my camera's infrared filter. "Purple content" might increase over on-time, as does the temperature.
Some tubes, including the UCC85 give a bright flash when cold starting the filament. There is no word about that in the datasheet and people in forums say thats perfectly normal. It happens every time I cold start the amp and I have not had issues with it yet. Not fully convinced, but at this point, I make myself believe its OK.
Once the filament seems to be working, try soldering a test circuit like the one indicated by the schematic (PDF or later pictures) in this step.
- Use a 100k 1W resistor between anode and positive high voltage supply pin.
- Be sure to have no voltage applied when putting the circuit together. Take safety measures to not accidently touch the anode or anode resistor potential when switching on the voltage.
- Make sure you have a 400V rated coupling capacitor off the anode and a 470k pull down resistor after it.
- Do not use passive speakers, not even headphones! You will not hear much, probably nothing at all, as you expect the tube and anode resistor to allow more current flow as they ever will.
- Better use an old active system, one that you wouldn't mind (too much) if you blew its inputs.
- Use like 1 to 3 kOhm bias resistor between cathode and ground, bypassed by a large (several hundreds nF) boost capacitor.
- Pull down the grid with a 1MOhm resistor and connect the guitar signal with 68k (or similar) in between.
- Make sure to connect the full setup before switching on the high voltage.
- Probably, soldering jacks is helpful - crocodile clips do the job too, but are more dangerous to slip or snap off and short or expose potential to unintended places.
- If you are sure you are ready, guitar feeding the test circuit, circuit feeding active speakers, try switching on the filament and when you see the glow, also the high voltage supply.
- Start playing - do you hear yourself?
If not:
- Is the guitar poti knob at non-zero?
- Are the speakers on and volume at non-zero?
- !! Please think twice before touching the live circuit if you still dont hear anything !! When in doubt, power off the high voltage, check with a multimeter that the supplied "high" voltage goes below 20V before checking the jack/plug or crocodile clip connections!
The optimum will be to test all the channels of all your tubes.
Maybe you can spot some channels having higher gain (hear it louder) than others, thus you can optimize, which channel to use for which stage in the amplifier circuit.
Attachments
Step 4: Schematic & Layout
Let's take a moment to decide on what to do with the tubes.
There is a very popular pattern of "high gain" tube amp schematics shared by several sweet sounding commercially available amps (Marshall JCM800, Soldano,...)
We will borrow this and implement some modifications suggested by Y. Blais, as read on Rob Robinette'stube overdrive info page. Most prominently: the optional, additional "0'th", "pre-pre-amplification" or "boost" tube.
This stage, I took from a schematic I found for the Hughes&Kettner Tri-Amp, which uses 2 tubes before the cold clipper, as the mod suggests. However, with the switching, the gain pot comes only after the 2nd tube, which is problematic for stability, as you can hear in the demo.
Anyway, lets get to business:
You find the schematics in the pictures, as well as a PDF for download.
Also, I tried to draw the last valid version of my solder strip layout, including wire connections. It has not gotten way too pretty, I'm really sorry.
The photograph of my real soldered circuit should serve as a warning - this is what it might look like if you apply insufficient wire management!
Attachments
Step 5: Preparing Hardware: Housing, Tube Holder, Solder Strip, Insulation, Drilling Holes, Cutting Slit, Removing Features in the Way
Now you know your tubes are working. Theres not much to fear then.
However, a working amplifier isn't all schematics and theory, its made of real components that need real space, some of them need to be mechanically functioning, and ideally also easy to access and operate, and none of the conductors should accidentally collide.
Also, assembly and maintenance should be possible, if not easy to do. So take a few minutes and try to imagine, which parts would go where and when in the assembly process.
How knobs go past each other and no pin collides with another one or the housing walls.
If in doubt, opt for a larger housing - space is always short, especially if you are an unexperienced and/or optimistic planner.
Tubes get hot - they should be placed away from the actual circuit board. That's more relevant if semiconductors are present on the board, but still is good practice.
However, this demand asks for a ton of wiring to connect the tube socket pins with the circuit board.
The tube sockets should be mounted on a sturdy, insulating plate that is insensitive to heat. I went for wood, but acrylic glass should be ok too. Best might be PCB material without any copper on either side. Many work with metal plates, but I learned to dislike their conductive nature...
- Make sure you find a way to mount your tube sockets on some sort of such plate and the plate inside your housing - in a way that promotes airflow for heat transfer sakes.
I went for tubes that come out of the housing's top plate, like we see in Hi-Fi tube amps. Not recommended for band rehearsal or even live rigs, but in my spare time I am rather a producer and recording artist, so its fine for me.
- Once you know where the tubes go, drill the holes as needed.
- Recommend a step-drill on a drill press with a
- step drill - smooth and easy and yields fine results.
- Tubes are about 25mm in glass outer diameter. Drilling 28mm holes will be fine to stick them through and also be able to change them from the top side.
- Be accurate with the holesfor the sockets in the holding plate, their diameters might vary from piece to piece, but usually don't have much tolerance
- Also, figure out an interface pattern to hold all potentiometers, jacks and switches.
- Mind the space needed for the knobs and the ergonomy of their operation.
- Drill holes as suitable.
If you seek to use a PC PSU as a power suppy without heavy modding like me, you will need a
- 20 pin ATX socket through the backside of your housing (24 pin is ok, too).
- Prepare to cut a slit that will hold the connector.
- I used an angle grinder, which is a rather coarse instrument, but it might have taken substantially longer if I had used a rotary tool or hand tools.
- Better cut it just a tiny little bit too small and file it up a bit. If the housing can hold the connector in place by some force already, then the hot glue is not strained that hard trying to keep it in place.
- My best bet for locking the atx connector in place and filling the gap is hot glue.
- "Glue" is not necessarily the best term, however, as the "hot gluing" procedure for metal parts almost fulfills the requirements for calling it "soldering".
- If the glue is hot, that does bot help you much, as the cold conductive metal walls will cool the glue before it can actually stick to the surface.
- You need to heat up the metal surfaces so the glue stays liquid enough there to bond with it.
- Thus my procedure:
- apply some glue as you would normally.
- you can carefully heat the metal parts with a small, lighter shaped butane torch, but better would be a hot air gun.
- Stay close to the glue blobs, but heating the zone around them can help, too
- Be careful not to burn anything non-heat resistant, like rubber device feet or the plastic of the connector.
- Heat it until you see the glue melting.
- stop for a moment and see whether the glue stops melting soon or if there's excessive latent heat stored, causing more and more of the glue to melt. If this gets out of hand, glue can get too liquid and begin to flow away.
- start heating again whenever you feel like it's appropriate. Apply more hot glue as needed, to fill gaps and complete the bonding
- observe and control the cooling when you feel there's enough glue and it has bonded well to the metal surfaces
- Mind the size of your solder board and imagine adding space of larger components on top and to all sides. Always add more than you actually expect!
- Find a way to fix that board in a place where it neither collides with interface components, nor with the tube board.
An important topic regarding user safety, but also influencing working order, debugability and noise characteristics is the electric potential of the housing.
- If you opt for a metal housing, you need some way to make sure that
- touching it is not dangerous under any circumstances. A way to provide that safety is to
- connect it to the GROUND pin of the high voltage supply. If the positive potential via any route ever touches the housing, the short circuit protection of the step-up converter will cut the power.
- The high voltage ground is also the ground of your signal circuit - thus grounding the housing like this will effectively shield the circuit from outer electric fields, potentially reducing noise.
_________________________
- Signal-wise, a non-grounded housing is just a cage-shaped antenna.
- Safety-wise, it is an electrocution hazard.
- Just ground it already!
_________________________
Another safety measure to reduce the risk of any unwanted potential ever touching the housing is to
- insulate everything. Seriously,
- use large heatshrinks or insulation tape to cover all jacks, potentiometer lugs and switch bodies. Wait until you soldered and tested them in the circuit, however. So you know they do work as intended. Debugging work
- Even more importantly, insulate the interior of the metal housing. Use tape, thin polymer sheets, cut-out PET bottles... whatever works for you works.
Step 6: Wire Management
This step is intertwined with the next one, as the wiring is also an internal part of the signal circuit. Make sure you constantly check both, circuit correctness and tidy wire routing.
Still, even before caring about the circuit, you will do yourself a favor planning the space where all the wires might go.
We got to see the need for plenty of wiring between the signal circuit and the tube holding location.
- Consider all the wiring needed with suitable wire core cross section and
- try to imagine, which wires to solder first and which last.
- Make them short enough for the space availale to handle the mass of wires inside - but also long enough to enable assembly and maintenance.
- Try to group them, for instance use same color for all wires that go to
- tube grids, another one for all
- anodes and a third for those to the
- cathodes,
- while zip-tie grouping each tube's wires into an easily recognizable bunch.
Take my photos as an absolute worst case scenario, I learned the above also by making mistakes in my build ;)
Also interface devices as potentiometers, switches, jacks and the ATX connectorneed to be wired. Try to find a meaningful pattern there, too.
With the ATX connector, make sure to solder the right pins. connect the PSU to have a definitive wire color reference, but do the soldering only while the PSU is inactive!
- Verify yourground goes to a black wire on the PSU side
- Measure the voltage of your +12V pin. Don't panic if it's just 11.8V or even a bit lower, thats ok. But be sure about correct polarity / direction of current flow.
- Solder-short the green wire's pin to ground. This is the ON-switch, it needs to be that way constantly to keep the PSU actively supplying the voltages.
!! Sometimes the colors of +12V (usually yellow) and -12V (usually blue) are swapped!!
As some power is needed for the filaments, I strongly suggest going for the GND / +12V, not the negative one - the power rating is way weaker for the latter.
- Whenever you are about to solder a wire to another conductor, ask yourself, whether a heatshrink or tape could potentially prevent incompatible conductors touching, e.g. when closing the housing.
- Apply wherever it is suitable to let safety go ahead of ease of maintenance.
Further advice on wire routing can (should?) be sought in this video by an absolute DIY gear specialist.
Just a pity I came to know and appreciate it only days too late. The full-blown chaos you see in the pictures had been created already.
Step 7: Soldering the Circuit
Usually I like to assemble a circuit in small bits, say
- solder the first amplification stage,
- then test the first amplification stage, and
- proceed alike with all others.
This way you catch problems early and before the board is too populated, leaving you the room for debugging and corrections.
The concept of solder strips was new to me, however, and I found the assembly to be easier all the way at once. You find the schematic, my soldering plan and pictures of the assembled board here - feel free to find a better layout, however, I bet you easily will!
Be mindful wherever you can place component in a space-economic way. Keep in mind:
- The circuit will have to fit in the housing in the end. But also,
- don't overdo it to the point where accessibility suffers too much. You might want to mod things later or need to debug it.
Be cautious with naked conductors sticking out, possibly touching each other or the housing if moved for case assembly. Murphy's Law: "if it can go wrong, it will..." applies way too often in real life.
When you're done:
- Double check whether you forgot something.
- Consider wiring up audio jacks to be able to test the circuit - its ok for now if its not the final installtion.
- Connect guitar and active speakers. Begin with low volume, if you have neighbors ;)
- Connect filament supplies to see if these are working
- Connect the high voltage supply module and check, whether it does supply the voltage.
- If thats ok, be sure there is no potential on the audio jacks. Measure their voltage against GND
- Only then, check if you hear anything. Start with guitar knobs and gain knob full up, take turns slowly raising the volume knobs of the pre-amp as well as the active speakers - until you hear yourself playing.
- You can also leave the guitar unplugged and the cable floating. Then you should hear a very prominent distorted mains buzz.
- Try grabbing the cable's isolator. You might hear a difference only by the change in dielectric material that is you hand now instead of air.
If you can't hear anything, make sure to have a wholesome debugging plan:
- Did you forget any knobs inbetween that could be at zero?
- Are the cable connections ok? !! Do not touch them live !!
- Cut the high voltage supply power and do monitor the voltage go below 20V.
- At times, connectors are loose and need to be bent to assure the connection.
- power up again, you gear anything now?
- If negative, check the bias (=cathode) and anode voltages. First should be in the range 1-4V, while the latter should be around 50-150V. The buffer stage is an exception.
- If those are ok, the signal must br getting lost somewhere inbetween. If you are lucky to have a oscilloscope rated for the voltages occurring, put it to good use probing the signal path of the live circuit.
- Have the guitar cable floating now. This way, you have a hands-free, constant loud buzzing noise that should be measurable anywhere
Step 8: Housing Paint Job
Clearly, the original Labels must disappear, they are distracting and not something you want to see when you are dreaming of a beautiful tone.
Before applying any paint, take a moment and decide whether there is a feature you want to protect from lacquer spray. If you already glued in your ATX socket, that could be one such thing. Mask it with an easily removable tape.
Black labels will be easiest removed
- spraying over with black color.
- Let dry thoroughly.
I wanted to give the pre-amp a "gnarly", "hot-rod" kind of look, so I did a
- quick, to say really really short dash of spray from a gold spray can, at a quite shallow angle from the left side.
- Repeat until sastisfied.
- Wait until completely dry.
Last, I wanted some protection to not accidentally scratch off the paint, thus,
- thorough spraying with clear lacquer
...was my best bet. I did not wait for long enough for the gold paint to dry, thus it partly disappeared into black again. Or maybe it would have happened anyway, but it got darker than intended. Still kind of like the results, although it must be said that the photos look more fresh and colorful than the real life object.
Step 9: On the Mounting of Interface Components
The best interface components are those featuring a spring ring, a disc and a nut.
The procedure with those is as follows:
- Put the spring ring onto the component's outer thread
- Stick the component through its hole in the device wall
- Add the disc
- Fix it with the nut.
And youre done.
Well, not exactly to be honest. If you have a row or a matrix of interface components to penetrate the housing wall, you do yourself a favor by
- preparing an additional plastic sheet with the same drilling pattern as the interface wall.
- Stick your interface components through that sheet first
- Then you can put the whole bunch of interface components through the wall all at once.
This way you don't have a hard time sorting out all the wires and it is more clear what is where. Take a look at the pictures and you will see the difference. Further...
- Some of the interface components come without the spring ring - thats the least problem, just omit it.
- Some come without a disc, then you have to be more careful not to scratch the interface surface.
- If there is no nut, then you're - "haha, screwed" - try to get a replacement. If that fails, but you can find out the thread specs and have access to the technology, then you can 3D-print your replacements. But be warned: quite some skill and slow iterative approaching is needed to get the tolerances right on your machine.
- Some components have little noses poking into the wall from the inside.
- If you ignore them, your component ends up awkwardly angled.
- You can use it as intended and drill a little hole into the housing wall, so the nose goes right into that and fixes the component against rotation
- Personally, I tend to break the noses off with pliers, as the squeezing force by the nut is usually plenty enough to prevent unwanted rotation.
Step 10: Finalization, Testing & Having Fun
Now it's about time to finish this - but dont hurry, there still are things that can go wrong. You would be amazed how many of my builds stopped working in the very moment of closing the case.
With low voltage circuits I usually do close the case while the device is running to see exactly where it stops if it does. That is a very valuable help at debugging. However I strongly discourage this practice with lethal voltage setups!!!
Take a very close and diligent look at
- all the components and how they go past each other to fill the space of the case when starting to close it.
- Be cautious whether conductors asume positions you havent thought about before, especially when getting dangerously close.
- Do the wires go past and/or around the components nicely?
- Avoid shearing wires with the case lid
- Avoid squeezing them with excessive force
- --> Tweezers can be helpful guiding the wires where they fit best while the case is almost closed
- Does the case close fully and easily? If not:
- Try to find the source and the
- mode how it prevents the closing.
- Mitigate with tweezers or even a better concept of component fixation within the housing.
- Quickly check working order, connecting PSU, Guitar and speakers.
- Once it works, secure the housing with screws!
Celebrate Finalization!
Play!
Have fun!
Comment, share...
Its a re-use contest, so feel free to re-use any of the wording and material presented in this instructable - but I'd gladly appreciate it, if you added some kind of reference whenever you do. Also I enjoy reading from you if some of it is helpful!
Step 11: Reflections & Suggestions for Improvement
I need to say I am highly satisfied with the outcome of this build. That probably is due to the fact that I did not do much designing work but more copy-pasting from well-established schematics.
12AX7's in a JCM800 circuit truly are a nice sounding combination.
Wait for my Instructable on trying to adapt the JCM800 circuit for the soviet built rod-types 1Ж24Б (1J24B), and you see things can end up quite differently. Actually, I can tease you with a video.
__________________________
Still, nothing is ever truly perfect...
If I were to build this again, I have some points I would do differently:
- Choose a housing that actually and easily can hold all the components needed. That would be a larger one ;)
- Use a step-up-module that will output ~~300VDC as the original schematic suggests
- Add another boost pot to control the amount of boosting by the boost stage.
- Experiment with and choose component values to have more control and more of a mid-to-high frequency boost than the all-the-way thing:
- The boost tube's bias cap (cathode bypass cap)... <200nF?
- The coupling cap between the boost tube's anode and the regular circuit's input (10, 5, 1nF?)
- If point (3) is not feasible, maybe add another fixed resistorafter the boost tube's coupling capacitor, to shift the ratio of the voltage division of the regular input towards draining more to ground, passing less to the input. That is said to be the key to modern high-gain circuits / tone.
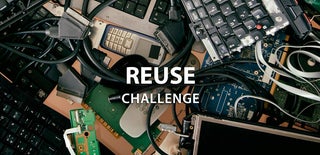
Runner Up in the
Reuse Challenge