Introduction: Casting a Rose With a Fish
I wanted to make a present for my lovely wife who has recently become a mum and for my mum to let them know they are amazing and very special to me. (That and I really wanted to use pewter and make a Tudor Rose).
Pewter casting doesn't have to be expensive to get into, certainly the pewter part is not expensive, but it looks like it should be to anyone who doesn't know how much the raw materials cost. I use some professional gear- mainly because it makes things a little easier, but you could use a hob and a non-stick pan.
Pewter is an alloy of tin with copper and antimony.
(old stuff was made with lead but this tends not to be the case any more, DO NOT USE THE LEAD VERSION as its a bit toxic (though admittedly we used to use lead pewter to make cups in the past)
About the design
I heard that The Game Of Thrones was inspired in part by the War of the Roses. (One of England's big civil wars).
Looking at the Tudor rose from this conflict, I was taken back at its resemblance to the banner of House Tyrell.
I particularly like House Tyrell's motto "Growing Strong" and thought it would be fitting to link the two best mum's I know to this message. + I am from Lancashire so the Tudor Rose feels like its part of the history of the place I grew up.
One of the brilliant things about making things yourself is you can take elements of things you like and mix and match them to suet you.
Step 1: Cuttle Cut
This method of pewter casting uses a cuttlefish bone. You might be lucky enough to find these on the beach but if not there is a good chance you will be able to find a good selection of kiln dried ones in pet shops, they are sold for small birds to play with. (the dryness is important so if you are picking them off the beach I would recommend storing them in a dry place for at least a couple of months before using them)
Using a saw cut down the length of the bone. It is important to do this in one go, the striations you make with the saw in this stage will act as registration marks later on when it comes to casting if they don't match up then the molten pewter is likely to pour out.
If you make a mistake at this point don't worry, not all is lost, you have just created an extra step. Flattening the cuttlefish. to do this take a flat sheet of sandpaper tape it to a flat surface and rub the sawed edged of the cuttlefish until they are as flat as they can get. (it shouldn't take long, cuttlefish bone is very soft)
Step 2: Drawing It Out
I had an idea of what I wanted to make so I gathered some reference materials and refined a design.
One side of a cuttlefish bone will be harder and firmer than the other, this is the side we will be working on.
I freehand drew my initial design using a HB pencil and then came to the realization that I wanted the finished product to be smaller, using a rubber I erased the original sketch and redrew my design smaller.
Its worth noting that this technique can be used to produce fine wire like designs as well as chunky work.
One of the really nice things with cuttlefish casting is the almost woodlike texture of the bone, it creates fab texture on casts which looks great, but if you don't like it you can file and sand it away after casting.
Step 3: Getting a Bit Scratchy
Cuttlefish is very very soft, as a result, you can use pretty much anything to carve out your design. I used a needle file.
At this point, it might help to have a straight edge handy to line up and help identify how deep you have carved.
Once you are happy with your carving its time to think about where your pewter will enter the mould. I think its always best to enter at a big fat or flat point (it makes cleaning up easier afterwards)
Step 4: Getting a Bit Tied Up
Using wire tie the two halves of the cuttlefish back together.
If you sawed the fish try to get the two sides to register together as well as possible, they should kinda click into place.
I think it is a good idea to start the tying process by creating a loop with some twists on one side of the wire and twisting on the other end. This gives a point for a later step and an easy place to twist in order to help clamp the two halves together.
Step 5: The Pewter Part
So this is the bit where you could use a proper adjustable melting pot or just a non-stick pan on the hob.
pewter has a low melting point so you can be creative in how you want to melt it, but once it has melted you will probably have to take off the slag or dross (the lair of containment floating on the top) I use a teaspoon with a long handle to scoop this and tap it off into a heap for binning after.
It is a good idea to get used to the weight of pewter by scooping some up in a ladle and pouring it out until you feel comfortable with it, (pewter is very dense and therefore heavy) once you are good to go pour it into the entry hole on your cuttlefish mould.
I held my cuttlefish upright for the cast on a baking tray using some heat proof rocks
IMPORTANT SAFETY POINT
Water and molten metal are not friends. If you are not sure about the dryness of your cuttlefish the expanding water and steam from the cast will come out of the entrance hole. with this in mind wear appropriate protection including safety specks and keep your face away from the hole whilst casting!
Step 6: Cleaning Up
If you are careful you might be able to get a few casts from your cuttlefish. :)
I used a jewellers saw with a fine blade to cut the spur (the bit that isn't rose) from my design.
once the spur was no longer attached I filed and sanded the rose until it looked good.
I could have designed the rose with a loop to attach to a keyring or necklace, instead, I used a small drill to make a hole in an aesthetically justified location.
If you have access to a tumbler you might want to use one to add an extra bit of sparkle.
Step 7: Attaching the Hardware
OK so this is the one step that is probably the most useful for lots of projects, not just casting in pewter.
To attach the hardware, in this case a silver chain or a key ring open the connecting link with two pliers by twisting the ring. Once the ring is open enough to attach your pendant or charm close the ring in the by twisting it back into shape.
(The first time i did this I pulled the ring open and deformed it to the extent that I needed to make an entirely new ring link)
I hope you have enjoyed reading this instructable and feel inspired to try cuttlefish casting for yourself. please do pay attention to health and safety warnings. Making is fun but injuries aren't
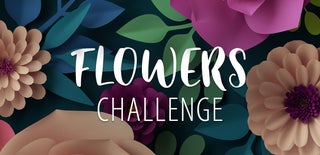
Participated in the
Flowers Challenge