Introduction: Hand-crank IPhone Charger
I had always wanted to make something that converted mechanical to electrical power. So when I salvaged a high-torque motor from a broken microwave, I knew exactly what I was going to do with it.
This Instructable details the making of a hand-crank iPhone charger, a charger that operates solely on mechanical energy YOU provide. The build uses a completely original circuit and a design that is sleek and easily portable. In addition, this charger is probably cheaper to build than it would be to purchase a normal wall charger. If you've ever been frustrated about running out of battery while on the go, you've come to the right place! With just a few adjustments, this charger can be used to power not just iPhones but anything that runs on electricity.
Step 1: What You Will Need (and How to Get It)
- high-torque DC motor:
Motors operate on the principles of electromagnetism to produce rotational energy from electrical current. In this Instructable, we will be reversing the motor's inputs and outputs in order to generate electrical potential from mechanical work. The motor I used was taken from a broken microwave, but any motor will work as long as it uses permanent magnets rather than polyphase coils and is coupled to a gearbox with a high torque output.
- step-down transformer:
A step-down transformer is needed to lower the voltage of the sinusoid generated by the motor. Transformers can be found in almost every piece of electronics that plugs into a wall. The precise primary to secondary ratio of the transformer will depend on the voltage produced by the motor you use. In my case, I used a 120:12.6 (approx. 10:1) transformer from RadioShack.
- diodes (x4):
Four diodes (or an equivalent bridge circuit) will be needed to rectify the AC generated by the motor to DC. Diodes are common in electronics, and red colored signal diodes tend to stand out on circuit boards. Since the emf's generated by rotating the motor are unlikely to be huge, signal diodes as well as power diodes are probably acceptable for use. I used power diodes purchased at RadioShack.
- resistors (assorted):
You will need several resistors for the timing and feedback circuitry. You should have no trouble finding resistors in old electronics. The values I used will be listed on the circuit schematic, but minute deviations from these specific values will not greatly affect performance.
- capacitors (x2):
You will need two capacitors: a low value ceramic capacitor for timing and a larger electrolytic capacitor for energy storage. The specific values I used will be given on the circuit schematic. Again, capacitors with slightly different values than the ones listed may be used. Electrolytic capacitors can be salvaged from old electronics with ease. RadioShack sells packets of assorted ceramic and electrolytic capacitors, which can be very helpful if you're just getting started in electronics.
- NPN transistor:
A transistor is used to control charging. Any transistor could work, but for this application a low power NPN bipolar junction transistor is probably best. Such transistors are abundant in electronics. I used a 2N4401.
- 555 timer IC:
A 555 timer is the central component of this switched mode power supply. The 555 will be configured in astable oscillator mode and will drive the discharge transistor with a pulse width modulation (PWM) signal. You will have to purchase the 555 timer from RadioShack (current price $2.00). I would recommend the low power TLC555 over the NE555.
- LM741 op-amp IC:
A LM741 op-amp provides linear feedback in order to maintain constant output voltage relative to a reference. You will have to purchase the LM741 from RadioShack (current price $1.50).
- button cell battery:
A button cell provides the reference voltage used to maintain steady output voltage. Button cells can be found in electronics with timing circuits that must operate even when the device is "off". I used a 3V lithium button cell taken from a radio. If button cells are unavailable, other batteries may be used so long as they do not drain quickly from continuous use.
- USB receptacle:
If you are planning on charging an iPhone or other device with a USB interface, you will need the proper USB receptacle to connects to the charging cable. You can find USB receptacles everywhere in electronics. I extracted mine from a USB port array found on a broken computer.
- housing for the complete project:
This can be anything, a cardboard box or tube for example, so long as it protects and encloses the working parts of the charger. You may also need some nuts and bolts to hold everything in place.
Step 2: Circuit Schematic
Now that you have gathered the required parts, its time to put them together.
The above schematic details the charger circuit. The functional diagram compartmentalizes the circuit and describes how various components interact to produce the regulated 5V output. Note that component values may deviate slightly from those given in the schematic with little noticeable effect on performance.
Step 3: Testing the Completed Charger
With your circuit built, you may now begin charging devices with energy you supply!
To demonstrate the working charger, I made several videos.
The first details the operation and construction of the charger. The second shows the output across a 100 ohm resistor, which is expected to exhibit slightly greater impedance than that of an iPhone. The third confirms the charger's functionality with a demonstration of the charger connected to an old iPhone. The fourth shows the charger powering a rail of LED lamps.
Step 4: Notes on Energy, Efficiency, and "green-ness"
The charger is innately a green-machine. As it relies solely on mechanical power (the button cell sources negligible current), the charger does not contribute any waste in the form of used batteries to the environment. The rotational input of the charger can be coupled to a bike to provide more energy on the go or to a stream to derive energy from nature.
The charger was built from several recycled materials, including a high-torque motor salvaged from a broken microwave and a USB receptacle taken from a USB port array.
After some experimentation and rough calculations, I approximated the charger's efficiency to be 53%. I based this result on the equation for the work required to complete one rotation of the motor shaft. I charged a capacitor first from the USB output of the charger and then directly from the rectified output of the motor. The ratio of the two energies produced by one rotation was 53%.
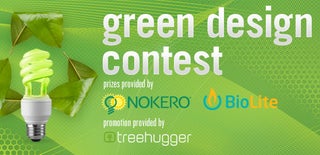
Runner Up in the
Green Design Contest
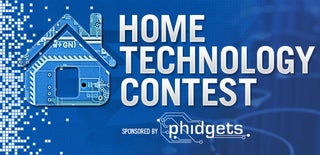
Participated in the
Home Technology Contest
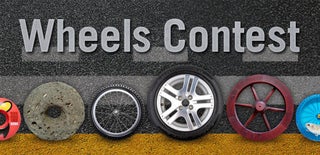
Participated in the
Wheels Contest