Introduction: Hex-House: Affordable Hexagonal Modular Homes
With both the average cost of homes and the poverty rate increasing, affordable housing is more crucial than ever. As of right now, the median home price is $320,000, an outrageous price for a low-wage family. To make matters worse, many of these expensive homes are completely unsustainable. They waste energy, cost excessive amounts to maintain, and at their end of life, their materials are simply left to rot, as they were not designed for deconstruction. Hex-House was designed to solve all of these issues and more and aims to change the housing market forever.
About the Authors
Diego Caples is an eleventh-grade student who attends Well-Trained Mind Academy. He enjoys design, math, and 3D modeling, which he has six years of experience doing. He started to learn how to 3D model, teaching himself with Instructables, after building his own 3D printer when he was eleven years old. He did the all of 3D modeling, structural analysis, and rendering in this project. Lucy Caples is a tenth-grade student who also attends Well-Trained Mind Academy. She has been interested in architecture and design since a young age and has pursued her interests through several architecture, engineering, and design classes since fourth grade. She did the research, interior design, and floor plans, and together they brainstormed the central concepts of the design and wrote the Instructable. They both have had a shared interest in tiny homes ever since they built their own treehouse as children. Over the past several months, their family has been traveling across the United States in an RV. They used their knowledge from their experience of living in a small space to guide their design.
Supplies
See the cost projection section for a detailed list of required materials.
Step 1: Conceptual Overview: Introduction
Hex-houses are hexagonal, affordable, modular homes with exteriors that can be connected in a vast variety of configurations. They pose a unique solution to all of the issues of traditional housing, the lack of affordability and sustainability. It is sustainable because of its resourceful design. Instead of using new materials and producing more waste, Hex-houses are built from previously used but no longer needed materials, such as decommissioned grain bins. Once a Hex-House is no longer in use, the materials that it is built from can easily be reused, completing the cycle of the circular economy. Because Hex-Houses are part of the circular economy, the cost of construction is also greatly reduced. The innovative design of modular interiors and exteriors allows for Hex-houses to adapt to their inhabitants.
Step 2: Conceptual Overview: Single-Unit House
The primary Hex-house design is a single-unit house that can accommodate up to three people with a loft (shown in image two). A low-income individual can buy this house for under $5000. (See image one for single unit top view)
Once Hex-House residents become more financially stable, they can expand their home to fit their personal needs. For example, suppose a resident wanted a larger living room and kitchen so as to better accommodate guests. The issue is that a single-unit house already contains both a kitchen and living room. To add another hexagonal unit with either a kitchen or living room would be redundant. The beauty of Hex-houses is that the interiors themselves are modular. Thus, the current kitchen or living room can be removed and replaced. There are two different types of interior modules: half modules and quarter modules.
The single-unit house is composed of two half modules, a bed and bath module and a kitchen and living space module, that can be removed and replaced whenever the resident so desires.
Step 3: Conceptual Overview: Expansion
Continuing with the hypothetical resident, they could remove their kitchen and living space module and exchange it for a new module, another demonstration of one of the many concepts that make Hex-houses unique. When a resident no longer needs a module, they can return it to the bank of Hex modules and receive a module in return. Their original module will later be used by another resident who needs it.
When expanding to a larger living room and kitchen, another hexagonal unit is added. In the place of the kitchen and living space module, a half living room module is added. In the new hexagonal unit, the half kitchen module is be added, in addition to a quarter office module and a quarter dining room. The result is a larger, more spacious house with an interior customized to the resident’s personal needs.
Step 4: Modular Complications
However, having modular interiors resulted in a plethora of complications. Primarily, if the interior modules were exchanged, the permanent fixtures on the wall such as windows and doors may not align with the interior modules. For example, modules could be exchanged and a permanent front door might lead to a bathroom, and so on. Additionally, there would be no way to add interior entrances to other modules without permanently changing the hexagonal unit. The only solution to this? Exchangeable walls. There are five different types of walls. Most notably, there is a connection wall, which allows for two hexagonal units to easily connect. Inserting and removing interior modules is done through the ceiling, meaning the roof and ceiling must be removable as well. A detailed overview of the roof and other interior structures will be given in the construction section.
Step 5: Conceptual Overview: Why Not Shipping Containers
Shipping containers seem to be the obvious material for upcycled modular housing. While they are common, they are not necessarily the best material. They are undeniably costly. On eBay, a shipping container can cost anywhere from $3,000 to $5,000, costing even more for a seaworthy container (the most desirable when transforming into a house). In addition to the cost, shipping containers are in demand due to the ongoing shipping container shortage that experts predict will continue well into the future. On the other hand, used grain bins only cost $0.20 per bushel, making a grain bin of the required size for a Hex-House approximately $400. They can be used to build the exterior walls. As we traveled through the US, we saw a surplus of grain bins no longer in use. This is partially what inspired Hex-Houses. As to why flatten the grain bin and use the metal to build the walls of a hexagonal prism instead of simply leaving it as a cylinder, having a hexagonal module allows for more possibilities because they can be tiled horizontally and also stacked, unlike with a cylinder. Additionally, hexagons are the shapes that allow for the most floor space when using the least amount of wall material. Another benefit of using a hexagonal module is that each unit truly feels like a room rather than a hallway like with a shipping container home, which would help the house feel more traditional.
Step 6: Sustainability: Circular Economy
In addition to evolving with its residents, Hex-Houses were also designed to be sustainable and affordable. At a certain point, the cost of a house is from the building materials, so to achieve the lowest possible price, the cost of materials must be reduced. It is for this reason, that being part of the circular economy is central to the Hex-House design. Most of the materials used to build the Hex-House have previously served another purpose, such as the exterior which is built from a grain bin. Once a module is no longer needed by a community, the materials can easily be repurposed and reintroduced into the economy. Hex-Houses are built with little glue, and, as many parts need to be removable, are easily deconstructed. Not only are the Hex-Houses' materials part of the circular economy, but the Hex-houses themselves are part of another independent circular economy. Once a resident wants to expand their Hex-House, they will return their old modules and exchange them for different modules. The modules they no longer need will then be used by another person. And the cycle will repeat. This reduces the cost of construction of Hex-Houses and reduces the amount of waste produced.
Step 7: Sustainability: Using Roof Space
Hex-Houses incorporate sustainable designs that increase affordability. We sought to lower the cost of actually living in a Hex-house, in addition to lowering the cost of construction and materials, which is why the roof space is used for a hydroponic garden or solar panels.
The hydroponic roof garden uses filtered grey water from the showers and kitchen sink. Each day, in the average American household, approximately one hundred gallons of water are used in the shower and kitchen sink. Hydroponic systems use only two cups of water per square foot per day. Therefore, there is no shortage of water.
A one hundred twenty-eight square foot space is used for the hydroponic garden on each module. This space is filled with PVC pipe hydroponic modules, each 38.6 inches long. The hydroponic modules are arranged in three rows of three on each hexagonal module.
However, when are solar panels more advantageous than gardens? In a single-module Hex-House, a hydroponic garden should always be built instead of solar panels. A single-unit Hex-House simply does not have the roof space to justify the cost of adding solar. Solar panels cost $4-$10 per square foot, which, in total, considering that rectangular panels could only partially cover the roof, would cost $380-$960 for only the solar panels. This price does not include the cost of batteries or any of the other many components. A solar panel optimally produces 15 watts per square foot on average throughout the day. The roof is flat, far from the ideal angle for solar. In this square footage, the system produces approximately 2.4 kW, which would produce 290 kWh per month. An average American home uses nearly 900 kWh per month. Since the solar panels would not produce enough energy for the house to be off the city electricity grid, residents would also have to pay for the installation of city electricity, solar panel installation, and monthly bills. On the other hand, if this space was used for a hydroponic garden, a three-person family could nearly grow the amount of vegetables needed for a balanced diet. The average family spends nearly 20% of their income on food, and the less money made by an individual the greater the percentage of their income spent on food is. However, in a multi-module Hex-House, a hydroponic garden might produce too much food and require excessive labor. The more modules there are to a Hex-House, the more beneficial a solar panel system would be.
Step 8: Sustainability: Sourcing Water
A hydroponic system uses a large amount of water, although still less than a traditional garden. As previously stated, the hydroponic system uses recycled grey water. However, if the water was simply sourced from city water, then used in the house, and finally used in the hydroponics, it will be costly because of the tremendous amount of water that a hydroponic system requires. To support the hydroponic system and reduce living costs, Hex-Houses required a sustainable and affordable source of water. Instead of using city water, each Hex-House has a rainwater collection system. The rainwater is purified for use in the shower, bathroom sink, and washing machine. Hex-houses are still connected to a city water line because the rainwater is not purified to be used as drinking water. This is because the few methods of rainwater purification that produce white water are extremely expensive. The small amount of water used to wash food, cook, and drink was not enough to warrant adding that level of purification.
In the average household, 24% of water is used for flushing the toilet. In order to reduce the utility bill, there had to be an alternative water source for the toilet as well. Like the hydroponic system, the toilet flushes with grey water; however, the grey water from the sink goes directly into the toilet tank, using a toilet sink tank system. The average toilet takes about 1.6 gallons to flush, meaning a family of three could save around 38 gallons of water per day, thereby saving money and helping the environment.
It is through these sustainable tactics that the cost of living in a hex-house is reduced.
Step 9: Construction: Foundation
While the cost of living in a Hex-House must also be low, the upfront cost must be small to be available to as many people as possible. This is accomplished by using upcycled materials.
All Hex-Houses are built upon earthbag foundations. Because concrete is costly (commonly priced at $5 per square foot, meaning a concrete foundation would cost nearly 20% of the budget) and it also has a negative impact on the environment, it was not the appropriate material.
Earthbag foundations are built using polypropylene bags. The first layer of bags is filled with gravel, while the others are soil-filled. However, in wetter climates, solely using gravel is preferable. Because soil wicks up moisture, it could damage the walls or even result in a collapsed structure after heavy rain. Earthbags can be filled with a wide variety of materials. Whatever is plentiful in the area can be utilized. In wetter regions, materials that do not soak up moisture are more desirable, but, in drier climates, options are more plentiful. In desert regions such as Utah, bags could be filled with sand. In Northern California, a volcanic region, they could be filled with pumice, which is naturally frost-resistant. As previously stated, concrete is a major environmental threat, but it is still constantly used in construction. Consequently, rubble from demolition sites is filled with concrete that will then get transported to a dump where it will sit for years on end. Hex-Houses utilize broken concrete to fill the earthbags. Concrete is not the only upcycled material Hex-Houses use in the foundation. While there are polypropylene bags specifically made for earthbag foundations, Hex-Houses use recycled polypropylene bags, commonly used in numerous large-volume consumer products, such as dog food or bird seed.
Step 10: Construction: Base
Upon the foundation, the base is built. The base is a single piece of metal from the bottom of a grain bin. The metal that the walls slot into is welded onto the base. While using metal for this is more expensive, it is also more structurally sound, which is critical, considering that this is the base of the entire structure. Additionally, welding the two pieces together provides a weather-proof space for the electrical and plumbing.
Step 11: Construction: Plumbing
Instead of using pipes as traditional plumbing does, the Hex-House uses tubes. This allows the interior modules to have different connection positions, and the plumbing can easily be changed when the interior changes. The plumbing also connects to where the walls are slotted in, and pipes up through the walls allow for water to be transferred to and from the roof
Step 12: Construction: Exterior Walls
The five different external walls have a similar skeleton. Each is built upon a 2x6 bottom plate. The double top plate, necessary because of the hydroponic garden, uses two boards of the same size. The wall studs (2x4) are spaced a foot apart. The wall sheathing, which prevents swaying and bending, is made of 7/16” OSB. Flashing paper is added above the sheathing around windows and doors to prevent leaks. The exterior finish is metal from a grain bin. Before the metal can be used as siding, the grain bin must be dismantled, unrolled, and painted. Grain bins are the perfect material for siding because they are made of galvanized steel, a durable material suitable for an exterior finish. The insulation is located between the wall studs. On the other side of the framing, gypsum board is used as the interior finish. Each exterior wall has a 4x4 post attached to the bottom plate that slots into the groove.
The walls slot into a groove that continues around the entire hexagonal foundation. Where two walls meet, there is a bracket that runs the full height of the wall and bolts both walls together. On top of this bracket, at the top, there is a metal bar that wraps around the walls to ensure that they cannot move outwards (unnecessary at the bottom because the walls are slotted into the foundation). This L-shaped bar goes around the roof and holds it in place.
When connecting units, the connecting walls on each hexagonal unit must be exchanged for matching connection walls. The restraining brackets of the connecting walls are then bolted together. However, before this, rubber is added to all four sides between the module to create a seal to ensure the connection is waterproof.
Step 13: Construction: Insulation
To make the Hex-Houses truly affordable, they must cost little to buy and maintain. To achieve this, insulation is incredibly important. Traditional insulation is expensive, costing up to $7 per square foot. Hex-Houses utilize shredded masks as insulation. Considering that each minute of the day, 3 million masks are thrown away, there is no shortage of mask trash and a solution must be developed. Masks are made of polypropylene, which is known for its insulating properties, making it the perfect material for insulation.
Using masks raises the question of how one cleans used masks? The masks would be cleaned in steam sterilizers. Steam sterilizers are inexpensive, efficient, fast, and sporicidal. It inactivates harmful bacteria, fungi, spores, and viruses by a 6-log reduction, meaning the number of organisms would be 1,000,000 times smaller. Once cleaned, the masks are shredded using an industrial shredder. Each wall would be insulated with 4 inches of mask insulation, and the floor and ceiling are insulated with 3 inches. To secure the insulation, it is covered in sheets of landscaping fabric (affordable and accessible) that are stapled to the wall studs.
Step 14: Construction: Interior Modules & Floor
The interior modules are self-contained sections of floor that can be arranged in a variety of ways. Both the quarter and half modules are built upon the same structure: a wooden lattice built with 2x4s. The subfloor, made of OSB, is built upon it. The floors of the interior modules are made from reclaimed pallets. Oftentimes, pallets can be found for free, which is why they were the material of choice. Finding the right pallets can be challenging mainly because of the hygroscopicity of wood and how pallets are treated. There are several different ways pallets are treated, but the ones that can be used to build are heat-treated, marked HT; debarked, marked DB; both, marked EPAL; or kiln-dried, marked KD. Pallets treated with methyl bromide, a toxic pesticide, should be avoided. Due to the fact that wood absorbs liquids, it is important to consider what was transported on the pallets. Pallets used to ship textiles and paper are ideal. To make the boards, the pallets are broken into planks. The planks are then cut to remove damaged edges and ensure uniformity. Then the wood must be planed using a thickness planer, which smoothes it and trims each board to a consistent thickness. The next step of preparing the floorboards is creating the tongue and groove edges, which is done with a router. Finally, the edges must be cut to match the hexagonal shape. All appliances in the interior modules are connected to the floor – not the walls, which are part of the exterior. Some interior modules do have interior walls, such as the bathroom and bedroom modules.
Step 15: Construction: Electrical
Electrical connections are modular as well. The street connection for each module is within the floor. Wires that can easily be moved allow power to be supplied to interior modules, where the position of connection can vary greatly. To provide electricity to the lights in the ceiling, the slot into which walls are inserted has electrical contacts. Exterior walls connect to these contacts and supply power to the ceiling, which in turn provides electricity for the lights and any other electrical device present on the ceiling.
Step 16: Construction: HVAC
The interior is heated using hydronic radiant floor heating. This is because the plumbing is already located below the floor, and can be used in the radiant heating system. The water in a hydronic radiant heating system is commonly heated to 140 degrees Fahrenheit at the very most. A solar water heater heats water up to 200 degrees, and, therefore, could easily be used in a radiant heating system, meaning it would be virtually free to power the heating system. An entire module can easily be cooled using an economical window unit on the roof. In a larger Hex-House, a split-unit A/C, a more sustainable solution, can be used.
Additionally, because of the modular design, Hex-Houses truly can be modified to fit their environment, which lets them take advantage of passive cooling and heating by allowing for customized window placement, amongst other things, to harness natural heating and cooling.
Step 17: Construction: Roof
Because the interior modules are removed through the roof, the roof must be easily detached. This also means that the removable section must include the interior ceiling to provide unrestricted access to the interior modules. Metal I-beams run across the entire hexagon. The beams are upcycled from 4” wide (the smallest common size) I-beams previously used as framing in a commercial building. I-beams are light and strong and are frequently used due to their impressive load-bearing capabilities. Consequently, the beams are significantly longer than a Hex-house is wide. Therefore, they can be easily salvaged because only short pieces are needed. On top of this, the roof decking would be added. Rather than using typical plywood or planks, the decking on Hex-houses uses high-density cellulose fiberboard made from fiber waste from paper mills. The roof, made of overlapping metal slats from the grain bin, is built upon this. The roof is connected to the walls using an L-shaped metal bracket that wraps around the entire structure's top, increasing strength and water resistance. The roof must be at a slight grade (2%) to prevent water from pooling on it. The water will run into gutters (with a simple leaf blocker) at the lower end of the roof. At the downspout, there is a 2” gap with a second, finer filter at the second pipe. This connects to the rainwater tank, which has a simple sand, charcoal, and gravel filter at the bottom. Four inches from the ground, a pipe continues out of the tank to bring water to the house.
Step 18: Construction: Cost Projection
The total cost for a single module is $4816. This is nearly $200 under the budget. Link to Excel workbook: https://1drv.ms/x/s!Aibg8gwxCq7QjzF9sTtmPS6lz22s?e=SNH5QC
Step 19: Construction: Structural Analysis
Considering the sheer number of untraditional building techniques used, the structural integrity of the building was a concern. A primary concern was the ability of the roof to withstand the weight of the hydroponic garden. To test this, we used Fusion 360’s static simulation capabilities to ensure that the design was structurally sound, assuming the garden could weigh up to 1,000 pounds. In the graphic, the displacement is greatly exaggerated for it to be visible. As seen in the above image, the real displacement caused by the weight would be but fractions of a millimeter. Another concern was that the weight of the roof with hydroponics would cause the walls to buckle. Unfortunately, it was not possible to simulate the walls connected to the roof, as such a large simulation caused the computer running the local simulation to crash. Instead, a single wall was simulated individually, which allowed the computer to process the simulation. The load placed on the single wall was ⅙ of the original 1,000-pound load because the rooftop load would be distributed evenly amongst the 6 walls of the house. In both simulations, the minimum safety factor was 15, which means that the house parts were more than strong enough (the safety factor ranges from 0 to 15, with 0 being the least safe and 15 being the safest).
Step 20: Additional Details: Other Interior Modules
QUARTER BATH
The quarter bathroom is a full bathroom equipped with a shower, toilet, and sink. The sink is not apparent in the floor plan because the toilet and sink are connected. The sink drains directly into the toilet tank, which flushes using the grey water. The average toilet takes about 1.6 gallons to flush, meaning a family of three could save around 38 gallons of water per day, thereby saving money and helping the environment. The sink has a pipe that extends from the bottom of the faucet through the floor to the plumbing section, where it connects to a water line from the rain tank.
HALF BATH
The half bath has more amenities and space. The shower is larger, and there is more storage. The bathroom is divided into two sections. The first section, which includes the entrance to the room, has a large vanity with storage and two sinks. Next to it is a shelf for additional storage. The second section contains the shower and toilet. The sinks, shower, and toilet all use purified (although still non-potable) rainwater, which, once used, will be filtered again and used to water the hydroponics.
HALF KITCHEN
The half kitchen has significantly more counter space as well as more storage. This design includes a pantry and a larger fridge. Additionally, the layout has much more space, making it easier to maneuver while cooking.
QUARTER CHILD'S BEDROOM
This small bedroom is intended for a single child. The bed is a murphy bed that folds up to be a small desk with overhead cabinets during the day. There is a small dresser and triangular nightstand for storage. It is overall a simple design that accomplishes
HALF BED
The half bedroom has a closet, full-sized bed, and sitting area. Between the two chairs, there is a small fold-up table. Instead of a Murphy bed, this bed has extra storage underneath.
QUARTER DINING
The quarter dining resembles the dining area in the kitchen and living space module, but the table is longer and able to seat more.
HALF DINING
A much more spacious design, the half dining has a traditional, circular dining table. There is also a small buffet.
QUARTER SITTING ROOM
The quarter sitting room is a small private space for reading.
These are a few examples of modules, but there are endless possibilities for different interior floor plans.
Step 21: Creation Process: Design Evolution
The original Hex-House differed substantially from the final design. Originally, there were only different hexagonal modules built from grain bins bent into hexagonal prisms with specific, permanent interiors. However, not only did this make expansion virtually impossible for single-unit residents, but it also eliminated the possibility of someone reusing a module after the original resident no longer needed it because there would be permanent holes for doors and windows, which meant that the modules could only ever be arranged in the same way as they originally were.
Step 22: Creation Process: Designing the Single-Unit Interior
The single-unit house is the foundation of Hex-Houses, but designing a family home in just 160 square feet was challenging. Having lived in and traveled in an RV of a similar size for months, we understand where space is necessary. In such a small space, amenities must be prioritized.
When designing the floor plan, I originally began with a layout that differed significantly from the final plan. While both floorplans essentially had the same appliances and furniture in them, the final one had nearly 50 square feet of open space while the first plan had only 30 square feet. I was unsatisfied with the first plan because, in many places, the walkway was narrow and would only allow for one person to pass at a time, because the kitchen used an unnecessarily large amount of space, and there was a significant amount of wasted corner space. When reviewing the first floorplan, I realized that it was the placement of the bathroom that was the source of many of the issues and the awkward layout. Moving it to a less intrusive place would remedy many of the present issues.
It was difficult to incorporate the bed without having the bedroom take up an unreasonable amount of space due to the limited amount of places where a 6.5-foot bed could be placed. Our solution was a foldable Murphy bed. The Murphy bed converts into a closet with clothing and bedding storage during the day.
Another challenge when designing the single-unit house was storage. With most of the space being taken up by furniture and appliances, there were not many places to add storage without further restricting the space. In the end, cabinets above the desk in the bedroom, the bathroom sink, and the kitchen counter were placed. The loft has storage for personal belongings including a small closet, drawers, and two shelves. Additionally, there is storage under the couch, as well as shelving above it.
The entrance to the single-module house uses a technique also used by Frank Lloyd Wright, which we learned of while taking a tour at Wright's Gordon House in Oregon. At the entrance, the space condenses with a much lower ceiling (caused by the loft), and then dramatically expands. This draws the eye in and makes the space seem bigger. Below the loft, the ceiling is seven feet, and, while still walkable, it was most fitting to use this space as an area for sitting, which is why both the couch and dining room table are located there.
While pure white paint is commonly used in small spaces under the guise that it will make the space feel lighter and brighter, it can actually make the space feel bland and accentuate shadows and dark corners. Instead, the walls are painted with a warm neutral color (Natural Linen, SW 9109) similar to but lighter than beige. The couch is neutral to match the walls, and the baseboards are white to accent the neutral colors.
Step 23: Creation Process: 3D Modeling
I used Fusion for most of the modeling. The reason I used the software was that it allowed for the rapid prototyping and creation of models using a non-destructive workflow. Thus, when something early along the pipeline of modeling needed to be changed (i.e. wall thickness) the modification could easily be made, and the entire model would be re-calculated automatically. Additionally, Fusion 360 was capable of simulations, which were critical to ensuring that the design would actually work.
After creating the floor plan, I began modeling the house. After completing the floor, I made a set of modular exterior walls which would allow many possible exterior configurations. Next, I created the roof. With most of the exterior complete, I then moved to the interior. I modeled many different interior modules based on Lucy’s floorplans, complete with basic furniture.
Although Fusion 360 worked well to create the models, the renders it produced were not photorealistic. We wanted photorealistic renders because they provided viewers the experience of seeing and understanding what living in a Hex-House would be like. So, to get the renders I desired, I used Blender. I began by exporting all of my models as .fbx files from Fusion 360 and importing them into Blender. Next, I added additional details to the furniture. After UV unwrapping everything, I applied PBR textures to the model. Next, I used procedural techniques via node-based programming to randomly create noise and surface imperfections on the textures for increased realism. Next, I created a realistic environment using particle systems to generate trees, grass, rocks, and some flowers, on a hill. I then used the scene to render the different module configurations. Finally, I created a scene with a white background and studio lighting to render each of the modules alone.
All 2D floor plans were created by Lucy in Revit.
Step 24: Conclusion
In creating this project, we learned about the circular economy, designing affordable housing, and how to implement sustainability in the housing industry. Most importantly, we learned about how they are intertwined with each other. When designing sustainably, oftentimes, the resulting designs are both affordable and a part of the circular economy. We believe that our design presents a unique solution to the housing crisis, and has the potential to change the world.
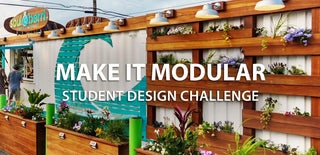
Second Prize in the
Make It Modular: Student Design Challenge