Introduction: Homemade Bench Oak Carvers Vice (Vise)
Ever since I set up the workshop, the missus (Grace) has found herself at home in there. This was no more apparent than when she discovered she had a taste for carving. All of a sudden my metalwork bench was awash with wood chips! And the reason for this gross indiscretion? Mechanic’s vices are rather handy for carving. Indeed, this is what many carvers use. But handy for me it certainly was not; the wood chips all over my surface plate were rather cramping my style. The solution was to make Grace a traditional carving vice. This would allow Grace to carve in style while keeping my mechanic’s vice blissfully free of woody matter.
The design is based very loosely on drawings published by Benchcrafted, which in turn were based on a vintage model. I started with some oak for the main construction. This started life as an oak sleeper, and at some point was ripped down into a 4×4 post:
Step 1: The Main Body of the Vice
I started with some oak for the main construction. This started life as an oak sleeper, and at some point was ripped down into a 4×4 post:
The oak was ripped to size and planed flat and square:
Step 2: The Jaws
Next I shaped the top of the front jaw and bored the 1″ hole for the
vice screw. The rear jaw was shaped and bored at the same time. Then I was ready to cut the massive dovetails that join the base to the front jaw. I cut these by hand, but in hindsight the bandsaw would have been the quicker option!
Grooves were ploughed down either side of the base to act as runners for
the rear jaw reinforcement brackets. The brackets will add some strength to the rear jaw, but are mainly there to capture the jaw to the base. A tee-shaped slot was mortised into the base using two forstner bits then tidying up with a chisel. The top part of the tee houses the top of the hold-down bolt.
Step 3: The Shaft
Now for the fun bit; making the 1″ shaft for the vice screw on my trusty Myford ML4. First to face off the rough-sawn end of the shaft:
(I can assure you the Dr Pepper cans are only there because I needed some shims, honest!)
Then some relief diameters were turned down on either end of what was to become the threaded portion of the screw, and the screwcutting began:
A perpendicular hole was drilled through the end for the tommy bar. No pics of the tommy bar being made; the ends are simply threaded on to the bar:
(not in the photo is the groove to accept the garter. That came later as I didn’t have the steel at the time)
Step 4: Hold Down Shaft
The vice needs a bolt to hold it down to the bench. Naturally this bolt has to be rather hefty (3/4″ in this case), and it has to have a square head in order to be trapped by a housing in the base of the vice. The bolt head was milled down from some steel bar using a home-made flycutter:
The main part of the bolt was screwcut and attached to the bolt head:
Step 5: The Garter
Eventually I managed to pinch some steel for the garter from the local
blacksmith. I drilled out the mounting screw holes on my bench drill, but the centre hole had to be bored out on the lathe:
The garter had to be cut into two halves to fit around and capture the
vice screw. I could have did this by hand, but it would be a lot tidier (and easier on my feeble arms!) to once again use the ML4:
Step 6: Assembly
Finally the vice could be assembled. A strip of steel was added down each side of the base as reinforcement and to prevent the side brackets from wearing away the grooves. The side brackets were made from some steel sheet I had lying about. I’m not very happy with the brackets, I think they need to be bigger. Maybe I’ll come back to those….
Step 7:
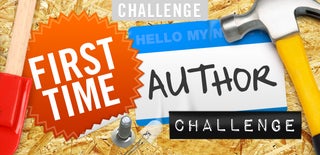
First Prize in the
First Time Author Challenge
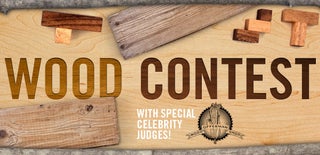
Runner Up in the
Wood Contest