Introduction: Homemade Carbide Wood Lathe Tool
I purchased a Carbide Insert Lathe Tool which can be seen in the top of the photo and decided that I wanted to make a better one using hard woods and Stainless Steal
Step 1: Parts List for Tool
There are not a lot of parts needed to make a nice Wood Lathe Tool
1. Description: Nut, Type Compression, Tube Size 3/4 In., Tube Outside Dia. 3/4 In., Thread Size 1-18, Thread Connection, Material of Construction Brass
Purchased: www.zoro.com
Model #: G3942032
Price: $1.53 ea
2. Description: 0.375" T-304 Annealed Stainless Square Rod, Random Length (10"-12")
Purchased: www.onlinemetals.com
Model #: N/A
Price: $ 3.78 ea
3. Description: 11 x 11 x 2 R50 Carbide Insert 6.5% colbolt
Purchased: eBay Putm-Bruc seller - Drop me a note if you would like to buy some
Model #: N/A
Price: $ 4.95 ea
4. Description: 8-32 Flush Head Stainless Steal screw
Purchased: Denault Hardware
Model #: N/A
Price: $ 0.33 ea
5. Description: Wood ( Wild Almond and Iron Wood )
Purchased: eBay
Model #: N/A
Price: $20 for both
6. Description: Rubber Washer 9.5 x 17.5 x 4 mm
Purchased: www.HarborFreight.com
Model #: N/A
Price: $3.99 set
Step 2: Tools That I Used for This Project, These Can Be Replaced by Others.
Photo 1: Jet Mini Lathe - Woodcraft
Photos 2-3: Powermatic (1971) Bandsaw - Craigslist
Photo 4: 12" Ridgid Miter saw - Home Depot
Photo 5: Shop fox Drill Press - Amazon
Photo 6: Jet 12" Disc Sander - Woodcraft
Photo 7: Jet parallel Clamp 12" or larger - Woodcraft
Photo 8: Files.. Course, Medium and Fine - Woodcraft
Photo 9: Countersink with tool to apply it - Woodcraft
Photo 10: Tap Handel with 8-32 tap - Lowes
Photo 11: Grinder - Sears
Photo 12: Metal vice and hand held disc grinder - Harbor Freight
Photo 13: 3/8" Chisel - Woodcraft
Photo 14: Plastic Mallet - Woodcraft
Photo 15: Wire wheel - Home Depot
Photo 16: Lathe Caliper - Woodcraft
Photo 17: Large adjustable Wrench 1 1/2" Capacity - Lowes
Photo 18: 2 Jorgensen Clamps - Woodcraft
Photo 19: Gorilla Glue - Woodcraft
Photo 20: Tap Magic - Anazon
Photo 21: Medium CA Glue - Woodcraft
Photo 22: Thin CA Glue - Woodcraft
Photo 23: EEE Ultra Shine - Woodcraft
Photo 24: Gloves and scissors - Lowes
Photo 25: Wax paper - Vons
Photo 26: Tape Measure - Woodcraft
Photo 27: 6 inch scale - Woodcraft
Step 3: Cutting Wood to Size
I cut the wood into 1 1/2" x 1 1/2" x 6 " pieces using my 1971 Powermatic Bandsaw and Ridgid 12" Chop saw.
Step 4: Gluing the Wood Together
I use gorilla glue to glue the 2 sections together.
This requires wetting the surfaces with water befor gluing..
I use parallel clamps to assure the parts stay square to one another and place wax paper on the clamp where the glue joint is to eliminate the need to scrape glue off the clamp
Step 5: Prepping the 3/8" X 3/8" Stainless Bar
For the Stainless bar, I needed at least 10", so when I purchased them I choose random lengths from 10 to 12 inches.
As you can see from the photo, mine were cut to 11 inches.
As the ends we're rough cut, I used a file to smooth them.
Step 6: Drilling - Learning - Drilling
I must say I learned a lot about 304 SS..
I started out drilling the holes for a 6-32 tap.. what I found is 304 SS work hardens fairly easily.
I read that when you drill SS you need keep the speed slow, 200 - 300 RPM, and use cooling fluid, oil and press hard.
You drill wood at approx. 1500 RPM's and you don't drive the drill by pressing too hard, plus you pull the bit out frequently to remove wood chips.
When I drilled the 6-32 tap hole I drilled through the material too slow. The good news it just work hardens in a local area, so drilling out for an 8-32 tap I drilled through quickly while sucking air over the metal with a shop vacuum.
Photos 1-8 are drilling the SS for a 6-32 tap
Photo 9 is a broken 6-32 tap
Photos 10-12 are drilling the SS for a 8-32 tap
Step 7: Tapping the SS Bar With a 8-32 Tap
Prior to Tapping, I used a countersink to help with starting the tap and also giving room for the screw.
I used tap magic on the tap and assured I removed metal chips as I cut.
Step 8: Marking and Grinding to Place the Carbide Insert Flush With the Top of the SS
Photos 1-7 are showing how I marked the SS to Grind for the carbide insert
Photos 8-9 show clamping a piece of maple to the SS to Grind it.. This did 2 things, one it produced a stop for Grinding and two allows me to hold the SS as it gets very hot.
Photos 10-12 show Grinding
Photos 13-17 show the ground SS before it is filed.
Photos 18-19 show the final cut, that has been filed and fitted with a carbide insert.
Step 9: Cutting the SS to Length
Measuring the Wood Turning Tool, it had 4 1/2" from the handle out. As I wanted 4 to 5 inches remaining in the handle I decided to cut the 304 SS to 9 inches.
I used a hand grinder and a vice to cut each piece to 9"
I then ground the end I cut in a bench grinder.
Step 10: Trimming the Glued Wood
Using the bandsaw, I trim off the foam from the gorilla glue and cut the corners off which I find is easier than doing it on the Lathe
Photos 3-7 show the trimming of the corners and results
Step 11: Marking the Centers, Tapping in the Spur Center and Mounting to the Lathe
I first mark an X for the center of the spindle piece, photo 1.. note that this could have been done before the last step in cutting the corners off, but since I have a lot of extra wood for turning I was not that concerned to getting it exact.
Photo 2 shows the spur center tapped in with a hammer. You can also make your X and then cut it on the bandsaw.
Photos 3-4 show the spindle mounted on the Lathe
Step 12: Measuring the Compression Nut Diameter and Depth and Marking on the Spindle, Turning for the Nut to Be Threaded On.
Now I measure thr brass compression nut thread diameter and depth. I use a Lathe caliper for the diameter and a 6 inch scale for the depth.
Photos 2-3 I mark the depth on the spindle where I turned it round on the end.
Photo 4 turning the spindle to diameter
Photo 5 checking with a caliper
Photos 6-7 I used a large adjustable wrench to thread the brass compression nut on the wood spindle.
Step 13: Using a Course, Medium and Fine File on the Brass Fitting
With the brass compression nut threaded on the spindle, I use a file to remove the flats on the nut as shown in the photos
Once it is round, I use a med. then fine file to smooth and polish the brass.
Note that I have dust collection hose just under the brass compression nut to remove the brass dust while filing.
Step 14: Finish Turning the Spindle and Applying CA Glue for the Finish. Polishing With EEE Ultra Shine
As I do a lot of pen turning, I am used to applying CA glue ( AKA Super glue ) to pens.. why not the tool that will turn the pens..
Photos 1-5 show turning the spindle
Photos 6-8 show the spindle with CA glue.. To understand how to apply CA glue, refer to my instructable on making a pen.
Once the CA is applied and sanded, I use EEE UNITA shine to polish the finish.
Step 15: Drilling for the SS Bar in the Spindle, Cutting, Sanding and Finishing the Spindle End
As my Lathe is a mini Lathe I there is not enough room to mount a drill on it, so I used my drill press to drill a 3/8 hole 5" deep
I could have used a parting tool to remove the end of the spindle but did want to take a chance of denting the brass or wood so I cut it on my bandsaw, photo 3.
Photo 4 shows the end after cutting on the bandsaw
Photo 5 sanding on my 12" disc sander
Photo 6 ready for finish
Photos 7-8 applying thin CA on the end... as this is a bit messy photo 8 shows with cap on.
Step 16: Using a 3/8 Chisel to Square the 3/8 Drilled Hole
If you have a metal Lathe you can replace this with turning the SS bar round on the end that goes into the handle
Step 17: Hand Grind the 304 SS to Better Fit in the Handle
Photos 1-2 show the Grinding of the bottom end of the 304 SS bar to assure I don't crack the wood while hammering it into the handle
Photos 3-4 shows installing the SS bar. Note that I added CA glue into the sides of the hole befor pushing and hammering in.
That last step was to slide the rubber washer over the 304 SS bar.
Step 18: Lightly Smooth the Surface of the 304 SS
I mounted a wire wheel on my drill press to lightly smooth the surface of the 304 SS
Step 19: Completed All 5 Tools.. 3 Sold, I'm Using 1and One on EBay
I've completed all 5 tools... a lot of work, but I am real happy with the finished tools..
If you are interested in buying the carbide inserts or one of the tools, please shoot me a note. I plan to auction 1 of the tools and will be selling the inserts for the remainder of this year depending on demand.
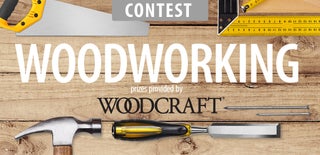
Runner Up in the
Woodworking Contest 2017