Introduction: How I Designed a Marble Pump - 3D-printable and Lego Compatible
For my godchildren, I developed and 3D-printed a marble pump. The marble pump is compatible with Lego / Duplo bricks and designed to use with Hubelino marble tracks.
First I explain you, how I made 3D-printable parts which fit the Duplo bricks.
Second I show you, how is designed the marble pump witch lift the marbles from the finish to the start of the Hubelino tracks.
I made a short video, where you can get a first impression.
Hubelino marble run http://amzn.to/2gon6T8 (affiliate)
Step 1: 3D-Printable Duplo Bricks Design
The design of the Duplo bricks is optimized for injection mold fabrication.
We want to 3D-print the bricks.But the design with is great for injection molding is not ideal for 3D-printing.
With a 3D-printer parts can have a different wall thickness and hollow bodies with an infill. The same is not true for injection molded parts.
So, I made some changes to the brick design for better printing.
- The top knobs are not hollow, they are filled with the infill pattern.
- The bottom as much contact surface to the printbed as possible.
- Thereby we can avoid the thin ribs on the inside. Instead, we have our infill pattern.
- The holes are shaped rectangular to provide a detachable fit to the knobs.
I made a parametric brick design in Fusion 360. There I can just pick the number of knobs in width and length and also the hight of the brick. I will add a link as soon is have published it.
Step 2: Tune in a Tight Fit (Adjusting to the Print Accuracy)
We want our 3D-printed bricks to fit the generic Duplo bricks.
If we just 3D print our CAD model, it will not fit perfectly. So we have to tune in the dimensions of our print.
- I made a test print with a brick. Then I compared printed one to the generic brick.
- With the scale function of the slicer, I adjust the error of the pitch of the knobs.
- With this, the shrinkage of the part can be compensated. For PLA I have to scale by 1.005.
- Next, the holes in the bottom and the knobs have to be tested to fit on its counterpart of the generic brick.
- If the holes ore the knobs need some adjustment, we have to change their size in the CAD.
With this steps our 3D-printed brick fist correct to the generic brick.
With this know-how, we now can design new things which are compatible with the bricks.
Step 3: Auger Fed Marble Pump
There are many different types of marble pumps known. I have chosen the auger type marble pump.
The principle of the auger marble pump can be explained with the model of a slope where we push the marble upwards. The auger is just an up wound slope. The rotation of the auger acts the same as a translation of the marble on the slope.
We want to prevent the marble from rolling down the slope. Therefore the geometry of the auger enclosure has to hold the marble in its horizontal position while allowing a vertical movement.
Step 4: Merging of the Marble Pump With the Brick Design
We have not to integrate the marble pump mechanism into some bricks. Due to the Hubelino marble tracks, a size of 4 by 4 knobs seems suitable for our pump.
I want to have the crank turning clockwise. (Because good product design uses always common conventions for better usability. And this is also true for toys.) Therefore the marble has to insert on the left side. Otherwise, the marble would be pushed out.
The insertion hole is sloped to let the marble roll inside the marble pump. To aid this it is best if the last marble track is also a sloped one.
The diameter dimension of the auger is given. The radius has to be 1.414 * dupolo-pitch. like this, the half marble is running inside the helix groove of the auger. the other half marble is guided in the vertical groove of the pump housing.
The height is chosen to match the height steps of the Duplo bricks. The mump main part measures 3 duplo-heights, the spacer, and top part one duplo-height.
Step 5: 3D-Printing of the Marble Pump
Now I explained to you how I designed the marble pump. You can either download my files and print them, or you can design your own marble pump and add some features to it.
As explained in the Video, I designed two versions. The differences in the feeding of the marble to the marble pump.
Version 1 (feeding with generic Hubelino track)
- Auger V1
- Pump housing V1
Version 2 (feeding with optimized marble track)
- Auger V2
- Pump housing V2
- Feeding slope V2
Common parts (version 1 and 2)
- crank short
- crank long
- spacer block
- top outlet right
- top outlet left
I recommend that you first print the following sample brick to tune in the printer settings for a perfect fit to the generic bricks.
- generic brick for testing
Enjoy!
Attachments
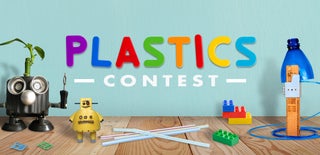
Runner Up in the
Plastics Contest
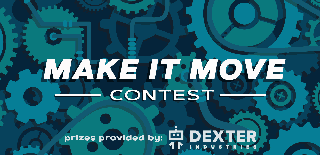
Second Prize in the
Make It Move Contest 2017